Физико-механические характеристики однонаправленных пластиков в сравнении с металлами
Стекло- | Угле- | Органо- | Боро- | Алю- | ||
Параметр | пластик | пластик | пластик | пластик | минии | |
Плотность ρ-10~3, кг/м3 | 2,1 | 1,5 | 1,38 | 1,9 | 7,8 | 2,7 |
Предел прочности, ГПа | ||||||
при растяжении вдоль волокон σ+1 | 1,75 | 1,1 | 1,8 | 1,6 | 3,8 | 0,29 |
при сжатии σ-1 | 0,65 | 0,45 | 0,28 | 2,4 | ||
при сдвиге т12 | 0,048 | 0,027 | 0,042 | 0,102 | ||
Удельная прочность | ||||||
при растяжении вдоль волокон σ+1 • 10~3 м | 83 | 73 | 130 | 80 | 50 | 11 |
Модуль упругости вдоль волокон Е+1-10"3, ГПа | 57 | 180 | 72 | 210 | 200 | 70 |
Удельная жесткость Е+1-10-6 кг6, м | 2,7 | 12 | 5,3 | 10,5 | 2,5 | 0,28 |
Модуль сдвига С]2, ГПа | 5,2 | 5,0 | 2,0 | 6,2 | — | — |
Сравнение характеристик однонаправленных композитов при растяжении или вдоль волокон показывает, что наибольшей удельной прочностью обладают органопластики, а угле- и боропластики значительно превосходят стекло- и органопластики по удельной жесткости.
Большинство однонаправленных композитов при сжатии в направлении вдоль волокон ведут себя как упругие тела, подчиняющиеся закону Гука вплоть до разрушения материала. Их модули упругости при растяжении и сжатии имеют одинаковое значение. У большинства ПКМ прочность при растяжении выше, чем при сжатии, за исключением боропластиков. Основные недостатки рассматриваемых ПКМ — их низкие механические характеристики при поперечном нагружении и сдвиге, обусловленные недостаточными прочностью матрицы и связи на границе раздела компонентов, низкие тепловая и радиационная стойкость, гигроскопичность, изменение физико-механических характеристик при старении и под воздействием климатических факторов.
|
|
Свойства ПКМ, армированных различными тканями и пропитанных разными связующими (табл. 1.18), зависят от большого числа факторов и в первую очередь характеризуют
составом, формой, длиной, диаметром армирующих волокон и способом подготовки их поверхности;
объемным содержанием армирующего наполнителя и связующего;
качеством пропитки армирующего наполнителя связующим;
свойствами связующего и прочностью его связи с наполнителем;
технологией (методом и режимом) изготовления ПКМ;
взаимным расположением армирующего наполнителя в изделии (схемой армирования).
Таблица 1.18
Характеристики КМ, армированных различными тканями
Марка ткани | Вид переплетения | Толщина ткани, мм | Плотность р. кг/м3 | Содержание связующего, % (масс.) | Прочность при растяжении σ+1, МПа | Модуль упругости при растяжении Е+1, ГПа
| ||||
основа | уток | основа | уток | |||||||
Стеклоткань АСТТ(б)-С (фенолфор- мальдегидное связующее) | Сатиновое 8/3 | 0,35 | 1850 | 38,8 | 530 | 280 | 26,6 | 20 | ||
Стеклоткань Т (полиэфирное связующее) | Полотняное | 0,27 | 1930 | 27,1 | 520 | 300 | 30 | 25 | ||
Стеклоткань МТБС-2,5 (полиэфирное связующее) | Мно-го- слой-ное | 2,5 | 1850 | 31,5 | 345 | 280 | 25 | 17,7 | ||
Углеткань П-5-13 (фенолфор- мальдегидное связующее) | То же | 3,0 | 1360 | 32,5 | 1Q1 | 92 | 12 | 13,5 | ||
Арамидная ткань (Кев-лар-49 на основе эпоксидного связующего) | Сатиновое 5/3 | 0,35 | 1330 | 50,0 | 517 | 310 | 27,6 | 21,5 |
1
Совмещение армирующих материалов со связующим для получения ПКМ можно осуществлять прямыми или непрямыми способами.
К прямым способам относятся такие, при которых изделие формуется непосредственно из исходных компонентов, минуя операцию изготовления полуфабрикатов.
Непрямыми называют способы, при которых изделие изготавливается из полуфабрикатов, т.е. из ПКМ, представляющих собой предварительно пропитанные материалы — препреги с ориентированным или неориентированным расположением волокон. К первым относятся однонаправленные ленты, ткани, монолисты, а ко вторым - премиксы, пресс-волокниты и т.п.
Элементарный вид ПКМ — микропластик, т.е. нить, пропитанная связующим.
|
|
На рис. 1.17 показано изменение коэффициента реализации прочности органических волокон от микропластика до натуральных изделий. Из рисунка ясно, что этот показатель уменьшается по мере усложнения технологии изготовления изделий. Поэтому основной задачей технолога является разработка способов (приемов), повышающих коэффициент реализации прочности в реальных технологических процессах производства изделий.
Современное производство элементов конструкций из полимерных композитов в значительной мере ориентируется на препреговую технологию изготовления изделий. Суть этой технологии состоит в использовании промежуточного полуфабриката препрега с большой жизнеспособностью, т.е. сроком существования активных радикалов в связующем, обеспечивающих отверждение матрицы. При нормальной температуре (20... 10 °С) этот срок составляет примерно три месяца, при
пониженной — до года. Препрег, полученный на специальных пропиточных установках, обладает наивысшим качеством пропитки наполнителя связующим, минимальными механическими повреждениями наполнителя, равномерным "наносом" связующего в наполнитель при оптимальном процентном содержании связующего.
|
|
Рис. 1.17.Влияние вида армирующего наполнителя на коэффициент реализации прочности волокон СВМ в различных образцах
Готовый препрег обычно представляет собой рулоны или пакеты ленточного калиброванного материала с разделительной пленкой между слоями. Отсутствие сколько-нибудь заметной липкости при нормальной температуре (20 °С + 10 °С) позволяет автоматизировать процесс нанесения препрега методами намотки, выкладки, делать технологически "чистыми" процессы ручной выкладки сложных изделий, проводить автоматизированный раскрой препрега на станках с программным
управлением, например на лазерных или ультразвуковых установках раскроя материала.
Препреги с ориентированным расположением волокон изготавливают на специальных установках вертикального (шахтного) или горизонтального типа. Последние являются более предпочтительными.
Схема пропиточной установки шахтного типа представлена на рис. 1.18. Поступая со шпулярника на распределительный барабан, нити наполнителя формируются в ленту, которая подсушивается нагревателем и далее подается на пропитку в ванну со связующим.
Рис. 1.18.Схема пропиточной установки для получения препрега: 1 — вакуумный насос; 2 — вакуумная камера; 3 — нагреватель; 4 - компенсатор уровня связующего; 5 — отжимное устройство; 6 - сушильная печь; 7 - бобина с разделительной пленкой; 8 - рулон с готовым препрегом; 9 - колибрующее устройство; 10 - нагреватель; 11 - ресивер; 12 - фильтр; 13 - вакуумный затвор; 14- ванна со связующим; 15- нагреватель; 16- шпулярник с нитяным наполнителем; 17 - распределительный барабан
После этого осуществляют пропитку, отжим, сушку и ка-либрование препрега. Наиболее важный этап в этой схеме -вакуумирование нитяного наполнителя, образующего препрег, его сушка и пропитка в вакуумной камере. Цель вакуумирова-ния и сушки заключается в удалении газовых включений и влаги из микротрещин и межволоконного пространства в нитях наполнителя для свободного проникновения в них связующего.
На малогабаритной установке для получения ленточных препрегов (рис. 1.19) непрерывные нити, сматываясь со шпулей, с большой скоростью (около 20 м/мин) протягиваются через ванночку с раствором связующего, где они пропитываются. Затем нити формируются специальным раскладчиком в ленту и поступают в цилиндрическую камеру сушки на барабан с транспортерами червячного типа, на котором транспортируемая лента частично отверждается. Подсушенная лента сматывается на приемную катушку (кассету), при этом между наматываемые слоями прокладывается разделительная бумажка или полимерная пленка, предохраняющая препрег от склеивания. В зависимости от типа связующего, условий хранения препреги сохраняют свою жизнеспособность от нескольких дней до нескольких месяцев. Лучший режим хранения препрегов — режим сухого льда.
Рис. 1.19.Малогабаритная установка для получения препрега в виде ленты: 1 - стеклонити с бобин, установленных в шпулярнике; 2 — пропиточная ванна с отжимными валиками; 3 — раскладчик нитей, формирующий из них ленту; 4 - подающий валик; 5 - цилиндрическая камера сушки ленты с барабаном, между двумя боковыми дисками которого расположены шесть транспортеров подачи ленты; 6 — катушка с лентой препрега на намоточном устройстве; 7 — калорифер; 8 — нагнетающий вентилятор; 9 — отсасывающий вентилятор
В последующих главах учебника будут рассмотрены различные технологические методы формования изделий из ПКМ.
Высокие удельные характеристики прочности и жесткости полимерных композитов позволяют использовать их в аэрокосмической техке. Углепластики применяют для изготовления космических антенн различного назначения. Низкие значения температурных коэффициентов линейного расширения, высокая жесткость и хорошая теплопроводнсть позволяют разрабатывать конструкции антенн, способные сохранять размеры и форму в условиях неравномерного лучистого нагрева. При этом важно проводить расчеты на жесткость и определять соответствующие структуры композиционного материала при проектировании. В существующих проектах при создании параболических антенн используются углепластики как для изготовления рефлектора, так и для опорной системы волновода.
Структура материального баланса в самолетных конструкциях, из которой следует, что к 2000 г. процентный состав металлических конструкций в самолетах составит 25...30 %, приведена на рис. 1.20.
Рис. 1.20. Структура материального баланса планера самолета
Применение углепластиков в конструкциях самолетов серии МИГ показано в табл. 1.19.
Таблица 1.19
Дата добавления: 2018-05-02; просмотров: 687; Мы поможем в написании вашей работы! |
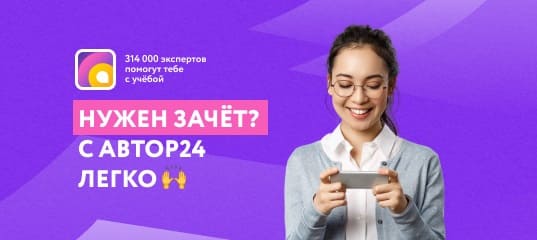
Мы поможем в написании ваших работ!