Плавка медных шихт в руднотермических печах.
Плавка сульфидных материалов в рудно-термических электропечах является близким аналогом отражательной плавки по физико-химическим превращениям шихты. Коренное различие заключается в условиях выделения тепла и его подвода к проплавляемым материалам. В электропечи шихта плавится за счет тепла, выделяемого при прохождении электрического тока через шлаковый расплав, выполняющего одновременно роль нагреваемого элемента.
В металлургии меди возможны варианты электроплавки:
1) Частичный обжиг высокосернистой шихты и плавка огарка на штейн;
2) Обжиг сульфидной шихты "намертво" и плавка огарка на черновую медь;
3) Плавка на штейн тугоплавкой шихты с повышенным содержанием кремнезема.
Первый вариант применялся на заводе Роншер (Швеция) .Получаемый штейн имел состав, %: Cu 40; Fe 27-30; S 24,6; Zn 5,4; Pb 2,7; Au 30 г/т; Ag 340 г/т. Отходящие газы электропечи объединялись с газами обжиговых печей и направлялись в сернокислотное производство. Однако технология плавки огарка в электропечи повторяет недостатки отражательной плавки и не дает повышения комплексности использования сырья.
Вариант плавки на черновой металл использовали на заводе Брикслег (Австрия). По технологии концентрат, содержащий 26-27% меди, 30-35% железа и 32-36% серы, обжигают в 7-подовой печи до содержания серы в огарке 1-1,2 %. Огарок смешивают с 25% кварцевого флюса, 12% известняка, 4-5% оборотных материалов и шихту проплавляют в электропечи с добавкой 6-7% кокса для восстановления меди, никеля и части железа.
|
|
Продуктами плавки являются: черновая медь, богатый медный штейн и шлак. Суммарное извлечение меди составляет 98%, из них в черновой металл 95% и в штейн 3%. Основные недостатки процесса: повышенное содержание железа в черновой меди и большое количество технологических газов, обогащенных летучими соединениями свинца, цинка и кадмия.
Рис.3.4 Продольный (а) и поперечный (б) разрезы электропечи завода «Роншер» (Швеция):
1-газоотвод; 2- электроды; 3-токоподводы; 4-течка для загрузки шихты. [Гудима-3,стр.120]
Третий вариант плавки был принят для переработки высококремнеземистых малосернистых концентратов на Жезказганском медеплавильном заводе, действующем с 1971 года. Шихта плавки содержит концентрат и известняковый флюс. По технологической схеме местные и привозные концентраты смешиваются в чане в виде пульпы, далее подвергаются обезвоживанию в сгустителе и на фильтрах. Кек концентратов поступает в штабельный шихтарник, где смешивается с известняковым флюсом и оборотными материалами. Готовая шихта гранулируется на чашевых грануляторах при добавлении связующего и увлажнении до 8-10%. Гранулы подсушивают топочными газами до остаточной влажности 1%. После сушки гранулированная шихта подается системой транспортеров в загрузочные бункера электропечей.
|
|
Применяли 2 прямоугольные электропечи с площадью пода по 109 м2, имеющие по 6 электродов диаметром 1200 мм. В электропечь через отверстия в своде по трубам загружается шихта и проплавляется с получением штейнов, шлаков и газов. Также заливается оборотный конвертерный шлак. Для этого со стороны конвертерного отделения в стене печи устраивают окно и устанавливают заливочный чугунный жёлоб. В 1997-98 гг. была проведена реконструкция плавильного отделения, при которой с целью совершенствования системы аспирации на печах боковые газоходы были объединены в один газоход каждой печи и внедрена система впрыска воды для охлаждения отходящих газов. Было увеличено подсводовое пространство за счет поднятия свода печи, проведена модернизация системы автоматизированного контроля и регулирования работы печей.
Расход энергии при плавке составляет 630-640 квт/ч на тонну шихты при проплаве 5-6 т/м2 в сутки. Выход штейна от массы шихты составляет 52%. Степень десульфуризации при плавке малосернистых материалов составляет небольшую величину (1-2%). Получаемые штейны содержат, %: 50-55 меди; 6-8 свинца; 4-5 цинка; железо и серу. Извлечение металлов в штейн составляет: меди 95%, свинца 84%, цинка 65%. В шлаке содержится, %: до 0,5 Cu; до 0,8 Pb; до 3,2 Zn; 10 FeO; 12-14 CaO; 53-59 SiO2; 6-7 Al2O3;1,4-1,6 MgO.
|
|
По сравнению с отражательной, руднотермическая плавка имеет более высокую удельную производительность [до 10-12 т/(м2.сут)], меньшие потери тепла с отходящими газами вследствие небольшого объема отходящих газов (нет топочных газов) и их низкой температуры (500-600 °С), более высокий тепловой коэффициент полезного действия (до 70%), возможность перерабатывать тугоплавкую шихту вследствие большего перегрева расплавов, меньшие потери меди со шлаками.
Расход электроэнергии при руднотермической плавке медных концентратов в зависимости от их состава и влажности колеблется от 380 до 650 кВт-ч/т шихты. Однако в целом руднотермическая плавка также не удовлетворяет большинству современных требований и в первую очередь необходимости исключить посторонние источники тепловой энергии для переработки сульфидного сырья.
Дата добавления: 2018-06-01; просмотров: 928; Мы поможем в написании вашей работы! |
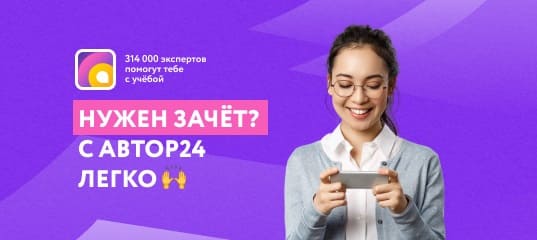
Мы поможем в написании ваших работ!