Наблюдения за поведением образцов при испытаниях
9.2.1 В процессе испытаний, кроме отсчетов по индикаторам, производят наблюдения за различными изменениями в образце (появление треска, перекоса, трещин и т. п.), фиксируемыми в журнале с отметкой моментов времени.
9.2.3 После разгрузки разрушенного образца производят его осмотр (фотографирование) с описанием характера разрушений.
Правила обработки и оценка результатов испытаний
10.1 Определение деформаций соединений
10.1.1 По записанным в журнале испытаний показаниям приборов вычисляют:
— полные деформации и их разности при испытаниях с непрерывным нагружением;
— остаточные за цикл и упругие деформации при испытаниях с периодической нагрузкой.
По вычисленным данным строят диаграммы деформаций с точностью до 0,01 мм.
10.1.2 Для испытанных соединений I группы на графике разности полных деформаций dn в зависимости от усилия F проводят в начальном его участке по точкам усредненную прямую, ордината последней точки которой соответствует величине усилия FI-II. По величине FI-II оценивают несущую способность соединения.
10.1.3 По диаграмме деформаций соединений I группы находят абсолютные величины:
— начальной деформации, которая определяется отрезком, отсекаемым на оси абсцисс продолжением графически построенной в области упругих деформаций линии диаграммы полных деформаций;
— полной деформации dI-II при значении усилия FI-II;
— максимальной полной деформации dmax при разрушающем усилии Fmax или вблизи него.
|
|
Оценка несущей способности соединений
10.2.1 Оценку несущей способности соединений производят на основании сопоставления факти-
ческой несущей способности Rsup с расчетной несущей способностью Rd, которая установлена на ис-
пытываемое соединение.
10.2.2 Фактическую несущую способность соединения Rsup в зависимости от продолжительности
испытаний определяют по формулам:
а) для пластического разрушения
(2)
где Fmax — максимальная разрушающая нагрузка, кН;
— коэффициент надежности при пластическом разрушении соединения, определяемый по формуле
(3)
здесь t — время, приведенное к неизменному действию нагрузки, с, равное
— время доведения нагрузки до разрушающей величины Fmax, с;
б) для хрупкого разрушения
(5)
где — коэффициент надежности при хрупком разрушении соединения, определяемый по формуле
(6)
10.2.3 Несущую способность соединения I группы при хрупком разрушении оценивают неравенством
(7)
где Rd — расчетная несущая способность.
При невыполнении неравенства (7) расчетная несущая способность Rd соединения должна быть снижена до величины
(8)
10.2.4 Несущую способность соединения I группы при пластическом характере разрушения определяют неравенством (9)
|
|
При невыполнении неравенства (9) расчетная несущая способность Rd соединения должна быть
снижена до величины (10)
10.2.5 Несущую способность соединения II группы оценивают неравенством (11)
с дополнительной проверкой по неравенству (2) в том случае, если разрушение образцов соединения
произошло с нарушением сплошности материала их элементов.
При невыполнении неравенства (11) расчетная несущая способность Rd соединения должна
быть снижена до величины
(12)
а при невыполнении неравенства (2) — до величины (13)
11 Правила оформления результатов испытанийРезультаты испытаний и расчетов, выполненных в соответствии с настоящим стандартом, заносят в протокол, хранящийся в лаборатории, проводившей испытания, и в отделе технического контроля изготовителя.
Требования к пиломатериалам
Пиломатериалы по видам обработки разделяют на обрезные, односторонне-обрезные и необрезные; по размерам – на доски, бруски и брусья.
Номинальные размеры толщины и ширины обрезных пиломатериалов с параллельными кромками и толщины односторонне-обрезных, необрезных и обрезных пиломатериалов с непараллельными кромками должны соответствовать указанным в таблице 1 стб 1713-2007.
|
|
Ширина узкой пласти, измеренная в любом месте длины необрезных пиломатериалов, должна быть:
- для толщин от 16 до 50 мм включительно не менее 50 мм;
- свыше 50 до 100 мм включительно не менее 60 мм;
- свыше 100 до 300 мм не менее 0,6 толщины.
Ширина пласти обрезных пиломатериалов с непараллельными кромками в узком конце должна быть:
- для толщин от 16 до 50 мм включительно не менее 50 мм;
· свыше 50 до 100 мм включительно не менее 60 мм;
· свыше 100 до 300 мм не менее 0,7 толщины.
Номинальные размеры пиломатериалов по толщине и ширине установлены для древесины с влажностью 20 %. При влажности древесины более или менее 20 % размеры пиломатериалов должны быть установлены с учетом величины усушки по ГОСТ 6782.1.
Номинальные размеры пиломатериалов по длине устанавливают:
· от 0,5 м до 2,0 м включительно с градацией 0,10 м;
· свыше 2,0 до 6,5 м с градацией 0,25 м.
По согласованию с потребителем допускается изготовлять пиломатериалы других размеров.
Предельные отклонения по длине пиломатериалов от 0 до + 3 % от номинальной длины, но не более + 50 мм - с учетом требований [1].
Предельные отклонения по толщине, мм:
- при размерах до 39 мм включительно ± 1,0;
- от 40 до 100 мм включительно от + 2,0 до минус 1,0;
|
|
- более 100 мм от + 3,0 до минус 2,0.
Предельные отклонения по ширине, мм:
- при размерах до 100 мм включительно от + 2,0 до минус 1,0;
- более 100 мм от + 3,0 до минус2,0.
Предельные отклонения от номинальных размеров по толщине и ширине пиломатериалов приведены с учетом требований [2].
Условное обозначение пиломатериалов при записи в документах и при заказе должно состоять из наименования пиломатериала (доска, брусок, брус), цифры, обозначающей сорт, наименования группы пород (хвойные) или отдельной породы (сосна, ель и др.), цифрового обозначения поперечного сечения (для односторонне-обрезного и необрезного пиломатериала - толщины) и обозначения настоящего стандарта.
Пример – Условное обозначение пиломатериалов:
Брусок – 2 – сосна – 75 × 100 – СТБ 1713-2007.
Доска – 2 – хв. – 25 – СТБ 1713-2007.
Пиломатериалы изготовляют сухими (с влажностью не более 22 %), сырыми (с влажностью более 22 %) и сырыми антисептированными. Антисептирование – по ГОСТ 10950.
Параметр шероховатости поверхности пиломатериалов Rmmax не должен превышать 1250 мкм для отборного, 1-го, 2-го и 3-го сортов, а для 4-го сорта - 1600 мкм по ГОСТ 7016.
Содержание цезия-137 в древесине пиломатериалов не должно превышать уровня, указанного в [3].
Непараллельность пластей и кромок в обрезных пиломатериалах, а также пластей в необрезных пиломатериалах допускается в пределах отклонений от номинальных размеров, установленных в разделе 4.
Пиломатериалы должны быть рассортированы по видам обработки (обрезные, односторонне-обрезные, необрезные), по размерам, сортам (группе сортов), породам (группе пород).
Примечание - Допускается поставлять обрезные пиломатериалы длиной до 2 м включительно, шириной до 150 мм включительно и толщиной до 25 мм включительно группой сортов (включая сочетания отдельных сортов или все сорта).
Сорт, размеры, порода, а также дополнительные требования к пиломатериалам, не влияющие на сортообразующие параметры качества, должны быть указаны в спецификации к контракту (договору).
Оценка качества пиломатериалов должна производиться по пласти или кромке, худшей для данной доски, а брусков и брусьев квадратного сечения - по худшей стороне.
Качество пиломатериалов должно соответствовать требованиям, указанным в таблице 2.
Требования к бревнам
Партия изделий из оцилиндрованного бревна (далее по тексту - изделия), произведенных для одного домостроения, должна состоять из бревен преимущественно одной породы.
Для изготовления изделий должны быть использованы бревна естественной влажности (влажность не нормируется), заготовленные из растущих деревьев. Использование бревен из сухостойных (засохших до рубки) деревьев не допускается.
На изделиях не допускаются: гниль, червоточина, трещины, сколы и механические повреждения обработанной поверхности и торцов. Для выявления этих недостатков проводится визуальный контроль каждого изделия.
Не допускается отклонение диаметра изделия (D) более чем на 2 мм от номинального диаметра, указанного в спецификации. Контрольные замеры диаметра должны производиться при помощи кронциркуля у каждого изделия по всей его длине.
Не допускается кривизна изделий со стрелой прогиба (H) более 0,5% от длины изделия. Измерение стрелы прогиба кривизны проводят с помощью шнура и линейки на поверхности изделия, по всей окружности изделия.
Не допускается отклонение продольных размеров изделия (L) более чем на 2 мм от значений, указанных в спецификации. Контрольные замеры должны производиться у каждого изделия по всей его длине
Не допускается нарушение продольной геометрии изделия (винт). Ребра теплового замка должны лежать в одной плоскости (Q).
Ширина теплового замка (F) должна быть равна радиусу (R) изделия. Не допускается отклонение ширины теплового замка более чем на 2 мм.
Радиус дуги теплового замка (R1) должен быть равен радиусу (R) изделия.
Не допускается отклонения глубины теплового замка более чем на 2 мм по всей длине изделия. Контрольные замеры производятся при помощи рейки и линейки у каждого изделия по всей его длине.
Радиус окружности обработанной поверхности чашек(R2) должен быть равен радиусу изделия (R). Обработанная поверхность чашек должна иметь строго цилиндрическую форму. Поверхность шаблона должна плотно, без зазоров прилегать к поверхности чашки. Не допускаются зазоры более чем 2 мм.Оси чашек (Х) должны перекрещиваться с продольной осью бревна (У) под углом 90 градусов.
Складирование, хранение, пакетирование, погрузка, транспортировка и разгрузка изделий должны исключать механические повреждения и загрязнение поверхности. При этом обращать особое внимание на чистоту кузова транспортного средства и, при необходимости, производить его уборку перед погрузкой изделий. Но дно кузова необходимо укладывать опорные рейки, на которые осуществляется равномерная укладка изделий
Дата добавления: 2018-08-06; просмотров: 384; Мы поможем в написании вашей работы! |
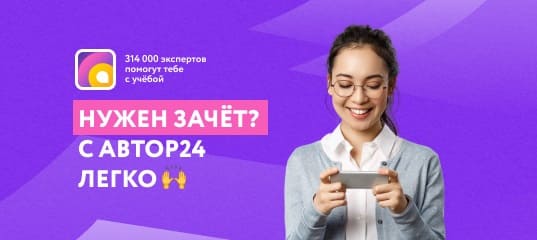
Мы поможем в написании ваших работ!