Характеристики однонаправленных композиционных материалов с алюминиевой и магниевой матрицей
|
6-243
|
|
Метод жидкофазного совмещения матрицы и волокон
Существует несколько разновидностей метода, различающихся между собой условиями пропитки армирующего наполнителя: пропитка расплавом при нормальном давлении; вакуумное всасывание; пропитка расплавом под давлением; комбинированные методы пропитки (с использованием давления и вакуума, центробежных сил и т.д.).
Условия пропитки в основном определяются реакционной способностью расплавленной матрицы и смачиваемостью волокон матрицей. Металлические матрицы, как правило, плохо смачивают керамические армирующие волокна. Увеличить способность металлов смачивать керамику удается за счет введения в расплав легирующих веществ: титана, хрома, циркония.
Пропитка волокон расплавом матрицы при нормальном давлении (его иногда называют методом непрерывного литья КМ) является наилучшим способом изготовления изделий сложной формы и полуфабрикатов в виде прутков, труб, профилей и т.д. Этот метод применим в тех случаях, когда волокна термодинамически стабильны в расплавленной матрице. Самый простой вариант этого метода заключается в укладке волокон в литейную форму и заливке в нее расплавленного металла матрицы. Перспективной и значительно более широко применяемой разновидностью метода пропитки расплавом при нормальном давлении является непрерывная пропитка пучка волокон (рис. 1.24).
|
|
Характеристики боромагниевых МКМ, полученных этим способом, представлены в табл. 1.21.
Таблица 1.21
Характеристики боромагниевых МКМ, полученные методом пропитки
Рис. 1.24. Схема процесса непрерывной пропитки жидким металлом (а) и получаемые виды изделий (б):
1 - композитный пучок; 2 — разделенные волокна; 3 — расплавленный металл; 4 — ограничители пучка волокон
Для упрочняющих волокон, склонных к окислению при нормальных условиях, необходимо применять защитную атмосферу либо вакуум при переработке их в МКМ. Методом пропитки в вакууме получают МКМ на основе алюминия и магния, упрочненные борными волокнами, на основе никелевых сплавов — упрочненные вольфрамовой проволокой, и др.
Композиционные материалы в силу метода пропитки в вакууме производят в промышленных вакуумных плавильных печках с нагревательными устройствами различного типа (индукционные, высокочастотные, электроннолучевые и др.), оснащенных устройствами для заливки форм в вакууме. Применяют для этой цели и специально сконструированные установки (рис. 1.25).
|
|
Установка представляет собой кварцевую трубу, в которой на керамической опоре размещен графитовый цилиндр. Верхняя часть этого цилиндра служит тиглем для приготовления расплава матрицы, а нижняя часть - формой для укладки упрочняющих волокон. Нижняя часть тигля сообщается с формой цилиндрическим каналом, расширяющимся вблизи верхней части формы и играющим после заливки роль прибыльной
6*
|
Рис. 1.25. Схема установки для пропитки волокон жидким металлом в вакууме: / - магнит; 2 — резиновая пробка; 3, 6 — тепловые экраны; 4 — графитовый тигель; J - графитовый шток; 7 - кварцевая труба; 8 — керамическая опора; 9 — графитовая форма; 10— волокна; // - расплав матрицы; 12 — индуктор; 13 — кварцевый колпак; 14 — стальное кольцо |
части. До заливки отверстие в дне тигля закрыто графитовой пробкой, выполненной в виде штока постоянного диаметра с утолщением в верхней части, опирающимся на стальное кольцо, через которое пропущен шток. При помощи этого кольца и постоянного магнита шток может подниматься и открывать отверстие в дне тигля. Верхняя и нижняя части кварцевой трубы заглушены резиновыми пробками. Нагрев тигля и расплавление металла осуществляются индуктором, расположенным поверх кварцевой трубы на уровне графитового тигля. Верхняя и нижняя резиновые пробки изолируются от горячего тигля специальными теплозащитными экранами.
|
|
Технологический процесс получения КМ заключается в следующем.
Форму с уложенным в ней уп-рочнителем вставляют в нижнюю часть графитового цилиндра. В тигель, отверстие в дне которого закрыто графитовым штоком, заливают металл матрицы. Систему вакуумируют, и включают нагревательные элементы. После расплавления матрицы шток поднимается при помощи магнита, и расплавленный металл заполняет форму. Для обеспечения минимального количества воздуха в установке в процессе вакуумирования ее несколько раз промывают аргоном.
Методом пропитки в вакууме получают композиты на основе алюминия и магния, упрочненные борными волокнами и нитевидными кристаллами, а также на основе никелевых сплавов, армированные вольфрамовой проволокой и др.
Значения предела прочности бороалюминиевого волокна, полученного при различных технологических параметрах методами заливки и пропитки в вакууме приведены в табл. 1.22. Очевидно, что пропитка жидким алюминием борного волокна без защитного покрытия приводит к его резкому разупрочнению даже при очень незначительном времени контакта волокна с расплавленным металлом. Об этом свидетельствуют низкие значения прочности композита.
|
|
Таблица 1.22
Характеристики бороалюминиевого композиционного материала, содержащего 60 % (об.) волокна, полученного в вакууме
Метод изготовления | Параметры технологического процесса | Предел прочности σ+1 МПа | Метод изготовления | Параметры технологического процесса | Предел прочности σ+1 МПа | ||
Т, °С | t, мин | Т, °С | t, мин | ||||
Заливка (волокна бора с покрытием) | 670 10 720 10 765 10 782 6 | 830 1020 910 750 | Пропитка | 701 4,5 770 3 860 3 | 520 440 330 | ||
Пропитку используют для получения углеалюминия. Применяют две разновидности метода пропитки: протяжку углеродного жгута через матричный расплав с последующим формованием пропитанных жгутов; принудительную пропитку каркаса из углеродных волокон, уложенных в пресс-форму. Характеристики материалов при этом получают примерно одинаковыми.
Газофазные методы осаждения— напыления
Осаждение—напыление — это газофазные, химические и электрохимические процессы получения МКМ. Главной технологической особенностью этих процессов является нанесение на волокна покрытий из матричного материала, который, заполняя межволоконное пространство, образует матрицу МКМ.
Преимущества метода осаждения—напыления: отсутствует разупрочнение волокон, поскольку волокно в процессе формообразования изделий из МКМ не подвергается воздействию
|
1.5. Металлические композиционные материалы |
|
Наполнитель | Содержание волокна v °6в, % | Прочность при растяжении σ+1, МПа | Модуль упругости при растяжении Е+1, ГПа |
16 | 1050 | 189 | |
Вольфрамовое волокно | 20 | 1190 | 175 |
диаметром 50-100 мкм | 30 | 1160 | 210 |
5.0 | 1640 | 238 | |
15 | 800 | 196 | |
Борное волокно диамет- | 23 | 840 | 210 |
ром 100 мкм | 35 | 1120 | 224 |
42 | 1310 | 224 | |
20 | 700 | 210 | |
Волокно карбида крем- | 40 | 1050 | 280 |
ния | 50 | 1300 | 315 |
|
В табл. 1.23 представлены свойства никелевых МКМ, полученных способом электролитического осаждения. |
Таблица 1.23 Характеристики никелевых МКМ |
высоких температур или значительным механическим нагрузкам; исключается возможность непосредственного нежелательного контакта волокон между собой; имеется возможность формообразования полуфабрикатов и изделий сложной геометрической формы; процесс введения матрицы может быть непрерывным, в том числе и в промышленных масштабах.
Главным недостатком процессов осаждения—напыления является трудность использования в качестве матриц сложноле-гированных сплавов.
В практике производства МКМ наибольшее применение получили методы газотермического (обычно, плазменного) напыления и электролитического осаждения. Плазменное нанесение покрытий заключается в следующем: наносимый материал матрицы в виде порошка или проволоки подводится к плазменной струе, температура которой составляет примерно 15000 К, расплавляется и подхваченный сильным потоком плазмообразующего газа (например, аргона) направляется к поверхности изделия. Двигаясь с большой скоростью (150 м/с), частицы материала при ударе о поверхность подложки (металлическая фольга) прочно соединяются с уложенными на ней определенным образом волокнами. Полученный таким образом МКМ требует дальнейшей обработки давлением или диффузионной сваркой.
Схемы получения МКМ с использованием метода плазменного напыления показаны на рис. 1.26.
Принципиальная схема изготовления МКМ электролитическим осаждением с использованием непрерывных волокон показана на рис. 1.27. Волокно перематывается с катушки на специальную металлическую оправку, служащую катодом. Оправка частично погружена в электролит и совершает вращательное движение с заданной скоростью. Анод, изготавливаемый из осаждаемого металла — матрицы, размещается на определенном расстоянии.
В результате осаждения материала анода на оправку образуется, как правило, плотный, малопористый материал, который фактически не требует дальнейшего уплотнения методами прессования, спекания, прокатки. Правда, при использовании волокон бора или металлических волокон диаметром 100 мкм и более в процессе формирования МКМ образуется пористость.
Рис. 1.26. Схемы плазменного напыления монослойных заготовок (а) и цилиндрической детали (б): / - плазмотрон; 2 — волокно; 3 — напыляемый материал
Рис. 1.27. Схема изготовления МКМ способом электролитического осаждения:
1 — источник питания; 2 — анод; 3 — шпуля с волокном; 4 — ванна с электролитом; 5 - катод-оправка
86
87
1. КОМПОЗИЦИОННЫЕ МАТЕРИАЛЫ И ИХ КОМПОНЕНТЫ
1.5. Металлические композиционные материалы
Металлические КМ можно получить также осаждением из газовой фазы, методом испарения и конденсации, катодным распылением и другими способами, которые для формирования МКМ применяются очень редко. Эти способы рассмотрены в специальной литературе.
Все чаще МКМ применяют в таких областях современной техники, где они должны работать при низких, высоких и сверхвысоких температурах, в агрессивных средах, при статических, циклических, ударных, вибрационных и других нагрузках. Наиболее эффективно применение МКМ в таких конструкциях, особые условия работы которых не допускают применения традиционных металлических материалов.
В настоящее время особое внимание уделяется бороалюми-ниевому волокну как одному из первых материалов, определяющих возможность применения МКМ в авиационно-космических конструкциях.
Например, согласно зарубежным данным, применение бо-роалюминиевого волокна в планере самолета F-106A (М-2) позволило снизить его массу с 3860 до 2990 кг, т.е. на 23 %, и увеличить за счет этого на 115 % полезную нагрузку без уменьшения скорости и дальности полета.
Первый отечественный МКМ этого типа (ВКА1), разработанный в ВИАМе, был получен с помощью диффузионной сварки. Предел прочности и модуль упругости бороалюминие-вого волокна ВКА-1 при объемном содержании волокон бора 50 % с прочностью волокон 2500 МПа составляют 1100 МПа и 260 ГПа соответственно.
Бороалюминиевые волокна практически сохраняют свои высокие прочностные и упругие свойства до температур 673...773 К. Существенно расширить рабочую температуру бо-роалюминиевых материалов можно, используя волокна из бор-сика (волокна бора с нанесенным защитным покрытием карбида кремния).
Об эффективности применения МКМ в авиационной технике можно судить по их использованию в конструкции самолета ИЛ-62, обеспечивающему снижение взлетной массы самолета при сохранении летных характеристик на 17 %, увеличение дальности полета на 15 % и увеличение полезной нагрузки на 20 %.
Применение бороалюминиевых композиций эффективно в космических летательных аппаратах, узлах конструкций, подвергающихся нагреву, в герметических кабинах, для элементов жесткости панелей, кожухов, юбок ракетного двигателя, соединительных отсеков ступеней баллистических ракет.
Легкие МКМ с алюминиевой матрицей, армированной углеродными высокомодульными волокнами, хотя и обладают пределом прочности, незначительно превышающем предел прочности лучших промышленных алюминиевых сплавов, однако имеют значительно более высокий модуль упругости (140... 160 ГПа вместо 70 ГПа) при меньшей плотности (2300 ГПа вместо 2750 кг/м3). Особенно велика разница в удельной жесткости, которая для углеалюминиевой композиции в 2,5 раза выше, чем для стандартных сплавов. Углеалю-миний отличается высокой усталостной прочностью, которая находится на уровне усталостной прочности титана и легированных сталей. Он обладает также малым коэффициентом температурного расширения при изменении температуры в интервале 293...673 К. Указанные свойства дают основание конструкторам использовать материалы в опытных конструкциях таких высоконагруженных деталей, как корпус и сопловые лопатки турбин двигателей самолетов, вертолетов и ракет.
Углеродные волокна используют также в композиции с медными, свинцовыми, цинковыми матрицами в изделиях различного назначения, для которых требуется высокая износостойкость, малый коэффициент трения, высокая электропроводность, хорошая термостабильность и способность сохранять высокие прочностные и упругие свойства при нагреве. Армирование свинца углеродными волокнами дает возможность получить МКМ с пределом прочности и модулем упругости более чем в 10 раз выше, чем у неармированного свинца. Это позволяет использовать углесвинец как конструкционный материал для оборудования и аппаратуры, обладающей высокой стойкостью в агрессивных средах, способностью подавлять звуковые колебания, поглощать гамма-излучения и выполнять другие функции.
Для изготовления подшипников, работающих без смазки, успешно опробован антифрикционный МКМ на основе свин-
ца, армированного проволокой из нержавеющей стали или оловянистой бронзой.
Введение арматуры из вольфрама или молибдена в медную и серебряную матрицы позволяет получить износостойкие электрические контакты для сверхмощных высоковольтных выключателей.
Металлические композиты на основе никеля и хрома, армированные нитевидными кристаллами оксида алюминия, а также композиции, в которых матрица изготовлена из жаропрочных сплавов, а арматура — из высокопрочных тугоплавких волокон являются перспективными для изготовления жаропрочных деталей газотурбинных двигателей.
Специалистами научно-исследовательского центра NASA (США) показана эффективность применения МКМ, полученного методом электролитического осаждения для изготовления камеры высокого давления жидкостного ракетного двигателя. Высокопрочную стальную проволоку наматывали на цилиндрическую оправку с шагом, равным диаметру проволоки, после чего осаждали плотный, беспористый слой никеля. Испытания показали, что использование стальной проволоки повышает прочность цилиндра не менее чем на 50 %.
Области применения МКМ практически не ограничены. К настоящему времени работы по созданию конструкций из них вышли далеко за рамки научных исследований и в ближайшие годы следует ждать их широкого внедрения.
1.6. Углерод-углеродные композиционные материалы
Углерод-углеродные композиционные материалы представляют собой углеродосодержащую или графитовую матрицу, армированную углеродным либо графитовым волокном. Эти матрицы обладают как свойствами монолитного графита, так и свойствами волокнистых КМ.
Основные преимущества УУКМ состоят в высокой теплостойкости, малой плотности, стойкости к тепловому удару и облучению. Эти материалы обладают высокими прочностными и жесткостными характеристиками при обычной и повышенной температурах, низким КЛТР и рядом других ценных свойств. УУКМ длительно работоспособны при температурах
до 773 К в окислительной среде и до 3273 К — в инертной среде и вакууме. При этом их прочность с ростом температуры повышается в 1,5 — 2 раза. Тем не менее применение графитов ограничено их прочностными свойствами и, прежде всего, термопрочностью, т.е. способностью материала сопротивляться температурным напряжениям, обусловленным неравномерным прогревом конструкции.
Современные конструкции могут подвергаться значительным перепадам температур, достигающим 1000 К/см. В этих случаях оказываются вне конкуренции УУКМ. От графитов ими унаследована углеродная матрица, обладающая высокой термостойкостью, при этом армирующий каркас из углеродных волокон позволяет в несколько раз увеличить прочность композита по сравнению с графитами. Причем углеродные волокна в этих материалах действуют не только как подкрепляющий набор, но и как механизм, препятствующий распространению трещин.
История применения УУКМ насчитывает около десяти лет. За это время разработан широкий спектр этих материалов, которые предназначались, в основном, для эрозионной защиты конструкций ракетно-космической техники. Современные УУКМ, обладающие высокой термостойкостью и высокими механическими характеристиками (прочность на растяжение материала в зависимости от структуры армирования изменяется от 100 до 1000 МПа), открывают возможность для совершенствования характеристик и создания качественно новых направлений в самых разных областях.
В качестве армирующего материала наибольшее применение нашли углеграфитовые волокна, нити, жгуты и пряжа. Типовым материалом для матриц служат смолы (фенольные, фурановые, эпоксидные и др.) и каменноугольный пек — продукт крекинга угля.
В настоящее время УУКМ получают в основном тремя способами: пропиткой смолой волокнистого каркаса и карбонизацией; осаждением углерода из газовой фазы между волокнами каркаса; сочетанием пропитки смолой и карбонизации с осаждением углерода из газовой фазы.
Основными этапами при первом способе технологического процесса получения УУКМ являются формование
заготовки методами намотки или выкладки из углепластика, полимеризация связующего, карбонизация, уплотнение пиро-литическим углеродом, окончательная термическая обработка и нанесение противоокислительных покрытий на основе карбидов кремния, иридия, циркония. Полимеризация связующего осуществляется при температуре не более 473 К. При последующем пиролизе связующего происходит образование на-углероженной фазы (кокса).
Чем больше содержание твердых продуктов пиролиза, прочность кокса и выше его сцепление с волокнами, тем выше качество получаемого УУКМ. При конечной температуре пиролиза, не превышающей 1073... 1773 К, образуется карбонизированный материал. В случае нагрева карбонизированного материала до 2773...3273 К происходит его графитизация. Процесс пиролиза органических матриц очень продолжителен и составляет примерно 75 ч. Для получения плотного материала с хорошими механическими свойствами осуществляют многократно цикл пропитка—-отверждение—карбонизация.
Плотность УУКМ в зависимости от режимов его получения находится в интервале от 1300 до 2000 кг/м3.
Свойства УУКМ изменяются в широком диапазоне, так как они определяются многими факторами: свойствами исходного волокна и природы связующего, степенью наполнения, свойствами кокса и прочностью его связи с волокном, условиями пропитки, отверждения, карбонизации, графитизации, числом циклов пропитка—карбонизация.
Второй способ изготовления УУКМ состоит в получении заготовки из сухого волокна методами укладки, намотки, плетения, армированием ткани в третьем направлении короткими волокнами, прошивкой. В настоящее время интенсивно разрабатываются УУКМ, армированные в трех и более направлениях. Углеродные волокна собирают с помощью специальных приспособлений в соответствии со схемой ориентации волокон в блоке. Получаемые таким образом пространственно армированные УУКМ характеризуются относительной изотропностью, низким коэффициентом термического расширения и позволяют изготавливать заготовки для деталей больших размеров.
При получении матрицы методом химического осаждения из газовой фазы применяют природный газ метан или анало-
гичный газообразный углеводород в комбинации с водородом или аргоном.
Этот способ перспективен, поскольку позволяет создавать материалы любой архитектуры с любыми наперед заданными свойствами при этом даже послойно. Например, можно осаждать таким образом не только углерод, но и такие материалы, как цирконий, медь, тантал и другие, осаждать послойно, придавая КМ различные желаемые свойства. Таким образом, полученный УУКМ в виде блока с определенной плотностью, жесткостью и подобными характеристиками, является полуфабрикатом, который может быть переработан в деталь методами механической обработки.
В общем случае УУКМ, полученные вторым способом, имеют большую плотность, более высокое содержание углерода, лучшие характеристики сцепления волокна с матрицей, но и большую стоимость, чем УУКМ, полученные пропиткой.
Структуры УУКМ обычно классифицируют по геометрическому принципу (рис. 1.28, а-м). Наиболее перспективным видом армирования УУКМ конструкционного назначения является многонаправленное армирование.
Многонаправленные УУКМ дают возможность реализовать заданные свойства материала в разных направлениях у готового изделия. В зависимости от выбранного типа волокон или их сочетания свойства УУКМ можно менять в широких пределах. Волокна с наиболее высоким модулем упругости обеспечивают самые высокие теплопроводность, плотность, содержание углерода и наиболее низкое термическое расширение композита. Такое сочетание свойств обусловлено высокой температурой при изготовлении высокомодульных волокон. Выбор самого подходящего типа волокна в каждом конкретном случае применения следует рассматривать как самостоятельную задачу проектирования.
Подходящим для армирования композитов материалом из переплетенных нитей является двунаправленная (2D) ткань. Ткани характеризуются шагом нитей, размером пучка, процентным содержанием нитей в каждом направлении, эффективностью упаковки нитей и сложностью узора плетения. Если необходима схема армирования с третьим направлением нитей, можно создать трехнаправленные (3D) ткани (рис. 1.29). Иде-
Рис.1.28. Структура УУКМ:
а - хаотичная; б - слоистая; в - розеточная; г - ортогональная ЗД д - 4JD е - 4D-Л; ж - 5£-Л; з - 5D; и - аксиально-радиально-окружная; к - аксиально-спиральная; л - радиально-спиральная; м - аксиально-радиально-спи-ральная
альной структурой обладают конструкционные композиционные материалы, в которых заданный тип и количество армирующих волокон в объеме изделия расположены так, что элемент конструкции из этого материала выдерживает расчетные нагрузки. Технология многонаправленного ткачества и является способом производства композитов с регулируемыми свойствами.
Простая многонаправленная структура из трех взаимно перпендикулярных нитей (3D) показана на рис. 1.30. Для максимального использования возможностей армирующего каркаса он составлен из прямых нитей. В ортогональных ЗД-структурах тип и количество нитей на единицу длины можно варьировать
Рис. 1.29. Однослой- Рис. 1.30. Схемы ортогонального трехна-
ная трехнаправленная правленного (3D) переплетения
(3D) ткань
во всех трех направлениях (см. рис. 1.30). Например, укладка 1.1.1 является сбалансированной с одной нитью на единицу длины в направлениях X, Y и Z Если считать нити твердыми стержнями квадратного поперечного сечения, то предельная плотность упаковки структурного элемента сбалансированной ортогональной 3.0-структуры равна 75 %, а остальные 25 % объема составляют пересекающиеся пустоты. Для получения малых пустот применяют плотную укладку нитей малого диаметра и схемы укладки с соотношением числа нитей 1.1.1 (рис. 1.31). Более равномерное распределение волокон в объеме обеспечивают за счет разных модификаций основной ортогональной 3D-структуры. Для получения композита с изотропными свойствами применяют структуры 4Д 5Д 7Д 11Z).
Проектирование схем армирования цилиндров и других тел вращения основано на тех же варьируемых параметрах, что и проектирование тканей и блоков. Схематически тканая структура тела вращения показана на рис. 1.32. Для обеспечения постоянной плотности армирования цилиндрических изделий с увеличением расстояний между радиальными нитями при приближении к наружному диаметру цилиндра диаметр осевых пучков нитей следует увеличивать (рис. 1.33, а). Другой способ обеспечения постоянной плотности структуры цилиндрических изделий основан на введении в основную схему армирования по мере приближения к наружному радиусу укороченных ра-
Рис. 1.31.Типичная схема укладки волокон малого диаметра в ортогонально армированном материале с целью получения высокой плотности каркаса
|
диальных элементов (рис. 1.33, б). Тканые армирующие каркасы могут также иметь форму усеченных конусов. Современная
Рис. 1.33. Компенсация осевых и
Рис. 1.32.Расположение нитей в трехна-правленном цилиндрическом переплетении: / — радиальные нити; 2 — осевые; 3 — окружные |
радиальных нитей: а — компенсация осевых нитей от внутреннего к наружному диаметру изменением диаметра осевых нитей; б — компенсация радиальных нитей изменением их длины
технология позволяет изготавливать изделие в виде комбинаций цилиндра и усеченного конуса или цилиндра с полусферическим куполом, выполненных как одно целое.
Дата добавления: 2018-05-02; просмотров: 1032; Мы поможем в написании вашей работы! |
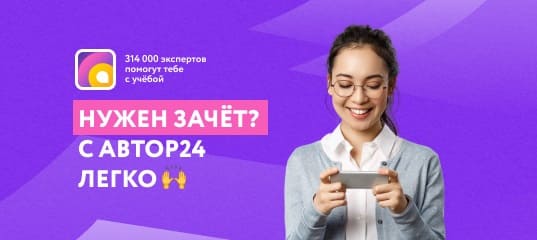
Мы поможем в написании ваших работ!