УСТРОЙСТВ И НАЗНАЧ ЛИТНИК СИСТ. СООТН СЕЧЕНИЙ
Литн система – сов каналов, по котор расплав поступает из разливочного ковша в полость формы. Осн элементы: литниковая чаша, служ для приема распл мет и подачи его в форму; стояк – канал для подачи металла из литн чаши в рабочую полость или к др элементам; шлакоуловитель, с пом которого удерж шлак и др немет примеси; питатель – через котор распл металл подводится в полость литейной формы. Для вывода газов, контроля заполн формы распл металлом и питания отливки при ее затверд служат прибыли или выпор.
Различают с питателями, располож в горизонт и вертик плоскостях.По способу подв распл в рабоч полость формы делят на: Нижняя–обеспеч спокойный подвод расплава к рабоч полости формы и постепен заполнен ее поступающим снизу, металлом. При этом усложн конструкция литн системы, увелич расход мет на нее, создается неблагоприят распределен температур в залитой форме ввиду сильного разогрева ее нижн части.
Возможно образ усадочн дефектов и внутр напряжений. При такой сист огранич возможн получ высоких тонкостен отливок (при литье алюминиевых сплавов форма не заполняется металлом, если отношение высоты отливки к толщине ее стенки превышает
,
).Верхняя. Достоинства: малый расход мет; конструкц проста; подач сверху обеспечивает благопр распредел темп Недост: струя может размыть песч форму, вызывая засоры; при разбрызг распл возник опасн его окисления и замеш воздуха в поток с обр оксидных включений; затрудн улавл шлака.
|
|
Боковая. Подвод мет осущ в ср часть отливки.Применяют при получ отливок из различ сплавов, малых и ср по массе деталей, плоскость симметри совпадает с плоск разъема формы.
1-выпор 2-литн чаша 3-стояк 4-вентиляц канал 5-шлакоуловитель 6-питатель
-суммарная площадь сечения питателя
СУЩН И СХЕМ ЛИТЬЯ В ПЕСЧ-ГЛИН ФОРМЫ. МОД КОМПЛЕКТ.
1- верх полуформа 2-ниж полуформа 3-стержень 4-выпор 5- чаша
6-стояк 78-опоки 9-вентиляция 10-штыри 12-шлакоулов 13-питатель
Изготавливают отливки из чуг, ст, цвет мет от неск гра до сот т. Сущность закл в получ отливок из распл мет, затверд в формах, которые изготовл из формов смесей путем уплотнен с использ модельного комплекта. Литейная форма сост из верхн и нижн полуформ, котор изгот в опоках – приспособлен для удержания формовочн смеси. Полуформы ориентируют с помощью штырей , которые вставляют в отверстия ручек опок. Для оброзован полостей отверст в формы уст литейные стержни, которые фиксируют посредством выступов, входящих в соотв впадины формы. Литейную форму заливают распл мет через литников сист. Литников система – совокупность каналов и резервуаров, по которым расплав поступает из разливочного ковша в полость формы. Осн элементы: литниковая чаша, прием распл мет; стояк – канал для подачи мет из литник чаши в рабоч полость или к другим элементам; шлакоуловитель, удерживает шлак и др немет примеси; питатель 13 – чере кот распл мет подвод в полость лит формы.
|
|
Мод компл–приспособления, включающие литейную модель, литн сист, стержн ящ, мод плиты, шаблоны.
Литейная модель–присп, с пом кот в литейн форм получ отпечаток, отливки. Модели разъемн и неразъемн, деревян, металлич и пластм.
Модели деревянные. Преимущ: дешево, просто, малый вес. Недост: недолговечн.Мет модели: долговечн, точность и чист раб поверхн. Изгот из алю сплавов. Модели из пластм устойч к действ влаги при экспл и хранен, легкие. Стержн ящик–формообр издел, имеющ раб полость для получ в ней литейн стержня. Обеспеч равномер уплотнен смеси, быстр извлеч стержня. Изгот из тех мат, что и мод.
ЛИТЬЕ В КОКИЛЬ, ЛИТЬЕ ПОД ДАВЛЕНИЕМ, ЦЕНТРОБЕЖНОЕ
Литьё в кокиль- сп получ фасонных отливок в мет формах — кокилях. При литье заполнен формы затвердеван происх без внеш возд, под действ силы тяж. Осн операции: очистка кокиля от стар облицовки, прогрев до 200—300°С, покрытие раб полости новым слоем облицов, простановка стержней, закрыван частей кокиля, залив мет, охлажд и удал отливки. Процесс кристаллиз при литье в кокиль ускоряется, способств получ отливок с мелкозернистым строен, хорошей герметичн и выс физ-мех св-вами. При многокр использ кокиль коробится и р-ры отливок увеличиваются. Примен: отливки из чуг, ст, алюмин, магн и др. сплаво, широко прим при серийн и крупносерийн про-ве.
Литье под давл Распл мет заливают в камеру прессования. Затем мет плунжером, под давлением 40…100 МПа, подается в полость пресс-формы, сост из неподвижной и подвижной полуформ. Внутр полость в отливке получают стержнем. После затвердеван отливка выталкивателями удаляется из раб полости пресс-формы. Перед заливкой пресс-форму нагр до 120…320 0C. После удаления отливки рабочую поверхн пресс-формы обдувают смазывают. При ЛПД темп залив сплава выбирается на 10…20 0C выше темп плав. ЛПД использ в масс и крупносерийн пр-ве отливок, с высокой точностью р-ров и малой шероховат поверхн, Недост: выс стоим, огранич габар р-ров и веса отлив, воздушн пористости в массивн частях отливки. 1-подв полуфор 2-стержень 3-неподв полуф 4-камера пресован 5-плунжер 6-выталкиват
Центробежное.Формир отливки осущ под действ центроб сил, что обеспеч выс плотн и мех св-ва отливок.
|
|
Центроб литьем изг отливки в мет, песч, оболоч формах и формах для литья по выплавл моделям на центробежн машинах. Перед работой изложницы нагревают до 200 0C.При получ отливок мет из ковша залив во вращ форму, укреплен на шпинделе, котор враща от электродвиг. Под действ центробеж сил мет прижим к стенке изложницы. Литейн форма вращ до полного затверд отливки. Изложницу уст на опорные ролики и закрывают кожухом. Изложницу приводит в движ электродвиг . Распл мет из ковшазаливают через желоб, который перемещ, что обеспеч получ равностенной отливки. Для обр раструба трубы использ песч или оболочк стержень.
|
|
Скорость вращ формы завис от диам отливки и плотн сплава, определяется по формуле:
где: – плотность сплава;
– внутренний радиус отливки.
Применен: изгот отливки из чуг, ст, титана, алюм, магн и цинка. Масса отливок от неск кг до 45т. Толщ стенок от неск мм до 350 мм. можно получ тонкостен отливки из сплавов с низкой текучестью. Недостаток: наличие усадочной пористости, ликватов и немет включен на внутренних поверхн; возможность появления дефектов в виде продольных и поперечных трещин, газовых пузырей.
ЛИТЬЕ В ОБОЛ ФОРМЫ, ПО ВЫПЛ МОДЕЛЯМ
оболочковые формы - получ отливок из распл мет в формах, изгот по горяч модельн оснастке из спец песч-смолян смесей. Формовоч смесь пригот из мелк кварц песка с добавл термореактивн связующ материалов.
Металлич модельную плиту с моделью нагр до 200…250 0C. Затем плиту закрепл на опрокидывающ бункере с формов смесью и поворач на 180 0. Под действ теплоты от модель плиты, термореакт смола в приграничн слое распл, склеивает песчинки и отверд с обр песч-смол оболочки, толщиной 5…15 мм. Модельная плита с полутверд оболочкснимается с бункера и прокаливается в печи при температуре 300…350 ?C, при этом смола переходит в тв необратимое сост. Тв оболочка снимается с модели с пом выталкиват.
Полуформы склеив или соед при помощи скоб. Формы небольш р-ров с гор плоск разъема уклад на слой песка. Формы с вертик плоск разъема и крупн формы для предохр от коробления и преждеврем разруш устанавл в контейнерыи засыпают чуг дробь.Преимущ: высокая геометрич точн, малая шероховат поверхн, низк расх формовоч мат-лов и объем мех обр.В оболочк формах изгот отливки массой 0,2…100 кг с толщ стенки 3…15 мм из всех литейных сплавов для приборов, автомобилей,
Литье по выпл моделям– получ отливок из распл мет в формах, раб полость котор образ благодаря удалению легкоплавк мат модели при ее предварит нагрев.
Выпл мод изгот в пресс-формах из модельных составов, вкл парафин, воск, стеарин, жирные кисл. Сост хорошо заполн полость пресс-формы, дает четкий отпечаток. После затвердев модельного сос пресс-форма раскрывается и модель выталкивается в хол воду.
Затем модели собир в модельные блоки с общ литников сист припаив, приклеив или мех креплением. Формы изгот многокр погруж модельного блока в спец жидкую огнеупорную смесь, налитую в емкость с послед обсыпкой кварц песком. Модельные блоки сушат на возд или в среде аммиака. Наносят 3…5 слоев огнеупорн покр с послед сушкой кажд слоя. Модели удаляют, погружая в гор воду или паром. Заливку в форму моделям произв сразу после прокалки в нагр сост. Заливка может быть свободн, под действ центробеж сил, в вакууме и т.д. Пеимущ получ точных и сложн отливок из различн сплавов массой 0,02…15 кг с толщиной стенки 0,5…5 мм. Недост сложн и длит процесса, применен спец оснастки.
Изг детали для приборостроит, авиац и др отраслей.
ВИДЫ ЛИТЕЙНОГО БРАКА ПРИЧИН ПУТИ УСТР
По внеш призн: наружн (песч раковин, перекос недолив); внутр (усад и газ раковины, горяч и холодн трещин),
Песч раковины – откр или закрытые пустоты в теле отливки, возникают из-за низк прочн формы и стержней, слабого уплотнен формы. Перекос –смещ 1-й части отливки отн др, возник в рез небрежн сборки формы, износа штырей, несоотв знаковых частей стержня на модели и в стержн ящике, неправильн устан стержня.
Недолив –некотор части отливки ост незаполн в связи с низк темп заливки, недост жидкотекуч, недост сечен эл-тов литник сист. Усадочн раковины –открытые или закр пуст в с шероховат поверхно и грубокристаллич строением. Возникают при недост питании массивн узлов, нетехнологичн конструкц отливки, заливки перегретым мет, неправ уст прибылей. Газовые раковины –открытые или закр пустоты с чист и гладк поверхн, кот возн из-за недост газопроницаемости формы и стержней, повыш влажн формов смес и стержн, насыщ расплавл мет газами. Трещины горячие и хол – разрывы в теле отливки, возник при заливке чрезмерно перегр мет, из-за неправ конструкц литн сист, отливок, повыш неравн усадки, низк податливости форм и стержн. Незначит дефекты испр заделкой замазками или мастиками, пропиткой разл составами, газовой или электр сваркой. Заделка замазками или мастиками – декоративн исправл мелких поверхн раковин. Перед заполне мастикой места очищ от грязи, обезжир. После заполн место заглаж, подсуш и затир пемзой. Пропитывание прим для устр пористости. Отливки на 8…12 часов погруж в водн р-р хлористого аммония. Проникая в промеж между кристал мет, р-р обр оксиды, заполняющ поры отливок Газовую и электро сварку прим для исправл дефектов на необрабат поверхн (раковины, сквозные отверстия, трещины). Дефекты в чуг отливках завар с использ чуг электрод и присад прутков, в сталь отливках – электродами соответств состава.
ОСН ЗАКОНЫ ОМД. КЛАС ВИДОВ ПЛАСТ ДЕФ ПРИ ОМД ПО ГУБК
Осн законы ОМД: 1.Объем и масса мет до деформ практически равен объему мет после деформ. 2.Частицы деформир мет всегда перемещ в напр наименьш сопротивл. 3. Пластической деф предшеств упругая, она снимается при снятии нагрузки. 4. При ОМД в мет возн внутр нарпяж, препятств развит пластич деф.
Различают хол и гор деформ: Хол деформ харракт изменен формы зерен, котор вытяг в напр наиболее интенсив теч мет. При холл деф формоизмен сопровожд измен мех и физ-хим св-в мет- наклепом. Возрастает прочн, уменьш пластичн. Зарожден и рост нов зерен взамен деформир, вытянут – рекристаллиз. Гор- деформ, харракт таким соотн деформир и рекристализац. Деформация при которой реккрист происх по всему объему мет, называется полной горячей деформацией. Деформация, когда рекрист происх по всему объему мет, называется неполной горячей деформациец. После хол деформ – текстурированные вытянутые зерна. При темп ниже темп рекрист в мет может иметь место процесс возврата – снятия внутр напряжений в металле. Если возврат – неполн холл дефор. нет возврата- полная холл деформ.
ВЫБОР ТЕМП ИНЛ ПРИ ОМД ПО ГУБК ВИД ПЛ ДЕФ ПРИ ОМД
Все мет имеют тенденц к увелич пластичн и уменьш сопротивл деформ при повыш темп. Мак темп нагрева- темп начала гор обраб давл следует назанач такой, чтоб избежать перегрев и пережог. При Т близкой к Т плавл наст пережог. Выраж в появл хрупк пленки мехду зерн мет, из-за окисл их границ, происх полн потеря пластичн. Неисправим, нужно отпр на переплавку. Ниже Т пережога нах Т перегрева. Прегрев закл в резком росте р-ров зерен. Исправляется отжигом. Заканч гор обр давл след также при опр Темп, ниже кот, вследств упрочн, покольку рекрист из-за сниж темп не успевает произойти, падает и в изделии возм образ трещин.
Различают хол и гор деформ: Хол деформ харракт изменен формы зерен, котор вытяг в напр наиболее интенсив теч мет. При холл деф формоизмен сопровожд измен мех и физ-хим св-в мет- наклепом. Зарожден и рост нов зерен взамен деформир, вытянут – рекристаллиз. Гор- деформ, харракт таким соотн деформир и рекристализац, при кот рекрисст успевает пройти во всем объеме загот. Деформация при которой реккрист происх по всему объему мет, называется полной горячей деформацией. Деформация, когда рекрист происх по всему объему мет, называется неполной горячей деформациец. После хол деформ – текстурированные вытянутые зерна. При темп ниже темп рекрист в мет может иметь место процесс возврата – снятия внутр напряжений в металле. Если возврат – неполн холл дефор. нет возврата- полная холл деформ.
ОБЪЕМНАЯ ШТАМПОВКА
Объемная штамповка - получения поковок, формообр полость штампа - ручей, заполн мет исходн загот и перераспр его в соотв с зад конфигурацией. Осущ при разных темп исход загот и - холодная и горячая. Исходн мат - сортовой прокат, прессов прутки, литая заготовка. Формообр осущ ручьем.
Технологич проц завис от формы поковки. По форме поковки делятся на группы: диски и поковки удлиненной формы. В зависимости от типа штампа выделяют штамповку в открытых и закрытых штампах (рис. 13.2).
Штамповка в откр штампах характериз перемен зазором между подв и неподв частями штампа. В этот зазор вытекает часть мет – облой, который закр выход из полости штампа и заст ост мет заполн всю полость. В облой выжимаются излишки мет. Можно получ поковки всех типов.
Штамповка в закр штампах. Полость штампа в процесс деформир ост закр. Зазор между подв и неподв частями штампа пост и небольш. Устр-во штампов завис от типа машин, на котор штампуют. При штамповке необх строго соблюдать рав-во объемов загот и поковки. Преимущ штамповки в закр штампах – уменьшен расхода мет из-за отсутств облоя. Поковки имеют более благоприятную структуру. Металл деформируется в условиях всестороннего неравномерн сжат при больш сжимающих напряжен, это позв получать большие степени деформации и штамповать малопластичные сплавы.
а-штамповка в откр штампах
б-штамповка в закр штампах
КОВКА
Ковка– ОМД, при котор деформир металла осущ или многократн ударами молота или однокр давлением пресса. Формообр происх за счет пластич течения мет в напр, перпендик к движ деформирующ инстр.Холодной ковке поддаются драг мет – золот, серебр; медь. Процесс холод ковки состоит из 2 операц: деформац мет и рекристаллизационн отжига.Горяч ковка примен для изгот изделий, инструмент: чеканов, зубил, молотков и т.п. Материал - малоуглеродист стали, углерод инструментальн, легированные стали. Осадка – ОМД, в рез котор уменьш высота и увелич поперечн р-ры загот.Боковая поверхность осаживаемой заготовки приобрет бочкообразн форму, это характериз неравномерн деформац. Протяжка (вытяжка) – кузнечная операция, в результате которой происходит увеличение длины заготовки за счет уменьшения площади ее поперечного сечения. Виды протяжки: Разгонка- опрерац увеличения ширины части загот за счет уменьш ее толщ. Протяжка с оправкой- операц увелич длины пустотелой загот за счет уменьш толщ ее стенок. Раскатка с оправкой– операция одновр увелич наружн и внутр диам кольц загот за счет уменьш толщ ее стенок. Прошивка– операция получ в загот сквозных или глух отверст за счет вытеснения мет. Инструм-сплошная или пустотел прошивка. Отрубка – примен для отделен от осн загот частей или для разделен загот на части. В холодн сост рубят тонк и узк полосы и прутки сечением 15…20 мм. Более толстые загот нагревают. Гибка – операц придан загот изогн формы по зад контуру Гибка сопровожд искажен первонач формы поперечного сеч загот и уменьш его площ в месте изгиба (утяжка). В качестве оборудования применяются ковочные молоты и ковочные прессы. Оборуд выбир в завис от режима ковки мет, массы поковки и ее конфиг. Необх мощн оборуд определяют по формул или таблицам. Молоты – машины динамич ударн действ. Продолжит деформац сост тысячн доли сек. Для получ поковок массой до 20 кг примен ковочные пневматич молоты, работающие на сжат воздухе. Для получ поковок массой до 350 кг прим ковочные паровоздушн молоты. Прессы ковочные гидравлич – машины статич действ.
1- рубка 2-осадка
ПРОКАТКА
Сущность: загот обжимается, проходя в зазор между вращ валками, при этом, она уменьш в попереч сеч и увелич в длину. Форма попереч сеч - профиль. При продольн прокатке деформ осущ между вращ в разные стороны валками. Попереч прокатка. Оси валков и обрабат тела параллельны или пересек под небольш углом. Оба валка вращ в 1ом напр, а заготовка круглого сеч – в противоп. Поперечно – винтовая прокатка. Валки, вращ в одну сторону, установл под углом друг другу. В кач-ве инструм примен валки прокатные, В зависим от прокатываем профиля валки могут быть гладкими ( прокатка листов, лент и т.п), калиброванными. Для получ сортового проката. Ручей – профиль на боковой поверхн валка. Промежутки между ручьями - бурты. Процесс осущ на спец прокатных станах -комплекс машин для деформир мет во вращ валках и выполнен вспомогат операций В 2хвалковых клетях осущ по одному пропуску мет в 1ом напр. Металл в 3хвалковых клетях движ в одну стор между ниж и верхн, в обратную – между ср и верхн валками.В 4хвалковых клетях устанав в опорные валки, которые позв применять рабоч валки малого диаметра, благодаря чему увелич вытяжка и снижаются деформир усилия. Процесс правки закл в 1кратном или многокр пластич изгибе искривлен участков полосы, каждый раз в обратн напр. Растяжные правильные машины используют для правки тонких листов (менее 0,3 мм), трудно поддающихся правке на роликоправильных машинах. Правильные машины с косо располож гиперболоидальн роликами предназн для правки труб и круглых прутков
продольн поперечн попер-винт 4валковая клеть
2валк клеть
ВОЛОЧЕНИЕ
Сущн закл в протягиван загот через фильеру в волоке. Конфигур отверстия определ форму получ профиля.
Вол-ем получ проволоку диам 0,002…4 мм, прутки и профили фасонн сеч, тонкостен трубы, в т.ч. и капиллярные. Волочен прим также для калибровк сеч и повыш кач-ва поверхн обрабат издел. Исходн матер - горячекатаный пруток, сортовой прокат, проволока, трубы. Осн инструмент – волоки различ конструкции. Волока раб в сложн услов: больш напряжен, износ при протяг, их изгот из тверд сплавов. Волока закрепл в обойме. Волоки имеют слож конфигур, ее сост части - заборная часть, (входной конус и смазочн часть; деформирующая часть с углом в верш
(6…18 0 – для прутков, 10…24 0 – для труб); цилиндрич калибрующий поясок длиной 0,4…1 мм; выходной конус. Технологич процесс осущ на спец волочильн станах. В завис от типа тянущ устр-ва различ станы: с прямолинейным движен металла; с наматыванием обрабат мет на барабан. Станы барабанного типа примен для получ проволоки. Число барабанов до 20. Скорос до 50 м/с
Обычно за один проход коэф вытяжки не превыш 1,3, степень деформации
– 30 %. При необх получить большую величину деформ производят многократное волочение. Коэф вытяжки – отн конечн и нач длины или нач и конечн площ поперечн сеч.
ПРЕССОВАНИЕ
Прессование – ОМД, при кот металл выдавл из замкн полости через отверстие в матрице, соотв сеч профиля.
Получ профильные загот: прутки диам 3…250 мм, трубы диам 20…400 мм с толщ стен 1,5…15 мм, профилей сложного сечения сплошных и полых с площадью поперечного сечения до 500 см2.
Произв на гидравлич прессах с вертикал или гор расп плунжера.
Методы прессован: При прямом прес движен пуансона и истечение мет через отверст матрицы происх в 1ом напр. Требуется приклад больш усилие. Пресс-остаток сост 18…20 % от массы загот.
При обратном прессован загот заклад в глухой контейнер, и она при прес остается неподвиж, а истечение мет из отверстия матрицы, происх в напр, обратном движению пуансона с матрицей. Требует меньш усилий, пресс-остаток - 5…6 %. При прес металл подверг всесторон неравномер сжатию, имеет высокую пластичн.
Преимущ: обр мет, которые из-за низкой пластич другими методами обработать невозможно; получ любого профиля попереч сеч; получ широкого сортамента изделий на 1ом прессовом оборудов с заменой матрицы; высокая производит, до 2…3 м/мин. Недост: повыш расход мет на единицу изделия из-за потерь в виде пресс-остатка; появление заметной неравномерн мех св-в по длине и поперечн сеч изделия; выс стоимость и низкая стойкость прессового инструмента; высокая энергоемкость.
1 – гот пруток; 2 – матрица; 3 – загот;
4 - пуансон
прямой метод обратный метод
ЛИСТОВАЯ ШТАМПОВКА
Листовая штамповка – ОМД, при кот листовой материал деформ в холод или подогрет сост.
При формообраз операц стремятся получ зад величину деформации, чтобы заг приобрела требуемую форму. Разделительные операции предназн или для получ заг из листа или ленты, или для отделения 1ой части загот от другой. Операции могут выполн по замкн или по незамкн контуру. Отрезка – отделение части загот по незамкн контуру на спец маш – ножницах или в штампах.Применяют как заготовительн операц для разделен листов на полосы и загот нужных р-ров. Вырубка и пробивка – отделение мет по замкн контуру в штампе. Вырубкой оформляют наружн контур детали, пробивкой – внутр контур. Гибку произв в штампах, а также вращающимися фигурными роликами, играющими роль матрицы, на профилегибочных станах. Вытяжка – обр полого изделия из плоск или полой загот. Отбортовка – получение борта диаметром
путем вдавливан центральн части загот с предварительно пробитым отверст
в матрицу Раздача – увелич периметра поперечн сеч концевой части полой заг коническим пуансоном. Обжим – уменьш периметра поперечн сеч концевой части полой заг. Рельефная формовка – местное деформир загот с целью образован рельефа в результате уменьшения толщины заготовки. Инструмент – штамп. Штампы для лист штамповк делятся по технологич признаку в завис от операции: вырубные, гибочные, вытяжные и т.д. В завис от числа выполн операц различ одно- и многооперацион штампы. Многооперацион штампы бывают последовательн действия, в которых операц выполняются послед при перемещен заг по неск рабоч позиц штампа, и совмещен действ, в кот операции выполн на одной позиции.
пробивка вытяжка
Дата добавления: 2018-08-06; просмотров: 227; Мы поможем в написании вашей работы! |
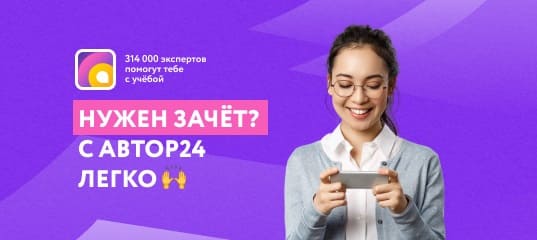
Мы поможем в написании ваших работ!