Диагностирование режущего инструмента
Существует несколько различных методов и устройств автоматической оценки работоспособности режущего инструмента. Рассмотрим один из универсальных методов, основанный на анализе амплитуды виброакустического сигнала (А) и амплитуды ЭДС сигнала (£), генерируемых в зоне контакта инструмента с заготовкой (рис. 5.40).
Значение Е сигнала снимается с резца и заготовки, а привязка сигнала по угловой координате производится с помощью датчика угла ДУ, который запускает систему измерения от синхроимпульса СИ.
Сигналы А и £ через усилители УI и У2 поступают на 6 полосовых фильтров —
а затем через коммутатор аналоговых сигналов КАС и АЦП попадают в ЭВМ для построения показателя затупления инструмента, в качестве которого служит изменение формы частного спектра сигнала E. (рис. 5.41),
Рис. 5.40. Схема диагностирования состояния режущего инструмента на основе анализа виброакустического {А) и ЭДС (Е) сигналов, генерируемых в процессе резания: СИ — синхроимпульс; ДУ — датчик угла поворота заготовки; ВД — вибродатчик; КАС — коммутатор аналоговых сигналов; СЗ — сигнализатор затупления; У1, У2 — усилители ЭДС резания; —
—— селективные фильтры; Шп — шпиндель; 3 — заготовка;
Р — резец
Рис. 5.41. График изменения частотного спектра Е сигнала по мере затупления инструмента: — частота начального периода резания;
, — частота предельного затупления инструмента
|
|
При частоте (начальный периода резания) амплитуда сигнала
огибающей кривой спектра соответствует образу острого инструмента, а по мере его затупления
сдвигается в область более
ких частот <
. Когда достигается предельное значение
ЭВМ выключает станок и происходит замена инструмента.
Диагностирование исполнительных механизмов оборудования
Решение задачи диагностирования исполнительных механизмов непрерывно связано с особенностями структуры электроприводов и этических схем технологического оборудования. Например, широко применяемый регулируемый электропривод подач для станков с ЧПУ содержит два замкнутых контура подчиненного регулирования: по току и по скорости. Датчики обратной связи по току и по скорости используются в качестве источника информации о состоянии электродвигателя. Кроме этих датчиков дополнительно можно использовать датчик путевого контроля (ДПК), который позволяет контролировать и механическую передачу электропривода. Когда обратная связь с ДПК полностью охватывает передачу от двигателя до рабочего органа станка, то можно контролировать состояние передачи (рис. 5.42). Датчик, связанный непосредственно с конечным звеном кинематической цепи, позволяет контролировать не только величину люфта, но и прогнозировать предельный износ механической передачи. В случае отсутствия указанной обратной связи такой контроль невозможен.
|
|
Рис. 5.42. Схема размещения датчика путевого контроля в кинематической цепи станка с полным охватом механической передачи: M — муфта; Р — редуктор; РО — рабочий орган станка; В—Г — тяговая пара винт—гайка; ЗП — зубчатая передача
Дата добавления: 2018-08-06; просмотров: 171; Мы поможем в написании вашей работы! |
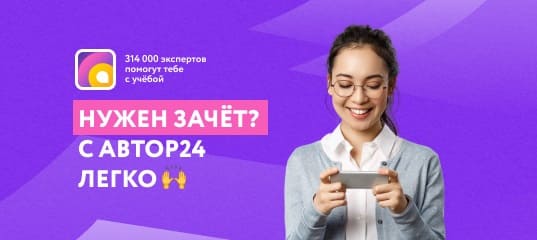
Мы поможем в написании ваших работ!