Расчет диаметральных размеров
Расчет припусков на диаметральную обработку поверхности Ø (IT6).
Технологические переходы обработки поверхности Ø | Элементы припуска, мкм | Расчетный припуск, мкм | Расчетный размер, мм | Допуск, мкм | Предельные размеры, мм | Предельные значения припуска, мкм | |||||
Rz | T | Ρ | ε | 2Zmin | dp | δ | dmin | dmax | ![]() | ![]() | |
Заготовка | 260 | 160 | 72 | - | 91,763 | 2300 | 91,763 | 94.063 | |||
Черн. точение | 100 | 100 | 4.32 | 120 | 1120 | 90,643 | 870 | 90,643 | 91.513 | 1120 | 2550 |
П/чист. точение | 50 | 50 | 3.6 | - | 409 | 90,234 | 350 | 90,234 | 90.584 | 409 | 929 |
Черновое шлифование | 10 | 20 | 2.16 | 30 | 167.2 | 90,067 | 140 | 90,067 | 90.207 | 167 | 377 |
Однократное шлифование | 5 | 10 | 1.44 | - | 24.3 | 90,043 | 54 | 90,043 | 90.097 | 24 | 109 |
Тонкое шлифование | 0.63 | 0 | - | 30 | 72.8 | 89.97 | 22 | 89.97 | 90 | 73 | 105 |
Расчет пространственного отклонения
[1, таб.4.7]
· Черн. точение
· Получист. точение
· Черн. шлифование
· Однокр. шлифование
Определение расчетных припусков
[1, таб.4.2]
;
Шлифование после ТО:
( при наличии
)
( при отсутствии
)
Определение расчетных размеров
dp5 = 89,97 мм;
dp4= 89,97+0,0728 = 90,043 мм;
|
|
dp3 = 90,043 +0,0243 = 90,067 мм;
dp2 = 90,067 +0,1672 = 90,234 мм;
dp1 = 90,234 +0,409 = 90,643 мм;
dpзаг = 90.643 +1.120= 91.763мм
Определение предельных размеров
dmax5 = 89,97+0.022= 89.992 мм;
d max4= 90.043+0.054=90.097 мм;
d max3 = 90.067 +0.14= 90.207 мм;
d max2= 90.234 +0,35 = 90.584 мм;
d max1 = 90.643 +0.87= 91.513 мм;
d max заг = 91.763+2,3= 94.063 мм.
Определение предельных значений припуска
=90.043 – 89,97 = 73 мкм;
=90.067– 90.043 = 24 мкм;
=90.234 – 90.067 = 167 мкм;
=90.643 – 90.234= 409 мкм;
=91.763 – 90.643 = 1120 мкм.
= 90.097 – 89.992 = 105 мкм;
= 90.207 – 90.097 = 109 мкм;
= 90.584 – 90.207 = 377 мкм;
=91.513 – 90.584 =929 мкм;
=94.063 – 91.513 = 2550 мкм.
Проверка
Рисунок 7.1 Схема графического расположения припусков и допусков на
обработку поверхности Ø втулки
Расчет припусков на диаметральную обработку поверхности Ø 45+0,06 (IT8).
Технологические переходы обработки поверхности Ø 45+0,06 (IT8) | Элементы припуска, мкм | Расчетный припуск, мкм | Расчетный размер, мм | Допуск, мкм | Предельные размеры, мм | Предельные значения припуска, мкм | |||||
Rz | T | ρ | ε | 2Zmin | dp | δ | dmin | dmax | ![]() | ![]() | |
Заготовка | 260 | 160 | 36 | - | 43.309 | 1800 | 41.509 | 43.309 | |||
Черновое расстачивание | 100 | 100 | 5,4 | 100 | 1052 | 44.361 | 620 | 43.741 | 44.361 | 1050 | 2080 |
П/ч растачивание | 20 | 25 | 4,5 | - | 410.8 | 44.772 | 250 | 44.522 | 44.772 | 410 | 780 |
Черновое шлифование | 10 | 20 | 2,7 | 100 | 249 | 45.021 | 100 | 44.921 | 45.021 | 250 | 400 |
Хонингование | 5 | 0 | 1,8 | - | 25.4 | 45.046 | 62 | 44.984 | 45.046 | 24 | 62 |
Хонингование | 5 | 0 | 1.8 | - | 13,6 | 45.06 | 62 | 45 | 45.06 | 14 | 14 |
|
|
Расчет пространственного отклонения
· Рассверливание
· Получист.растачивание
· Черн.шлифование
· Хонингование
· Хонингование
Определение расчетных припусков
Шлифование после ТО:
( при наличии
)
( при отсутствии
)
Определение расчетных размеров
dp5= 45,06 мм;
dp4= 45,06 – 0,0136= 45,0464 мм;
dp3 = 45,0464 – 0.0254= 45,021 мм;
dp2 = 45,021 – 0.249 = 44,772 мм;
dp1 = 44,772 – 0.4108 = 44.3612 мм;
dpзаг = 44.3612 – 1.052 = 43.3092 мм
Определение предельных размеров
dmin заг = 43.309– 1,8 = 41.509 мм;
dmin 1 = 44.361 – 0.62 = 43.741 мм;
dmin 2 = 44,772 – 0.25 = 44,522 мм;
dmin 3 = 45.021 – 0,1 = 44,921мм.
dmin 4 = 45,046 – 0,062 = 44.984мм.
dmin 5 = 45.06 – 0,062 = 44.994мм.
Определение предельных значений припуска
= 44.994 – 44,98= 14 мкм;
= 44.984 – 44,921= 62 мкм;
= 44,921– 44,522 = 400 мкм;
= 44,522 – 43.741 = 780 мкм;
|
|
= 43.741 – 41.51 = 2080 мкм
= 45.06– 45.054= 14 мкм;
= 45.054– 45.02= 24 мкм;
= 45.02– 44.77 = 250 мкм;
= 44,77 – 44.36 = 410 мкм;
= 44.36 – 43.31= 1050 мкм
Проверка
Рисунок 7.2 Схема графического расположения припусков и допусков на
обработку отверстия Ø 45+0,06 втулки
Расчет суммарной погрешности обработки
Диаметр Ø112, обрабатывается получистовым точением в патроне станка 16К20, с допуском IT12. Необходимо определить суммарную погрешность обработки Ø112. Заготовка - втулка из чугуна 45 ( =430 МПа)
Необходимо получить поверхность втулки Ø 112-0,35 по IT12 соответственно.
Условия обработки: резец с пластиной из твердого сплава Т15К6: ,
, подача S=0,32 мм/об., V=130 м/мин. [3, c.265-270 ]
Величину погрешности ΔИ, вызванную размерным износом резца по
[3, с.73]
L – длинна пути резания при обработки партии N деталей определяется:
Для сплава Т15К6 интенсивность изнашивания [3, с.74]
Определение колебания отжатий системы
[3, с.27]
|
|
Wmax; Wmin – наибольшая и наименьшая податливость системы;
РYmax ; РYmin – наибольшее и наименьшее составляющей силы резания.
Для станка 16К20, нормальной точности наибольшее и наименьшее допустимые перемещения продольного суппорта под нагрузкой 40кН, составляют соответственно 1000 и 630 мкм.
Наибольшая и наименьшая нормальная составляющая силы резания определяется согласно[4, с.271-275], исходя из условий задачи. На предшествующей операции заготовка была обработана черновым точением (IT14), следовательно возможно колебание припуска на величину 1/2 IT 12, что для диаметра составит 0.4/2=0.2мм, а колебание глубины резания
Определение погрешности, вызванной геометрическими неточностями станка согласно [3, с.53].
С – допустимое отклонение от параллельности оси шпинделя направляющим станины в плоскости выдерживаемого размера на длине L; l – длина обрабатываемой поверхности.
Для токарных станков нормальной точности при наибольшем диаметре обрабатываемой поверхности до 450мм, С=20, на длине L =450мм.[3, табл. 23]. При длине обработки l=120мм.
Определение погрешности настройки
[3, с.70-73]
ΔР – погрешность регулирования положения резца;
;
- коэффициенты учитывающие отклонения закона распределения величины ΔР и ΔИЗМ от нормального закона распределения;
ΔИЗМ – погрешности измерения размера детали.
Для заданных условий обработки [3, с.71-72] и
.
Определение температурной деформации технологической системы, приняв их равными 15% от суммы остальных погрешностей
[3, с.76]
Определение суммарной погрешности обработки
Данное условие удовлетворяет наши требования. Проанализировав значения элементарных погрешностей делаем вывод о том, что существенным мероприятием по снижению суммарной погрешности размера ø112-0.35 является снижение погрешности ΔИ, обусловленной размерным износом режущего инструмента.
Схемы базирования
Теоретическая схема базирования Базирование по Гост 3.1107-81
005 Токарная
010 Токарная
015 Фрезерная
020 Сверлильная
025 Шлифовальная
030 Шлифовальная
Заключение
В ходе курсовой работы проведена разработка технологического процесса обработки детали – втулки. На основе полученных знаний был определен тип производства - мелкосерийное - и соответствующая ему форма организации работ.
Для вышеупомянутого типа производства было произведено экономическое обоснование выбора метода получения исходной заготовки. В качестве заготовки была принята штамповка.
В курсовой работе были рассмотрены ряд вопросов, которые в итоге нам позволило разработать технологический процесс изготовления втулки. Во время этой работы были рассчитаны режимы резания, было произведено нормирование технологического процесса, выбрали технологическое оборудование, рассчитали припуски на обработку детали.
Список использованной литературы
1. Горбацевич, А. Ф.Курсовое проектирование по технологии машиностроения: учебное пособие для вузов / А. Ф. Горбацевич, В. А. Шкред. – 5-е изд., стереотипное. Перепечатка с четвертого издания 1983г. – М.: ООО ИД Альянс, 2007. – 256 с.
2. Расчет припусков и межпереходных размеров в машиностроении: учебное пособие / В. И. Аверчинков [и др.]; Под ред. В. А. Тимирязева – 2-е изд., стереотипное – М.: Высшая школа, 2007. – 272 с, ил.
3. Справочник технолога-машиностроителя. В 2-х т. Т. 1 /Под ред. А. Г. Косиловой и Р. К. Мещерякова. – 4-е изд., перераб. и доп. – М.: Машиностроение, 1986 г. 656 с, ил.
4. Справочник технолога-машиностроителя. В 2-х т. Т. 2/Под ред. А. Г. Косиловой и Р. К. Мещерякова. – 4-е изд., перераб. и доп. – М.: Машиностроение, 1986 г. 496 с, ил.
5. Колкер, Я. Д. Базирование и базы в машиностроении: учебное пособие для машиностроительных вузов / Я. Д. Колкер, О. Н. Руднев – К.: Выща шк., 1991. – 100 с, ил.
6.Общемашиностроительные нормативы времени и режимов резания для нормирования работ, выполняемых на универсальных и многоцелевых станках с числовым программным управлением/ под ред. С. Ю. Романова Часть 2. М.: Экономика, 1990.-472с.
Дата добавления: 2018-05-12; просмотров: 1163; Мы поможем в написании вашей работы! |
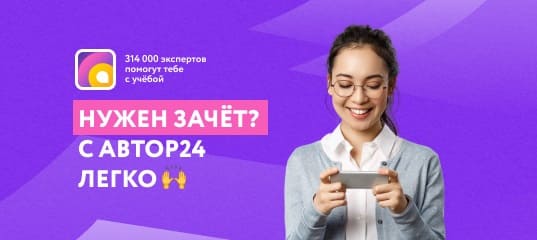
Мы поможем в написании ваших работ!