Требования к роботОТизированому оборудОВАНИю:
1. Соответствие конструктивно-технологических параметров робота (грузоподъемность, скорость перемещения рабочих органов, погрешность позиционирования, размер рабочей зоны, тип системы управления и многое другое) их функциональному назначению.
Объем операций, выполняемых ПР, и темп их выполнения в сочитании с затратами на приобретение и внедрения ПР должны обеспечивать экономическую эффективность его применения.
2. Соответствие число степеней подвижности ПР необходимому числу требуемого для выполнения операции.
3. Соответствие манипуляционных возможностей ПР схеме загрузки и зоны обслуживания станка, требование взаимодействия со вспомогательными устройствами при планировке, а так же минимальная площадь
4. Простота и кратность цикла переналадки, надежность и невысокая стоимость эксплуатации, высокий коэффициент использования ПР.
5. Обеспечение требования техники безопасности.
Требования к станкам:
1. Обеспечивать автоматический цикл обработки деталей
2. Обеспечивать автоматическую фиксацию и зажим деталей в рабочей зоне станка
3. Удаление стружки из зоны обработки
4. Возможность очистки базирующих и крепежных поверхностей от стружки и грязи
5. Станок должен обеспечивать форму и расположение рабочей зоны, позволяющих их обслуживать с помощью ПР
6. Автоматическое ограждение рабочей зоны
ТребованиЯ к вспомогательному оборудованию (ВО):
|
|
1. Габаритные размеры вспомогательных устройств должны позволять их стыковку с основным оборудованием и ПР.
2. Устройства должны иметь датчики, позволяющие производить контроль наличия детали их положение, деталь должна быть зажата во ВО; привязка детали к рабочей зоне ПР; привязка самого ВО к общей схеме РТК, с целью повышения надежности работы РТК в целом.
3. ВО д. надежно захватывать деталь, рационально ее перемещать, ориентировать и поштучно выдавать, а также поштучно ее размещать в таре и транспортировать.
4. ВУ должны учитывать возможность сопряжения с транспортирующими цеховыми устройствами, либо общезаводскими транспортирующими устройствами.
Требования к обрабатываемым деталям:
1.Деталь должна иметь возможность группирования по конструктивно-технологическому назначению, с целью обеспечения групповой формы организации производственного процесса, типизации ТП и использование одинаковых основного и ВО.
2.Деталь должны иметь ясно выраженные базы и признаки ориентации, позволяющие организовать их транспортировку и складирование в ориентированном виде с использованием стандартной оснастки.
3.Детали должны быть однородные по форме и расположению поверхности, это необходимо для базирования и захвата детали, что позволяет без дополнительной выверки устанавливать деталь в рабочую зону оборудования, при этом можно использовать широкоуниверсальную технологическую оснастку.
|
|
Построение компОновки РТК:
После определения операций, подлежащих роботизации и определения деталей, которые будут обрабатываться на РТК, составляется карта по применению ПР.
В этой карте приводятся все основные сведения о разрабатываемом РТК: схемы планировки, перечень оборудования, эскиз заготовки, эскиз обрабатываемой детали, кинематическая схема захвата ПР, характеристика движения робота, перечень переходов, выполняемых ПР, условия окружающей среды, трудоемкость на 1 деталь).
ГПМ для обработки ротАционной детали средней сложности и точности:
В данном примере ГПМ состоит из нескольких РТК или ГОЯ; РТК выполняет токарные операции деталей типа тел вращения с Æ20…120 мм, длиной 20…140 мм, массой до 7,5 кг.
В состав РТК входят встраиваемый ПР «Электроника НЦТМ-01», токарный станок, приемный стол для установки кассет с заготовками, плата сопряжения устройств управления ПР с ЧПУ станка, плата сопряжения ЧПУ станка с верхним уровнем управления (управление ГПМ) «Электроника НЦ80-10Д».
|
|
Для данной ГПМ характерен тип компоновки, при которой ГПМ образуется из трех РТК или ГОЯ, они группируются вокруг обслуживающего робота.
|
Доставка заготовок со склада и деталей на склад осуществляется в транспортной таре на поддонах, посредством транспортного робота (робокар).
Основные фазы функционирования ГПМ:
1.Робокар подъезжает к причальному устройству (ПУ) (фаза характеризуется загрузкой модуля пакетами кассет с заготовками).
2.Центральный ПР перегружает паллеты с кассетами заготовок на центральный стол РТК (загрузка РТК первыми кассетами с заготовками центрального ПР последовательно перегружающего верхние кассеты с ПУ на центральные столы РТК и дает команду на начало обработки заготовок).
3.Центральный робот перегружает оставшиеся кассеты на буферные загрузочного устройства, в результате ПУ освобождается для приема кассет с обработанными деталями).
4.Прием на ПУ кассет с обработанными деталями и загрузка РТК кассетами с новыми заготовками до последней, до тех пор циклично, и завершается перед началом обработки последней кассеты каждой РТК.
|
|
5. Робокар вызывается, отправление кассет с обработанными деталями на склад и разгрузка кассет с заготовками (пока обрабатываются последние кассеты).
6.Разгрузка кассет на буферные, загрузочные устройства. Далее цикл продолжается, начиная с 4 фазы.
Затем создается алгоритм работы ПР или РТК, на основании алгоритма создается циклограмма работы РТК или ГПМ.
Алгоритм отображает последовательность выполнения движений ПР, последовательность работы основного и ВО, выполнение команд на включение и отключение тех или иных устройств и механизмов комплекса.
Алгоритм представляется в виде блок схемы.
|
Далее составляется циклограмма. Циклограмма предназначена для учета временных характеристик работы РТК. На циклограмме указывают все возможные движения ПР, основного и вспомогательного оборудования.
ПР | Перемещение руки | Вверх | Ц | |
Вниз | И | |||
Поворот манипулятора | По час. стрелке | К | ||
Против ч.с. | Л | |||
Изгиб кисти | О | |||
Схват | Деталь | Гориз. | Г | |
Вертик. | Р | |||
Заготовка | Зажим | А | ||
Разжим | М | |||
Станок | Зажим заготовки в патроне | М | ||
Разжим детали в патроне | А | |||
Работа станка | ||||
Вспомогат. оборудование |
|
Время
Средства автоматизации, используемые в ГПС (гибкие произв. системы):
ГПС (система) представляет собой сложную техническую систему, предназначенную для комплексного выполнения технологических процессов обработки деталей или ТП сборки изделий.
ГПС определяется как различное сочетание станков и отдельных единиц технологического оборудования с ЧПУ, РТК, ГПМ и систем обеспечения их функционирования в автономном режиме в течении определенного времени.
ГПС имеет возможность автоматической переналадки в процессе обработки детали произвольной номенклатуры в определенных пределах.
Нормальная работа и правильное взаимодействие всех составных частей ГПС обеспечивается комплексом автоматизированного управления; автоматизированной транспортно-складской системой, системой инструментального обеспечения, автоматизации обеспечения контроля заготовок, автоматизация управления отходов, диагностика оборудования и режущего инструмента – автоматизация системы.
Наиболее высокая эффективность ГПС достигается при применении станочного оборудования, способного значительную часть суток работать в авторежиме, без вмешательства и постоянного контроля со стороны оператора. Лучше всего этому удовлетворяют многооперационные станки (обрабатывающие центра). Они позволяют производить обработку детали с нескольких сторон за одну установку. Производительность этих станков возрастает в несколько раз за счет применения многоиснтрументальных сменных наладок.
ГПС в значительной степени зависит от гибкости технологического оснащения (от станочных приспособлений, инструментального обеспечения).
Применение ГПС: автомобильная, инструментальная, станкостроительная, аэрокосмическая промышленность (из-за высокой серийности).
ГПС для механической обработки может включать в себя отдельные станки с ЧПУ, РТК и ГПМ.
Обычные станки с ЧПУ (компоновка на универсальных станках) трудно включать в состав ГПС Þ необходимо создавать станки с ЧПУ, которые удовлетворяли требованиям работы ГПС.
Среди токарных станков для состава ГПС – это станки повышенной точности (16К20Ф3 или Т1 – Москва, 16Б16Ф3 или Т11 – Самара).
Для токарных станков рекомендуется для встройки в ГПС в приводе главного движения использовать асинхронные электродвигатели с частотным регулированием, либо электродвигатели с постоянным током, приводы продольных и поперечных подач с высокомоментными электродвигателями пост. тока; режущий инструмент должен размещаться как минимум в автоматических револьверных головках в 6-10 позициях, в инструментальных магазинах. Они должны быть снабжены системами ЧПУ (2Р22 ввод с программы с клавиатуры, магнитные ленты).
Среди токарных станков с ЧПУ распространены болгарские станки ST161, ST201, ST251 с широкими технологическими возможностями (главное отличие – гл. привод имеет двигатель пост. тока и 2-х скоростную переборную головку, привода подач являются следящими и имеют высокомоментный двигатель пост. тока, на поперечном суппорте смонтирована 12-позиционная инструментальная головка с электромеханическим приводом поворота). Для станков данной серии разработана спец. Инструментальная система, охватывающая широкую номенклатуру режущего инструмента, необходимого для выполнения всего многообразия технологических операций.
В состав инструментальной системы входят блоки с различным положением измерительных головок для контроля за размерами обрабатываемой дет али.
Станки серии ST имеют ряд особенностей в конструкции, которые обеспечивают удобное присоединение к ним ПР, накопителей, питателей заготовок и другие для ГПС работы.
С этой целью направляющие продольного суппорта в вертикальной плоскости вынесены за ось шпинделя (для отвода стружки из зоны резания).
Токарные станки ST дают возможность обработки детали сразу с двух концов, для этого станок имеет контователь, спроектированный на базе задней бабки. Основным элементом контователя является устройство для захвата детали, которое унифицировано со схватом, установленным на станке ПР.
МНОГООПЕРАЦИОННЫЕ СТАНКИ:
В них реализуется принцип последовательной концентрации разнородных технологических операций.
Особенностью конструкции обрабатывающий центров (ОЦ) является наличие инструментального магазина, в котором может размещаться большое количество инструментов, благодаря этому ОЦ обеспечивают возможность обработки деталей различной сложности формы за одну установку.
В силу возможности своей кинематики, конструкции и системы управления ОЦ обладают следующими преимуществами:
1. высокая производительность;
2. высокая степень автоматизации;
3. сокращение вспомогательного времени;
4. повышение точности обработки;
5. повышение гибкости оборудования (из-за быстрой переналадки станка на обработку другой детали).
В зависимости от расположения осей шпинделя, числа и характера движения подвижных узлов, числа управляемых координат, имеется мноогообразие компоновочных решений ОЦ.
Как правило, эти станки имеют развязанную кинематику, т.е. функциональный орган станка имеет свой собственный электродвигатель, все привода имеют бесступенчатое изменение частоты вращения шпинделей и скоростей подач.
Основной отличительный признак ОЦ – наличие инструментального магазина, а также устройство для смены инструменты.
Виды инструментальных магазинов:
1.
|
2.
|
Определение необходимого числа инструментов в магазине производится в зависимости от технологического назначения станка. Практика использования ОЦ показывает, что при обработке деталей средней сложности с преобладанием операций по обработке отверстий достаточно 10-15 инструментов, а для более сложной детали в две смены – 30-40 инструментов или до 100.
В настоящее время основную группу многооперационных станков составляют станки сверлильно-фрезерно-расточные (2С132ПМФ2, 15VB).
Очень распространенные ОЦ: станки Ивановские – ИР500, ИР1000 – имеют в поперечном суппорте револьверные головки до 12 инструментов каждая по торцу и 12 по периферии. Некоторые инструменты имеют свой привод, револьверные головки сменные – 2 шт. (одна – на суппорте, вторая – в инструментальном магазине).
ВСПОМОГАТЕЛЬНЫЕ УСТРОЙСТВА:
Обрабатываемая деталь и заготовка хранятся в магазинах-накопителях – ЗУ (захватывающие устройства).
ЗУ накопителя обеспечивают накопление деталей для непрерывной работы в течении нескольких часов.
Конструктивно ЗУ выполняются с учетом формы и размеров деталей, емкости расположения относительно станка, простоты перенастройки; длительность цикла выдачи деталей в зону захвата роботом не должна превышать длительности работы ПР и станка.
В накопительных устройствах детали в зоне захвата должны быть ориентированны относительно приспособления, для их фиксации и установки на станке.
При выборе емкости накопительного устройства необходимо учитывать непрерывность работы РТК в течении половины рабочего дня или более.
|
а) наклонно
|
б) вертикально
|
в) горизонтально
Накопительные устройства отличаются друг от друга расположением деталей от общей горизонтали.
Все детали в накопительных устройствах должны быть размещены в едином порядке.
1. Спиральные накопительные устройства:
Лотки расположены по винтовой линии.
|
Преимущества: занимает минимальную производственную площадь.
Магазины для накопления деталей используют паллеты след. видов (паллет – часть магазина):
|
|
КОДИРОВАНИЕ ИНСТРУМЕНТОВ В ИНСТРУМЕНТАЛЬНЫХ МАГАЗИНАХ (ИМ):
Для автоматизированного поиска необходимого инструмента в ИМ используют различные методы кодирования, инструментальной оправки или гнезда магазинов.
Существуют следующие основные методы кодирования инструмента:
1.Располагают инструмент в магазине в определенной последовательности, в соответствии с ТП, при этом программируется только шаг поворота ИМ.
Недостаток: невозможность повторного использования одного и того же инструмента в течении одного цикла.
2.
|
Считывающие устройства:
а) контактные;
б) бесконтактные.
Они формируют двоичный код, который сравнивается с кодом управляющей программы. В момент совпадения кода инструмента с кодом заданным управляющей программы, подается сигнал на установ магазина и его фиксацию.
Данный способ позволяет расположить инструмент произвольным образом в ИМ Þ упрощается обслуживание станка.
Недостаток: усложняется конструкция инструментальной оправки, снижается жесткость, увеличивается масса ИМ.
3.Кодирование гнезд ИМ.
Виды кодирования:
1) поиск нужного гнезда осуществляется датчиками различного типа (оптические, сельсины, кодовые диски в сочетании с микровыключателями), датчики кинематически связаны с валом магазина (на вал магазина надевают кулачки).
|
2) с помощью ключей
Ключи выполнены в виде пластин с различной комбинацией проточек, которые формируют двоичный код. Выступы ключей воздействуют на различные контактные/бесконтактные микровыключатели считывающего устройства.
Преимущества: экономия времени смены инструмента.
Недостаток: цикл работы механизма автоматической смены инструмента усложняется.
Перспективным кодированием инструмента в ИМ является использование фотоэлектрического, электромагнитного и др. типов физической эффектов (для кодирования инструмента в определенном месте инструментальной оправки приклеивают этикетку со штрих – кодировкой или покрытую ферромагнитным слоем, на них можно запрограммировать размеры инструмента, двоичный код, с помощью сканера считывать).
СРЕДСТВА АВТОМАТИЗАЦИИ ПОГРУЗОЧНО-РАЗГРУЗОЧНЫХ И ТРАНСПОРТНО-СКЛАДСКИХ РАБОТ:
Эти средства автоматизации предназначены для накопления, транспортирования и доставки на рабочие места тары с заготовками, детали, оснастку, а также для вывоза с рабочего места стружки.
СКЛАДЫ:
· На фазе производства осуществляется хранение, группирование и комплектация различных видов заготовок и продукции до передачи их на магистральный транспорт.
Срок хранения на складах – 5-10 суток.
· На фазе потребления: хранение сырья, топлива, комплектующих изделий, материала до передачи их в производства.
Срок хранения – до нескольких месяцев.
Склад – стеллажи:
Стеллажный способ хранения относится к прогрессивной форме хранения пакетизированных тарно-штучных грузов (контейнеры).
Применений стеллажей создает благоприятные условия для применения и автоматизации складских процессов:
- учет;
- адрессование;
- планирование работ погрузочно-разгрузочных механизмов;
- комплектация партии грузов;
- погрузочно-разгрузочные работы.
Преимущества стеллажей:
1. улучшено использование объема и площади склада;
2. увеличение производительности труда примерно в 1,5 раза;
3. понижение себестоимости на35-40%.
Классификация стеллажей:
1.Класс статического хранения грузов:
а) полочные;
б) двух, четырехрядные стеллажи.
2. Класс динамического хранения грузов:
а) гравитационные/роликовые/приводные;
б) карусельные;
в) роликово-приводной стеллаж
Дата добавления: 2018-05-12; просмотров: 272; Мы поможем в написании вашей работы! |
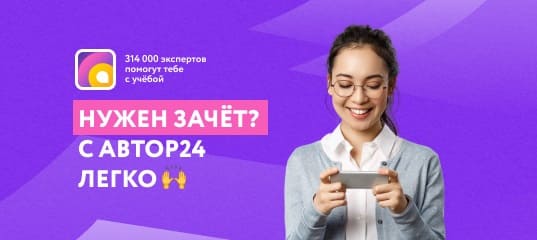
Мы поможем в написании ваших работ!