Методы достижения точности замыкающего звена. Метод полной взаимозаменяемости. Метод неполной взаимозаменяемости.
Пять методов: полной, неполной, групповой взаимозаменяемости, пригонки или регулирования.
Метод полной взаимозаменяемости
Сущность метода заключается в том, что требуемая точность замыкающего звена размерной цепи достигается во всех случаях ее реализации путем включения в нее составляющих звеньев без выбора, подбора или изменения их значений.
Сборка изделий при использовании метода полной взаимозаменяемости сводится к механическому соединению взаимозаменяемых деталей. При этом у 100 % собираемых объектов автоматически обеспечивается требуемая точность замыкающих звеньев размерных цепей.(Н-р: взаимозаменяемые детали и узлы автомобилей, телевизоров, холодильников, взаимозаменяемые шарико- и роликоподшипники, крепежные детали).
Преимущества метода:
- относительная простота достижения требуемой точности замыкающего звена, так как формирование размерной цепи сводится практически к простому соединению ее составляющих звеньев;
- возможность широкого кооперирования различных цехов и заводов при изготовлении отдельных деталей или сборочных единиц машин;
- возможность выполнения технологических процессов изготовления деталей и особенно сборки машин рабочими невысокой квалификации;
- простота нормирования технологических процессов во времени.
Метод неполной взаимозаменяемости
Сущность метода заключается в том, что требуемая точность замыкающего звена размерной цепи достигается с некоторым, заранее обусловленным риском путем включения в нее составляющих звеньев без выбора, подбора или изменения их значений.
|
|
Преднамеренный риск выхода значений замыкающего звена за пределы допуска, определяемого условиями задачи, обычно незначителен. Однако этот риск позволяет расширить допуски составляющих звеньев в сравнении с их значениями, установленными при достижении точности замыкающего звена методом полной взаимозаменяемости. Эта возможность создается малой вероятностью возникновения крайних отклонений составляющих звеньев и попаданий таких отклонений в одно изделие.
Методы достижения точности замыкающего звена. Метод групповой взаимозаменяемости. Метод пригонки. Метод регулирования.
Пять методов: полной, неполной, групповой взаимозаменяемости, пригонки или регулирования.
Метод групповой взаимозаменяемости
Сущность метода заключается в том, что требуемая точность замыкающего звена размерной цепи достигается путем включения в размерную цепь составляющих звеньев, принадлежащих к одной из групп, на которые они предварительно рассортированы.
Экономично использовать метод групповой взаимозаменяемости для малозвенных размерных цепей, к точности замыкающих звеньев которых предъявляются высокие требования.
|
|
Метод пригонки
Сущность метода пригонки заключается в том, что требуемая точность замыкающего звена размерной цепи достигается изменением размера компенсирующего звена путем удаления с него определенного слоя материала.
Основным преимуществом метода пригонки является возможность изготовления деталей с экономичными допусками. Методом пригонки может быть обеспечена высокая точность замыкающего звена. Однако пригоночные работы в основном выполняются вручную и требуют высококвалифицированных рабочих.
Метод регулирования
Сущность метода заключается в том, что требуемая точность замыкающего звена размерной цепи достигается изменением размера компенсирующего звена без удаления материала с компенсатора.
Преимущества метода регулирования особо ощутимы в многозвенных размерных цепях. Введение в конструкцию машин и механизмов компенсаторов облегчает обеспечение точности замыкающих звеньев не только в процессе изготовления, но и в процессе эксплуатации машин, что положительно отражается на их экономичности.
|
|
Настройка технологической системы.
Настройка технологической системы– процесс установления требуемой точности относительного движения и положения исполнительных поверхностей оборудования, приспособления и инструмента, с целью получения требуемой точности обрабатываемых поверхностей.
Статическая настройка технологической системы – первоначальное предание требуемого положения режущего инструмента относительно исполнительных поверхностей станка.
Для настройки технологической системы необходимо знать рабочий настроечный размер (АР). При этом необходимо различать обработку одной детали или партии деталей.
Настройка технологической системы по методу пробных деталей.методов настройки по пробным деталям.
1.Настройка с помощью универсальных измерительных средств.
2.Настройка по жестким предельным калибрам.
3.Настройка по суженным предельным калибрам.
4.Настройка по наблюдению за знаками отклонений..
Необходимость поднастройки возникает из-за того, что под воздействием систематических факторов точность первоначальной настройки теряется и возможно появление брака.
Поднастройка – восстановление требуемого положения режущей кромки инструмента относительно системы координат станка.
Дата добавления: 2018-05-02; просмотров: 545; Мы поможем в написании вашей работы! |
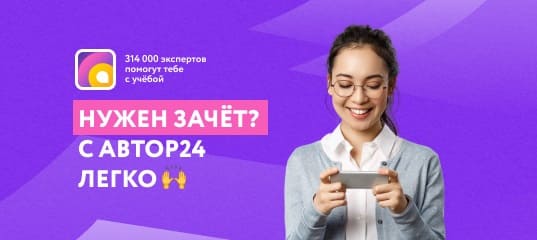
Мы поможем в написании ваших работ!