Оборудование, приспособления и инструмент применяемый при разборке
1 Пружинные кольца, которыми замыкаются подшипники качения в корпусах или валах, удобно снимать, разжимая или сжимая с помощью специального инструмента - щипцов. Закругленные губки щипцов вводят в отверстия в пружинных кольцах.
2 Шплинты удаляют шплинтодером или срубают головку зубилом, а тело шплинта извлекают плоскогубцами или выталкивают выколотками.
3 Штифты с резьбовым концом удаляют навертыванием гайки на резьбовую часть. Штифты установленные в сквозных отверстиях, выбивают с помощью выколотки или изготавливают специальные съемники.
4 Клиновые шпонки извлекают ударами со стороны ее меньшего сечения, или с помощью рычажного приспособления нажимом на головку или специальным инструментом. Призматические шпонки удаляют выполняя резьбовое отверстие и ввертывают винт, когда винт упрется в вал, его продолжают вращать и шпонка выходит из паза.
5 Маховики, шкивы, муфты и другие подобные детали снимают с помощью ручных (двухлапых или трехлапых ) съемников
6 При демонтаже подшипников качения их гнезда и шейки валов следует беречь от повреждений. Демонтаж подшипников целесообразней осуществлять с помощью прессов с использованием соответствующих наставок, винтовых приспособлений, обеспечивающих равномерное смещение подшипника. При этом усилие прилагают только к тугопосаженному кольцу. При демонтаже нельзя наносить удары по кольцам, использовать зубила, выколотки. Для этого следует применять специальные съемники (трехлапые или хомуты, которые осуществляют равномерный нажим на кольцо или роль хомута выполняет деталь расположенная непосредственно за подшипником).
|
|
. Если подшипник запрессован на вал с большим натягом, для облегчения съёма детали можно подогревать охватывающую деталь нагретым маслом при температуре 90-1000С. Производят эту операцию так: устанавливают съемник, создают натяг, изолируют вал асбестом или картоном в местах его примыкания к подшипнику, для облегчения снятия подшипника на него поливают минеральное масло.
Вопрос17Очистка и промывка деталей
Детали, сдаваемые на восстановление, очищают от загрязнений до такого состояния, чтобы их можно было осмотреть и выявить дефекты.
При разборке ремонтируемого оборудования необходимо все детали очистить от плёнок окислов, масла и грязи. Эта операция является весьма ответственной, т.к. цель её не только придать деталям опрятный вид, а главным образом выявить наличие износа и определить степень её годности для дальнейшей эксплуатации.
При очистке и промывке деталей особое внимание следует обратить на правильность выбора промывочного раствора, т.к. отдельные компоненты этого раствора (щёлочи, кислоты) могут войти в реакцию с металлом и ещё более ухудшить рабочую поверхность. Особенно осторожно нужно применять растворы для промывки деталей из цветных металлов, в частности алюминиевых, цинковых и медных сплавов.
|
|
Способы очистки деталей:
![]() |
Рисунок 3.4.5 – Способы очистки изделий, сборочных единиц и деталей при подготовке их к ремонту
Промывку деталей производят водными щелочными растворами и органическими растворителями. Сначала в горячем растворе, а затем в чистой горячей воде. Затем деталь тщательно высушивают.
Способы промывки деталей:
1 Ручной. В процессе разборки промывку деталей рекомендуется производить непосредственно у места разборки станка, пользуясь также передвижным промывочным устройством, обычно из ванн предварительной и окончательной промывки. Промывку ведут в двух ваннах, заполненных органическим растворителем ( керосином, бензином, дизельным топливом, хлорированными углеводородам). Первая ванна предназначена для замачивания и предварительной промывки, вторая - для окончательной промывки. Мойку ведут с использованием щеток, крючков, скребков и т.д.
|
|
2 В баках методом погружения.
Промывочный бак, который используется в условиях цеха используется следующим образом: в нижнюю часть бака заливается вода, которая не должна доходить до решётки на 10-30мм, а в верхнюю керосин. Грязь от промываемых в керосине деталей осаждается в поддоне. После многократного промывания деталей отстоявшийся керосин выливают через кран в какую-нибудь ёмкость, затем сливают воду через кран и извлекают поддон с грязью, который очищают и ставят на место. Затем в бачок наливают чистую воду, сверху заливают использованный ранее керосин. Рассмотренная конструкция позволяет использовать керосин многократно, что даёт большую его экономию.
.
Рисунок 3.18 – Промывочный бак:
1- кран для слива керосина; 2- кран для слива воды;
3- решетка; 4-керосин; 5-поддон; 6-вода.
3 В моечных машинах.
В условиях РМЦ и ремонтных заводов для мойки и очистки деталей и узлов станков применяются стационарные моющие машины.
Крупные корпусные детали укладывают непосредственно на транспортёр, а мелкие детали складываются в сетчатые ящики и подаются в моющую камеру, где горячие струи моющего раствора смывают грязь и масло, а затем в промывочную камеру под горячие струи воды, смывающие раствор, далее детали перемещаются в сушильную камеру под струи горячего воздуха. Пройдя весь процесс мойки, детали выходят из машины и чистыми и сухими.
|
|
4 Ультразвуковой. Промывку производят в специальной ванне с подогревом моющей жидкости. В ванне размещен источник ультразвуковых колебаний, создающий упругие волны высокой частоты. Детали размещаются в специальной сетчатой корзине. Сушат детали продувкой горячим воздухом или азотом.
Вопрос 18 Цель и способы проведения дефектации
Цель дефектации - выявить дефекты деталей, установить возможность ремонта или определить необходимость замены детали.
Классификация дефектов позволяет правильно выбрать технологические процессы восстановления деталей, особенно типовые; обосновать рациональную специализацию подразделений, занятых восстановлением; производить укрупненные расчеты трудовых и материальных затрат, связанных с восстановлением; планировать производство.
Дефект — каждое отдельное несоответствие продукции установленным требованиям (по ГОСТ 15467—79);
Устранимый дефект — дефект, устранение которого технически возможно и экономически целесообразно (по ГОСТ 15467—79).
В зависимости от назначения детали или от предполагаемого дефекта процесс дефектации производят различными способами.
1 Наружный осмотр используется для определения поверхностных дефектов: трещин, забоин, раковин, изгиба, значительных износов, поломок, и т.д., т.е. дефектов, обнаружение которых возможно визуально. При осмотре используют складные лупы ЛП-1, ЛАЗ и др., штативные лупы ЛШ, ЛПШ-25, ЛПШ-462, отсчетные микроскопы МИР-1М и МИР-2.
2 Проверка на ощупь. Определяется износ и смятие резьбы на деталях, легкость проворота подшипников качения и цапф вала в подшипниках скольжения, легкость перемещения шестерен по шлицам вала, наличие и относительная величина зазоров, плотность неподвижных соединений.
3 Остукивание детали молотком или рукояткой молотка позволяет обнаружить внутренние трещины, о чём свидетельствует дребезжащий звук. Этот процесс следует выполнять осторожно, чтобы не оставлять следов (вмятин) на поверхности проверяемой детали. Применяют для определения «ослабленных» посадок шеек, шипов и заклепок и контроля резьбовых сопряжений с натягом.
4 Гидравлической (пневматическое) испытание применяют для обнаружения трещин или раковин в корпусных деталях. При испытании в детали заглушаются все отверстия, кроме одного, через внутреннюю полость которого нагнетается жидкость при давлении 0,2-0,3 МПа. При наличии трещины или раковины наблюдается вытекание жидкости или запотевание стенок детали.
5 Измерения позволяют определить величину износа тех или иных поверхностей, отклонения элементов детали от правильной геометрической формы и нарушения во взаимном расположении поверхностей у детали. Выполняются измерения с помощью различных измерительных инструментов и приборов.
Для контроля линейных размеров элементов деталей применяют универсальный инструмент : штангенциркули (ГОСТ 166-89), штангензубомеры, штангенглубиномеры (ГОСТ 162-90), гладкие микрометры (ГОСТ 6507-90), индикаторные нутромеры (ГОСТ 868-82 и 9244-75) и скобы (ГОСТ 11098-75). Если деталь признается годной по линейным параметрам, то проверку продолжают для выявления годности по параметрам формы и расположению поверхностей. Отклонения от круглости измеряют кругломерами, от плоскостности - с помощью щупов или оптикомеханическими приборами. Отклонения от взаимного расположения поверхностей измеряют с помощью специальных средств, оснащенных индикаторами часового типа(ГОСТ 577-68)
6 Проверка твёрдости детали позволяет обнаружить изменения, происходящие в материалах детали в процессе эксплуатации из-за наклёпа, влияния высоких температур или агрессивных сред и т.д.
7 Магнитная и ультразвуковая дефектоскопия предназначена для обнаружения скрытых дефектов в стальных и чугунных деталях. Действие магнитного дефектоскопа основано на различной магнитной проницаемости сплошного металла и металла с трещинами. Сущность магнитного способа определения повреждений заключается в том, что магнитный поток, встречая на своем пути повреждение низкой магнитной проницаемостью по сравнению с ферромагнитным материалом, огибает его. Часть магнитного потока выходит за предел детали, образуя поле рассеяния. Поиск последнего составляет содержание способа.
Поверхностные трещины на деталях несложной формы определяют с помощью ультразвуковых дефектоскопов, использующих звуковые волны частотой 0,5... 15 МГц. При ультразвуковой дефектоскопии пороки металла выявляются при помощи ультразвуковых колебаний, которые отражаются на экране. Универсальные магнитные дефектоскопы типа М-217, УМД-9000, переносной дефектоскоп типа ПМД-77, ПМД-3М
8 Люминесцентный способ. Сущность способа заключается в свойстве некоторых веществ светиться в ультрафиолетовых лучах. Очищенные детали помещают в ванну с флюоресцирующей жидкостью на 10…15 мин. Или на поверхность детали наносят флюоресцирующий раствор пульверизатором или мягкой кистью. Через 10-15мин поверхность протирают, просушивают и наносят тонкий слой порошка впитывающего раствор из трещин или пор. Затем деталь осматривают в ультрафиолетовых лучах в затемнённом помещении. Расположение трещины определяется по свечению люминофора.
Дефектоскоп ЛЮМ-1, ЛЮМ-2, ЛДА-3, ЛД-4
9 Керосиновая проба. Предназначена для обнаружения трещин. Деталь погружают на 15-30мин в керосин, затем тщательно протирают и покрывают мелом. Выступающий из трещины керосин увлажняет мел и даёт чёткие её контуры.
В процессе дефектации детали сортируют на три группы: годные, ремонтопригодные и негодные. К годным относят детали, износ рабочих поверхностей у которых не вышел за пределы допуска на те или иные размеры, определяющие эти рабочие поверхности. У ремонтопригодных деталей износ может быть выше предельных допусков, но ремонт таких деталей экономически целесообразен. При ремонте негодные детали подлежат замене. При сортировке деталей по группам рекомендуется их помечать краской: годные - белой, ремонтопригодные - зелёной, негодные - красной.
Дата добавления: 2018-05-02; просмотров: 1784; Мы поможем в написании вашей работы! |
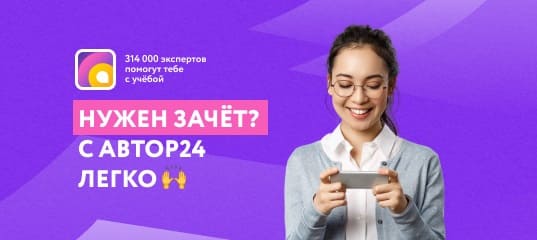
Мы поможем в написании ваших работ!