Глава 2. ТЕХНОЛОГИЧЕСКИЙ ПРОЦЕСС ЦВЕТНОЙ
КАПИЛЛЯРНОЙ ДЕФЕКТОСКОПИИ
Основные технологические операции методов капиллярного неразрушающего контроля деталей, сборочных единиц и сварочных соединений заключаются в следующем:
1) подготовка дефектоскопических материалов и проверка их качества;
2) подготовка изделий к контролю, их очистка и обезжиривание;
3) сушка изделий и удаление растворов из полостей дефектов;
4) нанесение на контролируемую поверхность изделия индикаторного пенетранта;
5) удаление избытка пенетранта с контролируемой поверхности;
6) нанесение проявителя пенетранта и выдержка, необходимая для того, чтобы проявитель вытянул пенетрант на поверхность из полости дефекта;
7) обнаружение дефектов при наблюдении контролируемой поверхности изделия в темноте в ультрафиолетовом или видимом свете;
8) разметка дефектов и оценка качества изделия;
9) удаление проявителя и следов других дефектоскопических материалов с контролируемой поверхности изделия.
Отдельные из перечисленных операций при контроле по той или иной конкретной технологии люминесцентного, цветного или люминесцентно-цветного методов могут быть исключены из технологического процесса.
Технологические режимы операций контроля (продолжительность, температуру, давление) устанавливают в зависимости от требуемого класса чувствительности, используемого набора дефектоскопических материалов, особенностей объекта контроля и типа искомых дефектов, условий контроля и используемой аппаратуры.
|
|
Подготовка дефектоскопических материалов и проверка
Их качества
Перед проведением производственного контроля осуществляется подготовка дефектоскопических материалов и проверка их качества. Дефектоскопические материалы подвергаются входному контролю: проверяют наличие паспортов заводов-изготовителей на дефектоскопические наборы или их отдельные составные части, а также соответствие материалов государственным стандартам и техническим условиям и т. д.
При проверке дефектоскопических материалов применяют обычно не менее двух образцов-имитаторов с трещинами одинакового характера и примерно равных размеров. Один образец – рабочий, его применяют постоянно, второй используют как эталонный при неудовлетворительном выявлении трещин на рабочем образце – имитаторе.
Конструкция и методика изготовления образцов-имитаторов должна соответствовать требованиям ГОСТ 18442 – 80.
Подготовка изделий к контролю
Подготовка объектов к контролю включает в себя очистку контролируемой поверхности и полостей дефектов от всевозможных загрязнений, лакокрасочных покрытий, моющих составов и дефектоскопических материалов, оставшихся от предыдущего контроля, а также сушку контролируемой поверхности и полостей дефектов.
|
|
Способ подготовки изделий к производственному контролю выбирают в зависимости от их материала, вида загрязнения и покрытий, предшествующих способов механической обработки и других факторов. Шероховатость контролируемой поверхности при проведении контроля должна быть RZ≤20 мкм; при RZ›20 мкм чувствительность значительно снижается.
2.2.1. Способы очистки контролируемой поверхности приведены ниже (рис.2):
механический – очистка струей абразивного материала (песком, дробью, косточковой крошкой, металлической щеткой) или механической обработкой поверхности (рис. 2, а, б);
паровой – очистка в парах органических растворителей (рис.2, в);
растворяющий – очистка промывкой, протирка с применением воды, водных моющих растворов или легколетучих растворителей (ацетон, авиационный бензин, растворитель 645 (рис. 2, г);
химический – очистка водными растворами химических реактивов для удаления коррозии и очистки устья и внутренних полостей дефектов от твердых частиц и отложений;
электрохимический – очистка водными растворами химических реактивов с одновременным воздействием электрического тока;
|
|
ультразвуковой – очистка растворителями, водой или водными растворами химических соединений в ультразвуковом поле с использованием ультразвукового капиллярного эффекта;
анодно-ультразвуковой – очистка водными растворами химических реактивов с одновременным воздействием ультразвука и электрического тока;
тепловой – очистка прогревом при температуре, не вызывающей недопустимых изменений материала контролируемого объекта и окисления его поверхности;
сорбиционный – очистка смесью сорбента и быстросохнущего органического растворителя, наносимой на очищаемую поверхность, выдерживаемой и удаляемой после высыхания.
а б
в г
Рис. 2. Предварительная чистка контролируемой поверхности детали:
а) механическая очистка металлической щеткой, б) механическая очистка струйным методом, в) обезжиривание горячим паром,
г) очистка растворителем
Примечания. Необходимые способы очистки, их сочетание и требуемую чистоту контролируемых поверхностей определяют в технической документации на контроль.
|
|
При заданном высоком классе чувствительности контроля предпочтительны не механические, а химические и электрохимические способы очистки, в том числе с воздействием на объект контроля ультразвука или электрического тока. Эффективность этих способов обусловлена оптимальным выбором очищающих составов, режимов очистки, сочетанием и последовательностью используемых способов очистки, включая сушку. Механический способ очистки применяют для неответственных деталей. При такой очистке происходит заполнение полости дефектов продуктами очистки.
2.2.2. При подготовке объекта к контролю в необходимых случаях проводят работы по снятию или компенсации остаточных или рабочих напряжений, сжимающих полости искомых дефектов в объекте.
При поиске сквозных дефектов в стенках трубопроводных систем, баллонов, агрегатов и аналогичных полостных объектов, заполненных газом или жидкостью и находящихся под избыточным давлением, полости таких объектов освобождают от жидкости и доводят давление газа в них до атмосферного.
2.2.3. После промывки и обтирки детали сушат для более полного освобождения внутренних полостей дефектов от растворителей. Возможны следующие способы сушки деталей: выдержка на воздухе, инфракрасными лампами, фенами, обдувка сжатым воздухом и прогревание в сушильных шкафах.
Продолжительность сушки на воздухе должна быть не более 15 – 20 минут. Лучше обдувать детали теплым воздухом.
Наиболее полное удаление жидкостей из внутренних полостей дефектов происходит при нагревании выше температуры кипения в сушильных шкафах. Нагрев выше 230 – 240 0С не рекомендуется, так как происходит окисление масла, смазки и образование нерастворимой поверхностной пленки у выхода трещины.
Дата добавления: 2018-06-01; просмотров: 418; Мы поможем в написании вашей работы! |
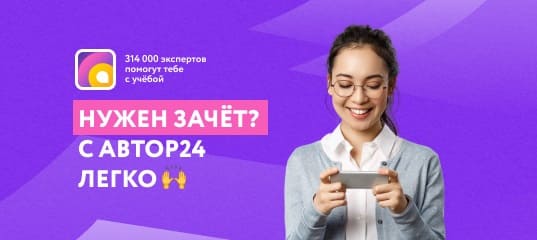
Мы поможем в написании ваших работ!