Выявление технологических цепей
Введение
Темой курсовой работы является разработка технологического процесса изготовления детали типа втулки. Эффективность технологического процесса и качество выпускаемой продукции напрямую зависит от развития машин, станков и аппаратов, а так же определяется совершенствованием применяемых на производстве и разработкой принципиально новых методов обработки.
Выбор оптимального варианта изготовления заготовки зависит от ее конфигурации, материала и объема производства. Особое внимание уделяется технико-экономическим расчетам.
Цель данной курсовой работы заключается в том, чтобы правильно применить теоретические знания, полученные в результате изучения общетехнических и специальных дисциплин за период обучения.
В процессе курсовой работы перед нами стояли следующие задачи: определение типа производства, анализ возможности изготовления втулки по двум маршрутам, расчет возможной суммарной погрешности обработки, выявление технологических цепей и расчет технологических размеров и припусков. Одна из основных задач данной курсовой работы - это правильно составленная технология изготовления детали типа вал, так как непосредственно от построения технологии напрямую зависит производительность и экономичность данного технологического процесса.
Определение квалитетов размеров обрабатываемой детали, методов и этапов обработки элементарных поверхностей
|
|
Табл.1.1 Квалитеты линейных размеров
Размер, мм | А1=22+0,21 | А2=44-0,25 | А3=60+0,74 | A4=18+0,43 | A5=18+0,43 | A6=8+0,36 |
Квалитет | IT 12 | IT 12 | IT 14 | IT 14 | IT 14 | IT 14 |
Размер, мм | А7=6+0,3 | А8=D/2=5+0,3 | ||||
Квалитет | IT 14 | IT 14 |
Табл.1.2 Квалитеты диаметральных размеров
Размер, мм | D1=112-0.35 | D2=80+0,12 | D3=45+0,06 | D4=90-0,03 |
Квалитет | IT 12 | IT 10 | IT 8 | IT 6 |
Табл.1.3 Шероховатость поверхностей
№ поверхности | 2, 3 | 1,4,7 | 5, 8 | 6 |
Шероховатость | Rz20 | Rz40 | Ra0,63 | Ra1,0 |
Рис.1.1 Заданная деталь
Таблица 1.4 Методы и этапы обработки
№ пов-ти | IT | Шероховатость | № этапа | Наименование операций | |
7 | 14 | Rz40 | 1 | черн. подрезка торца | |
1 | 12 | Rz40 | 1 | черн. подрезка торца | |
2 | п/ч токарная | ||||
2 | 12 | Rz20 | 1 | черн. токарная | |
2 | п/ч токарная | ||||
3,4 | 12 | Rz20 | 1 | черн. растачивание | |
2 | п/ч растачивание | ||||
5,6 | 7 | Ra0,63 | 1 | черн.токарная | |
2 | п/ч токарная | ||||
3 | черн.шлифование | ||||
4 | однократ.шлифование | ||||
5 | тонкое шлифование | ||||
8 | 8 | Ra0,63 | 1 | черн. растачивание | |
2 | п/ч растачивание | ||||
3 | черн.шлифование | ||||
4 | хонингование | ||||
5 | хонингование | ||||
9 | 14 | Rz40 | 1 | черн.токарная | |
10,11 | 9 | Ra2,5 | 1 | черн.растачивание | |
2 | п/ч растачивание
| ||||
3 | черн.шлифование | ||||
12 | 14 | Rz40 | 1 | фрезерование | |
13 | 12 | Rz40 | 1 | фрезерование | |
2 | сверление | ||||
3 | сверление |
Выбор типа производства
Расчет основного технологического времени на переходы ТО (*10-3) [1, c.146]
Поверхность №7
1. Черновая токарная
ТО=0,0224(D2 – d2) = 0,0224* (902 – 452) = 136,08*10-3 мин.
Поверхность №1
1. Черновая подрезка торца
ТО=0,0224(D2 – d2) = 0,0224(922 – 802) = 46,2336*10-3 мин.
2. Получистовая подрезка торца
ТО=0,011(D2 – d2) =0,011(922 – 802) = 22,704 *10-3 мин.
Поверхность №2
1. Черновая токарная
ТО= 0,017dl = 0,017*112*18 = 342,72 *10-3 мин.
2. Получистовая токарная
ТО=0,1dl = 0,1*112*18 = 201,6*10-3 мин.
Поверхность №3,4
1. Черновое растачивание
ТО= 0,134dl = 0,134*80*22 = 235,84*10-3 мин.
2. Получистовое растачивание
ТО= 0,18dl = 0,18*80*22 = 316,8*10-3 мин.
Поверхность № 5,6
1. Черновая токарная
ТО= 0,17dl = 0,17*90*60 = 918 *10-3 мин.
2. Получистовая токарная
ТО=0,1dl = 0,1*90*60 = 540*10-3 мин.
3. Черновое шлифование
ТО= 0,07dl = 0,07*90*60 = 378*10-3 мин.
4. Однократное шлифование
ТО= 0,1dl = 0,1*90*60 = 540*10-3 мин.
5. Тонкое шлифование
ТО= 0,15dl = 0,15*90*60 = 810*10-3 мин.
Поверхность №8
1. Черновое растачивание
ТО = 0,134dl = 0,134*45*64 = 385,9 *10-3 мин.
2. Получистовое растачивание
ТО = 0,18dl = 0,18*45*64 = 518,4 *10-3 мин.
3. Черновое шлифование
ТО = 0,146dl = 0,146*45*64 = 420,48 *10-3 мин.
|
|
4. Хонингование
ТО = 126*0,05 = 6,3*10-3 мин.
5. Хонингование
ТО = 126*0,03 = 3,78*10-3 мин.
Поверхность №9
1. Черновая токарная
ТО= 0,17dl = 0,17*92*8 = 125*10-3 мин.
Поверхность №10, 11
1. Черновое растачивание
ТО = 0,134dl = 0,134*70*18 = 168*10-3 мин.
2. Получистовое растачивание
ТО = 0,18dl = 0,18*70*18 = 226,8*10-3 мин.
3. Черновое шлифование
ТО = 0,146dl = 0,146*70*18 = 184*10-3 мин.
Поверхность №12
1. Черновое фрезерование
ТО = 7l = 7*90 = 630*10-3 мин.
Поверхность №13
1. Черновое фрезерование
ТО = 7l = 7*36 = 252*10-3 мин.
2. Сверление
ТО = 0,52dl = 0,52*10*10 = 52*10-3 мин.
3. Cверление
ТО = 0,52dl = 0,52*16*1 = 8*10-3 мин.
Суммирование ТО по группам операций
Токарные операции
ТОток=0,136+0,046+0,023+0,343+0,202+0,236+0,317+0,918+0,540+0,386+0,518+0,125+0,168 =3,958 мин.
Шлифовальные операции
ТОшл = 0,378+0,540+0,810+0,420+0,184= 2,332 мин.
Хонингование
ТОхон=0,0063+0,00378=0,01008 мин.
Фрезерные операции
ТОфр = 0,630+0,252 = 0,882 мин.
Сверление
ТОсвер=0,052+0,008=0,06 мин.
Расчет штучно-калькуляционного времени ТШ-К
ТШ-К = ᵠкТО . [1, с. 147]
Для токарных операций
ТШ-Кток = ᵠКтокТОток = 2,14*3,958 = 8,47 мин.
Для операций шлифования
ТШ-Кшл = ᵠКшлТОшл = 2,10*2,332 = 4,8972 мин.
Для операций хонингования
ТШ-Кфр = ᵠКфрТОфр = 2,10*0,01008 = 0,021168 мин.
|
|
Для операций фрезерования
ТШ-Кфр = ᵠКфрТОфр =1,84*0,882=1,62288 мин.
Для операций сверления
ТШ-Кфр = ᵠКфрТОфр =1,72*0,06=0,1032 мин.
Расчет коэффициента закрепления операций [1, с. 20]
Токарные операции
1. mp = .
2. р = 1.
3. mp/p = 0,07/1 = 0,07.
4. O = 0,9/0,07 =12,86≈ 13.
Операции шлифования
1. mp =
2. р = 1.
3. mp/p = 0,045/1 = 0,045.
4. O = 0,9/0,045 = 20.
Операцияи хонингования
1. mp = .
2. р = 1.
3. mp/p = 0,00019/1 = 0,00019.
4. O = 0,9/0,00019 = 4736.
Фрезерные операции
1. mp = .
2. р = 1.
3. mp/p = 0,015/1 = 0,015.
4. O = 0,9/0,015 = 60.
Операции сверления
1. mp =
2. р = 1.
3. mp/p = 0,001/1 = 0,001.
4. O = 0,9/0,001 = 900.
- крупносерийное производство.
Такт производства
Количество деталей в партии для одновременного запуска
где а – периодичность запуска в днях.
Принимаем n = 189.
Число смен
[1, c.23]
Принимаем CПР = 3.
Пересчет числа деталей в партии
Выбор исходной заготовки
В качестве вариантов получения исходной заготовки рассмотрим следующие:
1. Литье в кокиль.
2. Литье в землю.
Расчет объема детали
= 507656,36 мм3.
Расчет массы детали
𝜌 = 7,6 г/см3 ; V = 507656,36 мм3 = 508см3.
q = 𝜌*V = 7,6*508 = 3860,8 г = 3,86 кг.
1 вариант
Рисунок 3.1 Конфигурация литья в кокиль.
Назначение припусков:
черновое подрезание 2мм;
получистовое подрезание 1,2 мм;
Длина заготовки с учетом припусков
Расчет массы заготовки
=657см3.
Q=Vp=657*7,6=4993,2=4,993кг.
Стоимость заготовки.
С1=36000 руб. KT=1,1. KC=0,7. KM=1,04. KB=0,91. KП=0,52. Q=4,993 кг. q=3,86 кг.
65,3 руб.
Литье в кокиль.
Расчет себестоимости
=553132,74мм3=553см3.
Q=Vp=553*7,6=4202,8г = 4,203 кг.
74,96=75 руб.
Литье в землю.
Расчет себестоимости
Cn.з.=Сз+Сч.з.+Еn+(Кс+Кз)
, [1, c.30]
где Сп.з – приведенные затраты на рабочем месте, коп/час;
Тшк(ш-к) – штучное или штучно-калькуляционное время выполнения данной операции.
То=0.17*112*104=0.17*112*104*10-3 =1,9802мин.
Тш-к=То*φ=1,19*2.14=4.237мин.
Ц=60000 руб.
f=880*660=0.6 м2.
nз=0.95. KM=1.6. Eн=0.15. M=2. 2-й разряд 54.8 .
где Q – масса заготовки, кг;
S – цена за 1 кг заготовки, руб;
q – масса готовой детали, кг;
Sотх – цена 1т отходов, руб.
Сз=ECтфKУ, E=1,53. Стф=54.8*100 коп/ч. K=1, У=1.
Сз=1.53*5480*1*1=8384.4 коп/ч.
Cn.з.=Сз+Сч.з.+Еn+(Кс+Кз)=8384,4+7136+0,15*(1567,6+4,92)=15726,278 коп/ч.
Sзаг+Со=65,3+8,54=73,84 руб.
В результате принимаем литье в землю как метод получения исходной заготовки ввиду ее меньшей себестоимости.
4 Разработка двух маршрутов обработки детали с построением размерных схем и графов
Рисунок 4.1 Маршрут обработки детали (1 вариант)
Технологическое дерево
Исходное дерево
Технологический граф
Рисунок 4.2 Маршрут обработки детали (2 вариант)
Технологическое дерево
Исходное дерево
Технологический граф
Выявление технологических цепей
Для первого варианта
1) | –A8+S13 = 0; | А8=S13; | (S13) |
2) | – A7+S11 = 0; | A7=S11; | (S11) |
3) | – A1+S5 = 0; | A1=S11; | (S5) |
4) | -A6+S5=0; | A6=S3; | (S3) |
5) | -A2+S15=0; | A2=S15; | (S15) |
6) | -z2+S2=0; | Z2=S2; | (S2) |
7) | -z12-S15+S14=0; | Z12=S14-S15 | (S14) |
8) | -z13-S14+S10=0; | Z13=S10-S14; | (S10) |
9) | -z14-S10+S9=0; | Z14=S9-S10; | (S9) |
10) | -z15-S9+S8=0; | Z15=S8-S9; | (S8) |
11) | -z6-S1+S5=0; | Z6=S5-S4; | (S4) |
12) | -A5-A1+S16=0; | S16=A1+A5; | (S16) |
13) | -z10-S6+S16=0; | Z10=S16-S6; | (S6) |
14) | -A3-A2+S7=0; | S7=A3+A2; | (S7) |
15) | -A3-A4+S12=0; | S12=A3+A4; | (S12) |
16) | -z19-S7-S2+S1=0; | Z19=S1-S2-S7; | (S1) |
17) | -z1+З1-S1=0; | Z1=З1-S1; | (З1) |
18) | -z16-S8-S2+S1-З3=0; | Z16=S1-S2-S8-З3; | (З3) |
19) | -z9+З2-S1+S2+S6=0; | Z9=З2+S6+S2+S1; | (З2) |
∑и.б. = ∑к.б. = 8
∑исх.зв. = 34
Для второго варианта
1) | –A2+S15 = 0; | А2=S15; | (S15) |
2) | – A7+S10 = 0; | A7=S10; | (S10) |
3) | – A8+S12 = 0; | A8=S12; | (S12) |
4) | -z12-S15+S14=0; | Z12=S14-S15 | (S14) |
5) | -z13-S14+S13=0; | Z13=S13-S14; | (S13) |
6) | -z14-S13+S5=0; | Z14=S5-S13; | (S5) |
7) | -A6+S5-S6=0; | A6=S5-S6; | (S6) |
8) | -z2+S4-S5=0; | Z2=S4-S5; | (S4) |
9) | -A1+S5-S8=0; | A1=S5-S8; | (S8) |
10) | -z6+S7-S8=0; | Z6=S7-S8; | (S7) |
11) | -A5+S8+S3-A3=0; | A5+A3=S8+S3; | (S3) |
12) | -z15-S3-S2=0; | z15=S3-S2; | (S2) |
13) | -z1+S1-S3-S4=0; | z1=S1-S3-S4; | (S1) |
14) | -z16+S2-S1+З3=0; | z16=S2-S1+З3; | (З3) |
15) | -z19-S1+З1=0; | z12=З1-S1; | (З1) |
16) | -A5-A1+S16=0; | S16=A5+A1; | (S16) |
17) | -z10+S9-S5+S16=0; | z10=S9-S5-S16; | (S9) |
18) | -A4+S11-A3-A2+S16=0; | A4+A3A2=S11-S16; | (S11) |
19) | -z9+З2+S1-S3+S9=0; | z9=S1-З2-S3+S9; | (З2) |
∑и.б. = ∑к.б. = 4
∑исх.зв. = 39
Принимаем первую схему.
Расчет операционных размеров
(по схеме первого варианта)
1) A8 = S13
A8 = 5+0.3
S13 по IT14 в системе отверстия TS13 = 0.3
S4 = 5+0.3
2) A7 = S11
A7 = 6+0.3
S11 по IT14 в системе отверстия TS11 = 0.3
S6 = 6+0.3
3) A1 = S5
A1 = 22+0.21
S5 по IT12 в системе отверстия TS5 = 0.21
S16 = 22+0.21
4)А6 = S3
A6 = 8+0,36
S3 по IT14 в системе отверстия TS3 = 0.36
S3 = 8+0.36
5) А2 = S15
A2 = 44-0.25
S15 по IT6 в системе вала TS15 = 0.016
S15 = 44-0,016
6) z2= S2
z2min =S2min
z2min =1.5
S2min=1.5
S2 по IT12 в системе отверстия TS2 = 1.5+0.1
S2 = 1.5+0.1
z2= S2 = 1.5
z2max =1.6
z2min=1.5
7) z12 = S14 – S15
z12min = 0.05
S15 = 44-0,016
Z12min = S14min – S15max
S14min = 44 – 0.05 = 44.05
S14 no IT8 в системе вала TS14 = 0.039
S14max = S14min – TS14 = 44,05 - 0.039 = 44,089
S14 = 44,089-0,039
Z12min =0.05
Z12= S14 – S15 = 44.089– 44 = 0.089
Z12max = 44,089 – 43,984 = 0,105
8) z13 = S10 – S14
z13min = 0.1
S19 = 44,089-0,039
z13min = S10min – S14max
0.1 = S10min – 44,089
S10min = 44.089+0.1 = 44,189
S10 no IT10 в системе вала TS10 = 0.1
S10max = S10min +TS10 =44,189+0.1=44,289
S10 = 44,289-0.1
z13min = 0,1
z13 = S10 – S14 = 44,289 – 44,089 = 0.2
z13max = S10max – S14min = 44,289 – 44.05= 0.239
9) z14 = S9 – S10
z14min = 0.17
S10 = 44,289-0.1
z14min = S9min – S10max
0.17 = S9min – 44,289
S9min =44,289 +0.17 = 44.459
S9 no IT12 в системе вала TS9= 0.25
S9max = S9min +TS9 =44,459+0.25=44.709
S9 = 44.709-0.25
z14min = 0.17
z14 = S9 – S10 = 44.709 – 44.289 = 0.420
z14max = S9max – S10min = 44.709 – 44.189= 0.52
10) z15 = S8 – S9
z15min = 0.7
S9 = 40,709-0.25
z15min = S8min – S9max
0.7 = S8min – 44.709
S8min = 44.709+0.7 = 45.409
S8 no IT14 в системе вала TS8= 0.62
S8max = S8min +TS8 =45.409+0.62=46.029
S8 = 46.409-0.62
z15min = S8min – S9max=0.7
z15 = S8 – S9 = 46.029 – 44.709 = 1.320
z15max = S8max – S9min = 46.029 – 44.459= 1.57
11) z6 = S5 – S4
z6min = 1.5
S5 =22+0.21
z6min = S5min – S4max
1.5 = 22 – S4max
S4max = 22-1.5 =20.5
S4 no IT14 в системе отвертия TS4= 0.52
S4min = S4max +TS4 =20.5+0.52=19.98
S4 = 19,98+0,52
z6min = 1,5
z6 = S5 – S4 = 22– 19,98 = 2,02
z6max = S5max – S4min = 22,21– 19.98= 2,23
12) A1+А5= S16
A1 = 22+0.21
A5 = 18+0,43
S16 =A1 – A5 = 22+28=40
EcS16 = 0.105 +0.215 = 0.32
TS16 = 0.21 + 0.43 = 0.64
EsS16 = EcS16 + TS16/2 = 0.32+ 0.64/2 = 0,64
EiS16 = EcS16 – TS16/2 = 0.32– 0.64/2 = 0
S16 = 40+0,64 no IT 10 в системе отверстия TS16= 0.1
S16 = 40+0.1
13) z10= S16- S6
Z10min =0,17
S16 = 40+0,1
S6max =S16min – z10min = 40-0,17=39,83
S6 no IT12 в системе отверчтия TS6= 0.25
S6min = S6max +TS6 =39,83-0.25=39,58
S6 = 39,58+0,25
Z10min = 0,17
Z10 = S16 – S6 = 40– 39,58 = 0,42
Z10max = S16max – S6min = 40,1– 39.58=0,52
14) S7 = A3 + А2
A3 = 60+0.74
A2 = 44-0.25
S7 =A3 – A2 = 60-44=104
EcS7 = 0.37 -0.125 = 0,245
TS7 = 0.74 + 0,25 = 0.99
EsS7 = EcS7 + TS7/2 = 0.245+ 0.99/2 = 0.74
EiS7 = EcS7 – TS7/2 = 0.245– 0.99/2 =- 0.25
no IT 14 в системе вала TS7= 0.74
S7 = 104-0.74
15) A3 + А4= S12
A3 = 60+0.74
A4 = 18+0.43
S12 = A4 +A3 = 18+60=78
EcS12 = 0,37+0,215 = 0,585
TS12 = 0.74+0.43 = 1,17
EsS12 = EcS12 + TS12/2 = 0,585+1,17/2 = 1.17
EiS12 = EcS12 – TS12/2 = 0.585-1.17/2 = 0
S12 = 78+1.17 no IT 14 в системе отверстия TS12= 0.87
S12 = 78+0.87
16) z19 = S1 – S2 – S7
S2 = 1.5+0.1
S7 = 104-0.74
z19min = 1.5
z19min = S1min – S2 max – S7max
1.5 = S1min – 1.6 – 104
S1min = 1.5 +1.6+104 = 107.1
S1 no IT14 в системе вала TS1 = 0.87
S1max = S1min –TS1 =107.1+0.87=107.97
S1 = 107.97-0.87
z19min = 1.5
z19 = S1 – S2 – S7= 107.97-1.5-104 =2.47
z19max = S1max – S2 min – S7 min = 107.97-1.5-103.26 = 3.21
17) z1 = З1 – S1
Z1min =1.5
S1 = 107.97-0.87
z1min = З1min – S1max
1.5 = З1min –107.97
З1min = 107.97 + 1.5 = 109.47
З1 по IT16 ТЗ1 = 2.2
З1max = З1min + ТЗ1 = 109.47+ 2.2 = 111.67
З1= (З1min + З1max)/2 ТЗ1/2=(109.47 + 111.67)/2
2.2/2=110.57
1.1
z1min =1.5
z2 = З1 – S1= 110.57-107.97 = 2.6
z1max = З1max – S1min = 111.67-107.1 = 4.57
18) z16 = S1- S2 – S8 – З3
Z16min = 1.5
S1 = 107.97-0.87
S2 = 1.5+0.1
S8 = 46.029-0.62
Z16min = S1 min – S2 max – S 8max + З3 max
1.5 = 107.1 – 1.6 – 46.029 – З3 max
З3max =107.1 – 1.6 – 46.029 -1.5 =57.971
З3 по IT16 ТЗ3 = 1.9
З3min = З3max - ТЗ3 = 57.971- 1.9 = 56.071
З3= (З3min + З3max)/2 ТЗ3/2=(56.071 + 57.971)/2
1.9/2=57.021
0.95
Z16min =1.5
Z16 = S1 - S2 – S8 – З3= 107.97+1.5+46.029-57.021 = 3.42
Z16 max = S1 max - S2 min – S8 min – З3 min =107.97-1.5-45.409-56.071 = 4.99
19) z9 = З2 + S6 + S2 – S1
z9min = 0.7
S1 = 107.97-0.87
S2 = 1.5+0.1
S6 = 39.58+0.25
Z9min = З2 min + S6 min + S2 min – S 1max
0.7 = З2 min + 39.58 + 1.5 – 107.97
З2min = 0.7 – 39.58-1.5+ 107.97=67.59
З2 по IT16 ТЗ2 = 1.9
З2max = З2min + ТЗ2 = 67.59+1.9 = 69.49
З2= (З2min + З2max)/2 ТЗ2/2=(67.59 + 69.49)/2
1.9/2=68.54
0.95
Z9min = 0.7
z7 = З2 + S6 + S2 – S1=68.54+39.58+1.5-107.97 = 1.65
z9 max = З2 max + S6 max + S2 max – S1 min =69.49+39.83+1.6-107.1 = 3.82
Дата добавления: 2018-05-12; просмотров: 336; Мы поможем в написании вашей работы! |
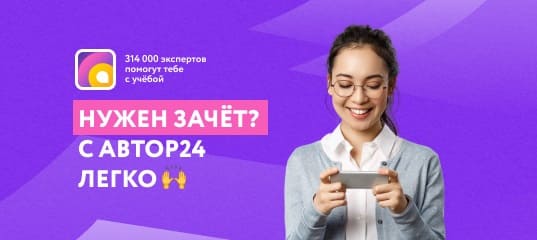
Мы поможем в написании ваших работ!