Тепловые деформации и деформации от внутренних напряжений заготовок:
АПП – это комплекс мероприятий по разработке новых прогрессивных ТП и проектирование на их основе высоко технического оборудования, осуществления рабочего процесса без участия человека. АВТОМАТИЗАЦИЯ – это комплексная технологическая задача. Она является основой тенденции и развития материально-технической базы производства. Автоматизация влияет (социально): «-» сокращение числа рабочих мест (безработица) «+» труд человека легче, но более квалифицирован «+» труд человека становится интеллектуальным Автоматизация влияет (производительность труда): «+» возрастает производительность труда и снижение себестоимости «-» повышает капитальные затраты на оборудование «-» за 2,5 года автоматизированное оборудование устаревает «-» система ЧПУ устаревает за 1 год Т.О. Автоматизация – это высшая ступень развития человеческого общества.
ОСНОВНЫЕ ОПРЕДЕЛЕНИЯ И ПОНЯТИЯ АПП:
Структура производственного процесса (п/п).
Под п/п понимается комплекс мероприятий, при помощи которых осуществляется производство тех или иных машин, узлов и любых изделий; ТП является составной частью п/п.
В ТП активными элементами являются человек и средства труда, предмет труда оказывает им сопротивление.
СРЕДСТВО ТРУДА – это вещь или комплекс вещей, которые человек помещает между собой и предметом труда, и которая служит для человека проводником его воздействия на предмет труда.
|
|
Модель: Человек®Средства труда®Предмет труда
Анализ этой модели показывает, что любую технологическую операцию можно рассматривать, как размещения объективного противоречия между активными элементами человеком и средством труда с одной стороны, с предметом труда с другой.
Любое обрабатываемое изделие, обладает тремя видами сопротивления:
1. субстатное сопротивление (зависит от материала детали)
2.функциональное (зависит от служебного назначения изделия, от его программы выпуска)
3. структурное сопротивление (связанно со способом обработки изделия)
Как показывает анализ, любое целенаправленное действие представляет собой взаимосвязанное единство трех основных систем:
1. Энергетическая
2. Технологическая
3. Управленческая
Каждая из них имеет свое назначение:
1. Состоит в обеспечении выполнения ТП необходимым видом и количеством энергии;
2. Совокупность действий над предметами труда для намеченного изменения его формы, размеров и т.д.
3. Совокупность действий по сбору информации о ходе выполнения целенаправленного действия, переработки этих сведений и выдачи командных сигналов для обеспечения намеченного режима процесса обработки и достижения заданных результатов.
|
|
Зная состав функций, можно установить какими методами они выполнены:
- если они все выполняются человеком, то труд ручной
- если 1 и 2 выполняются не человеком, а 3 за человеком, то этот метод – механизированным
- если все 3 функции выполняются за счет неживой природы, в этом случае человек исключается из процесса труда – автоматический.
Основным условиям механизации (М) автоматизации (А) является энергия неживой природы.
М или А процесса – это применение для воздействия на предмет труда энергии неживой природы, одновременно с энергией людей или без нее, при сохранении периодичного участия людей в управлении. При А – исключают участие людей из управления.
М и А живого труда людей – это исключение из выполнения целенаправленного действия живого труда людей, при сохранении частичном или полном исключении активного участия людей в управлении.
Полная М и А – это М или А, где все затраты энергии людей заменены энергией неживой природы, исключая или включая управление.
Частичная М и А – это тогда, когда часть затрат энергии людей заменена энергией неживой природы.
СИСТЕМА ОЦЕНКИ СОСТОЯНИЯ М И А ТП:
|
|
Под состоянием М и А понимается определенная в некоторый момент времени совокупность качественных и количественных характеристик М и А, обеспечивающих достижение ими установленных технико-экономических показателей применяемых ТП. Оценка состояния является начальным моментом любых работ по М и А, и во многом определяет их полезность.
Методика оценки состояния по профессору Полыньянову, использует принципы системы структурного подхода; она позволяет дать объективно-достоверную оценку состоянию М или а.
Предложенная оценка состоит из двух подсистем:
1. Качественные характеристики
2. Количественные характеристики
Подсистема качественных характеристик имеет три категории:
1.1Ступень М и А.
Ступень – это место проведения М и А или объекты М и А .
Существуют 10 ступеней:
1 Технологические операции и соответствующее им оборудование
2 ТП
3 ТП участка
4 ТП в разрезе цеха
5 ТП в разрезе однородных цехов
6 ТП в разрезе предприятия
7 ТП в разрезе корпорации
8 ТП в разрезе отдельного региона
9 ТП в разрезе отрасли
10 ТП в разрезе в рамках одной страны
1.2 Виды М и А
Вид показывает степень обхвата М и А структурных элементов системы управления ТП.
Различают 3 вида:
|
|
1 единичные (один структурный элемент охвачен М и А)
2 неполно комплексного (два и более структурных элементов охвачены М и А)
3 полное комплексное (все структурные элементы охвачены М и А)
1.3 Категории М и А
Они характеризуют величину основных количественных показателей, их 8:
0) нулевая - уровень 0
1) низшая категория – 0-0,25 уровень
2) вторая – 0,25-0,45
3) средняя – 0,45-0,6
4) большая – 0,6-0,75
5) повышенная – 0,75-0,9
6) высокая – 0,9-0,99
7) полная – 1
Для общей оценки состояния М и А ТП рекомендуется применять информационные модели, в которых приняты обозначения качественных показателей:
М- единичная М
А - единичная А
КМ - комплексная М
КА -комплексная А
Количественные показатели:
1 обязательные (основные):
- хронометрические (временные)
- эргодические (энергетические)
2 вспомогательные:
Для количественной оценки используется понятие уровня М и А
УРОВЕНЬ – это степень замены энергии людей энергией неживой природы.
Есть два вида показателей оценки состояния М и А:
1 уровень М и А живого труда;
2 уровень М и А процесса труда.
Основные расчетные показатели можно свести в таблицу:
Хронометрические:
Живой труд – dт =
Где SТм - сумма машинного времени, не перекрытой временем ручного труда
SТш - сумма штучного времени
Процесс – dп =
SТ- сумма машинного времени, включая и время перекрытия ручного труда
Эргодические:
Процесс – W =
SЭ - сумма количества полезной работы машины или механизма в кВт/ч
SЭр - сумма полной рабочей физического труда людей
При ручном труде хронометрический показатель живого труда dт =0, при автоматизированном труде
dт =1
ПОКАЗАТЕЛИ ПРОИЗВОДИТЕЛЬНОСТИ И ЭКОНОМИЧЕСКОЙ ЭФФЕКТИВНОСТИ АВТОМАТИЗИРОВАННОГО ОБОРУДОВАНИЯ (АО):
Для сравнения АО применяют набор показателей, которые характеризуют качество самого оборудования.
ЭФФЕКТИВНОСТЬ - это комплексный показатель который наиболее полно отражает главное назначение АО - это повышать производительность труда, и соответственно снижать затраты труда при обработке изделий.
Эффективность АО рассчитывают в показателях количества:
Э=
N - годовой выпуск деталей [шт],
З - затраты на их изготовления [руб]
При проектировании АО следует иметь в виду, что Э должна быть максимальной.
Сравнение Э 2-х вариантов АО при заданной программе выпуска производят по разности приведенных затрат, т.е.
Р=З1 -З2
Индекс 2 относится к более совершенному варианту оборудования, базовый вариант имеет индекс 1.
Число показателей экономической эффективности внедрение АО относят: коэффициент окупаемости, годовой экономический эффект, коэффициент увеличения производительности труда, коэффициент приращения стоимости обработки изделия на одного работающего по сменам, а также фонда отдача.
· Коэффициент окупаемости:
где Ток – время окупаемости (срок) [год]
Ток = (К2-К1)/(С1-С2)
Где К – капитальные затраты (по новой и старой технике)
С – себестоимость
Ток.номинал. – номинальное время окупаемости (нормативный срок) [год]
Ток.номинал.=1/Е=6,7 лет
Обязательное условие окупаемости:
Ток < Ток.номинал.
Капиталовложения складываются из затрат: на оборудование, на технические средства управления, на транспорт – складское оборудование, на технологическую оснастку, на инструментальное обеспечение, на содержание производственных, вспомогательных и бытовых площадей и прочее единовременные затраты.
Себестоимость изготовления изделия складывается из затрат на: з/п основных рабочих, вспомогательных рабочих и ИТР, на наладку оборудования, на амортизацию текущего оборудования, содержание вычислительной техники, содержание основного транспортно-складского оборудования, износ инструмента.
Амортизация - списание доли стоимости
· Годовой экономический эффект от внедрения АО рассчитывается:
Э=(С1-С2)*N – (К2-К1)+ Сэ *Drр
Сэ - социальный эффект на одного высвобождаемого рабочего
Drр - число высвобождаемых рабочих
N – годовой объем выпуска продукции
К – капиталовложения
С - себестоимость
· Повышение производительности труда, измеряется в %:
П=
где - снижение трудоемкости изготовления одной единицы изделия
где Т1, Т2 – трудоемкость изготовления на старом и новом оборудовании.
· Рост стоимости обработки, приходящегося на одного работника:
где - численность работников по старому и новому варианту
· Рост фондоотдачи:
а) абсолютная фондоотдача
, Ф1 и Ф2 – фондоотдачи до Авт. и после соотв.
б) относительная фондоотдача
Производительность оборудования определяет его способность обеспечивать обработку определенного числа деталей в единицу времени.
Различают штучную производительность – число деталей, изготовленных в единицу времени, при непрерывной безотказной работе:
Q=
Q – штучная производительность процесса
То - годовой фонд времени
Т – полное время всего цикла обработки изделия.
При изготовлении на станке разных деталей его штучную производительность определяют по условной детали - представителе. Формы и размеры этой детали – представителя (ДП) будут усредненными по всему рассматриваемому множеству деталей
Для станков с широкой универсальностью рассматривают набор ДП, каждая из которых соответствует семейству однотипных деталей, сходных по форме и технологии обработки. Производительность определяют по среднему значению времени цикла обработки;
если процесс обработки осуществляется непрерывно, то в этом случае вспомогательное время равно нулю, поэтому шт. производительность совпадает с понятием технологическая производительность – QТ.
Qт= ;
tр - время обработки резанием детали
Штучная производительность связана с годовым выпуском деталей с помощью коэффициента использования оборудования, который учитывает потери годового фонда времени по организационным и техническим причинам:
N=Qxh;
h-коэффициент использования оборудования.
Если учитывать потери на выходные и отпуск, то h=0,34,
Если учитывать потери, что нет 3-й смены, то h=0,22,
Отказы - h=0,04,
Переналадка оборудования h= 0,12
ОСНОВНЫЕ ПУТИ ПОВЫШЕНИЯ ПРОИЗВОДИТЕЛЬНОСТИ СТАНКОВ И АВТОМАТИЗИРОВАННОГО ОБОРУДОВАНИЯ (АО):
1.Повышение технологичности производительности
2.Совмещение разных операций в объеме
3.Сокращение времени на вспомогательные движения.
4.Сокращение времени на цикловые потери
НАДЕЖНОСТЬ АО:
Надежность оборудования - это свойство обеспечивать свою работоспособность в течении определенного срока службы, в условиях применения технического обслуживания, ремонта, хранения и транспортировки.
Нарушение работоспособности оборудования – отказ
В автоматических линиях и автоматизированных станках отказы могут быть связаны с нестабильностью работы под влиянием отдельных случайных факторов или сочетании этих факторов. Кроме того, причинами отказа могут быть потери первоначальной точности оборудования, из-за изнашивания его частей.
Безотказность оборудования - свойство оборудования сохранять свою работоспособность в течении некоторого времени.
Безотказность может быть оценена следующими показателями:
· Вероятность отказа по результатам испытания Nо - элементов, из которых некоторые отказали
Nот =Nо-Nи
Nи – исправные элементы
Qот= - вероятность отказа
· Вероятность безотказной работы:
р(t)=1- Qот = =
· Интенсивность отказа – это условие плотности вероятности возникновения отказа в единицу времени.
lот = х
Вероятность безотказной работы, выраженная через интенсивность отказа:
р(t)=
· Отказы, связанные с изнашиванием элементов оборудования подчиняются закону нормального распределения. В этом случае определяется наработка элемента на отказ
tср=
ti - наработка элемента оборудования на отказ за 1 час его работы;
N- число элементов оборудования;
m-число отказов элементов оборудования
· Долговечность (Д) – свойство оборудования сохранять работоспособность в течении некоторого времени, с необходимыми перерывами для технического обслуживания и ремонта до наступления предельного состояния.
Д отдельных механизмов и деталей связана с изнашиванием подвижных соединений, усталостью под действием переменных напряжений и старения.
· Ремонтопригодность – свойство, заключающееся в приспособленности к предупреждению и обнаружению причин возникновения отказов, повреждений, а также приспособленность к восстановлению работоспособного состояния путем технического обслуживания и ремонта.
· Технический ресурс – наработка от начала эксплуатации оборудования до перехода его в предельном состоянии. Оценка надежности сложной техники должна осуществляться на основе учета всех действующих факторов.
Рст(t)=Р1(t)xР2(t)xР3(t);
Р1(t)- надежность по внезапному отказу мех. узлов;
Р2(t)- надежность радиоэлектронного оборудования;
Р3(t)- надежность, обусловленная отказами по изнашиванию элементам узлов.
· Технологическая надежность – свойство сохранять во времени первоначальную точность оборудования и соответствующее качество обработки изделия.
· Диагностирование – эффективное средство повышенной надежности, при этом осуществляется направленный сбор текущей информации о состоянии оборудования, о его важных узлах и элементах. При непрерывном действии оборудования используют параметрический метод диагностики. В этом случае модель оборудования представляется в виде дифференциальных уравнений.
Для повышения надежности АО целесообразно :
1. Оптимизировать сроки службы наиболее дорогостоящих механизмов и узлов на основе статистических данных и анализов.
2. Обеспечивать долговечность ответственных подвижных соединений
3. Применять материалы и разные виды т/о, обеспечивающие высокую стабильность базовых деталей на весь срок службы оборудования.
4. Устранять в ответственных соединениях трение скольжения
5. Применять принцип резервирования
6. Распространять профилактические устройства обнаружения и предупреждения возможных отказов по наиболее вероятным причинам.
ПОГРЕШНОСТИ МЕХАНООБРАБОТКИ, ВЫЗЫВАЕМЫЕ СРЕДСТВАМИ АВТОМАТИЗАЦИИ:
Работая в полуавтоматическом или автоматическом режиме автоматизированное оборудование (станок с ЧПУ) должны обеспечивать точность обработки, которая зависит от суммарной точности обработки.
На точность влияют ряд факторов:
1.Точность самого оборудования
2.Точность системы управления
3.Погрешность установки заготовки
4.Погрешность наладки инструмента на размер
5.Погрешность станка на размер
6.Погрешность изготовления инструмента
7.Размер износа режущего инструмента
8.Жесткость системы СПИД
1. Точностью оборудования в ненагруженном состоянии называется геометрическая точность.
В зависимости от точностной характеристики станки делятся на 4 класса:
Н – нормальной точности
П - повышенной точности (~0,6 интервал отклонений получается на станках Н точности)
В - высокая точность (~0,4 интервал отклонений получается на станках от класса Н точности)
А - особо точные (~0,25 интервал отклонений получается на станках от класса Н точности)
Геометрическая точность зависит от погрешностей соединения элементов станка и влияет на точность взаимного расположения узлов станка при отсутствии внешнего воздействия. Она зависит в основном от жесткости изготавливаемых соединений базовых деталей станка, а также от качества сборки станка.
На погрешность в расположении основных узлов станка распространены нормы:
1) точность геометрических форм и относительное положение опорных поверхностей, базирующих заготовку и инструмент.
2) точность движений по направляющим станка
3) точность расположения осей вращения и траектории перемещения рабочих органов станка несущих заготовку и инструмент относительно друг друга и относительно базовой поверхности.
4) точность обработанных поверхностей образца
5) шероховатость обрабатываемых поверхностей образца
Для станков с ЧПУ точность дополнительно характеризуется:
1) Точностью линейной интерполяции рабочих орагнов (позиционная)
2) Величиной зоны нечувствительности, т.е это отставание в смещение рабочих органов при смене направления движения
3) Точность возврата рабочих органов в исходное положение
4) Точность обработки в режиме круговой интерполяции
5) Стабильность положения инструмента после их автоматической смены
Общая допустимая ошибка при позиционировании рабочих органов определяется:
Dр=D+d;
D - накопленная погрешность при позиционировании,
d - нестабильность достижения заданного положения.
Для сохранения точности станка в течении долгого времени нормы геометрической точности станка ужесточают на 40% - это запас на изнашивание элементов станка.
2. Точность системы управления зависит от ошибки интерполятора и режима интерполяции. Интерполятор вносит определенную погрешность в обработку детали. Для интерполяторов характерны отклонения обработанной траектории от заданного отклонения, зависит от угла наклона траектории к координатным осям и обычно не превышает цены дискреты на участке любой протяженности Тн в одну из сторон заданной траектории
Отклонение влияет на точность обработки (шероховатость) весьма существенно. Ошибками проявляются в режиме интерполяции, но они не зависят от него; их причиной являются циклические ошибки при передачи движения приводом подач.
При работе по одной координате эта ошибка проявляется в виде неравномерного движения рабочих органов. При одновременном движении рабочих органов по нескольким координатам, неравномерность приводит к погрешности обработки траектории и волнистости поверхности детали.
Погрешность апроксимации.
Проявляются тогда, когда применяется линейный интерполятор, для повышения точности уменьшают шаг апроксимации.
3. Погрешность установки заготовки на станке - d определяется суммой погрешностей базирования и погрешностей закрепления.
d=dб+dз
Погрешность является вектором, поэтому суммирование производится геометрически.
dб - возникает вследствии не совмещения установочной базы с измерительной
dз - проверяется под действием зажимных сил, смещение заготовки происходит вследствии деформации самой заготовки, деформируется установочный элемент и корпус приспособления.
В связи с неоднородностью качества поверхности и нестабильности удельных нагрузок возникают различные по высоте осадка для всех заготовок партии. Погрешность закрепления равна разности между предельным смещением измерительной базы в партии обработанной детали.
4. Погрешность наладки инструмента:
Сколько бы ни была высока точность приборов для наладки инструмента все равно есть отклонения. Эти отклонения определяются погрешность самого прибора и погрешностью закрепления на станке налаженном на размер инструмента.
Погрешность прибора зависит от шкалы отсчета прибора, отсчет размера по шкале, неточность совмещения инструмента с перекрытием экрана проектора, несовмещение начала координат шкалы и измерительного устройства при закреплении инструмента, неточность углового расположения на приборе устройства для закрепления инструмента.
Погрешность закрепления инструмента: несовпадение нуля отсчета координат инструмента с теоретическим положением из-за неточности расположения поверхностей базирования инструмента на станке, неправильное угловое расположение на станке базовых поверхностей, деформация элементов участвующих в зажиме инструмента на станке. Погрешность нельзя учесть и нельзя скомпенсировать.
5. Погрешность наладки станка на размер:
Наладка станка на размер заключается в согласовании установки налаженной на размер режущего инструмента, рабочий элемент станка и базирующих элементов приспособления в положения, которые с учетом происходящих в процессе обработки явлений обеспечивают получение требуемых размеров обрабатываемой поверхности детали с заданным допуском.
Взаимное положение элементов технологической системы – называется установочным размером.
Погрешность наладки станка возникает в следствии того, что при отыскивании нуля станка, либо нуля инструмента невозможно расположить рабочие элементы станка или инструмент точно в расчетное положение.
В процессе наладки, чтобы определить установочный размер для каждого инструмента, наладчик использует метод пробных рабочих ходов, а в процессе дальнейшей обработки партии детали метод автоматического получения размеров.
Погрешность наладки станка равна разности предельных значений установочных размеров и зависит от погрешности наладки инструмента на размер; установки нулевого положения станка по программе; от измерения пробных деталей при наладке станка; отклонения центра группирование пробных деталей относительно середины поля рассеяния в момент наладки.
Точность наладки повышается при увеличении числа пробных деталей, если уменьшить кол-во деталей то необходимо увеличить квалификацию наладчика.
Подрегулированием установочного размер понимается восстановление установочного размера изменившегося в следствии размерного изнашивания инструмента или температурной деформации системы. Инструмент для обработки наружных поверхностей с учетом размерного износа следует налаживать ближе к нижней границе поля допуска, а инструмент для обработки внутренних поверхностей – ближе к верхней границе допуска.
6. Погрешность изготовления инструмента:
При токарной обработке, обрабатываемая поверхность формируется различными точками, закругления поверхности инструмента. Это обстоятельство необходимо учитывать при программировании обработки конических и криволинейных поверхностей детали, если же фактический радиус при вершине резца имеет отклонения от заданного радиуса по программе, то это неизбежно приведет к погрешности обрабатываемого профиля.
Погрешность по оси Z:
Dd=Dr tg( );
Dr-относительно изменение радиуса закругления Dr=(rф-r) ;;
r-заданный радиус, rф- фактический;
Погрешность конического профиля; d=2Dr sin2( );
7. Размер износа режущего инструмента:
Износ инструмента сильно влияет на погрешность обработки, особенно при изготовлении деталей из жаропрочных и жаростойких материалов. Износ происходит по задней грани инструмента в результате трения между этой гранью и обрабатываемой поверхностью.
При износе резец уменьшает или увеличивает диаметр обрабатываемой детали.
Износ инструмента вносит в наладку станка погрешность, пусть первоначальная наладка инструмента была проведена так, что поле рассеяния размера детали совмещено с началом поля допуска на саму деталь.
Если через некоторое время t1 произвести повторную выверку детали, то поле рассеяние не изменится, но изменится центр группирования, он сместиться в сторону износа инструмента. Чтобы размеры детали не вышли за поле допуска, требуется наладка станка через период времени t1, для компенсации радиального износа инструмента.
8. Жесткость системы СПИД:
Характеризуется упругими деформациями. Силы резания при обработке вызывают упругие деформации отдельных элементов системы, особенно в местах соединения деталей. При отсутствии необходимой жесткости под действием составляющей силы резания система деформируется, что вызывает погрешности формы и размеров обрабатываемой заготовки.
Жесткость станка зависит от:конструктивного исполнения; предельной тяги отдельных элементов; качества сборки.
В процессе обработки заготовки погрешность формы на каждом последующем ходе инструмента будет уменьшаться, чем выше жесткость станка, тем за меньшее число рабочих ходов можно достигнуть требуемой жесткости.
Тепловые деформации и деформации от внутренних напряжений заготовок:
Тепловые деформации возникают в результате выделения тепла элементов детали гидравлической системы и движущимися частями станка (образование тепла в процессе резания, непостоянство температуры теплового режима в помещении).
Тепловые деформации частей станка в начале его работы протекают интенсивно, затем интенсивность уменьшается и по истечении некоторого времени величина деформации стабилизируется.
Для повышения точности обработки следует прогреть станок до начала обработки на нем детали. Для отвода тепла из зоны резания применяют СОЖ, чистовую обработку необходимо проводить после охлаждения детали.
Заготовкам присущи внутренние напряжения, которые с течением времени постепенно выравниваются и уменьшаются, при этом сама заготовка деформируется.
Для уменьшения внутренних напряжений заготовки необходимо черновую обработку отделить от чистовой.
ГИБКИЕ ПРОИЗВОДСТВЕННЫЕ МОДУЛИ (ГПМ) И СИСТЕМЫ (ГПС). СТРУКТУРА ГИБКОГО ПРОИЗВОДСТВА:
ГПМ как объект проектирования и управления представляет собой систему, отличающуюся от другой системы сложностью, комплектностью и многофункциональностью.
Одним из основных требований обеспечивающих типизацию решений в области ГАП является принцип модульности (ГАП комплектуется из отдельных модулей).
Классификация ГАП:
ГАП – производственная часть интегрированного предприятия или самостоятельное предприятие, состоящее из гибких производственных комплексов ГПК, системы и службы обеспечения, взаимодействующие и управляющие всей хозяйственной деятельностью с помощью ЭВМ.
Цель создания ГАП: малолюдные или безлюдные предприятия, способные обеспечить выпуск широкой, постоянно обновляемой номенклатуры изделий.
ГПК – это самостоятельное производственное подразделение, состоящее из ГПС и служб инженерно – технической – инструментальной подготовки производства, а также планово - диспетчерского отдела ПДО.
Функциональность производства и служб, обеспечивается компьютерной системой управления, выполняющей функциональное оперативное планирование, управление оперативной подготовкой производства, учета, анализа и управления ходом производства.
ГАП, ГПК – управленческие задачи, технозадачи не решают.
Гпс – производственная часть ГПК, состоящая из одного или нескольких гибких технологических комплексов (ГТК) и транспортно-складских комплексов (ТСК). Работой ГТК и ТСК управляет компьютероризированный диспетчерский комплекс.
ГПС автономно функционирует в малолюдном режиме, в течении заданного интервала времени, обладает свойством автоматической переналадки при производстве изделий произвольной номенклатуры в пределах технической возможностей оборудования.
ГТК –это совокупность однородных по виду техно-обработки или по типу обработанной детали ГПМ, объединенных единым транспортным модулем ТСК, управление производится от единой комплексной системы управления и контроля.
При объединении нескольких ГТК близкого технологического назначения можно получить ГТУ (участок), участок обслуживания одной производственной бригадой.
ТСК – это совокупность взаимосвязанных автоматизированных транспортных и складских устройств и средств вычислительной техники, предназначенных для организации движения материальных и сопровождающих их информационных потоков ГПС.
ГПМ – это автономно функционирующая группа гибких обрабатывающих ячеек (ГОЯ), объединенных групповым, локальным, автоматическим устройством загрузки партии заготовок и удаления обработанной детали.
ГОЯ или РТК – это автоматическая многофункциональная на время обработки партии детали единица оборудования, оснащенная автоматическими устройствами для загрузки, заготовления и удаления обработанных деталей, накопителями деталей.
ГОЯ имеет возможность автоматической переналадки на различные изделия ограниченного класса.
ВАРИАНТЫ КОМПОНОВОК ГТК:
1. С продольным расположением ГОЯ
|
2. С поперечным расположением ГОЯ
|
|
|
При последней структуре оператор с одной точки может контролировать от 3 до 4 обрабатываемых ячеек. Такое расположение ячеек предпочтительно при частых переналадках, в которых участвует человек, с точки зрения техники безопасности есть зоны, которые не пересекаются с транспортной магистралью.
3 схема - это схема с жестким примыканием ГОЯ к автоскладу, является наиболее простой по набору техно- средств, но не обладает необходимой гибкостью, а ограничивает возможные последующие расширения системы.
Большой гибкостью из предложенных компоновок обладают компоновки с использованием транспортирующей системы.
ГОЯ, входящие в состав ГПМ, различаются составом технологического оборудования, способами использования робототехники организации взаимодействия ячеек друг с другом, а также со складской системой, способом подачи заготовок в ГТК.
При выборе структуры, а также компоновочной структуры ГПС, входящих в нее ГТК необходимо учитывать ряд факторов: потребная площадь, удобство обслуживания, стоимость оборудования, сложность вспомогательного оборудования, изменение производственной мощности, удобство контроля за работой оборудования.
Наряду с этим, на структуру компоновочных решений накладываются ограничения техно-возможностей и некоторые особенности использования оборудования.
СРЕДСТВА АВТОМАТИЗАЦИИ ТП. СРЕДСТВА АВТОМАТИЗАЦИИ РТК:
РТК– это совокупность единицы технологического оборудования ПР и средств оснащения, автономно функционирующая и осуществляющая кратные циклы, т.е это ГОЯ, образуемая станком и роботом и параллельно вспомогательным оборудованием.
Организационным звеном РТК является ПР, который может производить манипулирование деталями, инструментом и оснасткой, а также выполнять вспомогательные функции.
В состав РТКвходят подсистемы: формообразования, манипулирования, накопления и выдача деталей, хранение инструмента, контроль и управление.
Подсистема формообразования служит для выполнения обработки детали
Она состоит из: привода инструмента, привода детали, кинематической и механической цепей, преобразователя энергии.
Подсистемой манипулирования предназначена для манипулирования и позиционирования обрабатываемой детали, инструмента, вспомогательного и зажимных приспособлений.
Подсистема накопления и выдачи деталей предназначена для накопления и складирования межоперационных заделов.
Состоит из: транспортно-накопительных устройств, загрузочных устройств, устройств для складирования.
Подсистема хранения инструмента это инструментальные магазины, конструктивно выполненные заодно со станком, или это самостоятельные агрегаты, установленные рядом со станком.
Подсистема контроля служит для контроля обрабатываемой детали, а также диагностирование износа и поломки элементов оборудования.
Подсистема управления служит для согласования работы всех вышеперечисленных систем (управляет ими).
Кроме всех этих систем в РТК должна быть вспомогательная подсистема, для выполнения различного рода вспомогательных работ (удаление стружки, очищение СОЖ, охлаждение масла).
Если РТК выполняет функцию ГПМ, т.е один робот обслуживает несколько станков, то появляется в РТК функция транспортирования, т.е. робот должен перемещать заготовки и изделия от станка к станку.
РТК отличается от станков с ЧПУ высоким уровнем автоматизации. Они могут функционировать в составе ГПМ, а так же ГТК
Главной отличительной чертой РТК является расположение станков относительно ПР.
Простейшей схемой является схема обслуживания одним роботом одного станка, в этом случае мы получаем ГОЯ, робот может встраиваться в станок, либо он является отдельной единицей РТК, тогда компоновка РТК будет напольная (а) или портальная (б).
|
|
(б)
Портальная компоновка чаще используется для обслуживания 2-4 станков, т.е. траверса портала увеличивает.
Напольные роботы также могут использоваться для обслуживания 2-3 станков, но для них могут использоваться не однотипные станки.
Выбор той или иной структуры компоновки РТК определяется конкретными условиями производства, обрабатываемой детали, самим ПР, а также станками.
Дата добавления: 2018-05-12; просмотров: 267; Мы поможем в написании вашей работы! |
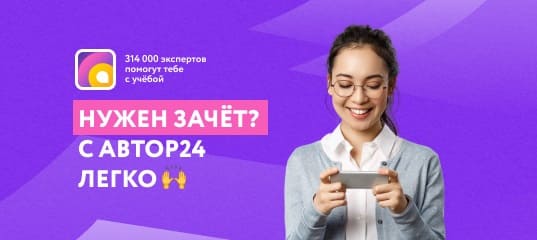
Мы поможем в написании ваших работ!