Розрахунок розмірних ланцюгів
Заняття 24( 2 години; всього 12 годин) ТЕМА 7: Методика проектування верстатних пристосувань. ЗМІСТ: 1 Вихідні дані для проектування пристосувань. 2 Формулювання його службового призначення. Розробка технічних вимог до пристосування 3 Застосування стандартних деталей при проектуванні пристосувань. 4 Розрахунки, які виконуються при проектування пристосувань
САМОСТІЙНА РОБОТА № 7
Заняття №24--28(3годин)
Тема: Методика проектування верстатних пристосувань.
Зміст: 1 Вихідні дані і послідовність проектування
2 Послідовність складання завдання на проектування оснастки
3 Виконання конструкторської документації по завданню на проектування
4 Особливості проектування універсально-налагоджуваних, спеціалізованих пристосувань.
5 Перевірка надійності затиску деталі в пристосуваннях по силам й обертаючих моментах діючих на заготовку в процесі різання
Література(1,с.6-11; 2,с.195-216; 3,с.44-52)
Принципову схему конструкції спеціального верстатногопристосування виконує технолог, що проектує технологічний процес обробки деталі. Конструкцію пристосування по схемі, запропонованій технологом, розробляє конструктор по технологічному оснащенню. У масовому великосерійному і частково в серійному виробництвах технолог при проектуванні технологічного процесу виготовляє операційні ескізи механічної обробки деталі для всіх основних операцій. При цьому технолог намічає установчі базові поверхні, схему установки деталі в пристосуванні і місця її затиску.
|
|
Розташування деталі на схемі пристосування повинне відповідати її положенню у верстатному пристосуванні при обробці деталі на відповідному верстаті. У разі установки деталі в пристосування не по конструктивних, а по допоміжних технологічних базах технолог повинен розрахувати погрішності базування і виробити перерахунок допусків на базисні розміри і на ескізі деталі проставити нові розрахункові допуски. Конструктор, одержавши від керівника групи завдання на розробку спеціального верстатного пристосування для обробки деталей на відповідному верстаті, проводить наступну роботу:
1 Вивчає принципову схему конструкції спеціального пристосування, розробленого технологом, в якій вказаний спосіб базування і закріплення деталі.
2 Вивчає робочі креслення заготівки і готової деталі з технічними вимогами.
3Знайомиться по технологічній карті з технологічним процесом механічної обробки деталі.
4 Вивчає операційний ескіз механічної обробки деталі на відповідній операції.
5 Знайомиться з верстатом, на якому буде встановлено проектоване спеціальне пристосування і яким інструментом буде оброблятися задана деталь, параметри режимів різання, норми часу на задану продуктивність обробки і схему її установки і закріплення в проектованому пристосуванні.
|
|
6 Вивчає в механічному цеху умови роботи проектованого пристосування і вирішує з інженерно-технічними працівниками цеху виниклі питання і виявляє їх пропозиції і побажання.
7 На закінчення конструктор з технологом вирішує ряд питань, що виникли у конструктора в процесі ознайомлення із завданням: взнають річну програму випуску деталей, обговорюють схему конструкції пристосування, визначають економічний ефект від застосування пристосування і остаточно встановлюють оптимальний варіант схеми конструкції пристосування.
8 Далі конструктор на підставі прийнятої схеми пристосування конструктивно оформляє елементи пристосування і його загальну компоновку з необхідними проекціями і розрізами.
При проектуванні конструкції пристосування конструкторвикористовує наступні матеріали:
- нормативні документи, стандарти , ДСТУ і ГОСТи на різні деталі і вузли верстатних пристосувань і механізованих приводів;
- креслення пристосувань, які застосовуються на даному заводі для обробки аналогічних деталей;
|
|
- креслення конструкцій спеціальних і групових пристосувань, які застосовуються на інших заводах.
Після розробки конструкції пристосування конструктор повинен показати технологу креслення пристосування і одержати його згоду на виготовлення даної конструкції в металі.
При ретельному опрацьовуванні початкової інформації конструктор може запропонувати технологу найраціональнішу побудову операції і вибрати іншу схему пристосування.
Обґрунтування конструкції пристосування слід пов'язувати із забезпеченням заданої продуктивності верстата на даній операції, яка визначається програмою випуску виробів. Ця програма враховується при розробці технологічного процесу виготовлення деталі і позначається на початкових даних для проектування пристосування. Чинником, що визначає досягнення заданої продуктивності верстата і конструкцію пристосування, є співвідношення такту випуску і штучного часу з урахуванням його складових, з яких головним в даному випадку є сумарний технологічний і допоміжний час, що витрачається на установку і зняття заготівки і управління пристосуванням. Тому прийняття рішення про конструкцію пристосування тісне зв’язано з нормуванням технологічного процесу.
|
|
Остаточне рішення про вибір тієї або іншої конструкції пристосування слід ухвалювати після розрахунку економічної ефективності, який полягає в зіставленні витрат і економічного ефекту при використовуванні прогресивного пристосування, відношуваних до річного періоду експлуатації.
Правильний вибір конструкції пристосування позитивно відображається на собівартості деталей, що випускаються, і машин.
При проектуванні пристосування конструктор повинен проводити роботу в певній послідовності.
Контур оброблюваної деталі показують тонкими суцільними або штрихпунктирними лініями, щоб вона виділялася на кресленні пристосування.
Навколо контура деталі спочатку викреслюють направляючі деталі пристосування. Потім вибирають і викреслюють установчі або опорні деталі пристосування. Далі визначають і викреслюють затискні і допоміжні деталі пристосування. На закінчення вибирають форму і розміри, а також матеріал деталей пристосування і вмонтовують всі деталі і вузли на йогокорпусі. Спроектовану конструкцію спеціального пристосування викреслюють в декількох проекціях, а також дають необхідні розрізи і перетини, необхідні для пояснення роботи конструкції пристосування. Загальні види проекції пристосування слід викреслювати в масштабі 1:1. Проекції загальних видів пристосування повинні мати габаритні розміри. Hа проекціях проставляють контрольні розміри з допусками, що визначають точність взаємного розташування деталей пристосування, які забезпечують точність розташування поверхонь оброблюваних деталей в даному пристосуванні.
Точність роботи пристосування, що виготовляється інструментальним цехом, перевіряють в механічному цеху шляхом контролю розмірів деталей, оброблюваних в даному пристосуванні.
На кресленні загального вигляду пристосування указують технічні умови на пристосування і його габаритні розміри. На кресленні проекцій пристосування на поверхнях деталей, що сполучаються, повинні бути проставлені класи точності з посадкам, а також допуски на форми і розташування поверхонь установчих елементів і осей центруючих деталей пристосування.
У технічних умовах задають необхідну точність збірки окремих деталей пристосування і указують його наладку, методи перевірки при установці на верстаті і т.д.
На кресленні загального вигляду пристосування дають нумерацію всіх позицій деталей, що входять в пристосування.Розробляють їх специфікацію з вказівкою матеріалу і марки, номера ДСТУ, ГОСТів або нормативні документи. Після виготовлення проекцій загального виду пристосування виконується його деталювання. Робочі креслення пристосування виконуютьтільки на спеціальні деталі.
Далі креслення пристосування передають в інструментальний цех заводу, де виготовляють пристосування в металі. Після цього інструментальний цех перевіряє пристосування і здає його на центральний інструментальний склад або в механічний цех, де воно проходить випробування на верстаті. Пристосування вважається пригодним, якщо оброблена в ньому деталь відповідає кресленню і технічним умовам на її виготовлення.
При проектуванні пристосувань слід розраховувати:
- похибку установки деталі;
- погрішності настройки верстата;
- погрішності обробки;
- сумарну погрішність обробки деталей в даному пристосуванні;
- сили затиску деталі в пристосуванні залежно від сил різання і їх моментів, діючих на деталь при її обробці на верстаті;
- для пристосувань з механізованим приводом діаметр циліндра (поршня) або діаметр діафрагми і осьову силу на штоку механізованого приводу, яка передається через проміжні ланки затискнимипристроями пристосування.
При розробці конструкції верстатного пристосування необхідно строго дотримуватися єдиної системи конструкторської документації, в якій вказані загальні правила виконання креслень.
Після обоснованого вибору розрахункових параметрів необхідно провести розрахунки пристосування на точність, тобто визначити точність виготовлення пристосування по прийнятим параметрам.
З метою забезпечення заданої точності обробки пристосування, яке проектується, повинне володіти достатньою жорсткістю (в першу чергу в напрямі дії сил затиску обробки). Для цього бажано застосовувати конструкції з якнайменшою кількістю стиків. Менш переважні збірні конструкції пристосувань з великою кількістю стиків; більш переважні цільні і зварні конструкції.
Деталі пристосувань повинні бути жорсткими при роботі
на вигин і кручення і міцними при всіх видах навантаження в
експлуатаційних умовах.
Корпусні деталі потрібно конструювати так, щоб не виникала деформація при затиску заготовок і деформація елементів верстата (стола шпінделя і т.д.) де вони розташовуються і закріпляються.
Зменшення контактних деформацій стиків, що працюють на стиснення, можливе за рахунок зниження шорсткості контактуючих поверхонь, підвищення твердості підповерхневого шару металу і попереднього затягування елементів пристосування кріпильними деталями, що сполучаються. Плоскі стики менш жорсткі на вигин, ніж на кручення. У працюючих на вигин стиках рекомендується розташовувати болти нерівномірно, зміщуючи їх по можливості на більшу відстань від нейтральної осі. В цьому випадку доцільно також скорочувати поверхню контакту деталей, що сполучаються, у області нейтральної осі.
Жорсткості стиків деталей з поверхням, обробленими шабренієм і притиранням, і з шліфованими поверхнями мало відрізняються. Достатньо висока жорсткість стиків з площинами, обробленими струганням, при збігу рисок (слідів) обробки. Контактну жорсткість стиків можна підвищити за рахунок попередньої термічної (гарт) або хіміко-термічної (наприклад, цементація з подальшим гартом) обробки деталей, а також за рахунок нанесення тонкого клейового шару між зв'язаними поверхнями, який підвищує демпфуючих властивості стику при виникненні вібрацій.
При розробці креслення загального виду пристосування і його робочих креслень конструктор повинен встановити допуски розмірів, які по точності розбиваються на три групи. До першої групи відносяться розміри елементів і спряження, які безпосередньо визначають точність обробки (відстань між осями кондукторних втулок свердлувального пристосування, відхилення від паралельності робочої площини установчих елементів і площини корпусу пристосування, контактуючої із столом верстата, і т. д.), а також розміри установчих елементів. До другої групи входять розміри деталей і сполучень пристосувань, похибки яких не роблять впливу на точність обробки (розміри сполучень затискних пристроїв і приводів, виштовхувачів і інших допоміжних пристроїв), в третю — розміри не спряжених оброблених і необроблених поверхонь деталей пристосувань.
Існують практичні рекомендації по вибору допусків розмірів деталей і сполучень пристосувань. Допуски розмірів першої групи звичайно приймаються в 2...3 рази меншими, ніж розмірів, що витримують при обробці заготівки. Це забезпечує в ряді випадків достатньо надійне виконання заданих розмірів заготівки і необхідний ресурс роботи пристосування до граничного зносу його елементів.
Доцільніше і правильно з технічної, методичної і економічної точок зору встановлювати допуски по розрахунку пристосування на точність.
Допуски розмірів другої групи призначаються при конструюванні пристосувань залежно від характеру і умов роботи даних сполучень і призначення механізму. Найчастіше допуски розмірів деталей, що сполучаються, приймаються по 6:..8-му квалітетам точність. Вільні розміри виконуються по 14-му квалітету точності для оброблених і по 16-му — для необроблених поверхонь деталей пристосувань.
Ретельне опрацьовування питань точності пристосувань сприяє підвищенню якості обробки заготівки, точності деталей ресурсу експлуатації пристосування. Так, погрішності виготовлення свердлувальних і розточувальних кондукторів впливають на точність міжцентрових відстаней між оброблюваними отворами, відстаней від технологічної бази до осей отворів, а також на відхилення від перпендикулярності осей отворів відносно опорного торця заготівки. За наявності поворотних пристроїв можуть виникати погрішності кутового розташування оброблюваних отворів, відхилення від паралельності їх осей відносно базової площини і відхилення від співвісної у разі розточування отворів з послідовним поворотом заготівки на 180 °.
Погрішності виготовлення і положення на верстаті фрезерних, стругальних, протяжних і довбіжних пристосувань приводять до неточностей взаємного положення оброблюваних і базових поверхонь заготівки, але не впливають на форму оброблюваних поверхонь і точність їх розмірів, забезпечуваних вимірювальним і іншим інструментом (при виконанні пазів, отворів, шліцьових поверхонь і т. д.). Неточності ділильних і поворотних пристроїв цих пристосувань можутьприводити до погрішностей відносного розташування оброблених поверхонь заготівки.
В цілому погрішності виготовлення пристосувань і установки їх на верстаті не впливають на точність розмірів і форму оброблюваних поверхонь, але приводять до погрішностей відносного положення поверхонь заготівки.
Контрольні питання
1 Вихіднідані
2 Знайомство з завданням
3 Базування
4 Визначеннязатискуючих пристроїв
5 Розрахунки
Заняття 25 (2 години)
Практична робота №4
ТЕМА: Ознайомлення з різними видами пристроїв до металорізальних верстатів
План: 1 По заданому типу пристосування визначити
тип пристосування, характеристику, будову
2 Розробити схему базування, закріплення заготовки та компоновки пристосування
3 Описати основні розрахунки
4 Відповісти на контрольні питання
Провести відповідно методичним вказівкам
Заняття 26-28 (6години)
Продовження теми 7
Тема: Послідовність проектування пристосувань
План: 1 Розробка теоретичної схеми базування обробляємої заготовки
2 Вибір типу установчих елементів
3 Розрахунок похибки встановлення заготовки
4 Вибір ріжучого інструменту та розрахунок режимів різання
5 Розрахунок зусилля затиску та вибір затискного пристрою
Проектування будь-якого пристосування починається з визначення теоретичної схеми базування об'єкту. Відповідно до ГОСТ 21495базування, тобто додання об'єкту, (заготівці, деталі, виробу) необхідного положення щодо прийнятої системи координат, здійснюється за допомогою вибраних на об'єкті баз у вигляді поверхонь, що належать йому, осей, крапок або їх поєднань. Сукупність трьох баз, утворюючих систему координат об'єкту, складає комплект баз. Використовування комплекту баз необхідне для забезпечення нерухомості об'єкту у вибраній системі координат. В цьому випадку на об'єкт накладається шість двосторонніх геометричних зв'язків, які символізуються шістьма опорними точками.
Під схемою базування розуміється схема розташування опорних точок на базах заготівки, деталі, складальної одиниці, виробу. Всі опорні точки на схемі базування зображаються умовними знаками і нумеруються порядковими номерами, починаючи з бази, на якій найбільша кількість опорних точок.
При викладі в якій небудь проекції однієї точки на іншу зображається одна точка і біля неї проставляються номери суміщених точок. Число проекцій об'єкту на схемі базування повинне бути достатнім для чіткого уявлення про розміщення опорних точок.
При накладенні геометричних зв'язків по комплекту баз тіло позбавляється можливості трьох переміщеньповздовж осей ОХ, OY і OZ і трьох поворотів навколо них, тобто стає нерухомим в системі OXYZ. Накладення двосторонніх геометричних зв'язків досягається в пристосуваннях через зіткнення (контакту) базових поверхонь заготівки або іншого об'єкту з робочими поверхнями установчих елементів - опор, до яких заготівки притискуються для забезпечення надійного контакту.
Шість зв'язків, що позбавляють заготівку руху в шести напрямах, можуть бути створені за рахунок забезпечення контакту її з опорами пристосування в шести точках: трьох по установчій, двох по направляючій і однієї по опорній базам. У разі ідеалізації форми контактуючих поверхонь вважається, що необхідні зв'язки досягаються при контакті об'єктів по поверхнях, а наявність реальних зв'язків символізується опорними точками. Таке положення застосовне, наприклад, при установці заготівок по плоских базуючих поверхнях на опорні пластини.
У теоретичній механіці розглядається визначення положення тіла відносно вибраної системи координат OXYZ через визначення положення пов'язаної з ним системи координат О1X1Y1Z1. Жорсткий зв'язок системи координат О1X1Y1Z1 з тілом дає можливість віднести до неї зв'язки, що накладаються на тіло.
Після остаточного уточнення питань установки заготівки в пристосування вибирають установчі, затискні і інші елементи пристосування, а також визначають вид затискного пристрою і його привід.
Як правило, проектування починається із зображення на листі контурів оброблюваної заготівки тонкими суцільними лініями. Заготівку зображають в потрібній кількості проекцій. Загальний вид (схема) пристосування викреслюється послідовним нанесенням його елементів навколо контурів заготівки (спочатку установчих елементів, потім затискних пристроїв з приводами, елементів для напряму і контролю положення інструмента, допоміжних пристроїв і деталей). Останнім креслять контур корпусу пристосування, який об'єднує все, вищеперелічені елементи в єдине ціле — пристосування.
Залежно від характеру обробки, конфігурації заготівки, прийнятого верстата і штучного часу на операцію вибирається одна з схем пристосування:
- одноміснеоднопозиційне;
- багатомісне однопозиційне;
- одномісне багатопозиційне;
- багатомісне багатопозиційне.
Доцільність цього вибору обґрунтовується при ескізному опрацьовуванні пристосування.
Найпростішими і часто застосовуємі, у всіх типах виробництва, є однопозиційні пристосування. При використовуванні багатопозиційних пристосувань необхідно створювати додаткові допоміжні пристрої (поворотні, ділильні, підйомні і ін.). Разом з тим багатопозиційні пристосування дозволяють значно підвищити концентрацію операцій, за рахунок чого зростає продуктивність обробки. Використовують їх переважно на спеціальних верстатах, застосування яких найбільш ефективне в умовах масового і великосерійного виробництв.
Залежно від допустимого допоміжного часу і з урахуванням необхідної сили затиску вибирають раціональну конструкцію силового приводу. Механізовані приводи забезпечують мінімальні витрати часу і енергії робітників на затиск заготівок, дозволяють автоматизувати управління пристосуванням або сумістити його з схемою управління верстатом.
Великий вплив на ефективність устаткування надає зручність роботи з пристосуванням. Для забезпечення простоти і безпеки установки і зняття заготівок на пристосуваннях слід передбачати завантажувально-розвантажувальні зони, вільні від виступаючих елементів пристосувань і рухомих частин їх пристроїв і механізмів. В умовах масового і великосерійного виробництв при обробці заготівок простої форми малих і середніх розмірів необхідно вивчити можливості автоматизації їх завантаження в пристосування і вивантаження з нього.
Для підвищення продуктивності потрібно поклопотатися про зручність і швидкість очищення пристосування. Цей процесу ряді випадків вдається автоматизувати, наприклад, за рахунок, періодичного обдування пристосування відпрацьованим в пневмоприводу стислим повітрям. Комплексна автоматизація пристосування, яка включає процеси автоматичного базування, закріплення, відкріплення і зняття заготівки, його очищення і піднастройки, забезпечує максимальну продуктивність і нерідко приводить до значного економічного ефекту.
Після відробітку схеми пристосування вибирають і обґрунтовують параметр для розрахунку його на точність. Потім виконують цей розрахунок, закінчуючи його розбиттям значення розрахункового параметру на допуски розмірів деталей пристосування, що входять в розмірний ланцюг. Після цього роблять силовий розрахунок, розрахунки на міцність і економічну ефективність.
Силовий розрахунок повинен ілюструватися схемою з вказівкою сил обробки і затиску, реакцій опор, сил тертя, діючих моментів, плечей дії сил і інших даних, необхідних для визначення потрібних сил затиску. Закінчують силовий розрахунок розрахунком затискного пристрою і приводу пристосування.
Для розрахунку на міцність вибирають одну-дві найбільш навантажені деталі пристосування. Економічне порівняння варіантів пристосування закінчують розрахунком річного економічного ефекту і терміну окупності нового, прогресивнішого пристосування.
Відповідно до даних розрахунків доцільно відкоректувати схему пристосування і розробити ескіз його складального креслення. Для складання специфікації на схемі (ескізі) пристосування потрібно пронумерувати його деталі.
Повний розрахунок пристосування виконується студентами при виконанні курсового і дипломного проектів. Так, для студентів він включає загальну частину, аналіз оброблюваної заготівки,опис роботи пристосування, вибір елементів пристосування, його розрахункових параметрів, схем пристосування і його установки, а також його розрахунки на точність і міцність, силовий розрахунок, розрахунок економічної ефективності застосування, складальне креслення пристосування, специфікацію.
На кресленні загального виду пристосування слід приводити технічні умови його збірки і експлуатації з вказівкою точності в зібраному вигляді по вибраних параметрах, обробки в зборі для забезпечення заданої точності (у разі потреби), виду фарбування і інших покриттів, періодичності контрольних оглядів і перевірок точності, догляду за пристосуванням і обслуговування (очищення, змазування, заміна елементів, зберігання), вимог до установки на верстаті і регулювання і ін.
Особливо слід зупинитися на важливості продумування питань догляду за пристосуваннями в період експлуатації і зберігання. Догляд за пристосуванням, від якого залежить його працездатність і зовнішній вигляд, полягає в огляді, своєчасному змазуванні, ремонті і підфарбовуванні.
Залежно від умов роботи в ТУ слід указувати періодичність оглядів, які доцільно пов'язувати з перевіркою пристосування на точність по допустимому зношуванню установчих елементів. Періодичність змазування залежить від складності пристосування і умов його роботи. Краще всього передбачати безперервне автоматичне змазування поверхонь пристосування, що труться, і лише у разі крайньої необхідності — періодичне змазування, яке при постійному знаходженні пристосування на верстаті бажане здійснювати під час змазування верстата. У ТУ бажано указувати робочі і змащувальні матеріали, рекомендовані для застосування.
При використовуванні лакофарбних покриттів в ТУ указують марку фарби, її колір, експлуатаційні вимоги до покриття і ГОСТ на фарбу і покриття. На кресленнях деталей (елементів) бажано відображати необхідні відомості про металопокриття і хімічній (електрохімічної) обробці поверхонь.
Пристосування для обробки заготівок є ланкою системи СПІД. Від точності його виготовлення і установки на верстаті, зносостійкості установчих елементів і жорсткості значною мірою залежить точність обробки заготівок. При обробці партії заготівок, що мають погрішності форми, кожна з них і її вимірювальна база при установці в пристосуванні займають різне положення. Тому погрішність положення заготівки в пристосуванні слід розраховувати з урахуванням її розташування в просторі, що значно ускладнює розрахунки. На практиці в технічних розрахунках пристосувань на точність обмежуються спрощеними плоскими схемами розрахунку.
Точність, яку вимагається, пристосування можна визначити рішенням розмірного ланцюга технологічної системи заготівка — пристосування — верстат — інструмент, що відображає роль кожної ланки в досягненні точності розміру, що витримується, на оброблюваній заготівці. При цьому виявляється роль пристосування в: досягненні заданої точності виконуваного на заготівці розміру — замикаючої ланки розмірного ланцюга і методично строго пояснюється необхідність розподілу допуску, що обмежує відхилення від виконуваного розміру, на частини, одна з яких виділяється для пристосування. Ця частка допуску розміру заготівки і буде допуском розміру пристосування (або відносне відхилення положення його поверхонь). Допуск розміру пристосування в зборі в процесі рішення іншого розмірного ланцюга повинен бути розподілений на допуски розмірів деталей пристосування, що є її складовими ланками. Такий підхід до розрахунку пристосувань на точність підвищує його точність і показує взаємозв'язок елементів системи СПІД в забезпеченні точності обробки.
Проте спеціальні пристосування проектуються найчастіше до запуску нових виробів у виробництво, коли немає можливості уточнення цілого ряду питань (оброблюваності застосованих у виробі матеріалів, виду використовуваного устаткування і ін.). Тому параметри точності пристосувань найчастіше визначаються аналітично по рекомендованих довідниками і іншими літературними джерелами формулах.
Розподіл одержаного допуску виготовлення пристосування в зборі на допуски розмірів деталей, що є ланками розмірних ланцюгів пристосування, забезпечується рішенням прямої задачі при розрахунку цих ланцюгів.
Мета розрахунку на точність полягає у визначенні необхідної точності виготовлення пристосування по вибраному параметру і завдань допусків розмірів деталей і елементів пристосування. Розрахунок, як правило, повинен складатися з наступних етапів:
1) вибір одного або декількох параметрів пристосування, які роблять вплив на положення і точність обробки заготівки;
2) ухвалення порядку розрахунку і вибір розрахункових чинників(факторів);
3) визначення необхідної точності виготовлення пристосування по вибраних параметрах;
4) розподіл допусків виготовлення пристосування на допуски розмірів деталей, що є ланками розмірних ланцюгів;
5) внесення в ТУ складального креслення пункту про забезпечення точності пристосування обробкою його в зборі (у разі неможливості або економічної недоцільності забезпечення одержаного розрахунком допуску розміру пристосування шляхом виготовлення з відповідною точністю і збірки деталей).
Вибір розрахункових параметрів здійснюється в результаті аналізу прийнятих схем базування і закріплення заготівки і пристосування, а також точності забезпечуваних обробкою розмірів. Пристосування розраховується на точність по одному параметру у випадку, якщо при обробці заготівки розміри виконуються в одному напрямі, по декількох параметрах, якщо на заготівці виконуються розміри в декількох напрямах.
Напрям розрахункового параметру пристосування повинен співпадати з напрямом виконавчого розміру при обробці заготівки. При отриманні на оброблюваній заготівці розмірів в декількох напрямах пристосування можна розраховувати тільки по одному параметру у напрямі найточнішого по допуску і найвідповідальнішого по кресленню деталі, що виготовляється, розміру.
Залежно від конкретних умов за розрахункові параметри можуть виступати допуск паралельності або перпендикулярності робочої поверхні установчих елементів до поверхні корпусу пристосування, контактуючої з верстатом; допуск лінійних і кутових розмірів; допуск співвісності (ексцентриситет) і перпендикулярності осей циліндрових поверхонь і т.п. Найчастіше розрахунковий параметр визначає точність положення робочих поверхонь установчих елементів (їх робочих поверхонь) пристосування відносно опорних (посадочних, приєднувальних) поверхонь корпуса, за допомогою яких пристосування з'єднується із столом або шпінделем верстата. Іншими словами, розрахунковий параметр повинен зв'язувати по точності відносного положення поверхні пристосування, які контактують із заготівкою і з верстатом.
На точність обробки впливає ряд технологічних чинників, що викликають загальну погрішність обробки , яка не повинна перевищувати допуск Твиконуваного розміру при обробці заготівки, тобто
≤ Т-ω
де Т – допуск на одержуваний розмір деталі;
ω – точність обробки, яку отримують при виконанні даної операції без обліку похибки базування (її можна приймати по таблицям з довідників при середній точності обробки).
Для виразу допуску Твиконуваного при обробці розміру слід користуватися формулою
де ∆у — погрішність внаслідок пружних віджимань технологічної системи під впливом сил різання;
∆н — погрішність настройки верстата;
— погрішність установки заготівки в пристосуванні;
∆и — погрішність від розмірного зношування інструменту;
∆т — погрішність обробки, що викликається тепловими деформаціями технологічної системи;
∑∆ф — сумарна погрішність форми оброблюваної поверхні, обумовлена геометричними погрішностями верстата і деформацією заготівки при обробці і входить в Т, оскільки погрішність форми поверхні є частиною поля допуску її розміру.
Розрахункову припустиму сумарну похибку пристосування [εпр]розраховують за формулою:
[εпр] ≤ Тd– (К1εб +εз + К2ω);(17)
де Тd - допуск на обробляємий розмір заготовки;
К1= 0,6-0,85 - коефіцієнт, що враховує наявність відхилень базових поверхонь, нерівних їх граничним значенням;
К2 =0,6 – 1,0 - поправочний коефіцієнт;
εб-дійсна похибка базування εб≤ [εдоп] (4, с 17)
εз - похибка закріплення;
Дійснупохибку базування εб, при несумісності установчої та вимірювальної бази в результаті неточності форми і розмірів деталі, що встановлюється, отримують розрахунковим шляхом (8).
εз - похибка закріплення; визначають дослідним шляхом або приймають по таблицямта емпіричними формулами (8, таблиця 22).
ω- точність обробки даним методом - приймають для конкретного методу обробки за допомогою таблиць точності обробки (( 8, таблиці 2-11).
По знайденій допустимій сумарній похибці [εпр] визначають допустимупохибку виготовлення і збірки елементів пристосування, що впливають на точність встановлення в неї обробляємої заготовки з урахуванням допустимого зносу цього пристосування в різних умовах експлуатації.
1) При використанні пристосування в серійному виробництві:
εуст =[εпр]-
; (18)
де εу- складова, що характеризує знос установчих елементів пристосування.
Величина зносу залежить від програми випуску деталей, їх конструкції і розмірів, матеріалу і маси заготовки, стану її базової поверхні, а також умов встановлення заготовки в пристосування та її зняття.
Величину зносу визначають за формулою:
або
(19)
де N - кількість контактів заготовки з опорою;
β1, β2- постійні(таблиця 2);(6)
n = 0,4 - 0,6(в середньому приймають 0,5)
Великі значення β1, β2обирають для важких умов роботи опор по навантаженню, шляху зсуву при встановленні і знятті заготовки, часу нерухомого контакту та абразивної дії заготовки.
Складоваεс виражає похибку установки пристосувань на століверстата. Вона визначається точністю направляючих елементів пристосування (направляючих шпонок, установчих пальців та ін.) і точністю Т-подібних пазів столу верстата та інших елементів. Величина εсскладає звичайно 10-12 мкм.
2)Привикористанні стаціонарногобагатоверстатногопристосування у масовому виробництві:
εуст = ; (20)
3) При використанні пристосувань-супутників на автоматичній лінії
εуст = ; (21)
4) При використанні одномісного стаціонарного пристосування у масовому виробництві похибки εуст і εс являються систематичними та можуть бути зведені відповідною наладкою практично до нуля, тобто:
[εпр]=εи (22)
Погрішності, залежні від пристосування, розраховуються в кожному, конкретному випадку по прийнятих схемах базування, закріплення і обробки.
Отже повинна виконуватись умова
εб<εуст<[εпр]<Тd
Один з останніх етапів розрахунку пристосування на точність— розбиття допуску розмірів при його виготовленні на допуски розмірів деталей. При цьому за замикаючу ланку розмірного ланцюга приймається погрішність по прийнятому параметру εпр, що є допуском виготовлення пристосування. Після виявлення розмірного ланцюга розв'язується пряма задача, тобто визначаються розміри і допуски ланок розмірного ланцюга.
Розрахунок розмірних ланцюгів
Основні терміни, позначення і визначення розмірних ланцюгів встановлені ГОСТ 16319, а методи розрахунку ланцюгів — ГОСТ 16320. При розрахунку розмірних ланцюгів можуть розв'язуватися пряма і зворотна задачі. У першому випадку по встановлених вимогах до замикаючої ланки визначаються номінальні розміри, допуски, координати середин полів допусків і граничні відхилення всіх складових розмірний ланцюг ланок. При рішенні зворотної задачі по значеннях номінальних розмірів, допусків, координат середин їх полів, граничних відхилень складових ланок визначаються ті ж характеристики замикаючої ланки або при необхідності обчислити погрішність замикаючої ланки встановлюються поле розсіяння, координати його середини або межі відхилень замикаючої ланки на підставі аналогічних даних для складових ланок. Рішенням зворотної задачі перевіряється правильність рішення прямої задачі.
Точність замикаючої ланки розмірного ланцюга досягається методами:
повної взаємозамінності (включенням в розмірний ланцюг всіх складових ланок без вибору, підбору або зміни їх значень);
неповної взаємозамінності (включенням в розмірний ланцюг обумовленої частини ланок без вибору, підбору або зміни їх значень);
групової взаємозамінності (включенням в розмірний ланцюг складових ланок, що належать однієї з груп, на які вони заздалегідь розсортовані);
пригонки (зміною розміру компенсуючої ланки шляхом видалення з компенсатора певного шару матеріалу);
регулювання (зміною розміру компенсуючої ланки без видалення матеріалу з компенсатора).
У розмірних ланцюгах, в яких повинна бути забезпечена повна взаємозамінність, допуски розраховуються методом максимуму — мінімуму. При цьому враховуються тільки граничні відхилення ланок розмірного ланцюга і найсприятливіші їх поєднання.
Розмірні ланцюги, для яких економічно виправданий ризик можливого виходу за межі поля допуску замикаючих ланок у частини виробів, розраховуються методом вірогідності. При цьому враховується розсіяння розмірів і вірогідність різних поєднань відхилень складових ланок розмірного ланцюга.
Розмірні ланцюги наносяться на схеми пристосувань. За замикаючу ланку розмірного ланцюга в пристосуванні звичайно приймаються допуски лінійних і кутових розмірів пристосування в зборі, а також допуски співвісності, паралельності, перпендикулярності. Остання група, як правило, зв'язує по точності відносного розташування поверхні верстатного пристосування, яке контактує із заготівкою і верстатом або з інструментом і верстатом. Допуск визначається розрахунком точності виготовлення пристосування εпр по вибраному параметру.
Рішення розмірних ланцюгів для прямої задачі здійснюється в приведеній нижче послідовності.
1 Формулюється задача і визначається замикаюча ланка.
2 Виходячи з поставленої задачі, встановлюються номінальний розмір, координата середини поля допуску Т0т, допуск Т або граничні відхилення замикаючої ланки.
3 Виявляються ланки і будується схема розмірного ланцюга, складається її рівняння і визначаються передатні відносини.
4 По формулірозраховуються номінальні розміри ланок.
5 Вибирається метод досягнення необхідної точності замикаючої ланки, економічний в даних виробничих умовах, з урахуванням середнього значення допуску.
6 Розраховуються і встановлюються допуски, координати середин полів допусків і граничні відхилення:
Рішення розмірних ланцюгів для зворотної задачі здійснюється в приведеній нижче послідовності.
1 Формулюється задача.
2 Розраховується номінальне значення розміру замикаючої ланки:
Після зіставлення з необхідним значенням допуску можна переконатися, що допуски і координати середин полів допусків встановлені вірно.
В процесі проектування пристосувань розмірні ланцюги можна розраховувати також і методом регулювання. Для цього слід використовувати компенсуючи ланки з регулюванням положення, за рахунок чого забезпечується необхідна точність замикаючої ланки розмірного ланцюга пристосування.
На заготівку при обробці в пристосуванні діють сили обробки, об'ємні сили (вага заготівки, відцентрові і інерційні сили), сили випадкового ідругорядного характеру, а також сили затиску і реакцій елементівпристосування. При цьому заготівка повинна знаходитися в рівновазі. Всі перераховані вище сили — величини векторні, що мають кожна свій напрям і значення. Тому бажаний силовий розрахунок пристосування шляхом рішення задач просторового характеру. Проте з метою його прискорення і спрощення можна розглядати умови рівноваги в найбільш небезпечних напрямах в одній або декількох площинах. Здійснення цього принципу дозволяє скоротити терміни проектування пристосувань і понизити їх собівартість при збереженні достатніх для практики точності силових розрахунків і якості пристосувань.
Потреба в затискних пристроях виключається у випадках, коли: 1) сили обробки вельми малі в порівнянні з вагою заготівок і силами тертя; 2) сили обробки (складки) по напряму такі, що не можуть порушити положення заготівки, обумовлене базуванням.
Виконання вимог, що пред'являються до затискних пристроїв, пов'язане з правильним визначенням значень, напряму і місць додатку сил затиску. Аналіз затисків і приводів пристосування припускає виявлення їх пристрою, принципу дії, розрахункових розмірів (плечей важелів; відстаней від місця додатку сил до опор; напрямів дії сил різання, затискних, тертя, реакцій опор; діаметрів циліндрів й штоків пневмо- і гідроприводів; кутів клинових пристроїв), а також груп, до яких відносяться дані затиски.
При визначенні потрібних сил затиску у випадках, коли сили обробки співпадають з ними по напряму, іноді необхідно враховувати пружні характеристики затискних пристроїв. У цьому плані вживані в пристосуваннях затискні пристрої підрозділяються на дві основні групи.
До першої групи відносяться пристрої, пружні віджимання яких прямо пропорційні прикладеним до них силам . Ці пристрої мають в своєму складімеханізми типу що самогальмуються (гвинтові, клинові безроликові і ексцентрикові елементарні затискачі), привід їх може бути ручним і механізованим. У разі додатку до затискних елементів додаткових сил їх пружні віджимання змінюватимуться по лінійному (або близькому до нього) закону у напрямі сил, що прикладаються, і пропорційно їх зміні.
До пристроїв другої групи відносяться пневматичні, гідравлічні і пневмогідравлічні механізми прямої дії . При додатку до затискного елементу таких пристроїв (наприклад, штоку гідроциліндра) наростаючої сили переміщення штока в початковий період не буде. Шток відразу одержує велике переміщення, коли прикладена до нього сила перевищить протидіючу, створювану тиском рідини на поршень гідроциліндра (порушення контакту базових поверхонь з опорами, порушення положення і затиску заготівки). При використовуванні пристроїв цього типу з проміжними ланками без самогальмування віджимання затискного елементу в перший період протікає по лінійному закону за рахунок пружних деформацій ланок, потім, при зростанні сили до певного значення, елемент може різко переміститися.
Розрахунок сил затиску зводиться, як правіло, до рішення задач статичної рівноваги заготівки, що знаходиться в пристосуванні, під дією прикладених до неї сил і моментів.
При виборі схеми встановлення, направлення і місця прикладання зусилля затиску необхідно враховувати наступні правила:
- закріплення не повинно порушувати положення заготовки, досягнутого при встановленні;
- зусилля затиску необхідно прикладати там, де воно викликає найменші деформації оброблюваної деталі;
- місце затиску слід вибирати по можливості ближче до місця обробки.
- діючі на заготовки зусилля повинні по можливості сприйматися опорами пристосування.
2) Складаються рівняння статичної рівноваги заготовки з урахуванням коефіцієнта запасу зусилля затиску і (длясомогальмуючих затискних пристроїв) з урахуванням жорсткості елементів пристосування:
Методика розрахунку сил затиску зводиться до розв'язання одного з 3-х рівнянь:
де, ∑T – сума сил тертя, ∑MТ- сума моментів тертя, ∑Mвс - сума моментів встановлення, ∑Р - сума сил різання; ∑Mпер – сума моментів перевертання.
При складанні і розв'язанні рівнянь керуються загальновідомимиправилами, законами і формулами з пройдених курсів фізики ітеоретичної механіки.
3) Виходячи з рівнянь визначається зусилля затиску.
W = k · P,
Використання коефіцієнта запасу зусилля затиску (k) диктується необхідністю врахування коливання сил різання внаслідок неоднорідності обробляємих заготовок, коливання величини припуску на обробку, затуплення ріжучого інструменту, а також непостійності інших умов операції. Використання в розрахунках середнього значення k набірне. При малих значеннях k- надійність затискногопристрою недостатня. При великих значеннях k -перебільшення сили затиску веде за собою збільшення розмірів затискних пристроїв.
В залежності від конкретних умов побудови технологічної операції значення k слід вибирати диференційовано. Величину k можна представити /6, с.90/ як добуток первинних коефіцієнтів (k0, k1, k2,…, k6), що відображують конкретну умову обробки і закріплення заготовки:
Коефіцієнт k0, що представляє собою гарантований коефіцієнт запасу, для усіх випадків рекомендовано брати рівним 1,5.
Коефіцієнт k1 враховує наявність випадкових нерівностей на чорнових заготовках, що веде за собою підвищення сил різання. При чорновій обробці k1=1,2; при чистовій і оздоблювальній k1=1,0.
Коефіцієнт k2 враховує збільшення сил різання від прогресуючого затуплення ріжучого інструменту (k2=1.0 - 1,9).
Коефіцієнт k3 враховує збільшення сил різання при переривчастому різанні. При переривчастому точінні (валика з канавками та ін.), торцевому фрезеруванні k3 досягає значення 1,2.
Коефіцієнт k4 характеризує затискний пристрій з точки зорупостійності сил, що він розвиває. При ручному затискному пристрої сили затиску непостійні.
Встановлено що для ручних затискачів можна прийняти k4=1,3. При наявності пневматичних, гідравлічних, пневмогідравлічних та інших затискних пристроїв прямої дії k4=1,0. Якщодопуск на розмір заготовки впливає на силу затиску, що має місце при використанні пневмокамер, пневмоважільних систем, мембранних цангових патронів, а також інших пристроїв k4=1,2.
Коефіцієнт k5 характеризує зручність розташування рукояток в ручних затискних пристроях. При зручному розташуванні рукоятки і малому діапазоні кута її повороту k5=1,0. При великому діапазоні кута її повороту рукоятки (більше 90°) k5=1,2.
Коефіцієнтk6 враховують тільки при наявності моментів, що намагаються повернути заготовку. Якщо заготовка встановлена базовою поверхнею на опори з обмеженою поверхнею контакту, k6=1,0.
Якщо заготовка встановлена на планки або інші елементи з великою поверхнею контакту, коли мікронерівності на базовій поверхні заготовки, k6 приймається в межах до 1,5. Вибираючи значення коефіцієнтів k1... k6 відповідно до умов виконання операції, можна отримати величину k для кожного конкретного випадку обробки.
5) На базі розрахункового значення затискної сили Q визначається сила Wабо потужність силового приводу пристосування (пневматичного, гідравлічного, пневмогідравлічного, електричного та ін.) з урахуванням передатного відношення та проміжних ланок, що передають зусилля від приводу до затискуючих елементів, а також коефіцієнта корисної дії ŋ приводу і кінематичного ланцюга пристосування
де і – передаточне відношення
У пневматичних циліндрів величина ŋ залежить від діаметра циліндра D, при D=150-200 мм - ŋ = 0,90-0,95. При менших значеннях D відносна величина витрат на тертя манжетів об стінки циліндру зростає і ŋ знижується. Всередньому для пневмоциліндрів величину ŋрекомендовано брати в межах 0,85-0,90, для пневмогідравлічних приводів - 0,80-0,85. Для практичних розрахунків ККД рейково-шестерних механізмів для кожної пари передаючих ланок при кутах зачеплення а a=20°рекомендується прийматиŋ= 0,9.
6) У відповідності з необхідною силою W або потужністю силового приводу розраховують його геометричні і інші параметри; округлюють їх до найближчих більших стандартних значень. Потім обирають стандартні інормалізовані типорозміри конструкції приводів (або елементів).
Ефективність затиску в значній мірі залежить від напряму і місця додатку сили. При виборі її напряму необхідно враховувати приведені нижче правила.
1 Сила затиску повинна бути направлена перпендикулярно до площин установчих елементів, щоб забезпечити контакт з опорами базових поверхонь і виключити при затиску зрушення заготівки.
2 При базуванні заготівки по декількох базових плоских поверхнях сила затиску повинна бути направлена до того установчого елементу, з яким заготівка має найбільшу площу контакту.
Напрями сили затиску і сили тяжіння заготівки повинні співпадати (це полегшить роботу затискного пристрою).
Напрям сили затиску по можливості повинен співпадати з напрямом сили обробки.
При виборі місця додатку сил затиску слід дотримуватися приведених нижче правил.
1 Сила затиску не повинна приводити до перекидання заготівки або її зрушення по установчих елементах. Для цього необхідно, щоб точка додатку сили затиску проектувалася:
а) на установчий елемент (якомога ближче до його центру) або в трикутник, утворений лініями, що сполучають центри трьох установчих елементів, розташованих в одній площині (якомога ближче до центру або в центрі тяжкості трикутника опор);
б) на ділянку поверхні заготівки, паралельної поверхні плоских установчих елементів, що сприймають силу затиску.
2 Дія сил затиску і реакцій опор, що викликаються ними, не повинна приводити до створення згинаючих моментів, які негативно позначаються на точності обробки нежорстких заготівок.
3 Точка додатку сили затиску повинна бути якомога ближче до місця обробки, особливо для нежорстких заготівок.
Чим повніше будуть виконані перераховані правила при виборі точки додатку сили затиску, тим вище будуть ефективність затиску і точність обробки заготівки. Розрахункиздійснюються рішенням рівнянь рівноваги відносно сил затиску.
При конструюванні спеціальних пристосувань необхідно обґрунтувати економічну доцільність його виготовлення й експлуатації.
Сучасні вимоги по забезпеченню високої і стабільної якості машин, що випускаються, підвищенню продуктивності праці і зниженню собівартості в машинобудуванні визначають необхідність підвищення рівня оснащеності технологічних процесів пристосуваннями.
Прискорення темпів технічного прогресу викликає необхідність частої заміни машин, що випускаються, новими, більш зробленими. При цьому майже все спеціальне оснащення списується, проектується і виготовляється нова. Це спричиняє за собою великий об'єм трудових і грошових витрат на виробництво пристосувань, що в свою чергу відображається на термінах технологічної підготовки виробництва і собівартості вироблюваної продукції. Більше половини всіх трудових витрат в технологічній підготовці виробництва доводиться на виготовлення пристосувань і оснащення. Тому проблема скорочення циклу і витрат на підготовку виробництва стає особливо гострою. Зменшення термінів конструювання і виготовлення пристосувань, скорочення витрат на їх виробництво, застосування систем пристосувань, що дозволяють в короткий термін перебудовувати виробництво на випуск нової продукції, сприяють рішенню цієї проблеми. В умовах серійного і дрібносерійного виробництва особливо важлива наявність гнучкої переналагоджуваної високомеханізованої системи пристосувань. Ефективними методами, що прискорюютьі здешевлюють проектування і виготовлення пристосувань, є уніфікація, нормалізація і стандартизація деталей і елементів пристосувань на основі наукових досягнень і передового досвіду.
Аналіз досвіду роботи машинобудівних заводів показує, що більшість спеціальних пристосувань може бути виготовлені з нормалізованих і стандартних елементів. Пристосування про нормалізованими елементами можуть бути економічними і для дрібносерійного виробництва, а багатократне використовування нормалізованих і стандартних елементів пристосувань знижує їх собівартість і підвищує технічну оснащеність виробництва.
Під нормалізацією розуміють стандартизацію в масштабі заводу, відомства і т.д. Вищою формою нормалізації є розробка державнихстандартів — ДСТУ. Проведенню робіт по нормалізації і стандартизації пристосувань передує уніфікація.
Уніфікація— це раціональне скорочення числа типів, видів і розмірів верстатних пристосувань, деталей і заготівок одного функціонального призначення при поліпшенні їх техніко-економічних і якісних характеристик.
Нормалізація і стандартизація дає економічний ефект на всіх етапах створення і використовування пристосувань:
1. На етапі проектування. Нормалізовані і стандартні деталі і складальні одиниці не конструюють наново, і, отже, немає необхідності робити на них робочі креслення. У зв'язку з цим зменшується вартість і скорочується час проектування пристосувань.
2. На етапі виготовлення. При виготовленні різноманітних пристосувань з використанням нормалізованих і стандартних деталей і складальних одиниць збільшується число однакових деталей і складальних одиниць. Тому їх можна виготовляти не одиницями, а партіями, а також в запас, користуючись яким можна скоротити термін виготовлення пристосувань.
3. На етапі експлуатації; Ряд швидкозношуваних деталей доводиться замінювати. При використовуванні нормалізованих і стандартних елементів швидшає і здешевлюється ремонт пристосувань.
Коли пристосування зношене або в ньому зникла необхідність, можливе подальше використовування ще, не зношених нормалізованих і стандартних деталей складальних одиниць при виготовленні інших пристосувань. Таким чином, нормалізація і стандартизація дає три джерела підвищення рентабельності пристосувань: зменшення вартості; здешевлення експлуатації; повторне використовування незношених елементів. Разом з цим нормалізація і стандартизація дозволяє значно скорочувати календарні терміни виготовлення пристосувань.
Дата добавления: 2018-05-09; просмотров: 386; Мы поможем в написании вашей работы! |
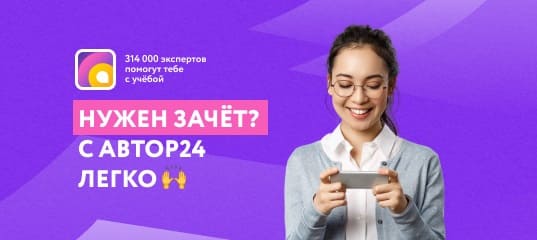
Мы поможем в написании ваших работ!