Уголь как источник углеводородных газов.
Для получения УВ газов из угля используют следующие процессы:
1. Гидрогенизация
С + Н2 → СnH2n+2 + СnH2n
Побочными продуктами могут быть NH3, H2S, H2O, например, если использовать древесный уголь.
Выделяют некаталитический и каталитический методы.
Метод Бергиуса (некаталитический), протекает под высоким давлением:
Стадии: измельчение угля →паста → гидрирование в автоклаве (300-500 атм) → УВ газы + бензин.
Среда, в которой делают пасту – декалин
Метод Шрёдера (каталитический). Используется трубчатый реактор, заполненный катализатором Mo/Al2O3. Температура около 400 °С.
2. Газификация угля
С + Н2О + ½ О2 → СО + Н2 (синтез-газ) , побочные продукты: СО2, СН4
3. Гидрогазификация угля – получаю заменитель природного газа (ЗПГ) с составом 97% СН4, 2 % Н2, 1 % остальные газы. В процессе выделяется большое количество энергии, мало побочного продукта СО2
1 стадия: С + Н2О + ½ О2 → СО + Н2
2 стадия: СО + Н2 изб → СН4 + Н2О
Газогенераторы Lurgi, Winkler, Koppers-Totzek
Метод Winkler
Газогенератор работает при атмосферном давлении и имеет диаметр 5,5 м, высоту 23 м и производительность до 1100 т угля в сутки. Дробленый и подсушенный уголь из бункера 1 шнеком 4 подают на распределительную решетку 6. С помощью первичного паровоздушного дутья, подаваемого под решетку, топливо переводится в псевдоожиженное состояние и газифицируется в шахте 2. Вторичное дутье через фурмы 3 вводят непосредственно в псевдоожиженный слой, чтобы повысить степень использования углерода топлива и газифицировать смолистые вещества, выделяющиеся в нижних слоях реакционной зоны. Твердый остаток – зола – удаляется в сухом виде, поэтому температуру в аппарате поддерживают не выше 1100 °С (ниже температуры плавления золы). Часть золы (~70 %) уносится из аппарата газовым потоком и затем выделяется в выносном мультициклоне, а оставшееся количество через отверстия распределительной решетки 6 ссыпается в нижнюю часть газогенератора, откуда шнеком 7 транспортируется в бункер 9. Для ускорения эвакуации частиц золы с поверхности решетки служит водоохлаждаемый вращающийся скребок 5, работающий от привода 8.
|
|
Метод Lurgi
В газогенераторе Lurgi исходный уголь (размер частиц 5–30 мм) из бункера 2 периодически загружают в шахту 7 газогенератора, снабженную водяной рубашкой 12. При помощи охлаждаемого вращающегося распределителя 5 и перемешивающего устройства 6 топливо равномерно распределяется по сечению аппарата. Парокислородное дутье подают под вращающуюся колосниковую решетку 11, на которой находится слой золы. Этот слой способствует равномерному распределению газифицирующего агента. При вращении колосниковой решетки избыточное количество золы с помощью ножей 8 сбрасывают в бункер 14. Образующийся в аппарате газ проходит скруббер 10, где предварительно очищается от угольной пыли и смолы (в случае необходимости смолу можно возвратить в шахту газогенератора). Вращение распределителя 5 и колосниковой решетки 11 осуществляется от приводов 4 и 9. В шахте газогенератора поддерживают давление ~ 3 МПа, поэтому, чтобы обеспечить безопасную загрузку топлива и выгрузку золы, каждый из бункеров 2 и 14 снабжают двумя конусообразными затворами 1, 3, 13 и 15. При загрузке топлива в бункер 2 затвор 1 открыт, а затвор 3 закрыт. Для передачи топлива в шахту затвор 1 закрывают, по обводной газовой линии соединяют бункер с шахтой газогенератора (для выравнивания давления) и открывают затвор 5. Перед следующей загрузкой топлива в бункер 2 закрывают затвор 3, сбрасывают газ в линию низкого давления, продувают бункер азотом или водяным паром, а затем открывают затвор 1.
|
|
Метод Koppers-Totzek
Одним из наиболее эффективных современных способов газификации пылевидного топлива (диаметр частиц менее 0,1 мм) является метод Koppers–Totzek. Из бункеров 1 подсушенное пылевидное топливо шнеками 2 подают через специальные форсунки 3 («горелочные головки») в горизонтальную реакционную камеру 4. В ней находятся две (а в последних конструкциях газогенераторов Koppers–Totzek – четыре) форсунки, расположенные друг против друга. В форсунках топливо смешивается с кислородом и водяным паром, причем подача последнего организована таким образом, что он обволакивает снаружи пылеугольный (точнее, угольно-кислородный) факел, тем самым предохраняя футеровку реакционной камеры от шлакования, эрозии и действия высоких температур. Особенность рассматриваемого процесса заключается в том, что зола в жидком виде выводится из
нижней части реакционной камеры, охлаждается и удаляется в виде гранулированного шлака. Газообразные продукты отводят через верхнюю часть реакционной камеры на охлаждение и очистку от пыли.
|
|
Дата добавления: 2018-05-02; просмотров: 723; Мы поможем в написании вашей работы! |
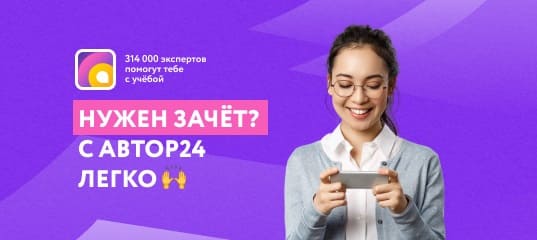
Мы поможем в написании ваших работ!