Динамическая модель эквивалентной упругой системы
Динамическая модель эквивалентной упругой системы плоскошлифовального станка приведена на рис. 1.7.
На данном рисунке приняты следующие обозначения:
СY1, CY2, CY3, CY4 – жесткости в направлении оси Y;
HY1, HY2, HY3, HY4 – коэффициенты демпфирования в направлении оси Y.
Основой построения математической динамической модели является уравнение колебаний одномассовой упругой системы (рис.1.8).
Это уравнение представляет собой дифференциальное уравнение второго порядка:
На рис.12. и в данном уравнении приняты следующие обозначения: M – масса, H – коэффициент демпфирования, C – жесткость, – возбуждающая сила, действующая в данном направлении, t – время, x - перемещение,
- скорость,
- ускорение,
- «обратная сила».
Рис 1.7. Динамическая модель эквивалентной упругой системы плоскошлифовального станка
Рис 1.8. Динамическая одномассовая модель
Смысл понятия «обратная сила» заключается в следующем – рис 1.9. ( на нем буквой «З» обозначена заготовка).
Рис 1.9. Иллюстрация понятия «обратная сила»
Под действием силы F(t) возникает смещение x упругой системы станка и, как следствие, уменьшение глубины резания, отсюда сила F(t) уменьшается на величину U(t) .
Итак, необходимо определить геометрическую сумму смещений эквивалентной упругой системы вдоль оси Y, которое определяет суммарное смещение оси вращения шпинделя от прямолинейного движения
Имея данные об упругих перемещениях несущей системы (шпинделя относительно детали) за n – е количество оборотов шпинделя можно определить величину непрямолинейности поверхности детали, получаемую после шлифования.
|
|
Деталь рассматривается как неподвижная, а все упругие перемещения
Однако, траектория перемещения оси шпинделя в координатах детали имеет форму сложной кривой 1. Это вызвано неравномерной жесткостью узлов, наличием упругих люфтов в стыках и т.д.
Таким образом, траектория движения торца шлифовального круга, полученная при его вращении, образуется при сложении двух движений:
1. Вращательного движения круга вокруг оси шпинделя.
2. Перемещения оси шпинделя по траектории 1 (смещение систем координат XшпO1Yшп и XoOYo).
Поэтому траектория движения торца шлифовального круга будет отличаться от идеальной. И это, в свою очередь, определит образование непрямолинейности шлифуемой поверхности.
Шлифовальному кругу сообщается круговое движение Vк, детали - продольное движение Vз. В процессе резания возникает сила резания, составляющая PY которой вызовет деформацию замкнутой технологической системы станка на величину y1, поэтому tф = t – y1. Кроме этого на глубину шлифования оказывает влияние и перемещение заготовки вдоль оси X. Оно имеет скачкообразный характер. В момент выхода шлифовального круга из контакта с заготовкой упругая система станка «выбирает» деформацию технологической системы y1. В момент врезания круга в заготовку глубина резания tф’ = t. Все это вместе взятое определяет характер образования непрямолинейности шлифуемой поверхности.
|
|
Для реализации имитационного моделирования процесса шлифования был применен программно – методический комплекс МИК (моделирования и конструирования). При его применении модель динамического процесса представляется в виде структурной модели. Затем с помощью специального языка вводятся параметры модели и осуществляется компьютерный эксперимент.
Согласно метода точности обработки, элементарные погрешности определяемые действием каждого из приведенных выше факторов, принимаются практически независимыми друг от друга. Их суммирование производят по вероятностному методу:
где – количество учитываемых погрешностей;
– коэффициент, учитывающий закон распределения i – ой погрешности (
) для разных законов распределения, например, для нормального закона распределения k = 1;
- i – я элементарная погрешность обработки [27].
|
|
Пример: расчет одной из составляющих погрешностей обработки, вызванной неточностью настройки инструмента на размер для станков с ЧПУ.
Современные приборы для настройки инструментов на размер имеют высокую разрешающую способность: цена деления координатных шкал 1мкм и оптическое увеличение проектора до 30 раз. Однако, сколь бы высокой ни была точность исполнения прибора, инструмент всегда настраивается с некоторыми отклонениями. Они складываются из погрешностей самого прибора ( ) и погрешностей установки на станке настроенного на размер инструмента (
).
По правилам сложения случайных величин погрешность положения вершины настроенного на размер инструмента равна:
где k1, k2, k3, k4, k5, k6, k7, k8 – коэффициенты, учитывающие законы распределения погрешностей;
- погрешность шкал отчета прибора;
- погрешность отсчета размера по шкалам;
- неточность совмещения вершины инструмента с перекрестием экрана проектора;
- не совмещение начал отсчета шкал и устройства для крепления инструмента;
- погрешность от неточности углового расположения на приборе устройства для крепления инструмента;
- несовпадение нуля отсчета координат инструмента с теоретическим положением из – за неточностей расположения поверхностей, базирующих инструмент на станке;
|
|
- погрешность от неправильного углового расположения на станке базирующих поверхностей;
- погрешность в связи с деформациями элементов, участвующих в зажиме инструмента.
Пусть
Тогда
.
В технологических справочниках приведены среднестатистические данные по точности обработки детали на станках. Все они получены статистическими методами на основе обработки результатов экспериментов. Основной недостаток определения точности обработки по среднестатистическим данным состоит в том, что при этом невозможно учесть индивидуальные особенности конкретных станков. Станки даже одной модели отличаются друг от друга по точности из–за различного износа, разной точности сборки и т.д. В идеальном случае необходимо иметь данные по точности каждого станка, причем эти данные должны периодически обновляются. Т.е. нужны математические модели, представляющие точность обработки деталей на станках, реальные, учитывающие динамические процессы, протекающие в конкретной технологической системе СПИД.
Дата добавления: 2018-08-06; просмотров: 348; Мы поможем в написании вашей работы! |
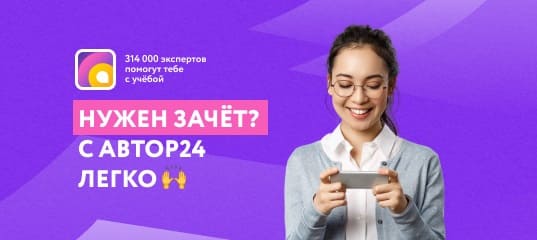
Мы поможем в написании ваших работ!