Диагностирование оборудования
Принципы технического диагностирования
Процедура диагностирования объекта включает два этапа: проверка его работоспособности и поиск дефекта. Поэтому основной задачей технического диагностирования (ТД) является поддержание работоспособности объекта путем своевременного распознавания отказов и устранения причин их появления.
По характеру взаимодействия объекта и технических средств можно назвать два метода ТД:
1) функционального диагностирования;
2) тестового диагностирования.
Первый метод основан на пассивном наблюдении за функционированием объекта и оценке его состояния по диагностическим признакам (например, уровень температуры, шумов или вибрации, величина потребляемой энергии, время выполнения цикла).
Второй метод предусматривает формирование специального воздействия, стимулирующего у объекта ответную реакцию, которая сравнивается с эталонной (активный эксперимент). Роль стимулирующего воздействия выполняют ступенчатые, импульсные, гармонические и другие сигналы.
В качестве диагностических показателей используются параметры динамических звеньев, коэффициенты уравнений, обобщенные параметры.
Типовой алгоритм системы поддержания работоспособности объекта (СПРО) имеет вид:
♦ сбор информации;
♦ оценка информации и выявление отклонений показателей от нормы;
♦ определение причины отклонения:
♦ принятие решения и выработка корректирующего воздействия (KB);
|
|
♦ ввод KB в систему с целью ликвидации отклонения.
Первые два этапа — операции контроля, третий — диагностирование.
Эксплуатируемый объект (система) подвержен как внезапным (случайным), так и постепенным (износ, старение) отказам. Если состояние объекта характеризовать обобщенным выходным параметром , то в случае внезапного отказа
принимает лишь два значения:
=
(норма) или
=
(отказ) (рис. 6.36). В случае постепенных отказов
принимает несколько значений:
зона нормы min <
< max
;
зона риска min <
< min Пэ max
<
< max
;
зона отказа max <
< min
, где
,
— эталонное и предельное значения параметра
.
Рис. 5.36. Зоны работоспособности технической системы (объекта): — обобщенный показатель системы;
— эталонное значение
;
— предельное значение Пр
В качестве параметра используют различные технические характеристики: температура, размер объекта, величина износа узла (или инструмента), сигнал конечного выключателя и т. п. В случае постепенных отказов можно реализовать мероприятия по предотвращению отказа, если вовремя зафиксирован переход параметра
от нормы в зону риска.
В информационной структуре системы поддержания работоспособности объекта (рис. 5.37) можно выделить следующие подсистемы: контроля (ПСК), диагностирования (ПСД) и принятия решений (ПСПР). Информация об объекте управления (ОУ) отдатчиков контроля (ДК) поступает на вход ПС К, которая обрабатывает ее, рассчитывает значения обобщенного параметра ПР и сравнивает их с эталонным. По результатам сравнения ПСК формирует сигнал об отклонении ПР от нормы, который подается в зависимости от ситуации в систему программного управления (СПУ) или в ПСПР. В случае угрозы аварийной ситуации СПУ вырабатывает
|
|
Рис. 5.37. Информационная структура системы поддержания работоспособности объекта:
ПК, ПД — программы контроля и диагностирования соответственно; РК, РД — результаты контроля и диагностирования; ИДК — исходные данные для контроля; ИДПР —исходные данные для принятия решений
блокировочный сигнал останова системы для ремонта. При отсутствии угрозы аварии ПСПР вырабатывает корректирующее воздействие (KB), которое передается в СПУ для осуществления подналадки системы.
Диагностирование оборудования
В технических средствах АСУ реализуется концепция функционального самоконтроля с определением состояния отказа и поиска неисправности (рис. 5.38). На схеме отказоустойчивой подсистемы АСУ блоки 1, 3, 4 представляют подсистему обеспечения безотказной работы диагностируемого блока 2.
|
|
Рис. 5.38. Схема отказоустойчивой подсистемы АСУ: СрЗНЭ — средства замены неисправного элемента; ТС — технические средства; СТД — средства тестовой диагностики; РО — решающий орган (машина или человек)
Процесс диагностирования технологического оборудования рассмотрим на примере станка с ЧПУ в составе ГПМ (рис. 5.39).
Рис. 5.39. Схема информационных связей системы диагностирования станка (ТО) с ЧГТУ в составе ГПМ:
КИМ — контрольно-измерительная машина; И — интерфейс; КДП — контрольно-диагностический пульт; ИСС — индикатор состояния станка
В процессе эксплуатации станка применяются следующие режимы диагностирования:
• непрерывное (например, температура в блоке ЧПУ или масла в гидросистеме);
• периодическое с повышенной частотой (например, давление в системе централизованной смазки, усилие зажима каждой заготовки, точность обработки);
• периодическое с меньшей частотой (например, раз в смену или после обработки партии заготовок определяется кинематическая точность и жесткость станка);
|
|
• по требованию (проводит оператор в зависимости от конкретной ситуации.
Структура информационных связей системы диагностирования станка с ЧПУ (см. рис. 5.39) показывает, что от ЭВМ верхнего уровня в ЧПУ поступают тест-программы и алгоритм диагностирования. От контрольно-измерительной машины (КИМ) передается информация по точности обработки заготовок, а от подсистем диагностирования станка — обобщенная оценка технического состояния исполнительных механизмов станка и фактической длительности цикла. По результатам тестирования станок выдает оперативную информацию в ЭВМ через КИМ, а также на контрольно-диагностический пульт (КДП) и индикатор состояния станка (ИСС).
Для выполнения сложных операций диагностирования оборудования используют специальные средства, которые монтируют на передвижной установке, связанной с ЭВМ верхнего уровня. Специальная установка позволяет проводить анализ технических характеристик станка, в частности точности позиционирования и обхода контура заготовки, точности геометрических параметров станка, жесткости кинематических пар и т. п. Специальные средства и ЭВМ в принципе позволяют решать задачу прогнозирования надежности функционирования станка.
Дата добавления: 2018-08-06; просмотров: 312; Мы поможем в написании вашей работы! |
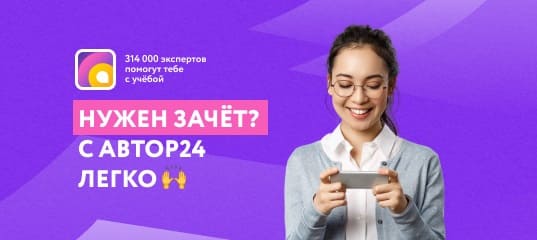
Мы поможем в написании ваших работ!