ТЕХНОЛОГІЯ СТИКОВОГО ЗВАРЮВАННЯ МЕТАЛІВ
ЗМІСТ
|
Вступ....................................................................................................................
1. Лабораторна робота №1 Вивчення будови і роботи
машини для стикового зварювання МС-802У......................................
2. Лабораторна робота №2 Технологія стикового
зварювання металів…….............................................................................
3. Лабораторна робота №3 Будова машини для
точкового зварювання типу МТ-1216.......................................................
4. Лабораторна робота №4 Технологія точкового
зварювання металів….................................................................................
5. Лабораторна робота №5 Вивчення будови і роботи
машини для конденсаторного зварювання ТКМ-7.................................
Рекомендована література..............……...........................................................
Лабораторна робота №1
ВИВЧЕННЯ БУДОВИ І РОБОТИ МАШИНИ ДЛЯ
СТИКОВОГО ЗВАРЮВАННЯ МС-802У
Мета роботи: Набути практичних навичок роботи на машині для стикового зварювання і вивчити її будову.
1.1 Короткі теоретичні відомості
Машини для стикового зварювання знайшли широке застосування для з’єднання деталей із сталі, кольорових металів і сплавів. За допомогою стикового зварювання з`єднують вироби з перерізом від сотих часток до декількох тисяч квадратних міліметрів.
Широко використовується стикове зварювання при виробництві ланцюгів, в прокатному виробництві для зварювання смуг і листів, при виготовленні автомобільних коліс, в інструментальному виробництві, для зварювання труб в котельному виробництві, зварювання залізничних рейок і в багатьох інших випадках.
|
|
По технологічному способу одержання з’єднань стикове зварювання поділяється на стикове зварювання опором і зварювання оплавленням. Машина МС-802У є з цієї точки зору універсальною.
Машина для стикового зварювання МС-802У, що показана на рисунку 1.1. складається із: корпусу 1, всередині якого вбудований зварювальний трансформатор 2, електромагнітний контактор 3, перемикач ступенів, блок пускача і система охолодження. Корпус призначений для закріплення на ній всіх основних вузлів. Зварювальний трансформатор використовується для отримання у зварювальному колі високого струму при відносно низькій напрузі. Трансформатор складається з сердечника, секціонованої первинної обмотки з відводами, вторинного витка з контактними колодками і трубками водяного охолодження. Перемикач ступенів потужності призначений для ступінчатого регулювання зварювального струму. Збільшуючи чи зменшуючи кількість витків первинної обмотки, ввімкнених у мережу, відповідно змінюють напругу на кінцях вторинного витка. Система водяного охолодження забезпечує охолодження всіх струмопідводящих частин машин, які дуже нагріваються в процесі зварювання. В стикових машинах в основному охолоджують вторинний виток трансформатора і струмопідводні електроди (губки).
|
|
Зверху зліва на корпусі машини змонтований нерухомий зажимний пристрій 4, призначений для закріплення і центрування зварювальних деталей в електродах (губках) машини, а також підводу до них зварювального струму. Основа зажимного пристрою електрично ізольована від корпуса прокладкою і втулками з шайбами. Справа від нього розміщений рухомий затискний устрій 5, який закріплений на напрямній штанзі 6, кінці якої знаходяться в двох підшипниках ковзання. Штанга виконана ексцентричною. При повороті її навколо вісі забезпечується вертикальне регулювання губок - центрування затиснутого виробу.
Рисунок 1.1 Загальний вигляд машини МС-802У
Справа на плиті встановлений механізм подачі і осадки 7, призначений для зближення зварювальних деталей і створення необхідного зусилля в момент зварювання і осадки. Він зв`язаний з рухомим затискачем коловим шарніром, за допомогою якого регулюється робочий хід рухомої частини (відстань між прижимами).
|
|
На важелі 8 змонтована електрична кнопка 9 для включення зварювального струму. Відключення відбувається автоматично вимикачем 10. Його спрацювання зв`язане з переміщенням рухомої частини машини.
Корпус машини безкаркасний. Для доступу в середину машини передбачені дверцята. Ліві дверцята з електричною блокіровкою мають задвижку для швидкого відкривання і доступу до перемикачів ступенів. Праві дверцята мають замковий пристрій. На задній стінці корпуса розміщений болт заземлення. Між рухомими і нерухомими затискаючими пристроями закріплено корито для захисту пристроїв, які розміщені всередині корпусу машини, від бризок та окалин.
Затискні пристрої мають радіальний хід верхньої затискаючої губки 11 і односторонній підвід зварювального струму до нижніх губок 12. Пристрої представляють собою важільно–ексцентрикові системи для затискання зварювальних виробів. При настройці на розмір виробу, що затискається, використовують ексцентриковий пристрій.
Верхня затискна губка 11 представляє собою гладкий змінний башмак, що не допускає відбитків на виробі, що затискається. Нижня губка 12 виготовлена з призматичним пазом для зручності укладки круглих виробів і зі скосом під кутом 65° для притиснення планкою. Струмопідвід охолоджується проточною водою і забезпечує достатній відвід тепла від контактних губок.
|
|
Електрична схема машини представлена на рис. 1.2, робота якої полягає в наступному. Поворотом пакетного вимикача ВП подається напруга на первинну обмотку трансформатора ТР. При подачі напруги на машині загорається сигнальна лампа 13 (рис. 1.1) на передній стінці машини. Натисненням на кнопку пуск КІ, яка розташована біля рукоятки привода осадки (див. рис. 1.1(поз 9)), вмикається пускач П. Замикаючим контактором ПІ пускач блокує кнопку КІ і залишається ввімкненим після її відпускання. Замикаючими контактами ПІІ і ПІІІ пускач вмикає коло з котушкою контактора Кт, і його силові замикаючі контакти КтІ і КтІІ замикають коло зварювального трансформатора ТС. Проходить процес зварювання.
При осадці спрацьовує кінцевий вимикач ВК (див. рис. 1.1, поз. 10) і вимикає котушку пускача П. Його нормально відкриті контакти ПІІ і ПІІІ вимикають котушку контактора Кт, який силовими контактами КтІ і КтІІ розриває коло зварювального трансформатора ТС. Кнопка КБ дозволяє вимкнення напруги від перемикача ступенів і зварювального трансформатора при відкриванні лівої дверці машини.
Кнопка К2 (див. рис. 1.1, поз. 14) використовується для відпалу зварних з’єднань. Для захисту кола управління від струмів короткого замикання в схемі передбачені плавкі запобіжники ПрІ-Пр4.
![]() |
Рисунок 1.2 –Електрична схема машини МС-802У
1.2 Обладнання
Машина для стикового зварювання МС-802У; заготівки.
1.3 Хід виконання роботи
1.3.1 Ознайомитись з питаннями техніки безпеки.
1.3.2 Підготувати машину до роботи. Зачистити деталі і затискні губки від бруду, іржи та ін. Включити систему водяного охолодження і перевірити герметичність з`єднань. Встановити необхідну відстань між затискними губками. Відрегулювати момент спрацювання кінцевого вимикача – пристрою відключення зварювального струму. Встановити потрібну ступінь зварювального трансформатора за допомогою перемикача ступенів по таблиці 1.1. Відрегулювати упори-обмежувачі кута повороту важеля осадки. Подати напругу на машину пакетним вимикачем ВП.
1.3.3 При зварюванні методом опору потрібно встановлювати деталі в затискні губки і закріпити їх (при відведеному в крайнє праве положення ричага). Підвести важіль в крайнє ліве положення і натиснути кнопку “Пуск” на важелі. Відбувається процес зварювання з автоматичним відключенням зварювального струму і пружинної осадки. Звільнити зварені вироби із затискачів.
1.3.4 При зварюванні методом оплавлення з підігрівом потрібно виконати слідуючи роботи. Підвести важіль так, щоб відстань між контактними губками дорівнювала 1,5...2 діаметра зварюваних деталей (для маловуглецевої сталі). Встановити деталі в затискачі і закріпити їх. Встановити відкидний щиток в робоче положення. Натиснути кнопку “Пуск” включення зварювального струму і розігріти заготовки періодичним замиканням і розмиканням їх торців при постійно включеному контакторі. При цьому відбувається процес переривчастого оплавлення. Витримка часу на замикання–розмикання і кількість циклів залежить від матеріалу і перерізу (діаметру ) заготовки і підбирається експериментально.
Після розігріву деталей до температури плавлення переходять до процесу постійного оплавлення, при якому зростає швидкість оплавлення металу. Швидкість оплавлення зростає і в момент оплавлення до заданого припуску починається осадка). В заданий момент після початку осадки спрацьовує кінцевий вимикач і відключає контактор. Послідуюча осадка відбувається без струму. На цьому зварювання закінчується.
Таблиця 1.1 - Ступені регулювання
№ ступеня | Положення перемикача | Ктр | |
№1 | №2 | ||
1 | 1 | 200 | |
2 | 2 | 1 | 180 |
3 | 3 | 160 | |
4 | 1 | 144 | |
5 | 2 | 2 | 124 |
6 | 3 | 104 |
1.4 Зміст звіту
1.4.1 Назва роботи мета і короткі теоретичні відомості.
1.4.2 Будова машини та її підготовка до роботи.
1.4.3 Висновки по роботі.
1.5 Контрольні запитання
1.5.1 Склад електричної та механічної частини машини МС–802У.
1.5.2 Принцип роботи машини МС–802У.
1.5.3 Робота електричної схеми машини МС–802У.
1.5.4 Порядок підготовки машини до роботи.
1.5.5 Порядок проведення зварювання.
ЛАБОРАТОРНА РОБОТА № 2
ТЕХНОЛОГІЯ СТИКОВОГО ЗВАРЮВАННЯ МЕТАЛІВ
Мета роботи: Ознайомитись з технологією і параметрами режиму стикового зварювання металів опором і оплавленням.
2.1 Короткі теоретичні відомості
Існує два способи стикового зварювання: стикове зварювання опором і стикове зварювання оплавленням. Підготовка деталей до стикового зварювання полягає у приданні їх торцям визначеної форми і ретельній очистці їх поверхонь. Торцеві поверхні обробляють механічним різанням за допомогою ножиців, пилок, гарячим та холодним висадженням на пресах, на металорізальних верстатах, а також газовим чи плазмовим різанням з наступним очищенням деталі від шлаку або хімічним травленням. Струмопідвідні поверхні на торці заготовок можуть оброблятися також дробострумінними або піскострумінними приладами і апаратами.
З метою рівномірного нагріву й однакового пластичного деформування під час осадження торці деталі спеціально обробляють. Форму та розміри перерізу заготовок після обробки бажано мати однаковими. Діаметри деталей в місці зварювання не повинні відрізнятися більш, між на 15 %, атовщини — відповідно 10%.
Зварювання опором проводять для деталей з поперечним перерізом до 100 мм2. Робочими параметрами режиму стикового зварювання опором є зусилля нагрівання або програма зміни зусилля під час зварювання, щільність струму або струм зварювання, тривалість нагрівання, установча довжина і зусилля затиску деталей у губках-електродах зварювальної машини. Кінці деталей випрямляють перед установленням у губках-електродах. Мінімальна установча довжина деталей компактного перерізу та припуску на осадку, а також зварювальний струм або його щільність, визначають з урахуванням площі поперечного перерізу і властивостей металу, що зварюють (таблиця 2.1).
Таблиця 2.1 Орієнтовні режими зварювання опором заготовок з круглим та квадратним перерізом із маловуглецевих сталей
Площа перерізу, мм2 | Щільність струму, А/мм2 | Час нагрівання, с | Установча довжина | Припуски на осадження, мм | ||
загаль-ний | під струмом | без струму | ||||
7 | 300 | 0,3 | 7 | 2,2 | 1,6 | 0,6 |
25 | 200 | 0,8 | 12 | 2,5 | 1,7 | 0,8 |
50 | 160 | 1,0 | 16 | 2,7 | 1,8 | 0,9 |
100 | 140 | 1,5 | 20 | 3,0 | 2,0 | 1,0 |
При стиковому зварюванні різнорідних металів з метою забезпечення рівномірного нагрівання установча довжина кожної деталі є відмінною . Для деталей із металу з більшою теплопровідністю установча довжина повинна бути більша.
Зусилля (тиск) осаджування визначає величину припуску на осадку – величину пластичного деформування деталей, а також якість очищення стиків від оксидів. Зусилля затискування деталей у губках зварювальної машини, щоб запобігти проковзуванню, повинно бути у 2-3 рази більшим зусилля осаджування.
Зварювання оплавленням застосовують для деталей з великим поперечним перерізом (вуглецеві і леговані сталі) та для тонкостінних деталей з розвитим перерізом (сталь з міддю, мідь з алюмінієм і т. ін.). При зварюванні оплавленням до підготовки торців деталей особливих вимог не ставлять. На зварювання деталі поступають безпосередньо після рубки чи газотермічного різання з окалиною.
До параметрів режиму стикового зварювання оплавленням, крім параметрів, характерних для зварювання опором відносяться швидкість оплавлення та швидкість осадки (таблиця 2.2)
Таблиця 2.2 – Орієнтовані режими зварювання оплавленням заготовок із вуглецевої сталі
Æ заго-товки, мм | Напруга, В | Щільність струму, А/мм2 | Установочна довжина в долях від діаметра заготовки | Швидкість оплавлення мм/с | Швид- кість осадки, мм/с | Питомий тиск осадки, МПа | Припуск при зварюванні, мм | |||
середня | перед осадкою | загаль-ний | на оплав-лення | на осадку | ||||||
6 8 10 | 4 4,5 5 | 10...50 | 0,5...1 | 0,5...1,5 | 2...5 | 15...20 | 80...100 | 6 8 12 | 4 5,7 9,5 | 2,0 2,3 2,5 |
Зварювання відбувається за наступною схемою. Деталі спочатку затискують у електродах-губках, потім на них подається напруга від зварювального трансформатора і тільки після цього повільно переміщують одну з деталей назустріч іншій з потрібною швидкістю до їх торкання. В момент виникнення первісного контакту в окремих точках торців крізь нього (при незначному зусиллі стиснення) приходить струм високої густини. В результаті цього метал контактів-перемичок миттєво розігрівається до температури кипіння та випаровування і відбувається його вибухоподібне руйнування. Під час вибуху частина металу перемичок витісняється із стику у вигляді іскр та бризок. Процес виникнення рідких перемичок та їх руйнування проходить безперервно до виникнення на торцевих поверхнях деталей рівномірного шару розплавленого металу.
Метал деталей нагрівається поступово за рахунок передачі тепла від іскрового зазору. Після прогріву деталей на потрібну глибину при оплавленні і при наявності шару рідкого металу на всій площині торців деталей їх стискують з підвищеною швидкістю осадження зусиллям осадки. Рідкий метал при осадженні разом із оксидами і іншими забрудненнями витискуються із стику у ґрат. Металеві зв'язки у з'єднання таким чином починають формуватися у рідкій фазі, а закінчуються у твердій фазі.
Внаслідок використання відносно жорстких режимів зварювання якісні з'єднання виникають при відношенні кінцевої площі перерізу стику (Sк) до площі деталей до зварювання (Sп) Sк/Sп<2, при якому обновлення поверхонь торців наближується майже до 100 %.
З'єднання деталей більших перерізів, коли виявляються недостатніми електрична та механічна потужності обладнання, здійснюється зварюванням оплавленням з попереднім підігрівом.
Кінці деталей при цьому способі спочатку підігрівають аналогічно зварюванню опором — їх періодично стискують невеликим осьовим зусиллям вмикають струм, що викликає виділення тепла у контакті деталь-деталь, та розмикають і розводять. Після підігрівання стиків до потрібної температури виконується з'єднання за схемою зварювання безперервним оплавленням. Закінчується процес осадженням. Осадка потрібна для витиснення із стику розплавленого та перегрітого твердого металу, що є забрудненим оксидами та для виникнення металевих зв'язків між деталями. При осадженні деформація металу допомагає реалізуватися процесу рекристалізації.
Для зварювання деталей з великим перерізом в ІЕЗ ім. Є.О. Патона розроблено два способи, що роблять більш ефективним підігрів під час оплавлення: зварювання з імпульсним оплавленням і з програмним керуванням напруги зварювання під час оплавлення.
При імпульсному оплавленні на головне поступове переміщення рухомої плити зварювальної машини накладаються додаткові механічні коливання з частотою 3—45 Гц і амплітудою 0,1—0,8 мм. Імпульсне оплавлення локалізує нагрів, розширює зону високих температур в деталях, запобігає швидку кристалізацію рідкого металу, зменшує потужність, що споживається під час зварювання, припуск на оплавлення та підвищує швидкість оплавлення.
Зварювання з програмуванням напруги (при незмінній швидкості оплавлений) потребує підвищеної початкової напруги для збудження оплавлення. Після виникнення стійкого оплавлення напругу зменшують до мінімально можливих значень, які здібні забезпечити стійке оплавлення. В фіналі оплавлення перед осадкою напругу холостого ходу зварювального трансформатора знову короткочасно підвищують для збільшення локальної стійкості процесу. При програмному регулюванні напруги у 3—5 разів знижується потужність зварювання та в 1,5—2 рази час зварювання.
2.2 Обладнання та матеріали
Машина для стикового зварювання МС-802У, лінійка, штангенциркуль, заготовки різного діаметру із різного матеріалу, шліфувальний папір, розривна машина.
2.3 Хід виконання роботи
2.3.1 Ознайомитись з питаннями техніки безпеки.
2.3.2 Провести стикове зварювання опором.
2.3.2.1 Для даної площі поперечного перерізу заготовки підібрати по таблиці 2.1 режим зварювання і налагодити машину.
2.3.2.2 Затиснути деталі в губках і виміряти відстань між ними.
2.3.2.3 Зварити заготовки. Повторно заміряти відстань між електродами.
2.3.2.4 Повторити пункти 2.3.2.2 та 2.3.2.3 для декількох стиків із маловуглецевої сталі, міняючи при цьому установочну довжину і визначити величину осадки.
2.3.2.5 Провести механічне випробування на розривній машині, отриманих зварних з’єднань.
2.3.2.6 Дати оцінку якості зварних стиків.
2.3.3 Провести стикове зварювання оплавленням.
2.3.3.1 Для даного діаметру (площі перерізу ) заготовок із вуглецевої сталі підібрати по таблиці 2.2 режими зварювання і налагодити машину.
2.3.3.2 Зварити заготовки методом оплавлення з нормальним відключенням струму (після початку осадки).
2.3.3.3 Повторити зварювання з передчасним відключенням струму (перед початком осадки).
2.3.3.4 Підрахувати сумарну величину осадки двох заготовок та провести механічне випробування на розривній машині.
2.3.3.5 Дати оцінку якості зварних стиків.
2.3.4 Оформити результати роботи у вигляді таблиці.
2.4 Зміст звіту
2.4.1 Назва роботи, мета і короткі теоретичні відомості
2.4.2 Результати дослідів і випробувань ( рисунки і таблиці).
2.4.3 Висновки по роботі.
2.5 Контрольні запитання
2.5.1 Умови видалення оксидних плівок зі зварювальних поверхонь при стиковому зварюванні.
2.5.2 Параметри процесу зварювання опором.
2.5.3 Параметри процесу зварювання оплавленням.
2.5.4 Механізм оплавлення торців при стиковому зварюванні.
2.5.5 Чим відрізняються зварні з’єднання після зварювання опором і оплавленням.
ЛАБОРОТОРНА РОБОТА №3
БУДОВА МАШИНИ ДЛЯ ТОЧКОВОГО
ЗВАРЮВАННЯ ТИПУ МТ-1216
Мета роботи: Набути практичних навичок роботи на машині для точкового зварювання і вивчити її будову.
3.1 Короткі теоретичні відомості
Машини для точкового зварювання поділяються наступним чином : по призначенню - на універсальні і спеціалізовані ; по характеру установки – на стаціонарні і пересувні; по виду живлення – на однофазні змінного струму, трьохфазні низькочастотні, трьохфазні з випрямленням у вторинному контурі, імпульсні; по способу підводу зварювального струму до виробу – на машини з одностороннім і двостороннім струмопідводом; по числу одночасно зварюваних точок – на одноточкові і багатоточкові; по типу привода стиснення – на машини з пневматичним, гідравлічним, електромеханічним, важільним, пружинним, електромагнітним приводами; по характеру переміщення електродів – на машини з прямолінійним рухом електродів і радіальним.
Точкові машини загального використання складаються з корпусу, який служить для встановлення всіх вузлів машини; вторинного контуру, зварювального трансформатора; апаратури керування.
Машина МТ-1216 (рисунок 3.1) складається з корпусу 1, зварювального трансформатора 2 з перемикачем ступенів 3, контактора тиристорного 4, регулятора циклу зварювання 5, струмопідводів верхнього і нижнього та привода зварного зусилля 6.
На верхній площині пневмоциліндра закріплений електропневматичний клапан 7 з мастилорозподільником 8 і регулятором тиску повітря 9. На боковій поверхні корпусу закріплений кран управління 10. На задній стінці корпуса встановлений автоматичний вимикач 11. Машина має переносну педальну кнопку 12.
Верхній струмопідвід складається з контактної колодки 13, гнучкої шини 14 і контактного конуса 15, в якому закріплюється електродотримач 16. Контактна колодка електрично ізольована від привода зварювального зусилля.
Нижній струмопідвід складається з кронштейна 17 і кришки 18, з`єднання яких утворює гніздо, в яке вставлений хобот 19 з закріпленим на ньому електродотримачем 20. Кронштейн вставляється на корпусі і закріплюється болтами. Передбачена можливість ступінчасто переставляти кронштейн на корпусі по висоті на 140 мм через кожні 70 мм, в залежності від форми зварювальних деталей.
Привод зварного зусилля, що забезпечує опускання верхнього електроду і стиснення деталі при зварюванні складається із направляючої, циліндра, кришки, двох поршнів зі штоками і ущільнювальних кілець.
Використання регулятора циклу зварювання РЦС-502, що виконаний на логічних елементах та призначений для управління циклом зварювання точкових машин змінного струму, дозволяє підвищити якість зварювання, надійність роботи і швидкість роботи машини (до 300 зварних точок за хвилину) за рахунок більш точного регулювання затримок часу, використання більш жорстких режимів зварювання, безконтактної схеми управління. Регулятор дозволяє змінювати час витримки в межах 0,02...2,0 секунди на 5-ти позиціях: попереднє стискання; стискання; зварювання; проковування; пауза.
![]() |
Рисунок 3.1 – Будова точкової машини МТ-1216
3.2 Обладнання
Машина для точкового зварювання МТ-1216, регулятор циклу зварювання РЦС-502-1.
3.3 Хід виконання роботи
3.3.1. Ознайомитись з питаннями техніки безпеки.
3.3.2. Провести налагодження машини і випробувати в дії всі механізми.
3.3.2.1 В залежності від форми і розмірів зварюваних деталей встановити відстань між верхнім і нижнім електродами.
3.3.2.2 Встановити величину оптимального робочого ходу верхнього електрода в залежності від товщини і форми зварюваних деталей.
3.3.2.3 Підключитись до водяної і повітряної магістралі.
3.3.2.4 Вийняти штепсельні ножі з перемикача ступенів.
3.3.2.5 Подати напругу, для чого ручку вимикача повернути в положення “Ввімкнено”.
3.3.2.6 Регулятором тиску встановити по манометру необхідний для зварювання даної деталі тиск повітря. Тиск підбирається в відповідності з зусиллям, необхідним для стиснення електродів по таблиці яка прикріплена на корпусі машини.
3.3.2.7 Відрегулювати дроселюючи клапани (обертанням регулюючого гвинта), які забезпечать плавне безударне опускання верхнього електрода.
3.3.3. Після опробування машини на холостому ходу встановити режими зварювання. Необхідний режим установлюється шляхом підбору величин зусилля стиснення електродів, ступеня трансформатора і часу проходження зварного струму через зварювані деталі.
3.3.4. Провести точкове зварювання.
3.4 Зміст звіту
3.4.1 Назва роботи, мета і короткі теоретичні відомості.
3.4.2 Будова точкової машини та її налагодження.
3.4.4 Висновки по роботі.
3.5 Контрольні запитання
3.5.1 Класифікація точкових машин.
3.5.2 Устрій машини.
3.5.3 Призначення складових вузлів машини.
3.5.4 Склад циклу зварювання
3.5.5 Принцип роботи машини та регулятора циклу зварювання
ЛАБОРОТОРНА РОБОТА №4
ТЕХНОЛОГІЯ ТОЧКОВОГО ЗВАРЮВАННЯ МЕТАЛІВ
Мета роботи: Ознайомитись з технологією і параметрами режиму точкового зварювання.
4.1 Короткі теоретичні відомості
Основними параметрами режиму точкового зварювання є: струм зварювальний (амплітудний або діюче його значення), тривалість проходження струму, зусилля стиснення деталей електродами до зварювання, під час та після зварювання (проковки), діаметр робочої поверхні електрода або радіус сферичної поверхні електрода певного діаметра.
Вихідними даними щодо визначення перерахованих параметрів є фізико-механічні властивості металу і товщина деталей, що зварюються.
Зі зменшенням товщини деталей щільність зварювального струму підвищується. Матеріали з низьким питомим опором потребують більшого струму, ніж матеріали з високим питомим опором.
При високій теплопровідності та температуропровідності металу зварювання ведуть на більш жорстких режимах, тобто зменшують час проходження та збільшують силу зварювального струму.
Зусилля тиску електродів також залежить від товщини зварюваних деталей і механічних властивостей металу, який зварюється.
З підвищенням коефіцієнту лінійного розширення та опору пластичної деформації треба збільшувати тиск на електродах та встановлювати більш м'які режими. Циклограми точкового зварювання наведені на рисунку 4.1
Розмір та якість зварних точок залежать також від форми, величини контактної робочої поверхні електродів. Форма робочої поверхні звичайно відповідає конфігурації зовнішньої поверхні деталей. Для листових, плоских чи не дуже зігнутих деталей застосовують циліндричну (плоску) чи сферичну форму робочої поверхні електродів. Параметри режиму зварювання звичайно визначають за спеціальними номограмами, таблицями чи обчислювальним шляхом.
На практиці для визначення режиму зварювання частіше використовують спеціальні таблиці. Наприклад, зварювання виробів із маловуглецевих сталей може відбуватися як на м'яких, так і на жорстких режимах (табл. 4.1) при обмежених величинах зусилля на електродах, які мають плоску робочу поверхню, звичайно використовують циклограму з постійним зусиллям і одним імпульсом зварювального струму (рис. 4.1 а). Якщо товщина деталей більш ніж 2 мм, зварювання відбувається за циклограмою з попереднім обтисненням деталей, а також з їх проковуванням зусиллями підвищеної величини (рис. 4.1 в, г). Маловуглецеві гарячекатані сталі з товщиною більше 4 мм потребують використання м'яких режимів з відносно низькою щільністю струму. Для зварювання цих товщин потрібно також підвищувати зусилля зварювання та проковування, а також і тривалість проходження струму.
зусилля зварювання;
зусилля проковування;
обтискування;
зварювальний струм;
струм підігріву;
тривалість струму зварювання;
тривалість імпульсу струму підігрівання перед зварювальним струмом;
тривалість імпульсу струму підігрівання після зварювального струму;
тривалість паузи між імпульсами струму;
тривалість модулювання зварювального струму;
тривалість підвищення зусилля проковування.
Рисунок 4.1–Типові циклограми зварювальних струму та зусилля при
точковому зварюванні
Таблиця 4.1– Орієнтовні режими точкового зварювання маловуглецевих холоднокатаних сталей товщиною до 2 мм.
Товщина металу, мм
| Æ ел-ду, мм | Характер режиму | ||||||||
жорсткий | середній | м'який | ||||||||
Fзв, dаН | Ізв, кА | tзв, с | Fзв, dаН | Ізв, кА | tзв, с | Fзв, dаН | Ізв, кА | tзв, с | ||
0,5 | 3,5 | 120 | 6,5 | 0,08 | 100 | 5,5 | 0,1 | 100 | 4 | 0,2 |
0,8 | 4,5 | 180 | 9,0 | 0,1 | 125 | 8,5 | 0,12 | 125 | 7,0 | 0,3 |
1,0 | 5,0 | 230 | 10,5 | 0,12 | 150 | 9,5 | 0,2 | 150 | 7,5 | 0,4 |
1,5 | 6,5 | 400 | 12 | 0,18 | 300 | 10,5 | 0,3 | 300 | 8,5 | 0,54 |
1,8 | 7,0 | 500 | 12,5 | 0,2 | 350 | 12,5 | 0,44 | 350 | 10,5 | 0,6 |
2,0 | 7,5 | 600 | 19 | 0,22 | 350 | 12,5 | 0,44 | 350 | 10,5 | 0,6 |
Якщо зварюють деталі різної товщини, робочі параметри режиму вибирають за найтоншою з них. Зварювання різнотовщинних деталей (при співвідношенні товщин > 1:3) утруднене відсутністю надійного проплавлення більш тонкої деталі. Щоб запобігти цьому, рекомендується на поверхні однієї деталі виготовляти технологічний виступ-рельєф або установити між електродами і тонкою деталлю змінний тепловий екран із металу з меншою теплопровідністю у вигляді стрічки товщиною 0,15-0,3 мм. Екран акумулює тепло в тонкій деталі, а інколи і сам служить додатковим джерелом теплоти. Комбінуючи склад та товщину стрічки-екрана, можна добиватися стійкого проплавлення. Дуже ефективний у цьому випадку є також спосіб зварювання листових конструкцій з додатковим кільцевим обтисненням тонкої деталі довкола точки. Цей спосіб забезпечує глибину проплавлення тонкої деталі до 30—70 %.
При зварюванні деталей із різноманітних матеріалів із-за неоднакового виділення та підведення тепла діаметр ядра та глибина проплавлення збільшується в деталях з високим питомим опором та меншим коефіцієнтом теплопровідності.
При з'єднанні деталей із різнорідних металів точковим зварюванням імпульсами уніполярного струму (постійного або струмом розрядження конденсаторів) слід ураховувати ефект Пельт’є. Цей ефект виявляється у виділенні додаткового або вбиранні такого ж тепла із загального у контакті деталь-деталь. Якщо електрони зварювального струму спрямовані із металу з відносно підвищеною енергією власних електронів у метал з відносно меншою енергією власних електронів, то спостерігається підвищення величини загального тепла на величину тепла Пельть'є. Якщо електрони прямують у протилежному напрямку, то загальне тепло між деталями зменшується на величину тепла Пельть'є. Для запобігання виникнення непроварів та суттєвого викривлення форми литого ядра в зв'язку з проявленням ефекту Пельть'є під час точкового зварювання, наприклад, нержавіючої сталі із низьковуглецевою потрібно, щоб негативний полюс джерела живлення постійно знаходився з боку нержавіючої сталі.
Способи зварювання різних матеріалів, що утворюють між собою під час розплавлення ряд твердих розчинів, які забезпечують номінальне проплавлення одночасно обох деталей, не відрізняються від способів, що використовуються при зварюванні деталей різної товщини.
4.2 Обладнання та матеріали
Машина для точкового зварювання МТ–1216, регулятор циклу зварювання РЦС–502–1, заготовки різної товщини із різного матеріалу, шліфувальний папір, розривна машина.
4.3 Хід виконання роботи
4.3.1 Ознайомитись з питаннями техніки безпеки.
4.3.2 Провести точкове зварювання пластин різної товщини з вуглецевої сталі на жорсткому та м’якому режимі. Режим зварювання підібрати по таблиці 4.1.
4.3.3 Оцінити продуктивність зварювання на різних режимах, провести візуальний контроль зварних з’єднань та провести механічне випробування отриманих з’єднань на зріз.
4.3.4 Для точкового зварювання пластин однакової товщини з вуглецевої сталі експериментально визначити мінімальний крок між точками, при якому їх розмір та форма будуть однаковими.
4.3.5 Провести механічне випробування на зріз зварних з’єднань з різним кроком між точками.
4.3.6 Оформити результати роботи у вигляді таблиці.
4.4 Зміст звіту
Назва роботи, мета і короткі теоретичні відомості.
Результати дослідів і випробувань ( рисунки і таблиці).
Висновки по роботі.
4.5 Контрольні запитання
4.5.1 Основні параметри точкового зварювання.
4.5.2 Типові циклограми при точковому зварюванні.
4.5.3 Основні умови отримання якісного з’єднання при точковому зварюванні.
4.5.4 Особливості точкового зварювання деталей різної товщини.
4.5.5 Шунтування струму при точковому зварюванні.
Лабораторна робота №5
Дата добавления: 2018-05-30; просмотров: 480; Мы поможем в написании вашей работы! |
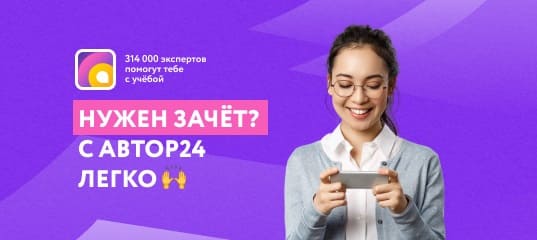
Мы поможем в написании ваших работ!