Плавка медных шихт в отражательных печах.
Лекция 3. Процессы плавки медных шихт на штейн.
Плавка медных шихт на штейн в шахтных печах.
Шахтная плавка медных руд является наиболее старым способом плавки на штейн, существовавшим еще в прошлые столетия и сохранившим свое практическое значение до настоящего времени. Применительно к переработке медных руд и концентратов возможны четыре разновидности шахтной плавки: восстановительная, пиритная (окислительная), полупиритная и усовершенствованная пиритная или медно-серная. В современной металлургии меди сохранили свое практическое значение при переработке рудного сырья только два последних метода. Восстановительную шахтную плавку используют до настоящего времени как основной метод получения черновой меди из вторичного сырья.
Пиритная плавка в противоположность восстановительной теоретически полностью может протекать за счет тепла от окисления (сжигания) самой сульфидной шихты, имеющей теплотворную способность 5000-6000 кДж/кг. Вследствие очень напряженного теплового баланса на практике в печь вводили до 2 % кокса. Пиритная плавка, пригодная для переработки только высокосернистых руд, содержащих не менее 75% пирита (около 42% серы), потеряла свое практическое значение.
Рис.3.1 Шахтная печь для полупиритной плавки медного агломерата:
1-шахтная печь; 2- газоход печи; 3- пылевая камера; 4- наружный миксер (отстойник). [3,стр.108]
|
|
Полупиритная плавка занимает промежуточное место между восстановительной и пиритной плавками. При восстановительной плавке, пригодной для переработки окисленного или вторичного сырья, все необходимое для процесса тепло получается за счет сжигания кокса, расход которого составляет не менее 15 %от массы твердой шихты.
Когда сульфидов в исходной шихте не хватает для автогенного ведения шахтной плавки, недостаток тепла компенсируют сжиганием углеродистого топлива. Такой вид шахтной плавки, при которой тепло получается как от горения сульфидов, так и от сжигания топлива, получил название полупиритной, расход кокса составляет 5- 12 %. Процессы, определяющие ход полупиритной плавки, развиваются в фокусе печи, где достигаются максимальные температуры (до 1600°С) и протекают процессы горения кускового кокса и сульфидов (в твердом и жидком состояниях), плавления компонентов шихты, штейно- и шлакообразования. Основные реакции этой зоны:
С + О2 = СО2 + 393780 кДж;
2FeS + 3O2 = 2FeO + 2SO2 + 937340 кДж;
2FeO + SiO2 = 2FeО • SiO2 + 92950 кДж.
Для успешного и быстрого завершения этих реакций плавку нужно вести форсированно с большим избытком дутья- до 100 % от теоретически необходимого. Интенсификации процесса полупиритной плавки способствуют обогащение дутья кислородом и его подогрев. При большом избытке воздуха кислород дутья не успевает израсходоваться в фокусе печи и в большом количестве выносится в верхние слои шихты, в подготовительную зону. В результате этого в верхней части столба шихты наряду с обычными для этой зоны процессами нагрева, сушки и термической диссоциации высших сульфидов и карбонатов происходит горение твердых сульфидов.
|
|
За счет выделяющегося тепла в фокусе печи происходит плавление шихты и завершается образование продуктов плавки. Жидкие продукты плавки (шлак и штейн) стекают во внутренний горн, откуда они совместно выпускаются по сифонному желобу в передний горн на отстаивание. Раздельный выпуск штейна и шлака осуществляется из переднего горна. Содержание меди в штейнах в зависимости от состава сырья изменяется от 15 до 50 %, шлаки содержат, %: 35-40 SiO2; 45-60 FeO; 3-12 СаО и 0,3- 0,35 Сu.
Таблица 3.1 Технико-экономическими показатели полупиритной плавки
Удельный проплав, т/(м2-сут) | 60-120 |
Содержание серы в шихте, % | 20-38 |
Степень десульфуризации, % | 60-75 |
Расход кокса, % от массы шихты | 5-12 |
Шахтная плавка является сравнительно дешевым технологическим процессом. Для ее осуществления требуется мало топлива и огнеупоров и применяются простые и дешевые конструкции печей. Достоинствами этого вида плавки являются пригодность процесса для малых масштабов производства, так как шахтные печи могут быть построены любой длины, и высокая удельная производительность. Ограниченность применения шахтной плавки обусловлена отсутствием пригодного для плавки рудного сырья и низкой степенью комплексности его использования.
|
|
Медно-серная плавка по существу представляет собой пиритную плавку высокосернистых руд в комбинации с усовершенствованным методом обработки печных газов с целью получения серы в элементарном состоянии. Для этого сульфидную руду в смеси с кварцевым флюсом и увеличенным количеством кокса (до 12%) плавят в герметизированной шахтной печи с увеличенной высотой. Характерным для медно-серной плавки является существование в печи по высоте трех четко выраженных зон: окислительного плавления (нижняя), восстановительной и подготовительной.
В зоне окислительного плавления, расположенной в области фурм и имеющей очень ограниченные размеры, развиваются самые высокие температуры (1200-1450°С). Необходимое для плавки тепло выделяется в результате основной реакции плавки:
|
|
2 FeS + 3 О2 + SiO2 = 2 FeO.SiO2 + 2 SO2 + 1030290 кДж.
В классической пиритной плавке не допускается никаких отклонений от стехиометрии реагентов этой реакции. Избыток или недостаток любого из исходных реагентов приводит к нарушению теплового режима плавки, сокращению или растягиванию фокуса печи. Теоретически при пиритной плавке весь кислород дутья должен обязательно полностью расходоваться в области фурм, и до фурм не должен доходить кокс. В противном случае пиритный эффект пропадает и печь замерзает с образованием «козла».
Жидкие продукты пиритной плавки стекают во внутренний горн печи и далее в наружный отстойник, а газы, состоящие почти полностью из сернистого ангидрида и азота, поступают в среднюю, восстановительную зону, заполненную раскаленным коксом. Основным процессом этой зоны является восстановление сернистого ангидрида до паров элементарной серы по реакциям:
2 SO2 + 2 С = S2 (naр)+ 2СО2
2SO2 + 4CO = S2 (naр)+ 4 CO2
Для наиболее полного восстановления SO2 в средней зоне на этом участке печь, резко расширяется вверх, что снижает скорость движения газового потока и увеличивает за счет этого время контакта между реагентами. В восстановительной зоне, кроме указанных выше реакций протекают другие побочные процессы, приводящие к образованию CS2, COS, H2S и др. Газы восстановительной зоны, пронизывая верхние слои шихты, обогащаются парами элементарной серы, образующимися при термической диссоциации высших сульфидов.
Специфика процесса медно-серной плавки требует применения для ее осуществления печей специальной конструкции. Для того чтобы сохранить серу в парообразном состоянии, нужно в верхней части печи иметь температуру не ниже 500-550 °С. Это достигается уменьшением потерь тепла через стенки печи, которые в верхней части представляют огнеупорную кладку, закрепленную в железном кожухе. В печах медно-серной плавки кессонируется только фурменный пояс.
Чтобы избежать обратного окисления серы, печь герметизируют и внутри нее поддерживают положительное давление. Герметизация загрузки достигается установкой затворов колокольного типа. Шихта поступает на верхний колокол, затем перепускается в межколокольную емкость, откуда после закрытия верхнего колокола разгружается в печь.
Дальнейшее совершенствование медно-серной плавки, хотя несколько и снизило извлечение серы в газовую фазу, однако позволило повысить устойчивость режима процесса и существенно интенсифицировать его. Этому способствовало также обогащение дутья кислородом и его предварительный нагрев.
Колошниковые газы имеют следующий состав, г/м3: 250-290 S2; 28-32 SO2; 17-20 H2S; 28-33 CS2+COS. (Температура кипения серы равна 444,5 °С.) Они содержат также N2, CO и СО2. После выхода из печи из газов сначала в газоходах и пылевой камере выделяется грубая пыль, а затем в электрофильтрах улавливают тонкую пыль. Очищенные от пыли газы проходят двух или трехстадийную обработку с целью извлечения элементарной серы. На каждой стадии газы пропускают через контактную камеру с пористым катализатором на основе глинозема и гидроксида алюминия с целью восстановления связанной серы (SO2, H2S, CS2 , COS) до элементарного состояния. После катализа газы направляются в конденсатор и в орошаемые жидкой серой башни, где улавливаются взвешенные в газе капли серы. Каждая ступень катализа позволяет повысить суммарное извлечение серы из газов. Продуктом химического цеха является кристаллическая сера.
Медно-серная плавка требует качественной подготовки шихты. Всю рудную мелочь в смеси с коксом, известью и трепелом обязательно подвергают брикетированию на штемпельных прессах с последующей пропаркой брикетов в автоклавах, что придает им пористость и высокую прочность. Наиболее вредными примесями при медно-серной плавке являются цинк и мышьяк. При содержании цинка в руде выше 2% он накапливается в печи с образованием верховых настылей из тугоплавкого сульфида цинка. Причиной этого является частичная возгонка оксида цинка, образовавшегося в области фурм. Попадая в верхние слои шихты, ZnO восстанавливается до металла и сульфидируется элементарной серой. Мышьяк на 80-85% переходит в газовую фазу в элементарном состоянии и конденсируется вместе с серой, загрязняя ее. Наиболее эффективным способом очистки серы от мышьяка, является обработка жидкой серы твердой известью (СаО) с добавкой хлоридов щелочных металлов. В России по методу медно-серной плавки работает Медногорский медно-серный комбинат.
Таблица 3.2 Технико-экономические показатели медно-серной плавки
Удельный проплав, т/(м2.сут) | 30- 40 |
Содержание меди в штейне, % | 4- 15 |
Расход кокса, % от массы шихты | 9,5- 12 |
Извлечение меди в штейн, % | 90- 94 |
Извлечение серы, % | 80- 90 |
Содержание серы в кристаллическом продукте, % | 99,6-99,95 |
В целом шахтные печи сохраняют свои позиции в металлургии свинца благодаря высокой производительности и универсальности к составу шихты, но постепенно вытесняются прогрессивными автогенными процессами, не требующими дорогостоящего и дефицитного кокса, а также предварительного агломерирующего обжига.
Плавка медных шихт в отражательных печах.
Различают две разновидности отражательной плавки медного сырья по характеру перерабатываемой шихты: плавка обожженной шихты (огарка); плавка необожженной подсушенной шихты.
Рис.3.2 Отражательная печь завода «Маунт-Айза»:
1-линия первичного воздуха и угольной пыли; 2- линия вторичного воздуха; 3- водоохлаждаемый кессон;
4- водоохлаждаемый блок; 5-уровень ванны расплава; 6,7-рельсовые пути для вагонеток; 8-водоохлаждаемая рама; 9-передвижной желоб для слива шлака; 10-конвертерный пролет; 11-передняяя стенка печи; 12-канал загрузки огарка; 13-уровень ванны; 14-начальная линия пода; 15-шлаковое окно; 16-шпуры для выпуска штейна; 17-линия пода; 18-котлы-утилизаторы; 19-водоохлаждаемый блок для выпуска штейна; 20-шпур для выпуска штейна; 21-шлаковый желоб. [3,стр.115]
Для загрузки шихты в своде отражательной печи вдоль каждой из боковых сторон устраивают 20-23 вертикальных загрузочных отверстия диаметром до 300 мм на расстоянии 1,2-1,5 м. Шихта в печь подается с помощью виброконвейеров, скребковых транспортеров или специальных вагонеток с донной разгрузкой. Необожженная шихта ложится откосами вдоль стен и в этом случае плавление шихты протекает в тонком поверхностном слое. Такой способ загрузки шихты сопровождается большим пылевыносом и быстрым разъеданием свода печи, особенно вблизи загрузочных отверстий. Наибольшая химическая коррозия свода наблюдается при плавке обожженной шихты. Более рациональным признано считать подачу шихты непосредственно на поверхность шлакового расплава через боковые стены печи.
Рис.3.3 Газовые горелки отражательных печей:
а-турбулентная газомазутная горелка; б- двухпроводная горелка. [3,стр.110]
В отражательную печь обычно загружают жидкий оборотный конвертерный шлак, сливаемый из конвертеров в течение первого периода конвертирования. Шлак стальными ковшами емкостью 6-8 т заливается в печь с помощью мостового крана через специальные чугунные желоба - ложки, установленные в окне передней торцевой стены печи.
Механизм плавки в отражательной печи можно представить следующим образом. Нагрев шихты, лежащей на поверхности откосов, за счет тепла, излучаемого факелом, сопровождается сушкой материала и термической диссоциацией высших сульфидов и других неустойчивых соединений. По мере нагрева в поверхностных слоях шихтовых откосов начинают плавиться легкоплавкие составляющие шихты (сульфидные и оксидные эвтектики). Образующийся при этом первичный расплав стекает по поверхности откосов, растворяет в себе более тугоплавкие компоненты и попадает в слой шлакового расплава. С этого момента начинается разделение шлаковой и штейновой фаз; капли оксидной фазы растворяются в общей массе шлака, имеющегося постоянно в печи, а капли штейна проходят через слой шлака и образуют в нижней части ванны самостоятельный слой.
Скорость отстаивания капель штейна будет тем выше, чем больше их размеры. Мелкие штейновые включения в условиях отражательной плавки (спокойная ванна) не полностью успевают отстояться за время пребывания расплава в печи (10-14 час) и выносятся со шлаком. В печи наиболее нагреты поверхностные слои шлака, а с увеличением глубины температура расплава снижается. Это приводит к отсутствию конвекции расплава.
При переработке в отражательной печи обожженных концентратов, механизм плавки другой: частицы огарка, растекаясь по поверхности шлаковой ванны, контактируют с ней, оксидные пленки на частицах растворяются в шлаке, а сульфидные зерна оседают на дно расплава, образуя штейн. Различным при плавке огарка или подсушенных концентратов будет и химизм плавки. При переработке подсушенных концентратов степень десульфуризации составляет 25-50% за счет дополнительно протекающих реакций диссоциации высших сульфидов с выделением и окислением элементарной серы, взаимодействия сульфидов железа с магнетитом, поступающим в печь с оборотным конвертерным шлаком, по реакциям:
FeS2 = FeS + 1/2 S2
CuFeS2 = Cu2S + FeS + 1/2 S2
CuS = Cu2S + 1/2 S2
S + O2 = SO2
FeS + 3 Fe3O4 + 5 SiO2 = 5 (2 FeO • SiO2) + SO2
Химизм плавки огарка, поскольку разложение высших сульфидов практически полностью закончилось при обжиге, сводится к химическому взаимодействию между оксидами и сульфидами. Основными в этой плавке являются следующие реакции:
Cu2O + FeS = Cu2S + FeO
10 Fe2O3 + FeS = 7 Fe3O4 + SO2
При плавке огарка степень десульфуризации составляет 15-20% и протекает за счет реакций магнетита с сульфидами и в первую очередь с сульфидом железа:
3 Fe3O4 + FeS + 5 SiO2 = 5 Fe2SiO4 + SO2
Необходимость проведения предварительного обжига концентратов определяется сравнением технико-экономических показателей плавки по двум вариантам. Считают, что если при плавке концентрата в отражательной печи получается штейн с содержанием меди менее 20%, то целесообразно проведение обжига сырья с частичным удалением серы. При плавке огарка отражательная печь имеет более высокий проплав, снижаются затраты топлива, получают более богатые по меди штейны, конвертирование которых требует меньших затрат. Положительный эффект при плавке огарка достигается за счет тщательной подготовки шихты при перемешивании в обжиговых печах, использования тепла горячего огарка, загружаемого в отражательную печь при температуре 1023-1073 К.
В процессе плавки в отражательной печи получают расплавы штейна и шлака. Выпуск штейна осуществляется через сифон или шпуровые отверстия, расположенные в нижней части боковых стен. Для выпуска шлака используют шлаковые окна, размещенные в конце печи, чаще всего на обеих боковых сторонах печи. Высота расположения порога шлакового окна определяет общий уровень расплава в печи, составляющий обычно по высоте 0,8-1,2 м, в том числе 0,4-0,6 м штейна.
Удельная производительность печей при плавке сырой шихты составляет 4,5-4,8 и при плавке огарка 5,9-8,7 т/(м2.сут) с расходом условного топлива 175-180 и 120-135 кг/т шихты соответственно. Извлечение меди и благородных металлов в штейн достигает 96-99,5%. Технология выплавки меди в отражательных печах совершенствовалась путем использования тепла отходящих газов в котлах-утилизаторах и рекуператорах, так как термический к.п.д. печи низкий (25-30%) и до 70-75% тепла, полученного при сжигании топлива, теряется с отходящими газами. При утилизации тепла термический к.п.д. возрастает до 55-65% и значительно снижается стоимость отражательного передела.
Предварительный подогрев воздуха и газообразного топлива в трубчатых рекуператорах за счет тепла отходящих газов позволяет повысить температуру в рабочем пространстве печи, снизить расход топлива и повысить удельный проплав. Для интенсификации плавки применяют обогащение дутья, подаваемого в горелки кислородом. Доказано, что рентабельно обогащать кислородом дутье до 30%. При этом на 17,5-20,5% возрастает удельный проплав, на 13,2-18,5% снижается расход топлива, сокращается подача вторичного воздуха и количество отходящих газов. Но при обогащении дутья кислородом увеличивается износ кладки свода и боковых стен печи.
Недостатками отражательной плавки являются: сравнительно низкая удельная производительность; низкое содержание SO2 в газах, не позволяющее их перерабатывать на серную кислоту; значительные капитальные и эксплуатационные затраты. В связи с указанными недостатками в настоящее время отражательные печи заменяют более прогрессивными автогенными технологиями.
Дата добавления: 2018-06-01; просмотров: 1435; Мы поможем в написании вашей работы! |
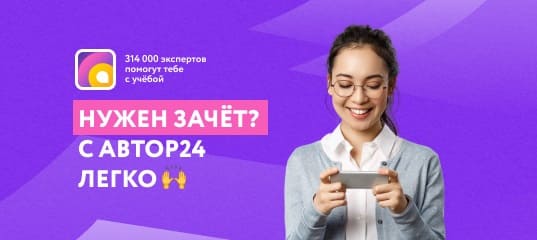
Мы поможем в написании ваших работ!