Газотермическое плазменное напыление
Плазменное напыление - это процесс получения покрытий заготовок, заключающийся в нагреве материала выше температуры плавления и распылении его с помощью газовой струи на подложку.
При высокотемпературном нагреве, осуществляемом тем или иным способом, напыляемое вещество плавится, а газовая струя распыляет расплавленный материал и направляет его с большой скоростью на поверхность изделия. При соударении расплавленных частиц с покрываемой поверхностью и между собой на поверхности образуется слой покрытия, толщина которого, а также плотность и прочность сцепления с основой определяются технологическим режимом процесса напыления и природой материалов покрытия и основы.
Важная особенность нанесения покрытий газотермическим напылением заключается в том, что покрытия можно наносить без существенного повышения температуры изделия и других процессов физико-химического взаимодействия покрытия с покрываемой поверхностью. Прочность сцепления покрытия с основой определяется тремя видами связи: механическим сцеплением частиц металла (в случае металлизации) с шероховатой поверхностью, силами адгезии и химическим взаимодействием и микросваркой в очень тонком поверхностном слое основы.
Весь процесс можно подразделить на три непрерывные основные стадии: распыление исходного материала; образова-
254
3. ТЕХНОЛОГИЯ ИЗГОТОВЛЕНИЯ КОНСТРУКЦИЙ ИЗ МКМ И УУКМ
|
|
ние направленного потока распыляемых частиц; образование слоя напыленного материала в результате кристаллизации рас-
пыляемых частиц на подложке.
Схема плазменного напыления показана на рис. 3.14. В плазменном распылителе, состоящем из водоохлаждаемых катодного (вольфрамовый катод) и анодного (медное сопло) узлов, с помощью источника постоянного тока возбуждается электрическая дуга, которая стабилизируется стенками канала сопла и плазмообразующим газом, поступающим от системы газоснабжения. Управление расходом рабочего газа и мощностью дуги осуществляется с помощью пульта управления. В высокотемпературную плазменную струю, истекающую из сопла распылителя, подается распыляемый материал в виде порошка, стержня или проволоки, в соответствии с чем и различаются виды напыления. Причем в случае напыления проволокой последняя может служить анодом, замыкая на себе дугу, при этом существенно увеличиваются производительность и коэффициент осаждения материала.
Рис. 3.14.Схема плазменного напыления:
а — расплавление исходного материала; б — формирование направленного потока распыляемых частиц; в — формирование слоя напыленного материала; / — источник питания; 2 — плазменный распылитель; 3 - пульт управления; 4 — система подачи распыляемого материала; 5 — система газоснабжения; 6 — система водоснабжения
|
|
255
3.3. Газофазные методы изготовления деталей
В качестве плазмообразующих газов применяют азот, аргон, гелий, водород и их смеси. Нейтральные газы способствуют предотвращению окисления напыляемых материалов. Плазменное напыление порошковыми материалами, на транспортировку которых расходуется около 10 % газа, предпочтительнее, так как позволяет в более широких пределах варьировать свойства образующихся покрытий за счет динамических харак- теристик процесса и использовать механические смеси порош-ков различного состава.
Принципиальные схемы устройства головок плазменных горелок показаны на рис. 3.15. В головке (представленной на рис. 3.15, а) напыляемый порошок вводится в дуговую плазму, образуемую между вольфрамовым электродом (катодом) и соплом (анодом). В головке, представленной на рис. 3.15, б, сопло остается электрически нейтральным, а дуговой разряд возни-; кает между вольфрамовым электродом горелки и напыляемой проволокой, которая является расходуемым анодом.
Рис. 3.15.Схема устройства головок плазменных горелок для нанесения покрытий из порошков (а) и проволоки (б):
|
|
/ — медное сопло; 2 — изолирующее кольцо; 3 — ввод плазмообразующего газа; 4 — вольфрамовый электрод (катод); 5 - прижимной контакт; 6 — проволока из напыляемого металла (анод); 7— направляющая труба
В отечественной практике обычно используют серийно выпускаемые аппараты УПУ-ЗМ (напыление из проволоки и порошка) и УМП-5 (напыление из порошка).
Принципиальная технологическая схема изготовления волокнистых КМ с использованием метода плазменного напы-
3. ТЕХНОЛОГИЯ ИЗГОТОВЛЕНИЯ КОНСТРУКЦИЙ ИЗ МКМ И УУКМ
ления матрицы состоит из следующих операций: укладки волокон, например, на металлическую фольгу; плазменного напыления тонкого слоя материала, служащего матрицей; разрезки монослойного (или многослойного) полуфабриката и укладки в форму для прессования; диффузионной сварки под давлением, приводящей к образованию плотного материала.
В процессе плазменного напыления очень важно обеспечить достаточно хорошую связь между напыленным слоем и тиюкнами, а также между напыленным слоем и фольгой. Хорошая связь между этими тремя составляющими КМ значительно облегчает операции раскроя и укладки, предотвращает отрыв и поломку волокон. Прочность связи покрытия с волокнами и фольгой, так же как и качество покрытия, его пористость, содержание примесей, определяют следующие основные технологические параметры: состояние поверхности подокон и фольги (чистота, шероховатость); рабочая среда (воздух, аргон, водород, азот); температура напыляемой поверхности (подложки); расстояние от дуги до напыляемой поверхности; напряжение и плотность тока дуги; расход плазмообра-зующего газа; скорость подачи напыляемого материала (порошка и проволоки); размер частиц напыляемого порошка; скорость перемещения факела относительно напыляемой поверхности.
|
|
При напылении на поверхность алюминиевой или титановой фольги последнюю подвергают обезжириванию и осветляющей химической обработке для полного или частичного растворения слоя оксидов, неизменно присутствующих па поверхности фольги. В некоторых случаях для лучшего растворения оксидной пленки целесообразно предварительно подвергнуть поверхность фольги пескоструйной обработке или механической чистке металлической щеткой; такая обработка приводит к механическому разрушению оксидной пленки и облегчает процесс химического растворения ее. Следует отметить, что удаление оксидной пленки с поверхности фольги не только повышает прочность связи ее с напыляемым слоем, но и значительно облегчает последующий процесс диффузионной сварки.
256
17-243
257
3.3. Газофазные методы изготовления деталей
Оксидную пленку следует удалять перед напылением, так как длительное хранение очищенной фольги приводит к образованию нового оксидного слоя.
Технологический процесс плазменного напыления (рис. 3.16) позволяет не только наносить различные покрытия,
Рис. 3.16.Схема построения технологического процесса
3. ТЕХНОЛОГИЯ ИЗГОТОВЛЕНИЯ КОНСТРУКЦИЙ ИЗ МКМ И УУКМ
по и изготавливать изделия, состоящие из одного или нескольких напыленных материалов и сплавов. При этом напыление осуществляют на специально изготовленные формы или моде-пи, называемые оправками, которые придают напыляемым материалам заданную конфигурацию и размеры. После напыления изделие извлекают из формы или снимают с оправки (либо последнюю уничтожают). Учитывая специфические особенности и свойства напыленных материалов, изделия можно конструктивно упрочнить цельнометаллическим каркасом, арматурой и др.
Осаждение из газовой фазы
В последние годы все большее распространение в различных областях современной техники получил метод осаждения металлических и неметаллических материалов из газовой фазы, сопровождающийся химической реакцией. Несмотря на то, что метод был известен еще в конце XIX столетия, лишь недавно его начали применять для получения защитных покрытий и формообразования изделий из МКМ.
Общим для всех разновидностей метода является то, что к нагретой поверхности поступают пары легколетучего соединения металла и в результате химической реакции на покрываемой поверхности образуется покрытие заданного состава. Остальные продукты реакции находятся в газообразном состоянии и удаляются из реакционной системы.
В зависимости от рабочего давления в системе различают установки для осаждения материалов при атмосферном и пониженном давлении. Установки первого типа несколько проще как в аппаратурном оформлении, так и в эксплуатации, в частности для них не так важно требование полной герметичности. К их преимуществам следует отнести возможность достижения больших скоростей осаждения металла, что обеспечивает высокую производительность процесса.
Преимуществом установок, работающих при пониженном давлении, является качество получаемых металлов с достаточно высоким сцеплением с подложкой.
Установки для осаждения металлов из газовой фазы при атмосферном давлении в системе состоят обычно из реакционной камеры, где происходит осаждение металла в результате
258
17*
259
3.3. Газофазные методы изготовления деталей
протекания реакции на горячей поверхности, устройства для нагрева подложки и регистрации ее температуры, системы очистки газоносителя, измерителей скорости потока - расходомеров (водорода, гелия, аргона), испарителей металлосодер-жащего соединения и приборов для измерения упругости паров в реакционной камере (рис. 3.17).
Рис. 3.17.Схема процесса осаждения из газовой фазы: / - смеситель реакционной камеры; 2 - нагреватели подложки; 3 - нагреватели камеры; 4 - вакуумный насос; 5 - осадительная печь; 6 - емкость-поглотитель; 7 - факел продуктов сгорания; 8 - фильтры исходных продуктов; 9 - реакционная камера
Реакционная камера (реактор) представляет собой один из основных узлов установок для газофазного осаждения. Для изготовления камеры используют специальные материалы, не существенно взаимодействующие с газовыми средами, как пра-
260
3. ТЕХНОЛОГИЯ ИЗГОТОВЛЕНИЯ КОНСТРУКЦИЙ ИЗ МКМ И УУКМ
вило, стекло, медь, нержавеющую сталь. Преимуществом стеклянных установок является возможность визуального наблюдения процессов. Для предотвращения опасности конденсации паров металлосодержащих соединений на холодных частях реакционных камер, часто предусматривают термостатирование стенок реактора, которое позволяет поддерживать заданную температуру (180...200 °С) в течение всего эксперимента. Для электрической и тепловой изоляции используют асбест, асбоцемент, оксиды алюминия, пенопласт. Вакуумные уплотнения Изготавливают из тефлона, меди, алюминия. Установки имеют откалиброванные диафрагмы для регулирования скорости откачки газов.
Равнотолщинность слоя осаждаемого металла по длине изделия обеспечивается оптимальной скоростью потока парога-зовой смеси. Кроме того, на толщину покрытия и эффективность процесса существенно влияют способ нагрева детали, а также его геометрическое расположение в камере.
В процессах осаждения из газовой фазы применяют в основном три способа нагрева: индукционный, прямым пропусканием тока и с помощью инфракрасного излучения. При этом очень важно обеспечить равномерный нагрев детали и предотвратить появление значительных перепадов температуры.
В реакторе происходит термодинамическая реакция
WF6 + ЗН2 -> W + 6 HF
или
WC16 + ЗН2 -> W + 6НС1,
при этом оптимальная температура осаждения покрытия составляет 500...700 °С и 800...1100 °С соответственно.
Максимальная скорость осаждения вольфрама W из гек-сафторида вольфрама WF6 получена при температуре 550 °С и парциальном давлении 0,1 атм и составляет 6 мкм/мин.
Гексафторид вольфрама WF6 представляет собой белый порошок. При температуре 17 °С этот порошок превращается в жидкость, а при дальнейшем повышении он начинает испаряться.
Водород Н2 и гексафторид вольфрама WF6 нагревают отдельно до температуры порядка 170 °С и смешивают только
261
3.3. Газофазные методы изготовления деталей
перед подачей в реакционную камеру. Водород проходит сис тему фильтров, освобождаясь от примесей воды. Фильтрами служат емкости с гранулированной медью или палладиевые сушители. Через реакционную камеру чаще всего эта смесь проходит прямотоком со скоростью потока от 0,3 до 2 м/с. При этом вначале температура подложки должна быть несколь ко выше температуры газа, а затем она снижается, но не ниже температуры газа. В случае равенства температур или, что еще хуже, если температура газа будет выше температуры подложки, произойдет интенсивное осаждение вольфрама или выпадение порошка в реакционную камеру. Вакуумные насосы для откачки газа из камеры применять сложно ввиду присутствия фтора F в газе.
После прохождения реакционной камеры газы попадают в печь с температурой 1000 °С, где WF6 выпадает в осадок в вши-порошка, а непрореагировавшие продукты, в том числе фторид HF, поступают в емкость-поглотитель, которая представ ляет собой цилиндр с размещенными в нем полочками, расположенными лабиринтом. На этих полочках насыпан карбонат кальция СаС03, который, реагируя с HF, образует плави ковый шпат CaF2 (минерал) и углекислый газ С02- Плавиковый шпат — вещество безвредное и даже полезное. В промышленном производстве можно было бы использовать и плавиковую кислоту HF, но в условиях опытного производства это достаточно сложно и дорого.
Вместо печи, с температурой / = 1000 °С для осаждения WF6 можно использовать ловушки с жидким азотом N2, в которых при температуре / = —87 °С WF6 выпадает в виде кристаллов. В процессе осаждения те места, на которые не должен осаждаться металл, закрывают графитовыми кольцами с особой геометрией (с острыми углами). После окончания процесса осаждения поверхность трубы обтягивается до нужной толщины, при этом графитовое кольцо срезается также механическим путем.
Выходящая из реактора смесь продуктов разложения, обычно содержащая соляную и плавиковую кислоты, является очень агрессивной и токсичной. Утечка этих веществ в атмосферу не допустима, а проникновение смеси в вакуумные насосы резко снижает продолжительность работы насосов.
3. ТЕХНОЛОГИЯ ИЗГОТОВЛЕНИЯ КОНСТРУКЦИЙ ИЗ МКМ И УУКМ
Обычно с целью предотвращения нежелательных явлений № пользуют щелочные ловушки, противоточные водяные газоуловители с системой снижения излишка водорода на выходе.
Процессы осаждения из газовой фазы имеют большое число параметров, оказывающих влияние на характеристики получаемых покрытий, — температура подложки, температура испарения металлосодержащего соединения, скорость газового потока, общее давление в реакционной камере, скорость откачки. Измерение высокой температуры (свыше 1000 °С) целесообразно проводить пирометрами через специальные окна из молибденового стекла. В области средней температуры (до 1000 °С) измерения осуществляют с помощью термопар. Для измерения скорости газовых потоков используют реометры. Общее давление в камере измеряют с помощью манометров, мановакуумметров и вакуумметров.
Осаждение из газовой фазы широко применяют для различных целей — для защиты сопел, камер сгорания ЖРД (диаметром до 50 см), тиглей, блоков и сердечников, лопаток турбин, микротермопар, трубопроводов насосов, деталей реакторов и т.д.
Кроме того, этот способ позволяет получать тугоплавкие материалы и сплавы с плотностью, близкой к теоретической, а также изделия сложной формы из этих материалов, например молибденовые и вольфрамовые трубы, носовые конуса ракет и
др.
Методом осаждения из газовой фазы можно изготавливать материалы с уникальными свойствами, например пиролитичес-кий графит, т.е. материалы, получаемые термическим разложением углеводородов. В зависимости от условий осаждения можно регулировать анизотропию свойств осажденного слоя. Например, носовые конуса ракет, полученные таким способом, обладают термической проводимостью вдоль поверхности, почти в 100 раз превышающей проводимость в перпендикулярном направлении.
Известно, что осаждением из газовой фазы получен алюминий чистотой 99,999 %.
Качественно новым направлением является создание КМ из несплавляемых компонентов. Кристаллизацией из газовой фазы получены монокристальные усы из оксида алюминия,
262
263
3.4. Технология изготовления конструкций из УУКМ
карбида кремния, большинства металлов, графита и других материалов. Упрочнение тугоплавкими волокнами значительно улучшает физические характеристики жаростойких конструкционных материалов. Так, нитевидные кристаллы графита, корунда, железа имеют при комнатной температуре предел прочности, равный 20000, 15000 и 13000 МПа соответственно (прочность массивных образцов из этих материалов равна 0,3 и 3 МПа соответственно). Этим возможности метода не ограничиваются.
3.4. Технология изготовления конструкций из углерод-углеродных материалов
Дата добавления: 2018-05-02; просмотров: 497; Мы поможем в написании вашей работы! |
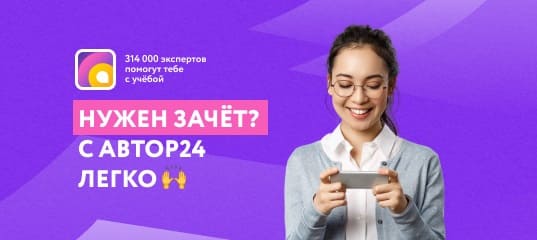
Мы поможем в написании ваших работ!