Методы определения твердости металлов.
2.1. Определение твердости по Бринеллю Твердость определяется вдавливанием в изделие стального шарика определенного диаметра (D) с определенной нагрузкой (Р). Число твердости по Бринеллю НВ (Н/м2 ) равно отношению на- грузки к площади отпечатка (F).
НВ = Р/ F = Р / π D
h = 2P/ π (D – D 2 – d 2 )
где d – диаметр отпечатка, измеренный после снятия нагрузки, h – глу- бина отпечатка, вычисленная по D и d. Для определения твердости металла применяют шарики следующих диаметров: 2,5 мм; 5 мм и 10 мм, для металла толщиной, соответственно, до 3 мм; 3-6 мм; более 6 мм. Между диаметром шарика и нагрузкой существует определенная за- висимость:
Для черных металлов Р = 30 D 2 ;
Для меди, латуни, бронзы Р = 10 D 2 ;
Для алюминия и его сплавов Р = 2,5 D 2 . 2.2.
Определение твердости по Роквеллу. В поверхность испытуемого материала вдавливают наконечник под действием предварительной (Р1 = 100 Н) и окончательной (Р2) нагрузок. В качестве наконечников для твердых металлов применяют алмазный конус 8 с углом при вершине 120º или стальной закаленный шарик диаметром 1,59 мм для мягких металлов. В зависимости от типа испытуемого материала выбирается тип наконечника и назначается окончательная нагрузка. (см. табл. 1). Показания снимают по одной из шкал прибора (А, В или С). В за- висимости от шкалы, по которой определяют число твердости, приняты следующие обозначения: HRA, HRB и HRC.
Твердость по Роквеллу определяют по формуле: HR = K – (h2 – h1) / b где h1 и h2 – глубины внедрения наконечника под действием предвари- тельной (Р1) и окончательной (Р2) нагрузок соответственно, мм; К – посто- янное число, имеющее размерность в мм; b – цена деления шкалы индика- тора, соответствующая углублению наконечника на 0,002 мм
|
|
2.3. Определение твердости по Виккерсу. При определении твердости в испытуемый материал вдавливают че- тырехгранную алмазную пирамиду с углом при вершине 136º. При этом 1,59 мм 120º 120º 9 применяют нагрузки от 50 до 1200 Н. После действия нагрузки на образце остается отпечаток в виде квадрата. Число твердости определяют как нагрузку, приходящуюся на еди- ницу поверхности отпечатка. НV = 2 P sin 0,5α / d2
где Р – нагрузка на пирамиду; α – угол при вершине пирамиды; d – длина диагонали отпечатка.
В чем отличие твердости HRA, HRB и HRC.
Определение прочность,пластичность и тякучесть
Испытание на растяжение производят на разрывных машинах с автоматической записью кривой растяжения металла. На вертикальной оси диаграммы откладывается нагрузка Р, по гори- зонтальной абсолютное удлинение образца Δℓ.
На участке ОРр удлинение Δℓ образца увеличивается прямо пропорционально нагрузке Рр, называемой нагрузкой предела пропорциональности. На этом участке происходят упругие (обратимые) деформации образца и сохраняется закон Гука (ε = ζ / Е). Пределом пропорциональности ζр называется наибольшее напряжение, до которого относительное удлинение образца остается прямо пропорциональным нагрузке Рр. ζр = Рр / F0
|
|
Пределом текучести ζт называют наименьшее напряжение, при котором образец деформируется без заметного увеличения нагрузки. За площадкой текучести нагрузка снова растет до некоторой максимальной величины Рв, после которой на образце начинается образование местного сужения (шейки). Уменьшение сечения в области шейки вызывает снижение нагрузки, и в точке К при нагрузке Рz происходит разрыв образца. Наибольшую нагрузку Рв, при которой начинается образование шейки, называют нагрузкой предела прочности при растяжении. Пределом прочности при растяжении называют отношение наибольшей нагрузки, при которой начинается образование шейки к площади поперечного сечения образца. 11 ζв = Рв / F0.
Дата добавления: 2018-09-20; просмотров: 488; Мы поможем в написании вашей работы! |
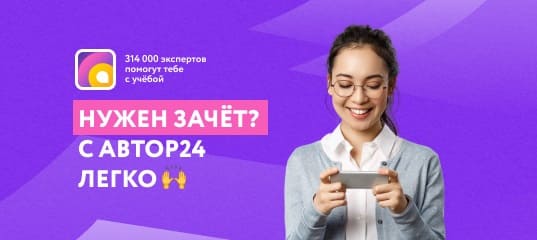
Мы поможем в написании ваших работ!