Расчет режимов резания и назначения режимов резания
Переход 2
Скорость резания определяется по формуле:
, (2.4)
где T – стойкость инструмента, T= 60 мин;
CV – коэффициент, учитывающий режим работы, CV =328;
x, m, y – показатели степени; x=0,12; y=0, 5; m=0,28.
, (2.5)
где KuV – учитывает инструмент;
KnV – учитывает глубину резания;
KmV – учитывает материал заготовки.
Частота вращения определяется по формуле:
(2.6)
Принимаем = 800 об/мин, тогда скорость резания:
где d – диаметр заготовки.
Сила резания определяется по формуле:
Рz =10∙cр ∙tx ∙sy ∙vn ∙Kp (2.7)
Рz =10∙40 ∙1 ∙0,40,75 ∙148,7 ∙1,5 = 300 Н
Мощность резания определяется по формуле:
(2.8)
Переход 3
Скорость резания определяется по формуле:
,
где Т – стойкость инструмента;
t – глубина резания, мм;
S – подача, мм/об.
Частота вращения определяется по формуле:
Принимаем = 800 об/мин, тогда скорость резания:
Сила резания определяется по формуле:
Рz =10∙cр ∙tx ∙sy ∙vn ∙Kp
|
|
Рz =10∙40 ∙1 ∙0,40,75 ∙148,7 ∙1,5 = 300 Н
Мощность резания определяется по формуле:
Переход 4
Скорость резания определяется по формуле:
,
где Т – стойкость инструмента;
t – глубина резания, мм;
S – подача, мм/об.
Частота вращения определяется по формуле:
Принимаем = 800 об/мин, тогда скорость резания:
Сила резания определяется по формуле:
Рz =10∙40 ∙1 ∙109,3 ∙1,5 = 210 Н
Мощность резания определяется по формуле:
Переход 5
Скорость резания определяется по формуле:
,
где Т – стойкость инструмента;
t – глубина резания, мм;
S – подача, мм/об.
Частота вращения определяется по формуле:
Принимаем = 800 об/мин, тогда скорость резания:
Сила резания определяется по формуле:
Рz =10∙40 ∙1 ∙0,40,75 ∙148,7 ∙1,5 = 300 Н
Мощность резания определяется по формуле:
Определение норм времени на операцию
Основное время по переходам определяем по формулам, вспомогательное и подготовительно-заключительное время определим по нормативам, время на обслуживание рабочего места и отдых определяем в процентах от оперативного времени.
|
|
Штучно-калькуляционное время мех. обработки определяем по формуле:
Тшт.к. = Топ + Т обсл + Тотд (2.9)
Основное время для точения, сверления, зенкерования и развертыва-ния определяем по формуле:
(2.10)
где l - длина обрабатываемой поверхности;
l1- величина врезания инструмента;
l2 - величина перебега инструмента;
S0 - подача;
n - частота вращения шпинделя.
Основное время для нарезания резьбы:
Общее основное время обработки Т0= 3,52 мин
Тшт.к. =3,52 + 0,598 + 0,123 +0,164 = 4,4 мин
Организация тех. процесса на участке мех. обработки
Определим потребное количество оборудования на участке по формуле:
, (2.11)
где Фд.о. - действительный годовой фонд времени работы оборудования;
К3 - коэффициент загрузки станка.
|
|
Принимаем один станок 16К20 на участке механической обработки.
Определим количество основных рабочих по формуле:
(2.12)
где Фд.р.- действительный годовой фонд времени рабочего;
Кмн - коэффициент многостаночного обслуживания, Кмн=1-3;
Кв - коэффициент выполнения норм, Кв =1,3.
Принимаем одного токаря.
Составим планировку рабочего места токаря, рисунок 2.3.
Рисунок 2.2 - Планировка рабочего места токаря
1 - станок 16К20;
2 - тара с заготовками;
3 - тара с обработанными деталями.
Cписок используемой литературы.
1. Тамаркин М.А., Прокопец Г.А и др. Методическое руководство по проектированию маршрутных технологических процессов механической обработки, 2001.
2. Г.А. Прокопец, Азарова А.И. и др. Справочные материалы для выполения курсовых и дипломных проектов, 2006.
3. Общетехнический справочник. / Под ред. Е.А. Скороходова. М.: Машиностроение, 1990.
4. Ю.М. Лахтин. Основы металловедения. М.: Металлургия, 1998.
5. Прокопец Г.А., Тищенко Э.Э. и др. Технологическая подготовка и технология производства машин. Учебное пособие, 2008.
|
|
6. Справочник технолога-машиностроителя. / Под ред. А.Г. Косиловой, Р.К. Мещерякова. Т1. М.: Машиностроение, 1995.
7. Справочник технолога-машиностроителя. / Под ред. А.Г. Косиловой, Р.К. Мещерякова. Т2. М.: Машиностроение, 1995.
8. Прокопец Г.А., Тищенко Э.Э. Проектирование технологических процессов в курсовых проектах. Учебное пособие, 2009.
9. Общемашиностроительные нормативы времени и режимов резания для нормирования работ, выполняемых на универсальных и многоцелевых станках с числовым программным управлением. Ч. 1. Нормативы времени. М.: Экономика, 1990.
10. Н.А. Силантьева, В.Р. Малиновский. Техническое нормирование труда в машиностроении, М.: Машиностроение, 1990.
Дата добавления: 2018-05-02; просмотров: 257; Мы поможем в написании вашей работы! |
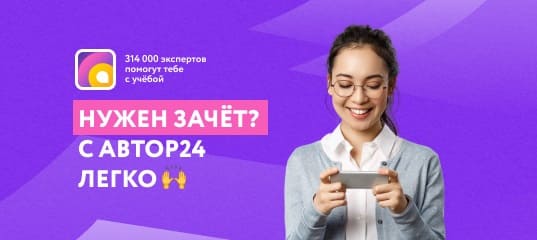
Мы поможем в написании ваших работ!