Технологическая последовательность выполнения работ
Термины и определения основных понятий по сварке металлов устанавливает ГОСТ 2601–84. Сварные соединения подразделяются на несколько типов, определяемых взаимным расположением свариваемых деталей. Основными из них являются стыковые, угловые, тавровые, нахлесточные и торцовые соединения. Для образования этих соединений и обеспечения требуемого качества должны быть заранее подготовлены кромки элементов конструкций, соединяемых сваркой. Формы подготовки кромок для ручной дуговой сварки стали и сплавов на железоникелевой и никелевой основе установлены ГОСТ 5264–80.
Тавровым соединениемназывают сварное соединение, в котором торец одного элемента примыкает под углом и приварен угловыми швами к боковой поверхности другого элемента. Стандартом предусмотрено несколько типов таких соединений: с Т1 по Т9. Распространенным является соединение, для металла толщиной 2–40 мм. Для такого соединения никакого скоса кромок не делают, а обеспечивают ровную обрезку примыкающего элемента и ровную поверхность другого элемента.
При толщине металла 3–60 мм и необходимости сплошного шва между элементами, что предусматривается проектом конструкции, в примыкающем элементе делают разделку кромок под углом (45±2)°. На практике часто применяют тавровое соединение с подкладкой при толщине стали 8–30 мм, а также соединение с двусторонним скосом кромок примыкающего элемента при толщине стали 8–40 мм. Все эти соединения со скосом кромок примыкающего элемента обеспечивают получение сплошного шва и наилучшие условия работы конструкций
|
|
При конструировании тавровых соединений следует учитывать, что совместная работастроганой кромки и угловых швов практически невозможна, так как плотность примыкания кромки, даже если она обеспечена при сборке, при сварке нарушается. Для передачи больших сжимающих усилий от полки к стенке следует предусматривать разделку кромок или автоматическую сварку с глубокой проваркой. При этом обеспечивается полная проварка таврового соединения с двух сторон при толщине ребра, равном двум катетам шва.
Тавровое соединение стали
Материалы
Для сбора и сварки таврового соединения необходимы к следующие материалы и инструменты:
· листы из металла подходящей толщины и размера;
· уголки из металла, из которых будут созданы ножки для мангала;
· аппарат для сварки металлических элементов;
· электрическая дрель;
· болгарка, которая должна быть оснащена специальными дисками, предназначенными для резки металла;
· набор электродов;
· инструменты для измерения, к которым относится рулета, уровень и стандартная линейка.
|
|
Дополнительно нужно подготовить чертежи.
·
На рисунке показана поверхность и обратная сторона нахлёсточного соединения стальных оцинкованных листов толщиной 0,75 мм, спаянных тугоплавким припоем. Как непосредственно возле шва, так и с обратной стороны слой цинка полностью сохраняется. В процессе пайки он становится жидким, но не испаряется. В автомобилестроении также все чаще применяются смешанные соединения стали и алюминия.
Расходные материалы для сварки
Сварочный электрод — металлический или неметаллический стержень из электропроводного материала, предназначенный для подвода тока к свариваемому изделию.
В настоящее время выпускается более двухсот различных марок электродов, причем более половины всего выпускаемого ассортимента составляют плавящиеся электроды для ручной дуговой сварки.
Инструменты и приспособления
В принадлежности и инструмент сварщика входят:
Электрододержатели служат для зажима электрода и подвода к нему сварочного тока. Они должны прочно удерживать электрод, обеспечивать удобное и прочное закрепление сварочного кабеля, а также быстрое удаление огарка и закладку нового электрода.
|
|
Электрододержатели должны выдерживать 8 тыс. зажимов электрода при затратах времени на каждую замену не более 4 с. Электрододержатели для тока 500
А и более должны иметь щиток для защиты руки сварщика от воздействия электрической дуги.
· Щитки, маски или шлемы служат для защиты глаз и лица сварщика от излучения сварочной дуги и брызг металла. В них имеется смотровое отверстие, в которое вставляют светофильтр, задерживающий инфракрасные и ультрафиолетовые лучи и снижающий яркость световых лучей дуги. Снаружи светофильтр защищен от брызг металла простым прозрачным стеклом.
· Металлические щетки (ручные и с электроприводом) для зачистки, разделки швов и очистки сварных швов от шлака.
· Молоток, зубило, крепежный инструмент.
· Набор шаблонов для контроля размеров швов.
· Стальные клейма для клеймения сварных швов.
· Индивидуальные защитные средства сварщика. Для защиты тела от ожогов сварщик пользуется брезентовым костюмом, брезентовыми рукавицами и кожаной или валяной обувью. Брюки должны быть гладкими, без отворотов с напуском поверх ботинок или валенок. Рукавицы должны иметь напуск на рукава и завязываться тесьмой. Прямая одежда и отсутствие открытых частей тела исключают возможность попадания брызг металла на тело и в складки спецодежды.
|
|
Кроме спецодежды к средствам индивидуальной защиты сварщика относятся: пояс предохранительный с лямками (при работе на высоте), резиновые диэлектрические шлем, перчатки, сапоги (или галоши), коврики. При сварке внутри резервуаров, баков, цистерн необходимо пользоваться резиновыми сапогами и резиновым шлемом. При сварке металлических конструкций, если сварщик работает лежа, сидя или стоя на элементах свариваемой конструкции, кроме резиновых сапог (или галош) и шлема необходимы резиновые коврики, а также наколенники и подлокотники, подшитые войлоком.
Болгарка и сварочный аппарат
Сварочный аппарат – это источник энергии для электродуговой сварки. При этом для возникновения электрической дуги применяется низкое напряжение с высокой силой переменного или постоянного тока.
Требования к качеству работ
Сварка – это самый распространенный метод, применяемый при изготовлении металлоконструкций самого разного назначения. Такой тип неразрывного соединения отдельных деталей в единое целое считается на сегодняшний день самым надежным и прочным. Поэтому и применяется он в тех металлоконструкциях, которые должны в процессе эксплуатации выдерживать самые серьезные нагрузки. А долговечность конструкции в полной мере зависит от того, насколько при ее изготовлении соблюдалось требование к сварным швам, прописанное в ГОСТ и проектной документации.
Сварное изделие после завершения всех технологических: операций предъявляют для технического контроля. Контроль осуществляют поэтапно. Внешним осмотром проверяют отсутствие подрезов, наплывов, непроваров, крупных пор и в соответствии с техническими требованиями чертежа дефекты могут быть устранены путем вырубки и заварки. При отсутствии внешних дефектов сварки производят контроль размеров изделия в соответствии с требованиями чертежа, а затем контроль качества сварных швов. Наружные поверхности сварных швов покрывают меловой обмазкой, а внутренние смачивают керосином. Керосин проникает в имеющиеся поры и трещины и окрашивает меловую обмазку в желтый цвет. Такой пробой можно выявить сквозные трещины и поры.
Основные показатели, влияющие на общее качество сварки:
Контроль качества сварных швов
Основные технологические факторы, влияющие на качество сваривания:
· режим сварочного процесса – это и сила тока, и напряжение;
· материалы необходимые для сваривания: электроды, флюсы, защитные газы;
· материалсвариваемогоизделия;
· профессионализм сварщика – это и разряд, и опыт работы;
· условия, в которых производится сваривание.
Операционный контроль качества сварных соединений ультразвуком
Виды диагностики, проводимые для выявления брака:
- Внешний осмотр.
- Аммиаком
Принцип тот же самый. Только с внешней стороны на шов накладывается «индикатор» (полоска бумаги, смоченная в специальном растворе), а с противоположной он подвергается обработке смесью воздух + аммиак. Изменение цвета «индикатора» свидетельствует о проницаемости сварного шва.
- Красками
- Вакуумом
Такую проверку целесообразно проводить при невозможности доступа к шву с обеих сторон, например, при сборке или во время профилактического осмотра различных резервуаров. Смысл в том, что в емкости искусственно создается вакуум. Проникновение внутрь воздуха свидетельствует о дефекте в сварных соединениях. А далее уже необходимо определить конкретный участок любым приемлемым способом.
- Воздушным давлением
Методика зависит от габаритов проверяемого образца. Если он имеет небольшие размеры, то испытания проводятся в специальной ванне. При нагнетании воздуха (под давлением) он будет проходить сквозь имеющиеся щели, поры, вызывая появление пузырьков в воде. Швы на крупных изделиях покрываются или специальным составом, или мыльным раствором. Вспучивание массы – свидетельство нарушения герметичности шва.
- Гидравлическим способом
Принцип такой же. Только внутрь сосуда (трубы) под давлением подается вода, и по наличию протечек определяются проблемные участки.
Дата добавления: 2018-08-06; просмотров: 315; Мы поможем в написании вашей работы! |
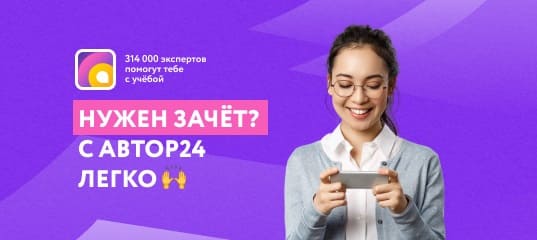
Мы поможем в написании ваших работ!