Описание технологического процесса
Для бесперебойной работы основных производственных цехов на заводе организовано складское хозяйство всех компонентов железобетонных изделий.
Заполнители поступают в приемное устройство автотранспортом. Выгрузка заполнителей производится гравитационным способом. Затем ленточным транспортером подаются в бункера склада заполнителей. Бункера оборудованы паровыми регистрами. Ленточным транспортером заполнители подаются через поворотную воронку в расходные бункера крупного и мелкого заполнителя. Для предотвращения переполнения в каждом расходном бункере установлены верхние и нижние ограничители уровня.
Из расходных бункеров инертные поступают в автоматические весовые дозаторы и, через сборную воронку, подаются в бетоносмеситель.
Добавки поступают на склад автотранспортом в мешках. Они разгружаются и отправляются электрокарами в машину для распаривания. Из машины для растаривания с помощью шнекового питателя добавки поступают в баки для хранения, где они хранятся в различных концентрациях, приготовленная добавка подается насосом в расходный бак, оборудованный дозатором, далее поступает в бетоносмеситель. Вода для приготовления бетонной смеси из резервуара для воды подается насосом в расходный бак для воды оборудованный дозатором, затем подается в бетоносмеситель.
Цемент поступает на завод железнодорожным транспортом. Специализированные вагоны бункерного типа разгружаются в приемный бункер и пневмоподъемником подают цемент, очищая воздух от влаги и масла в аэрожелоб и далее в силосы. Выдача цемента в расходные бункера цемента предусмотрена с помощью донных пневморазгружателей. Перемещение цемента в расходные бункера бетоносмесительного отделения осуществляется с помощью пневмовинтового насоса. Для предотвращения переполнения в каждом силосе установлены указатели уровня. Очищение запыленного воздуха производят в циклонах и фильтрах с помощью вентилятора очищенный воздух уходит в атмосферу.
|
|
Арматурные изделия производятся с максимальной заводской готовностью в арматурном цехе. Стержневая арматура и арматура в бухтах поступает на склад
автотранспортом. Арматура правится и режется в станке PSC-812 SQ, сварка каркасов и сеток производится на машинах одно и многоточечной сварки, резка стержневой арматуры на станке для резки, остатки стержневой
арматуры свариваются на станке для контактной сварки, монтажные петли изготавливаются на гибочном станке. Арматурный блок собирается на поворотном кондукторе, оборудованном подвесными клещами. Готовый блок устанавливается в отсеки кассеты.
|
|
Приготовление бетонной смеси на заводе производится в БСУ одноступенчатой компоновки. Прием материалов со склада и распределение по бункерам осуществляется в верхнем надбункерном этаже. Здесь размещаются приводы ленточных транспортеров, а также распределительные устройства - поворотная воронка, циклоны, матерчатые фильтры и шнеки для распределения цемента. Цемент отделенный от воздуха поступает в расходные бункера цемента. Течки бункеров заполнителей оборудованы секторными питателями, течки бункеров цемента шнековыми питателями. Под каждой течкой располагается дозатор, соответствующий данному материалу. В смесителях принудительного действия происходит перемешивание бетонной смеси. Готовая смесь через воронку выдачи бетонной смеси подается бетононасосом через бетонопровод который поддерживается мостовым краном в отсеки кассеты.
Разборка кассеты осуществляется с помощью установки для распалубки кассеты. В разобранные, предварительно очищенные пневмоскребком и смазанные рапылительной удочкой разделительной смазкой ОЭ-2 отсеки кассеты устанавливается арматурный блок, после закрытия кассеты и фиксирования отсеков с помощью замков заливается бетонная смесь и проводится виброуплотнение навесными вибраторами ИВ-104. Наиболее целесообразно на каждом из разделительных листов устанавливать два вибратора, по одному с каждой стороны. При этом вибраторы следует устанавливать в верхней трети листа на расстоянии не менее 500 мм от верхней кромки и ротор вибраторов располагать вертикально.
|
|
С целью повышения эффективности виброуплотнения и надежности работы оборудования непрерывное время работы прикрепляемых вибраторов не должно превышать 2-3 мин, с последующими перерывами в течение 6-8 мин. В соответствии с указанным подачу бетонной смеси следует планировать таким образом, чтобы в течение 2-3 мин смесь подавалась в первые два отсека, затем в последующие с возвращением к первым отсекам до тех пор, пока форма не будет заполнена полностью. Далее проводится тепловлажностная обработка по заданному режиму. Готовые изделия распалубливаются установкой для рапалубки кассет с помощью мостового крана изделия кантуются на кантователе, из вертикального в горизонтальное положение, укладываются мостовым краном на вывозную тележку (52) и отправляются на склад готовой продукции.
Методы контроля
1. Испытания плит нагружением для контроля их прочности, жесткости и трещиностойкости (если это предусмотрено рабочими чертежами плит) проводят согласно ГОСТ 8829-94 и рабочим чертежам этих плит.
|
|
При испытании нагружением плиты должны выдерживать контрольные нагрузки, установленные рабочими чертежами этих плит.
2. Методы испытаний бетона и бетонной смеси, а также материалов для
их приготовления следует принимать для тяжелого бетона - по ГОСТ 26633-91;
3. Контроль сварных соединений арматурных и закладных изделий - по ГОСТ 10922-90.
4. Размеры плит, отклонения от прямолинейности профиля верхней их поверхности и профиля боковых граней, отклонения от плоскостности лицевой нижней (потолочной) поверхности, разность диагоналей плиты, размеры и положение арматурных и закладных изделий, выпусков арматуры и монтажных петель или строповочных устройств, а также качество бетонных поверхностей плит проверяют методами, установленными ГОСТ 26433.1-89.
5. Положение арматуры в плите, а также толщину защитного слоя бетона до арматуры определяют по ГОСТ 22904-93.
При отсутствии необходимых приборов допускается вырубка борозд и обнажение арматуры плит с последующей заделкой борозд. Борозды допускается вырубать на расстоянии от торцов плит, не превышающем 0,25 длины плиты.
6. Диаметр каналов и трубок для сменяемой электропроводки проверяют путем протаскивания через них по всей длине стального шарообразного калибра диаметром, равным 0,9 номинального диаметра канала (трубки), указанного в рабочих чертежах плит.
Калибр должен быть закреплен на гибком тросе. Отклонение действительного диаметра калибра от номинального не должно превышать 0; - 0,2 мм.
7. Контроль наличия закладных изделий, выпусков арматуры, монтажных петель или строповочных устройств, очистки от наплывов бетона, наличия антикоррозионного покрытия, наличия жировых и ржавых пятен на лицевых поверхностях плит, правильности нанесения маркировочных надписей и знаков - путем внешнего осмотра
Дата добавления: 2018-09-22; просмотров: 163; Мы поможем в написании вашей работы! |
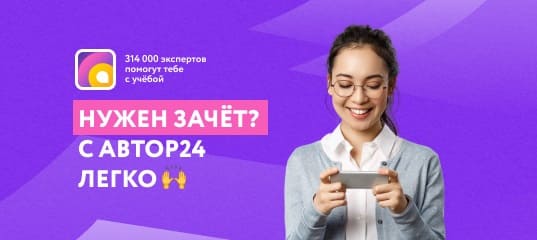
Мы поможем в написании ваших работ!