Типовые технологические процессы обработки зубчатых колес.
Зубчатые передачи широко распространены в промышленности: их применяют для передачи вращательного движения и крутящего момента между параллельными, пересекающимися и скрещивающимися осями валов, а также для преобразования вращательного движения в поступательное.
В зависимости от служебного назначения зубчатые колеса изготовляют из углеродистых, легированных сталей, реже — из чугуна, пластических масс и бронзы. Материал зубчатых колес должен обладать однородной структурой, которая способствует стабильности размеров после термической обработки, особенно размеров отверстия и шага колес. Нестабильность размеров возникает после цементации и закалки, когда в заготовке сохраняется остаточный аустенит. Нестабильность размеров может возникнуть также и в результате наклепа и при механической обработке. Равновесие внутренних напряжений в металле нарушается при большой глубине резания. При изготовлении высокоточных зубчатых колес для снятия в них внутренних напряжений рекомендуется чередовать механическую обработку с операциями - термической обработки.
Большое значение имеет также неоднородная твердость заготовки в различных местах зубчатого венца. При этом возникают различные упругие отжатия системы станок – приспособление – инструмент - деталь; они приводят к дополнительным погрешностям эвольвентного профиля зуба, окружного шага, биению зубчатого венца и другим погрешностям зубьев.
|
|
Точность колеса после термообработки снижается на 0,5— 1 степень, и тем меньше, чем лучше подобран материал по стабилизации размеров при термической обработке. Легированные стали, по сравнению с углеродистыми, как правило, обеспечивают более глубокую прокаливаемость и меньшую деформацию.
Виды заготовок зубчатых колес зависят от материала, конструкции и серийности выпуска.
В крупносерийном и массовом производстве стальные заготовки зубчатых колес получают:
штамповкой на винтовых и гидравлических прессах;
штамповкой на штамповочных молотах, кривошипных прессах и горизонтально-ковочных машинах.
Чугунные и бронзовые заготовки получают литьем в кокиль, под давлением, по выплавляемым моделям.
В мелкосерийном производстве стальные заготовки зубчатых колес обычно получают горячей штамповкой в одно-, двух-, и многоручьевых штампах на молотах и прессах.
Заготовки, получаемые ковкой на молотах, имеют большие уклоны-напуски.
Штамповка заготовок в закрытых штампах имеет ряд преимуществ: снижается расход металла из-за отсутствия облоя, форма заготовок ближе к готовой детали, экономия металла составляет от 10 до 30%. Однако получается повышенный износ и расход штампов.
|
|
Штамповка на прессах имеет большое преимущество перед штамповкой на молотах, получается точная штампованная заготовка, припуски и напуски меньше на 30%, по конфигурации заготовка ближе к готовой детали.
Штамповкой на горизонтально-ковочных машинах получают заготовки зубчатых колес с хвостовиком или с отверстием. Для изготовления заготовок ступенчатых валов-шестерен в крупносерийном производстве применяется поперечно-винтовая прокатка.
Вращение заготовки во время прокатки дает возможность получать более высокую геометрическую точность размеров и снизить припуски на механическую обработку резанием шеек вала-шестерни. Производительность прокатных станов 360-900 шт./ч.
Качество работы цилиндрических зубчатых колес, кроме норм кинематической точности, характеризуется нормами плавности работы и нормами контакта зубьев для различных степеней точности. Для зубчатых колес в нормы плавности входят: допуск на погрешность профиля зуба, допуск на местную кинематическую погрешность колеса; предельное отклонение шага в зацеплении; и др.
|
|
При изготовлении зубчатых колес высокой степени точности важно обеспечить требуемое отклонение от перпендикулярности торца к оси центрального отверстия на операциях до формообразования зубьев.
Точность размеров. Самым точным элементом зубчатого колеса является отверстие, которое выполняют обычно по 7-му квалитету, если нет особых требований, а для прецизионных колес 5—6-й степени точности — по 5—6-му квалитетам.
Точность формы. В большинстве случаев особых требований к точности формы поверхностей не предъявляется.
Точность взаимного расположения. Несоосность начальной окружности зубчатого колеса относительно посадочных поверхностей допускается не более 0,05-0,1 мм. Неперпендикулярность торца к оси отверстия или вала (биение торцов) обычно принимается не более0,01-0,015 мм на 100 мм диаметра. В зависимости от условий работы колеса эта величина может быть повышена или несколько уменьшена.
Твердость рабочих поверхностей. Зубья колес работают в условиях переменных ударных нагрузок и подвергаются износу, поэтому часто бывает необходимость повысить твердость поверхности зубьев при сохранении мягкой сердцевины. Для повышения твердости поверхностного слоя наиболее часто применяются:
- цементация - насыщение углеродом поверхностного слоя зубьев колес из низкоуглеродистой стали (с содержанием не более 0,25% С), толщина слоя h=0,1...3 мм, твердость после термообработки НRСэ45...64;
- цианирование - насыщение поверхности зубьев одновременно углеродом и азотом в расплавленных цианистых солях. Толщина слоя h =0,5...0,8 мм, твердость после термообработки НRСэ 45...53.
Дата добавления: 2018-05-12; просмотров: 751; Мы поможем в написании вашей работы! |
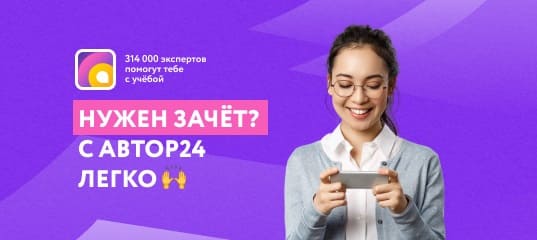
Мы поможем в написании ваших работ!