Вопрос 15 Структура технологического процесса ремонта
Технологический процесс ремонта представляет собой комплекс работ, выполняемых в определенной последовательности. Основные работы при выполнении производственного процесса ремонта оборудования представлены на схеме
Внешний осмотр и прослушивание |
![]() | ![]() | Составление предварительной дефектной ведомости |
Акт приемки | ![]() | Приемка станка в ремонт |
Транспортировка станка для ремонта |
![]() | ![]() | ![]() |
Разборка сборочных единиц на детали | Технологический процесс разборки узла |
![]() |
![]() ![]() | ![]() | ![]() | ![]() |
Технологиче-ский процесс ремонта | ![]() | ![]() |
Ремонт деталей | Новые детали |
![]() | ![]() |
Сборка сборочных единиц |
Технологический процесс сборки узла |
Испытание сборочных единиц |
![]() |
Технологический процесс сборки оборудования | ![]() | Общая сборка оборудования |
Обкатка и испытания оборудования | ![]() | Карты проверок на точность |
|
|
Акт сдачи | Сдача отремонтированного оборудования в эксплуатацию |
Для большинства деталей применяется следующая последовательность восстановления:
1 Термическая обработка (отжиг);
2 Восстановление базовых поверхностей (центровых отверстий, фасок, опорных плоскостей;
3 Правка детали;
4 Предварительная механическая обработка для придания поверхностям правильной геометрической формы
5 Наращивание поверхностей;
6 Механическая обработка;
7 Термическая обработка (закалка);
8 Окончательная отделочная обработка;
9 Контроль.
Пункты 1,3,5,7 не являются обязательными и выполняются при необходимости.
Вопрос 16 Правила разборки оборудования
Успешное выполнение ремонта станка в значительной степени зависит от того, как была осуществлена разборка.
Перед разборкой поступающей в ремонт машины ее осматривают и фиксируют дефекты выявленные в процессе эксплуатации. Перед разборкой оборудование проверяют на точность и проверяют характер нарушения основных координат.
Первоначальная разборка станка производится нерасчленёнными узлами, каждый из которых в дальнейшем разбирается на детали. Необходимость разборки узлов определяется видом и задачами ремонта.
|
|
Разборка металлорежущего станка или другого вида оборудования должна производится с соблюдением следующих правил:
- следует разбирать только ту сборочную единицу, которая подлежит ремонту. Следует помнить, что разборка механизма ведёт к нарушению плотности соединений. Полная разборка станка производится только при капитальном ремонте.
- перед разборкой станка ознакомиться с техническим паспортом, кинематической и гидравлической схемами, составить схему-график разборки-сборки, т.е. ознакомиться с его устройством, назначением и взаимодействием сборочных единиц и деталей. Если это трудно сделать во время его обследования, необходимо ознакомиться с прилагаемыми инструкциями и чертежами и только после этого приступить к его разборке. А перед по детальной разборкой той или иной сборочной единицы следует хорошо изучить её внутреннее устройство и способы крепления отдельных деталей, установить порядок и способы разборки.
- при отсутствии кинематической и гидравлической схем их нужно составить в процессе разборки ремонтируемой сборочной единицы.
- произвести дефектацию деталей и составить дефектную ведомость.
|
|
- разборку станка и сборочных единиц начинать со снятия предохранительных щитков, кожухов и крышек. В первую очередь снимают узлы препятствующие снятию других узлов.
- разборку узла производить инструментами и приспособлениями, исключающими повреждение годных деталей Для снятия с валов шкивов, зубчатых колёс, муфт, подшипников пользуются прессами, съёмниками или винтовыми приспособлениями. При применении молотков ударять по деталям следует через подставки или выколотки из дерева или мягкого металла.
- при разборке деталей нельзя допускать их перекосов, заклинивания и повреждений.
- нельзя прилагать больших усилий к трудно снимаемым деталям: необходимо выяснить причину заедания и устранить её.
- детали каждого разбираемого узла необходимо укладывать в отдельные ящики и нумеровать. Для выдерживания взаимного расположения деталей ставят метки так, чтобы зафиксировать нужное положение. Существуют следующие методы метки деталей: стальным клеймом, электрографом, кислотным клеймом и краской.
Клеймить незакаленную деталь можно, если клеймение не нарушает рабочей поверхности и не деформирует деталь. Краской метку можно наносить и на рабочую поверхность детали. Эту метку снимают при сборке. В гидравлических и пневматических механизмах должны маркироваться все трубопроводы и места их подсоединения. Ящики с деталями обязательно закрывают крышками.
|
|
- крупные детали укладывают на подставки возле ремонтируемого станка.
- при отворачивании гаек и винтов нужно применять ключи соответствующих размеров и форм. Отвёртки для вывинчивания винтов должны соответствовать размеру шлица и головки винта. Шпильки должны выворачиваться специальными шпильковёртами.
- при частичной разборке узла рекомендуется после снятия соответствующих деталей заворачивать крепёжные детали в их отверстия.
Дата добавления: 2018-05-02; просмотров: 771; Мы поможем в написании вашей работы! |
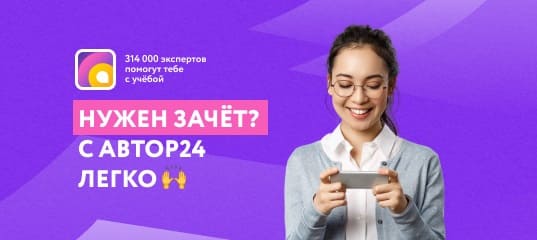
Мы поможем в написании ваших работ!