Пропитка заготовок в инертной среде
Аргон
Вследствие высокой реакционной способности большинства армирующих материалов в контакте с металлическими матрицами требуется проводить операции пропитки отформованных заранее заготовок в среде инертных газов.
Вода |
Рис. 3.2. Схема установки для пропитки: / "~ графитовый тигель; 2 ~ запорный плунжер; 3 - фильтр (графит); 4 -пробка с коллектором и питателями (графит); 5- заливочная камера (графит); 6- дно (графит); 7~ холодильник (коррозионно-стойкая сталь); 8 - заготовка из армирующего материала; 9— нагреватель (нихром); 10 -контейнер (коррозионно-стойкая сталь); // - крышка (графит); 12 -термопара |
Установка для получения КМ методом пропитки в инертной атмосфере (рис. 3.2) состоит из плавильного тигля и заливочной камеры, выполненных из графита и заключенных в контейнер. Снаружи контейнера расположен ни-хромовой нагреватель мощностью 5 кВт, изолированный от контейнера термоизоляционным цементом. Нижняя часть плавильного тигля имеет коническую форму, соответствующую форме запорного плунжера. Между плавильным тиглем и заливочной камерой установлен графитовый фильтр с отверстиями небольшого диаметра и графитовая пробка с коническим коллектором и двумя питателями. Сверху установка закрыта крышкой, а в
232
233
|
3. ТЕХНОЛОГИЯ ИЗГОТОВЛЕНИЯ КОНСТРУКЦИЙ ИЗ МКМ И УУКМ |
3.1. Жидкофазные методы изготовления деталей
|
|
нижней ее части расположен холодильник с проточной водой. Подача инертного газа — аргона — осуществляется через отверстие в запорном плунжере. Температура расплава измеряется в тигле термопарой. Установка работает следующим образом.
В заливочную камеру помещают заготовку из армирующего материала. В контейнер устанавливают графитовую пробку и плавильный тигель. В тигель, нижнее отверстие которого закрыто запорным плунжером, загружают материал матрицы. Контейнер закрывают крышкой, и через отверстие в плунжере его полость заполняется аргоном. Затем осуществляется нагрев и расплавление матричного материала, после чего плунжер поднимают вверх, и матрица, заполняя заливочную камеру, пропитывает заготовку из армирующего материала. Этим методом изготавливают детали, имеющие форму тел вращения, детали коробчатого сечения и другие.
Вакуумно-компрессионная пропитка
Особенность технологии МКМ заключается в том, что применение какого-либо одного из известных технологических процессов не позволяет получить компактный материал, обладающий требуемыми свойствами. При изготовлении таких материалов весьма часто приходится прибегать к последовательному осуществлению двух и более технологических процессов, например плазменного напыления и последующего горячего прессования, горячего прессования и последующей прокатки и т.д. К одному из таких комбинированных методов изготовления МКМ относится и вакуумно-компрессионная пропитка, сочетающая в себе элементы вакуумной пропитки и литья под давлением.
|
|
Схема одной из установок, предназначенных для получения МКМ методом вакуумно-компрессионной пропитки, показана на рис. 3.3. Установка представляет собой камеру, имеющую две зоны нагрева: зону предварительного нагрева формы с упрочнителем и зону плавления матричного металла, являющуюся одновременно и зоной пропитки. Нагрев этих зон осуществляется с помощью двух, печей сопротивления, установленных на разных уровнях по высоте снаружи камеры. Сверху камера герметично закрыта крышкой. В крышке имеется отверстие с уплотнением, в котором перемещается вверх и вниз
234
Рис.3.3. Последовательные стадии изготовления КМ методом вакуумно-ком-прессорной пропитки:
1 - намотка волокна на цилиндрическую оправку; II — установка в форму; III— предварительный нагрев; IV — пропитка; V — охлаждение; VI — разборка, удаление формы и избытка металла и извлечение трубы из КМ; / — оправка;
|
|
2 — волокно; 3 — вакуумированная форма; 4 — тонкостенное дно (0,15 мм); 5 — холодильник; 6 — печь предварительного нагрева; 7 - форма с волокном; 8 -печь для плавления металла; 9 — расплав матрицы; 10 — иглы для прокалывания дна формы; 11 — рукоятка; 12 - шток; 13 — металл, заполнивший форму
полый шток контейнера с загруженным в него упрочнителем. Контейнер представляет собой герметичную металлическую оболочку, дно которой, по сравнению со стенками, имеет меньшую толщину. На представленном здесь рисунке контей-
235
3.1. Жидкофазные методы изготовления деталей
нер имеет форму, позволяющую изготовить из КМ изделия в виде колец. Шток контейнера связан с вакуумным насосом.
Крышка камеры имеет патрубок, через который в камеру под давлением подается инертный газ. Для предотвращения нагрева уплотнения штока контейнера в крышке имеется холодильник, выполненный в виде навитой на него по спирали металлической трубки, через которую непрерывно подается вода.
Рассмотрим технологический процесс вакуумно-компрес-сионной пропитки, схема которого также показана на рис. 3.3.
Упрочняющие волокна укладывают в контейнер, внутренняя часть которого изготовлена по форме будущего изделия (на приведенной схеме изображен контейнер для получения кольца и поэтому волокно в данном случае предварительно наматывается на специальную оправку, вместе с которой загружается в контейнер). В нижнюю часть камеры, выполненную в виде тигля, помещают металл матрицы. Крышку вместе с контейнером устанавливают на камере и герметично закрепляют. Полый шток контейнера подключают к вакуумной системе, и контейнер вакуумируется. Затем контейнер устанавливают в зону предварительного нагрева, а в камеру под нужным давлением подают инертный газ. Включают печи, обогревающие зоны предварительного нагрева и плавления металла матрицы, при этом в холодильник подают воду. Когда матричный металл и волокно подогреваются до нужной температуры, контейнер опускается в расплавленный металл и его дно накалы-j вается на иглы, расположенные на дне тигля с расплавом. В результате вакуума в контейнере, а также избыточного давления газа в камере, расплавленный металл заполняет контейнер с волокном. После пропитки контейнер поднимают в холодильник, где происходит кристаллизация матричного расплава. Затем изделие извлекают из контейнера и подвергают механической обработке.
|
|
В результате подбора оптимальных температурных условий, удачной комбинации вакуума и давления, совершенствования конструкции формы можно получить плоские и кольцевые образцы для испытания при растяжении, практически не имеющие усадочных пор горячих трещин и непропитанных участков между волокнами. Путем вакуумирования каркаса волокон
I. ТЕХНОЛОГИЯ ИЗГОТОВЛЕНИЯ КОНСТРУКЦИЙ ИЗ МКМ И УУКМ
перед пропиткой устраняют в форме отверстия для прохода металла и тем самым исключают контроль за расходом металла. | связи с этим появляется возможность получать, например, кольцевые образцы намоткой волокна на твердую оправку и пропиткой расплавленным металлом, поступающим только с наружной поверхности намотанного каркаса в результате погружения оправки в расплавленный металл. Наличие избыточного давления необходимо в том случае, когда расстояния между волокнами очень малы, либо при плохой смачиваемости.
Чтобы устранить усадочную пористость, в конструкции формы делают выпоры и осуществляют подогрев ее верхней масти.
Для обеспечения качественной пропитки необходим тщательный расчет теплоемкости системы, учитывающий температуру подогрева, массу волокна, оправки или формы, объем выпоров и др. Так, например, если волокна не подогреты до необходимой температуры, то матрица затвердеет прежде, чем произойдет полная пропитка.
Дата добавления: 2018-05-02; просмотров: 690; Мы поможем в написании вашей работы! |
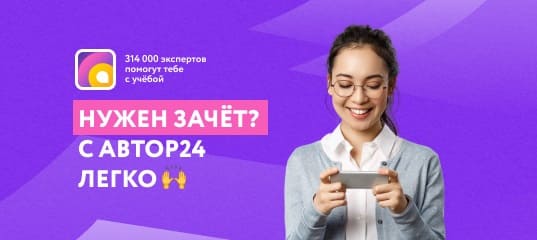
Мы поможем в написании ваших работ!