Упрочняющие методы обработки наружных поверхностей.
Упрочняющие методы обработки внутренних поверхностей.
Электроразрядные методы обработки (электроискровая, электроимпульсивная)
Отдельные способы электрофизической обработки основаны на использовании явления электрической эрозии – направленного локального разрушения электропроводящих материалов в результате теплового действия импульсных электрических разрядов между электродами, в роли которых выступают инструмент и заготовка. Эти способы называют так же электроэрозионной обработкой.
При разности потенциалов на электродах происходит ионизация межэлектродного пространства заполученного диэлектрической жидкостью. При достижении определенного значения напряжения происходит искровой или дуговой разряд. Мгновенная плотность тока в канале проводимости достигает 8000…10000 А/мм2, температура на поверхности электрода и заготовки – 10000…12000о С. это приводит к мгновенному испарению металла с поверхности, а на поверхности образуется лунка. В диэлектрической жидкости испарившийся металл застывает в виде гранул размером 0,01…0,005мм. При непрерывном подведении к электродам импульсного тока процесс эрозии продолжается до тех пор, пока возможен электрический пробой при заданном напряжении. Для продолжения процесса необходимо сближать электроды до расстояния 0,01…0,05 мм, что обеспечивается следящей системой станка. В результате совокупности эрозионных и других процессов, возникающих в межэлектродном пространстве, происходит формообразование поверхности обрабатываемой за
|
|
готовки. В качестве диэлектрической жидкости при эрозионных процессах используются преимущественно керосин, минеральное масло или их смеси 1:1; 1:2.
В зависимости от продолжительности импульса, величины накопленной энергии разряда и др. различают электроискровую и электроимпульсную обработку.
Схема электроискровой обработки (разработана в 1943 году супругами Б. Р. и Н. М. Лазоренко) предусматривает использование генератора импульсов RC (рис. 7.1). Необходимая энергия разряда накапливается в конденсаторе С, питаемым через резистор R источником постоянного тока напряжением 100…200 В. Продолжительность импульса составляет 20…200 мкс. В зависимости от количества энергии, расходуемой в импульсе, различают жесткий или мягкий режимы обработки. Мягкий применяют для чистовой обработки: обеспечивается точность размеров до 0,002 мм при шероховатости 0,63…016 мкм. Производительность обработки составляет 25…1900 мм3 / мин.
Электроискровым методом обрабатываются практически все токопроводящие материалы. Зависимость интенсивности эрозии от свойств металлов называют электроэрозионной обрабатываемостью. В относительных единицах ее значения представляют как: сталь – 1; твердые сплавы – 0,5; титан – 0,6; никель – 0,8; медь – 1,1;латунь – 1,6; алюминий – 4; магний – 6.
|
|
Электроискровым методом целесообразно обрабатывать твердые сплавы, труднообрабатываемые материалы и сплавы и т. п. Некоторые схемы обработки поверхностей показаны на рисунке 7.1. Электроискровую обработку применяют для изготовления пресс-форм, фильер, матриц, режущего инструмента, деталей топливной системы двигателей внутреннего сгорания, сеток и т. п.
Электроискровую обработку применяют так же для упрочнения рабочих поверхностей пресс-форм, матриц, режущего инструмента. Упрочнение заключается в нанесении на рабочие поверхности тонкого слоя высокопрочного материала, например твердого сплава, композиционного материала. Покрытие повышает твердость, износостойкость, жаропрочность и др. свойства поверхностей изделий.
При электроимпульсной обработке (рис 7.1б) продолжительность импульсов составляет 500…10000 мкс, в результате происходит дуговой разряд. Необходимая мощность обеспечивается питанием от генераторов постоянного тока. В сочетании с применением графитовых электродов и обработкой поверхности в процессе электроимпульсивной обработки в 8 – 10 раз (по сравнению с электроискровой) повышается производительность и снижается разрушение электродов. Низкочастотная электроимпульсная обработка с питанием от машинных генераторов позволяет получать поверхность с шероховатостью Rz 40, а высокочастотная (с частотой 7…25 кГц) – шероховатостью до 1,25 мкм. Применяется электроимпульсная обработка преимущественно для штампов, пресс-форм, турбинных лопаток и др. (В США и Японии более половины всех штампов изготавливается электроэрозионной обработкой).
|
|
Электроконтактная обработка основана на электромеханическом разрушении металла под воздействием электродуговых разрядов быстро перемещающимся инструментом. Съем металла с заготовки осуществляется в воздушной среде вращающимся диском – электродом, который служит инструментом (рис. 7.2). На диск и заготовку подается электроэнергия от понижающего трансформатора 3. При вращении диска, к которому заготовка прижимается под давлением (2…5)·104 Па, происходит периодический разрыв контактов, возникают электродуговые разряды, под воздействием которых и разрушается металл заготовки. Соприкосновение под небольшим давлением двух металлических электродов (инструмента и заготовки) приводит к выделению джоулевого тепла, которое размягчает и даже плавит металл заготовки, облегчает его удаление. Во избежание разогрева инструмента – электрода его вращают со скоростью порядка 30 м/с, которая обеспечивает очень малое время соприкосновения контактирующего участка диска с заготовкой. Вращающийся диск выбрасывает частицы разогретого или расплавленного металла заготовки в виде снопа искр. При большой мощности подводимого тока интенсивность процесса достаточно велика и в ряде случаев превосходит процессы резания.
|
|
Анодно-механическая обработка (разработана в 1943 году В. Н. Гусевым) основана на сочетании электротермических и электромеханических процессов, протекающих в среде электролита, и занимает промежуточное место между электроэрозионным и электрохимическими методами. Обрабатываемую заготовку подключают к аноду, а инструмент – катоду (рис. 73). В зависимости от характера обработки и вида обрабатываемой поверхности в качестве инструмента используют металлические диски, ленты, проволоку, цилиндры. В зону обработки 3 подается электролит – водный раствор жидкого натриевого стекла. Инструменту и заготовке сообщаются движения, как при обычных процессах резания. При пропускании через раствор электролита постоянного тока на аноде (заготовке) образуются пленки продуктов анодного растворения металла, которые удаляются из зоны обработки инструментом. При образовании определенных зазоров между микронеровностями обрабатываемой заготовки и электродом – инструментом происходит электроразряд, присущий электроэрозионной обработке. Кроме того, в случаях образования контакта между заготовкой и вращающимся электродом происходит разогрев металла заготовки и размягчение, как при электроконтактной обработке. Продукты электроэрозии, анодного растворения и механического воздействия удаляются из зоны обработки при относительных движениях инструмента и заготовки. При мягком режиме (плотность тока <15А/см2) обработка осуществляется в основном за счет электрохимического растворения и механического удаления пленки, обеспечивается шероховатость поверхности 0,32…0,04 мкм. При более жестких режимах процесс осуществляется в основном за счет электроэрозии и электроконтактной обработки, шероховатость поверхности соответствует Rz 160…20мкм.
Анодно–механическая обработка используется для заготовок из всех токопроводящих металлов, высокопрочных и труднообрабатываемых сплавов и т.п.
Анодно–механическим методом (рис. 7.4) разрезают заготовки на части, прорезают пазы и щели, обтачивают поверхности тел вращения, шлифуют плоские поверхности и поверхности тел вращения, производят заточку инструмента и т.д.
Для анодно–механической обработки используют и станки с ЧПУ. Программа обработки управляет режимами движения заготовки и инструмента, поддерживает постоянство зазора в рабочем пространстве между ними, задает параметры электрических режимов при переходе с черновой обработки на чистовую. Инструменты изготовляют из мягкой стали, меди, чугуна и других материалов.
Дата добавления: 2018-05-12; просмотров: 463; Мы поможем в написании вашей работы! |
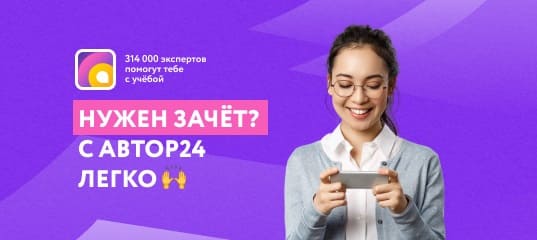
Мы поможем в написании ваших работ!