Бесконтактные методы контроля параметров
Важным достоинством бесконтактных методов является возможность реализации на их основе принципа неразрушающего контроля.
Рассмотрим на примерах некоторые из этих методов.
Основу индуктивного метода контроля целостности инструмента составляет измерительный мост с эталонной катушкой индуктивностью (полное сопротивление Z,) и измерительной катушкой Lи (Zи) в зоне инструмента (рис, 5.32).
Рис. 5.32. Схема индуктивного метода контроля целостности инструмента
При цельном инструменте индуктивности равны Lи = Lэ, и ток в измерительном мосту равенI= 0,а при поломке инструмента ток I> 0.Эта информация попадает и систему управления СУ станка, которая вырабатывает сигнал останова системы для замены инструмента.
Пневматический метод контроля линейных размеров с помощью датчика «сопло—заслонка» в принципе может быть использован и дляконтроля качества поверхности деталей. При измерении, например, высоты h детали с изменением hменяется зазор δ между измерительным соплом 1 и поверхностью детали 4 и, следовательно, расход воздуха через сопло (рис. 5.33, а).
Рис. 6.33. Схемы контроля линейных размеров деталей с помощью пневматического датчика «сопло—заслонка»: α – контроль высоты h детали; б – контроль внутреннего диаметра D гильзы ( или цилиндра ) ДВС
При уменьшении зазора δ возрастает давление Рвых, что вызывает прогиб диафрагмы 2 пневмоэлектрического преобразователя и замыкание контактов 3. Сигнал через усилитель поступает в систему управления. Измерение внутреннего диаметра гильзы проводится одновременно в трех уровнях датчиком со сдвоенными соплами (рис. 5.33, б).
|
|
Из оптических достаточно широко применяются методы на базе фотоэлектрического датчика, лазерного луча и твердотельных камер технического зрения. Контроль размеров деталей с помощью фотоэлектрического датчика основан на изменении светового потока ΔФ, вызывающего изменение силы тока ΔI в цепи фоторезистора (рис. 5.34). Ток пропорционален величине светового потока ΔI~ ΔФ, где ΔI = I - I0; I0 — темновой ток, когда фоторезистор не освещен. Контролируемая деталь диафрагмирует световой поток, изменяя тем самым величину силы тока в цепи.
Схема контроля размеров методом сканирования детали лазерным лучом показана на рис. 5.35, а.
Рис. 5.34. Схема контроля линейных размеров деталей с помощью фотоэлектрического датчика: 1 – источник света; 2 – линза; 3 – деталь; 4 – диафрагма; 5 – фоторезистор; Фи, Фд – световой поток начальный и после диафрагмы соответственно
Рис. 5.35. Схема контроля детали сканированием лазерным лучом (а) и диаграмма изменения напряжения на оптическом детекторе ОД (б): ОГК – оптический квантовый генератор (лазер); УОС – устройство обработки сигнала; 1 – поворотное зеркало; 2 – линза; 3 – контролируемая деталь
|
|
Время Δt = t2– t1 перекрытия деталью лазерного луча пересчитывается в размер Iд по формуле
Iд = vcΔt,
гдеvc= const— скорость сканирования (скорость качания зеркала).
Время Δt на диаграмме соответствует отсутствию напряжения на оптическом детекторе (светочувствительном элементе) (рис. 5.35, б). Программа пересчета Δt хранится в ЭВМ.
Дата добавления: 2018-08-06; просмотров: 346; Мы поможем в написании вашей работы! |
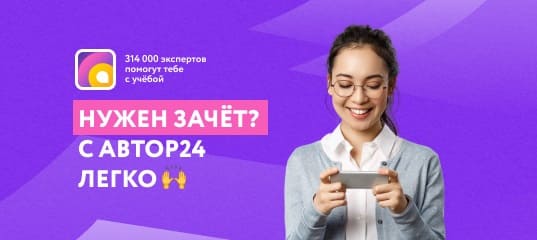
Мы поможем в написании ваших работ!