Токарная получистовая обработка.
1. Элементами резания при токарной обработке являются: скорость резания , подача
и глубина резания
.
При черновой обработке t и s назначают в зависимости от требований точности размеров и шероховатости обрабатываемой поверхности.
Подача = 0,5 мм.
Глубина резания = 1,2 мм. (количество проходов = 4).
Скорость резания - путь перемещения точки режущего лезвия относительно поверхности резания в единицу времени, т. е.
м/мин
м/мин.
где - произведение ряда коэффициентов. Важнейшими из них являются:
· kмv – коэффициент, учитывающий качество обрабатываемого материала;
, nв – коэффициент и показатель степени, характеризующие группу стали по обрабатываемости (
=1,0; nв= 1,13 ).
· kпv – коэффициент, отражающий состояние поверхности заготовки (kпv=0,9);
· kиv – коэффициент, учитывающий качество материала инструмента (kиv =0,8).
,
,
- соответствующие коэффициенты, учитывающие обрабатываемый материал, материал инструмента и другие факторы (
= 350;
= 0,15;
= 0,35);
m – показатель относительной стойкости (m = 0,2).
Т – оптимальная стойкость токарных резцов 30 – 90 мин.
2. На практике силы резания определяют экспериментально или рассчитывают по эмпирической формуле:
Н
где ,
,
- коэффициенты, зависящие от механических свойств обрабатываемого и инструментального материалов (
;
;
; n=0);
kp – поправочный коэффициент. Представляет собой произведение ряда коэффициентов, учитывающих фактические условия резания
|
|
kp=kмp·kφp·kγp·kλp·krp
kмp – коэффициент, учитывающий качество обрабатываемого материала
kφp; kγp; kλp ; krp – поправочные коэффициенты, учитывающие влияние геометрических параметров режущей части инструмента на составляющие силы резания при обработке стали (соответственно 1,08; 1,15; 1,0; 0,93).
3. Зная силу резания, определяют эффективную мощность резания по формуле:
кВт
кВт
4. Число оборотов детали в минуту определяем по формуле:
об/мин
об/мин.
5. Производительность труда при работе на металлорежущих станках тем выше, чем меньше штучное время обработки одной детали :
, мин
мин
где - основное, или машинное время, в течении которого происходит изменение формы или физического состояния детали;
,
мин
где L – длина прохода инструмента;
а – число проходов.
- вспомогательное, или ручное время на установку и снятие детали, подвод и отвод инструмента, управление станком и другие манипуляции;
, мин
мин
- время обслуживания – время технического перерыва, время организационного обслуживания места, время технического обслуживания;
мин
Топ – оперативное время:
|
|
Топ = То + Тв
Топ =0,15 + 0,21 = 0,36 мин
Тп.з – подготовительно – заключительное время – время, затраченное на получение задания, ознакомление с заданием, на сдачу готовых деталей на склад, на уборку рабочего места.
Тп.з.=0,6·Тшт
Тп.з.=0,6 · 0,41 = 0,25 мин
6. По данным и
рассчитывается коэффициент использования штучного времени:
Токарная чистовая обработка.
1. Элементами резания при токарной обработке являются: скорость резания , подача
и глубина резания
.
При черновой обработке t и s назначают в зависимости от требований точности размеров и шероховатости обрабатываемой поверхности.
Подача = 0,224 мм. (радиус при вершине резца r=1 мм).
Глубина резания = 0,25 мм. (количество проходов = 2).
Скорость резания - путь перемещения точки режущего лезвия относительно поверхности резания в единицу времени, т. е.
м/мин
м/мин.
где - произведение ряда коэффициентов. Важнейшими из них являются:
· kмv – коэффициент, учитывающий качество обрабатываемого материала;
, nв – коэффициент и показатель степени, характеризующие группу стали по обрабатываемости (
=1,0; nв= 1,13 ).
· kпv – коэффициент, отражающий состояние поверхности заготовки (kпv=0,9);
· kиv – коэффициент, учитывающий качество материала инструмента (kиv =0,8).
|
|
,
,
- соответствующие коэффициенты, учитывающие обрабатываемый материал, материал инструмента и другие факторы (
= 420;
= 0,15;
= 0,2);
m – показатель относительной стойкости (m = 0,2).
Т – оптимальная стойкость токарных резцов 30 – 90 мин.
2. На практике силы резания определяют экспериментально или рассчитывают по эмпирической формуле:
Н
где ,
,
- коэффициенты, зависящие от механических свойств обрабатываемого и инструментального материалов (
;
;
; n=0);
kp – поправочный коэффициент. Представляет собой произведение ряда коэффициентов, учитывающих фактические условия резания
kp=kмp·kφp·kγp·kλp·krp
kмp – коэффициент, учитывающий качество обрабатываемого материала
kφp; kγp; kλp ; krp – поправочные коэффициенты, учитывающие влияние геометрических параметров режущей части инструмента на составляющие силы резания при обработке стали (соответственно 1,08; 1,15; 1,0; 0,93).
3. Зная силу резания, определяют эффективную мощность резания по формуле:
кВт
кВт
4. Число оборотов детали в минуту определяем по формуле:
об/мин
об/мин.
5. Производительность труда при работе на металлорежущих станках тем выше, чем меньше штучное время обработки одной детали :
|
|
, мин
мин
где - основное, или машинное время, в течении которого происходит изменение формы или физического состояния детали;
,
мин
где L – длина прохода инструмента;
а – число проходов.
- вспомогательное, или ручное время на установку и снятие детали, подвод и отвод инструмента, управление станком и другие манипуляции;
, мин
мин
- время обслуживания – время технического перерыва, время организационного обслуживания места, время технического обслуживания;
мин
Топ – оперативное время:
Топ = То + Тв
Топ =0,2 + 0,28 = 0,48 мин
Тп.з – подготовительно – заключительное время – время, затраченное на получение задания, ознакомление с заданием, на сдачу готовых деталей на склад, на уборку рабочего места.
Тп.з.=0,6·Тшт
Тп.з.=0,6 · 0,55 = 0,33 мин
6. По данным и
рассчитывается коэффициент использования штучного времени:
Токарная тонкая обработка.
1. Элементами резания при токарной обработке являются: скорость резания , подача
и глубина резания
.
При черновой обработке t и s назначают в зависимости от требований точности размеров и шероховатости обрабатываемой поверхности.
Подача = 0,15 мм. (радиус при вершине резца r=1 мм).
Глубина резания = 0,1 мм.
Скорость резания - путь перемещения точки режущего лезвия относительно поверхности резания в единицу времени, т. е.
м/мин
м/мин.
где - произведение ряда коэффициентов. Важнейшими из них являются:
· kмv – коэффициент, учитывающий качество обрабатываемого материала;
, nв – коэффициент и показатель степени, характеризующие группу стали по обрабатываемости (
=1,0; nв= 1,13 ).
· kпv – коэффициент, отражающий состояние поверхности заготовки (kпv=0,9);
· kиv – коэффициент, учитывающий качество материала инструмента (kиv =0,8).
,
,
- соответствующие коэффициенты, учитывающие обрабатываемый материал, материал инструмента и другие факторы (
= 420;
= 0,15;
= 0,2);
m – показатель относительной стойкости (m = 0,2).
Т – оптимальная стойкость токарных резцов 30 – 90 мин.
2. На практике силы резания определяют экспериментально или рассчитывают по эмпирической формуле:
Н
где ,
,
- коэффициенты, зависящие от механических свойств обрабатываемого и инструментального материалов (
;
;
; n=0);
kp – поправочный коэффициент. Представляет собой произведение ряда коэффициентов, учитывающих фактические условия резания
kp=kмp·kφp·kγp·kλp·krp
kмp – коэффициент, учитывающий качество обрабатываемого материала
kφp; kγp; kλp ; krp – поправочные коэффициенты, учитывающие влияние геометрических параметров режущей части инструмента на составляющие силы резания при обработке стали (соответственно 1,08; 1,15; 1,0; 0,93).
3. Зная силу резания, определяют эффективную мощность резания по формуле:
кВт
кВт
4. Число оборотов детали в минуту определяем по формуле:
об/мин
об/мин.
5. Производительность труда при работе на металлорежущих станках тем выше, чем меньше штучное время обработки одной детали :
, мин
мин
где - основное, или машинное время, в течении которого происходит изменение формы или физического состояния детали;
,
мин
где L – длина прохода инструмента;
а – число проходов.
- вспомогательное, или ручное время на установку и снятие детали, подвод и отвод инструмента, управление станком и другие манипуляции;
, мин
мин
- время обслуживания – время технического перерыва, время организационного обслуживания места, время технического обслуживания;
мин
Топ – оперативное время:
Топ = То + Тв
Топ =0,24 + 0,33 = 0,57 мин
Тп.з – подготовительно – заключительное время – время, затраченное на получение задания, ознакомление с заданием, на сдачу готовых деталей на склад, на уборку рабочего места.
Тп.з.=0,6·Тшт
Тп.з.=0,6 · 0,65 = 0,39 мин
6. По данным и
рассчитывается коэффициент использования штучного времени:
Дата добавления: 2018-05-12; просмотров: 206; Мы поможем в написании вашей работы! |
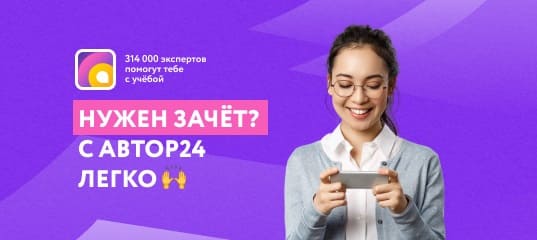
Мы поможем в написании ваших работ!