ПР-ВО СТАЛИ В ЭЛЕКТРОДУГ И ИНДУКЦИОН ПЕЧАХ
ОПРЕДЕЛ. ХАР-К ПРОЧН И ПЛАСТИЧ. ИСПЫТ НА РАСТЯЖЕНИЕМех св-ва- св-ва, которые проявляет мет при внешнем силовом воздействии. Для испытаний использ разрывные машины. Для испыт изготавливают цилиндрические или плоские образцы исслед материала. расчет мех св-в осуществляется по диаграмме растяжения. Усилие Рпц – предел пропорциональности, напряжение σпц-предел пропорциональности. для Рпц удлиннение пропорционально усилению растяжения и при его снятии форма восст. Рт – усилие предела текучести, деформация образца происх без ее увеличения. Рв– максимальное усилие которое выдерживает образец при растяжении - Ртах. σв– временное сопротивление. При испытаниях на растяжение определяются характеристики пластичности сплава:относит удлин относит сужен поперечн сужен ТВЕРДОСТЬ МЕТАЛЛОВ МЕТОДЫ ЕЕ ОПРЕДЕЛЕНИЯТвердость – способность материала сопротивляться упруго-пластич деформации, при внедрении в него более твердого тела. Методы измер твердости: статического и ударного вдавливания, царапин, отскока и др. Твердость оценивают по разным критериям. Измерение твердости по Бринеллю: о твердости судят по глубине отпечатка – чем мягче, тем больше. Деталь уст на столик и подводят к индентору до упора. Индентор-стальн закален шарик. на шарик диаметром D действ усилие Р от которогошарик вдавливается в пов-ность мет, за время t. Тверд по бринеллю - отношение усилия Р к площади получ отпечатка Испытание действительно, если D отпечатка =0.24-0.6D.метод позволяет измерять твердость от 8 до 450 единиц НВ закаленным шариком. Измерение твердости по Роквеллу: Для вдавливания в материал исп индентор в виде алмазного конуса, с углом 120, а также закаленного шарика диаметром 1,588 мм. Шариковый индентор позволяет определить твердость до 250 НВ. Индентор в виде алмазного конуса используется для измерения твердости закаленных сталей и др. ПРОИЗВОДСТВО ЧУГУНА В ДОМЕННОЙ ПЕЧИЧугун выплавляют в дом печах. Сущность: восстановление оксидов железа, входящих в сост руды оксид углерода, водородом и тверд углеродом, выделяющимся при сгор топлива. При выплавке происх: Восст железа из окислов руды, науглероживание и удаление в виде жидк чугуна опр хим состава. Оплавление пустой породы руды, обр шлака, растворение в нём золы кокса и удаление его из печи. Горение топлива. Вблизи фурм природный газ и углерод кокса, взаимодействуя с кислородом воздуха, сгорают: Продукты сгор взаимодейств с раскален коксом по реакц: Горяч газы, , отдают теплоту шихтовым материал и нагревают их, охлаждаясь до 300…400 0С у колошника. Восст железа происх по мере продвижен шихты вниз по шахте и повышен температуры от высш оксида к низш, в неск стадий: Восст коксом - прямое, протекает в нижн части печи (зона распара), где более высокие температуры, по реакции: . Восст газами ( и ) - косвенное, протекает в верх части печи при с низких температурах, по реакциям: В ниж части печи обр шлак в рез сплавления окислов пустой породы руды, флюсов и золы топлива. Шлаки содерж . Шлак образуется постепен, его сост меняется по мере стекан в горн, где он скапливается на поверхн жидк чугуна, благодаря меньшей плотности. Литейный чугун примен после переплава на заводах для получения фасонных отливок. Ферросплавы – сплавы железа с кремнием, марганцем и др элементами применяют для раскислен и легир стали. Побочные продукты домен плавки - шлак и доменный газ. Из шлака изготовляют шлаковату, цемент, удобрен, доменный газ использ как топл для нагре воздуха, вдуваемого в печь. Коэффициент использования полезного объёма доменной печи (КИПО) – это отношение полезного объема печи V (м3) к ее среднесуточной производительности Р (т) выплавленного чугуна. (м3/т). Удельный расход кокса, К –отношение расхода кокса за сутки А(т) к кол-ву чугуна, выпл за это же время Р(т). Удельн расход кокса в домен печах сост 0,5…0,7 (для передовых – 0,36…0,4) НАЗНАЧ И СОСТ КОМПОНЕНТОВ ШИХТЫ Шихта — смесь материалов, в опр пропорции, подлежащая переработке в металлургич, химич и других агрегатах. Шихтами называют исходные смеси, использующиеся в пирометаллургич или иных высокотемпературных процессах. В состав металлургич шихт обычно входят исходн или обогащённое рудное сырьё, сырьё с флюсами и оборотными материалами. Шихты в чёрной металлургии зачастую содержат и топливо. Типичные требования к качеству шихты определяются обеспечением стабильности и воспроизводимости результатов процесса, в котором она используется: постоянство химического состава; однородность по химическому, минералогическому и гранулометрическому составу; оптимальная крупность компонентов шихты; оптимальная влажность. Шихта состоит из железной руды 40% (окислы железа), известняк 15-20%, возврата мелкого агломерата 20-30% коксовой мелочи 4-6%, влаги. назначение флюсов состоит в том, чтобы, перевести тугоплавкие окислы в жидкое состояние. Агломерация – спекание шихты, при которой из нее удаляются вредные примеси, разлогаются карбонаты. ПОЛУЧ СТАЛИ В КОНВЕРТЕРЕСтали – железоуглерод сплавы, содерж практически до 1,5% углерода. Осн исходн мат для пр-ва стали-передельный чугун и стальной лом (скрап). Кислородно-конвертерный процесс – выплавка стали из жидкого чуг в конвертере с осн футеровкой и продувкой кислородом через водоохлаждаемую фурму. Кислородный конвертер – сосуд грушевидной формы из сталь листа, футерованный кирпичом. Вместимость конвертера – 130…350 т жидк чугуна. Шихтов матер - жидкий передельный чугун, стальной лом (не более 30%), известь, железная руда, а также боксит плавиковый шпат для разжижения шлака. Перед плавкой вконвертер наклоняют, с помощью завалочных машин загружают скрап, заливают чугун при температуре 1250…1400 0C. После этог внутрь вводят охлаждаемую фурму и через неё подают кислород под давлением. Одновременно с началом продувки загружают известь, боксит, железную руду. Кислород проникает в металл, вызывает его циркуляцию в конвертере и перемешивание со шлаком. Оксид железа растворяется в шлаке и металле, обогащая металл кислородом. Растворенный кислород окисляет кремний, марганец, углерод, и их содержание падает. Происходит разогрев металла теплотой, выделяющ при окислен. Фосфор удаляется в нач продувки ванны кислородом Сера удаляется в теч всей плавки Подачу кислорода заканч, когда содержание углерода в металле соответствует заданному Плавка в конвертерах вместимостью 130…300 т заканч через 25…30 минут. В кислородных конвертерах выплавляют стали с различным содержанием углерода, кипящие и спокойные, а также низколегированные стали. Легирующие элементы в расплавленном виде вводят в ковш перед выпуском в него стали.
|
|
|
|
|
|
|
|
ПР-ВО СТАЛИ В ЭЛЕКТРОДУГ И ИНДУКЦИОН ПЕЧАХ
Дуговая печь питается трёхфазным переменным током. Имеет три цилиндрич электрода из графитизир массы, закреплённых в электрододержателях,. Между электродом и металлической шихтой возникает электрич дуга. Корпус печи имеет форму цилиндра. Снаружи заключён в прочный стальной кожух, внутри футерован кирпичом. Вместимость печей составляет 0,5…400 тонн. В основной дуговой печи осуществляется плавка двух видов:
на шихте из легированных отходов ведут без окисления примесей. Так выплавляют легированные стали из отходов машиностр заводов.
Плавка на углеродистой шихте - производства конструкц сталей. Шихта плавится. Оксид кальция из извести и оксид железа образуют осн железистый шлак, способствующий удалению фосфора из металла. После прекращения кипения удаляют шлак. далее удаление серы и раскисл мет зад хим состава. Для опр хим сост мета берут пробы выплавляют высококачественные углеродистые стали – конструкционные, инструментальные, жаростойкие и жаропрочные.
Индукционные тигельные плавильные печи
Выплавляют коррозионно-стойкие, жаропроч и др. Вместимость от дес кг до 30 т.
Печь сост из индуктора, внутри кот нах тигель , через индуктор от генератора выс част прох однофазн переменный ток повыш частоты (500…2000 Гц). При пропуск тока через индуктор в металле, индуцир мощные вихревые токи, обеспеч нагрев и плавление металла. Под действ электромагнит поля индуктора при плавке происх интенс циркуляция жидк металла, что способств ускорен хим реакций, получению однородн по хим сост металла, быстрому всплыванию неметаллич включен, выравниванию температуры. В индукционных печах выплавляют сталь и сплавы из легир отходов методомпереплава, или методом сплавления.
После распл шихты на поверхность металла загружают шлаковую смесь для уменьшения тепловых потерь металла и уменьшения угара легирующих элементов, защиты его от насыщения газами.
В печах можно получать стали с незначительным содержанием углерода и безуглеродистые сплавы, так как нет науглероживающей среды.
При вакуумной индукцион плавке индуктор, тигель, дозатор шихты и изложницы, помещают в вакуумн камеры. Получ сплавы выс кач-ва с малым содерж газов, неметаллич включ и сплавы, легированные любыми элементами.
РАЗЛИВКА СТАЛИ В СЛИТКИ
Из ковша сталь разливают в изложницы или кристаллизаторы. В изложницах или кристаллизаторах сталь затвердевает и получают слитки, которые подвергаются прокатке, ковке.Изложницы – чугунные формы для изготовления слитков. Сталь разливают в изложницы сверху. недостатки менее качественную поверхность слитков, из-за наличия пленок оксидов от брызг металла, затвердевающих на стенках изложницы.Применяется для разливки углеродистых сталей.
При сифонной разливке одновременно заполняются несколько изложниц. Изложницы устанавливаются на поддоне, в центре которого располагается центровой литник, футерованный огнеупорными трубками, соединённый каналами с изложницами. Жидкая сталь из ковш поступает в центровой литник и снизу плавно, без разбрызгивания наполняет изложницу . Поверхность слитка получается чистой, можно разливать большую массу металла одновременно в несколько изложниц. Используют для легированных и высококачественных сталей.
Непрерывная разливка сост в том, что жидк сталь из ковша непрерывно подают в водоохлаждаемую изложницу без дна – кристаллизатор, из нижней части которого вытягивается затвердевающий слиток. Перед заливкой металла в кристаллизатор вводят затравку – стальную штангу со сменной головкой, которая в начале заливки служит дном кристаллизатора. Жидкий металл у стенок кристаллизатора и на затравке затвердевает, Затравка движется вниз при помощи тяговых роликов, постепенно вытягивая затвердевающий слиток из кристаллизатора. После прохождения тяговых роликов, затравку отделяютСлитки имеют плотное строение и мелкозернистую структуру, отсутствуют усадочные раковины.
СТРОЕНИЕ СЛИТКА СТАЛИ
Залитая в изложн сталь отдает тепло ее стенкам, поэтому затвердевание начинается у стенок.
Толщина корки увеличивается. Кристализация заканчивается приблизительно вблизи его продольной оси
В основе кристаллизации лежат явления образования зародышей новой фазы, рост зародышей (центров кристаллизации).
Спокойная сталь затвердевает без выделения газов, в верхней части литка образуется усадочная раковина. Для устранения усадочных дефектов слитки отливают с прибылью. Слиток спокойной стали имеет тонкую наружную корку, зону столбчатых кристаллов, зону равноосных кристаллов.
Дентритная ликвация-неоднородность в пределах одного кристалла. Зональная ликвация-неоднородность в различных чатях слитка.
В кипящей стали не образуется усадочной раковины, она перераспределяется на газовые поры. Кипение влияет на зональную ликвацию. Для уменьшения ликвации кипение после заполнения изложницы прекращают, накрывая слиток металлической крышкой, либо раскисляют металл алюминием.
Полуспокойная сталь имеет преимущества спокойной и кипящей стали и не имеет их недостатков.
МЕТОДЫ ПОВЫШЕНИЯ КАЧЕСТВА СТАЛИ
Обработка сталей синтетич шлаком 45%-СаО(jосновный), 55%-Al2O3(кислотный)
Реакции: FeS+CaO—Fe2O+CaS, Fe+P+CaO—(CaO)4*P2O5+Fe на 0.001% уменьш Р и С
Вакуумная дегазация В ковше ковш с жидкой сталью помещают в камеру, закрывающуюся герметичной крышкой. насосами создают разрежение. При понижении давления из жидкой стали выделяются водород и азот. Всплывающие пузырьки газов захватывают неметаллические включения, в результате чего содержание их в стали снижается. Улучшаются прочность и пластичность стали.
Электрошлак переп Источник теплоты -шлаковая ванна, нагреваемая электрич током. Электрический ток подводится к переплавляемому электроду, погруженному в шлаковую ванну, и к поддону. Выделяющаяся теплота нагревает ванну до температуры свыше 1700C и вызывает оплавление конца электрода. Капли жидкого метпроходят через шлак и образуют под шлаковым слоем металлич ванну. Перенос капель металла способств удалению из металла серы, немет включ и газов. Мет ванна пополняется путём распл электрода, и постепенно формируется в слиток. Содерж О2 уменьш в 1,5…2 раза, серы в 2…3 раза. Слиток имеет выс плотн, однородн, хор кач-во поверхн, Выс мех и эксп св-вами.
1-шлак 2-затравка 3-электрод 4- кристализат 5-капля Ме
Вакуумно-дуговой переплав осущ в вакуумно-дуговых печах с расходуемым электродом. Катод изготовляют мех обр слитка . Расходуемый электрод закрепляют на водоохл штоке и помещ в корпус печи и в медную водоохлажд изложницу. Из печи откач воздух до остаточн давлен 0,00133 кПа. При подаче напряжения между расходуем электр (катодом) и затравкой (анодом) возникает дуга. Теплота расплавляет конец электрода. Капли жидк мет, проходя зону дугового разряда, заполняют изложницу и затвердевают. Дуга горит между на протяжении всей плавки. Неметаллич включения сосредоточ в верхн части слитка, усадочн раков мала. Слиток имеет выс равномерност хим сост, повыш мех св-ва.
1-корпус 2-электрод 3-капля Ме 4-слиток 5-затравка
КЛАССИФИКАЦИЯ И МАРКИРОВКА УГЛЕРОД И ЛЕГИР СТАЛЕЙ
1.Углеродистые стали обыкновенного кач-ва: 3 группы
ГРУППА А: Длясталей группы А ГОСТ гарантирует определенный уровень мех свойств при комнатной температуре. Состав стали не фиксирован. Стали группы А нельзя подвергать термообработке.
ГРУППА Б. Стали группы Б обозначаются также, как и стали группы А. Для них ГОСТ гарантирует хим состав. Перед маркировкой может добавляться буква, указывающая на способ получения стали: К- конвектор, М-мартеновская печь, Б-бисимеровский метод.
ГРУППА В: Для сталей ГОСТ гарантирует хим состав и мех св-ва.
2. Углеродистые качественные конструкционные стали: сталь08, сталь10, сталь 15…….сталь85. Цифра показывает содержание углерода в сотых %, содержание Р,С<=0,03%.
3. Углеродистые инструментальные стали. У7, У8…..У13, цифра показ содерж углерода в десятых %, S, Р<=0,02% более кач чем конструкцион.
3. Легированные стали. Существует болшое число легирующих компонентов, напримерВ-вольфр(жаропрочн), ф-ванад(прочность, тверд), М-молибден (корозион). Если в конце маркировки есть буква А, то это сталь повыш кач-ва.
4. Быстрорежущая сталь. Р19- легир б-р стл 19%-вольфр С=1%
5. Шарикоподшипниковая сталь. ШХ15 1,5% хрома, С=1%
6. Электротехнические ЭС 30 С=0,5-0,7%, кремния 3%
Дата добавления: 2018-08-06; просмотров: 187; Мы поможем в написании вашей работы! |
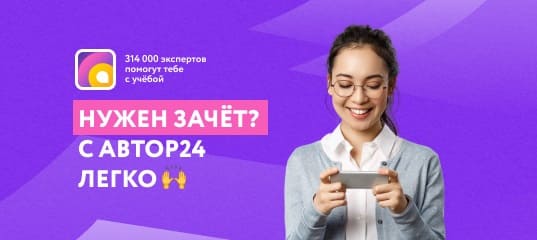
Мы поможем в написании ваших работ!