Технико-экономическое обоснование оптимального варианта заготовки
Определим коэффициент использования материала заготовки:
Для проката:
Для штамповки: КИ.М.П. КИ.М.Ш.
Вывод: в результате расчета исходной заготовки детали в условиях среднесерийного производства, штамповка наиболее приемлима, т.к. КИ.М.Ш.=0,66; КИ.М.П.=0,58; СИЗГ.Д.П.= 319,02 руб.>СИЗГ.Д.ШТ.= 287,01 руб.
Проектирование исходной заготовки.
Определим исходный индекс заготовки по ГОСТ 7505-89 по ранее назначенным классу точности Т, группе стали М, степень сложности С, ориентировочно определенной массе МШ=19,8кг.
Исходный индекс – ИИ13, класс точности – Т3, группа стали – М2, степень сложности С2.
Определим величины односторонних основных припусков 𝑍0 на обработку поверхности разъёма штампа 𝑍Ш и на изогнутость оси вала 𝑍Ф. Внесем их значения в таблицу 3.5.
Вычислим значения общих односторонних припусков на каждую обрабатываемую поверхность заготовки:
𝑍𝑖=𝑍0+𝑍СШ+𝑍Ф
0.5 0.2
Z1 = 1,8 + 0.5 = 2,3; Z3 = 1,8 + 0.5+ 0,2 = 2,5;
Z5 = 1,8+0,5 = 2,3; Z6 = 1,8 + 0,5+ 0,2 = 2,5;
Z9 = 1,8+ 0,5 = 2,3;Z12 = 1,8 + 0,5 + 0,2 = 2,5;
Z13 = 1,8+ 0,5 = 2,3; Z14 = 1,8 + 0,5+ 0,2 = 2,5;
Z15 = 1,8 + 0,5 = 2,3; Z17 = 1,8 + 0,5 + 0,2 = 2,5;
Z19 = 1,8 + 0.5 = 2,3;
Вычислим в соответствии с рисунком 2 размеры заготовки, используя размеры детали и величины припусков. Данные внесем в таблицу 3.5.
2АЗ = 2А + Z3*2 = 50 + 5 = 55мм.
2БЗ = 2Б + Z6*2 = 65 + 5 = 70мм.
2ВЗ = 2В + Z12*2 = 85 + 5 = 90мм.
|
|
2ДЗ = 2Д + Z14*2 = 76 + 5 = 81мм.
2ЕЗ = 2Е + Z17*2 = 60 + 5 = 65мм.
ЖЗ = Ж+Z1–Z5 = 55 + 2.3 – 2.3= 55мм.
ЗЗ =З + Z5 – Z9 = 142 + 2.3 – 2.3 = 142 мм.
ИЗ =И + Z9 + Z13 = 86 + 2,3 + 2,3 = 90,6 мм.
КЗ=K + Z13 + Z15 = 130 + 2,3 + 2,3 = 134,6 мм.
РЗ =Р + Z1 + Z19 = 435 + 2,3 + 2,3 = 439,6мм.
Код размера | Размер мм. | Номер поверхности | Шероховатость, Ra | Основной Z0мм. | На смещение штампа ZCШ. | На отклонение формы ZФ | Суммарный Ziмм. | Допуски отклонение мм. | Размеры мм. |
1 | 2 | 3 | 4 | 5 | 6 | 7 | 8 | 9 | 10 |
2А | ∅50 | 3 | 1,6 | 1,8 | 0,5 | 0,2 | 2,5 | ![]() | ![]() |
2Б | ∅65 | 6 | 1,6 | 1,8 | 0,5 | 0,2 | 2,5 | ![]() | ![]() |
2В | ∅85 | 12 | 6,3 | 1,8 | 0,5 | 0,2 | 2,5 | ![]() | ![]() |
2Д | ∅76 | 14 | 6,3 | 1,8 | 0,5 | 0,2 | 2,5 | ![]() | ![]() |
2Е | ∅60 | 17 | 1,6 | 1,8 | 0,5 | 0,2 | 2,5 | ![]() | ![]() |
Ж | 55 | 1 | 6,3 | 1,8 | 0,5 | - | 2,3 | | |
5 | 1,6 | ||||||||
З | 142 | 5 | 1,6 | 1,8 | 0,5 | - | 2,3 | | |
9 | 6,3 | ||||||||
И | 86 | 9 | 6,3 | 1,8 | 0,5 | - | 2,3 | | |
13 | 6,3 | ||||||||
К | 130 | 13 | 6,3 | 1,8 | 0,5 | - | 2,3 | | |
15 | 1,6 | ||||||||
Р | 435 | 1 | 6,3 | 1,8 | 0,5 | - | 2,3 | | |
19 | 6,3 |
Выбор черновых технологических баз.
При разработке схем базирования следует использовать следующие принципы:
- схема базирования должна обеспечивать нулевую погрешность базирования путём использования в качестве технологических баз одни и те же поверхности заготовки на протяжении всего технологического процесса;
|
|
- на первой операции обрабатывать те поверхности заготовки, которые на последующих операциях будут использоваться в качестве технологических баз;
- в качестве технологических баз на каждом переходе использовать измерительные базы получаемых размеров (принцип совмещения баз);
- обработку наиболее точных поверхностей будем планировать в конце техпроцесса.
Выбрать технологическое оборудование, технологическую оснастку.
Выбор станочных приспособлений
В среднесерийном производстве целесообразно применение специализированных групповых переналаживаемых приспособлений для обработки однотипных заготовок, отличающихся размерами и некоторыми конструктивными элементами. Станочные приспособления по составному технологическому маршруту приведены в таблице 6.9.
Выбор режущих инструментов
Режущие инструменты должны удовлетворять требования максимальной стойкости, что снижает время на переналадку оборудования. Вместе с этим не следует забывать о снижении затрат на инструмент, которые зависят от
стоимости инструментов. Наименование, количество и характеристики инструментов приведены в таблице 6.9.
Дата добавления: 2018-06-27; просмотров: 202; Мы поможем в написании вашей работы! |
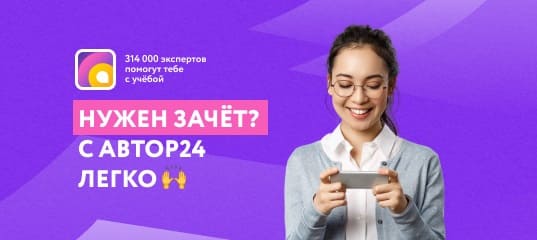
Мы поможем в написании ваших работ!