Пути оптимизации производственной инфраструктуры на предприятии
Направления технологического развития производственной инфраструктуры
Основные пути совершенствования производственной инфраструктуры ОАО «САН Инбев» подразумевают:
- регулярное изучение достижений в области проектирования и развития производственных структур с целью обеспечения мобильности и адаптивности инфраструктуры предприятия к нововведениям и новой продукции;
- укрепление и разукрепление предприятий и цехов;
- поиск и реализация более совершенного принципа построения цехов;
- оптимизация числа и размеров производственных подразделений предприятия;
- соблюдение рационального соотношения между основными, вспомогательными и обслуживающими цехами;
- постоянная работа по рационализации планировки предприятий;
- обеспечение пропорциональности между всеми цехами предприятия;
- обеспечение соответствия компонентов производственной инфраструктуры предприятия принципу пропорциональности по производственной мощности, прогрессивности технологических процессов, уровня автоматизации, квалификации кадров и других параметров;
- обеспечение соответствия инфраструктуры принципу прямоточности технологических процессов с целью сокращения длительности прохождения предметов труда;
- обеспечение соответствия уровня качества процессов в системе (производственной структуре предприятия) уровню качества входа системы. Тогда и качество выхода системы будет высоким;
|
|
-создание внутри крупного предприятия (объединения, акционерного общества, фирмы) юридически самостоятельных мелких организаций с предметной или технологической специализацией производства;
- быстрое изменение производственного профиля в условиях рыночной экономики, совершенствование специализации и кооперирования;
- развитие комбинирования производства;
- сокращение нормативного срока службы основных фондов;
- соблюдение графиков планово-предупредительного ремонта основных производственных фондов предприятия, сокращение продолжительности проводимых ремонтов и повышение их качества, своевременное обновление фондов;
- достижение конструктивно-технологической однородности продукции в результате широкой унификации и стандартизации;
- повышение уровня автоматизации производства;
- создание бесцеховой, где это возможно, инфраструктуры управления предприятием.
Соблюдение рационального соотношения между основными, вспомогательными и обслуживающими цехами и участками должно быть направлено на повышение удельного веса основных цехов по количеству занятых рабочих, стоимости основных фондов, доли прибыли в общей прибыли ОАО «САН Инбев».
|
|
В структурном отношении экономика ОАО «САН Инбев» должна формироваться как экономика отдельных звеньев и цехов. Пропорциональность входящих в состав ОАО «САН Инбев» звеньев характеризуется рациональным соотношением производственной мощности цехов и участков, связанных между собой совместным изготовлением конечного продукта.
Развитие комбинирования приводит к комплексному использованию сырья и материалов, экономии живого и овеществленного труда, а также уменьшению вредного воздействия на окружающую среду.
Конструктивно-технологическая однородность продукции создает хорошие условия для углубления специализации производства, организации поточного и автоматизированного изготовления изделий, повышению их качества и снижению издержек, что необходимо в условиях рыночной экономики.
Бесцеховая структура управления предприятием приводит к совершенствованию управления его подразделением, сокращению обслуживающего и управленческого аппарата, а, следовательно, к снижению издержек производства и лучшему реагированию на изменение спроса на продукцию. Правильно построенная производственная структура предопределяет пропорциональность всех цехов и служб ОАО «САН Инбев», что, в свою очередь, положительно влияет на улучшение технико-экономических показателей: уровень специализации и кооперирования, ритмичность изготовления продукции, рост производительности труда, улучшение качества изделий, сокращение численности управленческих кадров, наиболее целесообразное использование трудовых, материальных и финансовых ресурсов, увеличение прибыли.
|
|
Высшей формой поточного производства является автоматизированное производство, где сочетаются основные признаки поточного производства с его автоматизацией, данное направление и будет рассматриваться как оптимизация производственной инфраструктуры ОАО «Сан Инбев».
В автоматизированном производстве работа оборудования, агрегатов, аппаратов, установок происходит автоматически по заданной программе, а рабочий осуществляет контроль за их работой, устраняет отклонения от заданного процесса, производит наладку автоматизированного оборудования.
Различают частичную и комплексную автоматизацию.
При частичной автоматизации рабочий полностью освобождается от работ, связанных с выполнением технологических процессов. В транспортных, контрольных операциях при обслуживании оборудования, в процессе установки — полностью или частично сокращается ручной труд.
|
|
В условиях комплексно-автоматизированного производства технологический процесс изготовления продукции, управление этим процессом, транспортировка изделий, контрольные операции, удаление отходов производства выполняются без участия человека, но обслуживание оборудования — ручное.
Основным элементом автоматизированного производства являются автоматические поточные линии (АПЛ).
Автоматическая поточная линия — комплекс автоматического оборудования, расположенного в технологической последовательности выполнения операций, связанный автоматической транспортной системой и системой автоматического управления и обеспечивающий автоматическое превращение исходных материалов (заготовок) в готовое изделие (для данной автолинии). В АПЛ рабочий выполняет функции наладки, контроля за работой оборудования и загрузки линии заготовками.
Основные признаки АПЛ:
- автоматическое выполнение технологических операций (без участия человека);
- автоматическое перемещение изделия между отдельными агрегатами линии.
Автоматические комплексы с замкнутым циклом производства изделия — ряд связанных между собой автоматическими транспортными и погрузо-разгрузочными устройствами автоматических линий.
Автоматизированные участки (цехи) включают в себя автоматические поточные линии, автономные автоматические комплексы, автоматические транспортные системы, автоматические складские системы; автоматические системы контроля качества, автоматические системы управления и т.д. Примерная структура автоматизированного производственного подразделения приведена на рисунок 3.1.
Рисунок 3.1 - Структурный состав автоматизированного производственного подразделения
В условиях постоянно изменяющегося нестабильного рынка (тем более многономенклатурного производства) важной задачей является повышение гибкости (многофункциональности) автоматизированного производства, с тем чтобы максимально удовлетворить требования, нужды и запросы потребителей, быстрее и с минимальными затратами осваивать выпуск новой продукции.
Методы повышения гибкости автоматизированных производственных систем:
- использование автоматизированных систем технической подготовки производства (САПР);
- применение быстропереналаживаемых автоматических поточных линий;
- применение универсальных промышленных манипуляторов с программным управлением (промышленных роботов);
- стандартизация применяемого инструмента и средств технологического оснащения;
- применение в автоматических линиях автоматически переналаживаемого оборудования (на базе микропроцессорной техники);
- использование переналаживаемых транспортно-складских и накопительных систем и т.д.
Однако следует заметить, что любая универсализация требует значительных дополнительных затрат и при ее применении необходим взвешенный экономический подход на базе маркетинговой информации и исследований.
Автоматические поточные линии эффективны в массовом производстве.
Состав автоматической поточной линии:
- автоматическое оборудование (станки, агрегаты, установки и т.д.) для выполнения технологических операций;
- механизмы для ориентировки, установки и закрепления изделий на оборудовании;
- устройство для транспортировки изделий по операциям;
- контрольные машины и приборы (для контроля качества и автоматической подналадки оборудования);
- средства загрузки и разгрузки линий (заготовок и готовых деталей);
- аппаратура и приборы системы управления АПЛ;
- устройства смены инструмента и оснастки;
- устройства удаления отходов;
- устройство обеспечения необходимыми видами энергии (электрическая энергия, пар, инертные газы, сжатый воздух, вода, канализационные системы);
- устройства обеспечения смазочно-охлаждающими жидкостями и их удаления и т.д.
В состав автоматических линий последнего поколения также включаются электронные устройства:
1. «Умные супервизоры» с мониторами на каждой единице оборудования и на центральном пульте управления. Их назначение — заблаговременно предупреждать персонал о ходе процессов, происходящих в отдельных агрегатах и в системе в целом и давать инструкции о необходимых действиях персонала (текст на мониторе). Например:
- негативная тенденция технического параметра агрегата;
- информация о заделах и количестве заготовок;
- о браке и его причинах и т.д.
2. Статистические анализаторы с графопостроителями, предназначенные для статистической обработки разнообразных параметров работы АПЛ:
- время работы и простоев (причины простоев);
- количество выпускаемой продукции (всего, уровень брака);
- статистическая обработка каждого параметра обрабатываемого изделия на каждой автоматически контролируемой операции;
- статистическая обработка выхода из строя (поломка, сбой) систем каждой единицы оборудования и линии в целом и т.д.
3.2 Внедрение работ технологических процессов в структуру производства
Направления технологического развития ОАО «САН Инбев» включают в себя:
· установление параметров, которые надо контролировать: параметров проверки входящих материалов, параметров контроля полупродуктов и готового продукта (А.03.11.19-Пер «Перечень спецификаций службы качества»), параметров контроля во время остановок производства (процедура С.06.11.07-П «Управление остановками»), изменений в технологии и запуске новых сортов (С.06.11.05-П «Правила запуска новых сортов и внесения изменений в технологию»), запуске нового оборудования и при проведении других изменений (Е.16.11.03-П «Корректирующие и предупреждающие действия»).
· установление периодичности измерений;
· назначение исполнителей измерений;
· установление методов измерений (А.03.11.16-Пер «Перечень методик анализов аналитической лаборатории», А.03.11.17-Пер «Перечень методик микробиологической лаборатории», А.03.11.18-Пер «Перечень методик лаборатории солодовенного производства»);
· определение видов записей, мест записей, видов отчетов и информирование заинтересованных сторон;
· назначение лиц, ответственных за анализ данных.
На Саранском филиале планирование измерения полупродуктов и готового продукта осуществляется через разработку Графиков отбора проб. Исполнители измерений, записи по результатам и способ проведения анализа установлены, как в методиках службы качества, так и в рабочих инструкциях, картах технологического процесса, процедурах производств.
Подтверждение соответствия продукции осуществляется через получение санитарно-эпидемиологического заключения, декларирование и добровольную сертификацию (процедура С.06.11.02-П «Получение санитарно-эпидемиологического заключения, добровольного сертификата соответствия и декларации о соответствии на пиво»).
Планирование измерения, анализа, улучшения процесса: При описании процесса в процедуре указываются критерии эффективности процесса, кроме того, критерии эффективности процесса указаны в А.02.00.01-Пер «Перечень процессов Саранского филиала ОАО «САН Инбев». Владелец процесса устанавливает методы сбора информации по данным критериям. Измерение процесса проводится также по результатам внутреннего аудита Системы качества и Системы EHS при участии менеджера по качеству и специалиста по системам качества и сертификации на Комитете по качеству (Е.16.11.01-П «Порядок действия Комитета по качеству»).
Планирование измерения, анализа, улучшения системы: Измерение функционирования Системы качества осуществляется через проведения внутренних и внешних аудитов, через совещания для оценки эффективности системы, согласно процедуры Е.17.11.01-П «Проведение совещаний управленческого комитета Саранского филиала ОАО «САН Инбев».
Саранский филиал проводит периодические внутренние аудиты, чтобы оценить соответствие реальности требованиям стандарта ISO 9001:2000, процедурам и другой документации ОАО «САН Инбев», данного руководства по качеству и определить эффективность функционирования системы качества. Внутренними аудитами оценивается степень эффективности системы качества для обеспечения и гарантии качества выпускаемой продукции потребителю. Внутренними аудитами устанавливается также соответствие проведенных работ запланированным мероприятиям.
Менеджером по качеству составляется График проведения аудитов на год, в декабре предыдущего года. Этапы проведения аудита: сбор информации, планирование и подготовка, составление программы проведения аудита, вводное совещание,аудит,выработка, исправительных/корректирующих/предупреждающих действий заключительное совещание, составление отчёта о проведении аудита. Результаты аудита используются владельцами процессов, систем для измерения процессов, для составления анализа со стороны руководства о функционировании системы, для разработки планов, программ, направленных на постоянное улучшение процессов, систем.
Проведение внутренних аудитов описано в процедуре D.13.00.01-П «Внутренние аудиты Саранского филиала ОАО «САН Инбев».
Улучшение системы качества происходит в процессе планирования и анализа деятельности менеджерами производств и руководителями подразделений.
На Саранском филиале установлено правило системного подхода при планировании и выполнении любой работы. Установленное правило обеспечивает оценку эффективности выполненной работы, корректировку относительно запланированного результата и как цель - улучшение.
Предприятие проводит корректирующие действия, чтобы устранить причину несоответствий с целью их предотвращения в дальнейшей деятельности.
Проблемами системы качества являются те условия, которые вызывают или могут вызвать появление продукта несоответствующего качества или несоответствия деятельности установленным требованиям.
Проведение корректирующих действий включает:
а) определение несоответствия;
б) определение причин несоответствия;
в) определение и осуществление необходимого корректирующего действия, записи об этом;
г) записи результатов реализованного действия;
д) анализ реализованного корректирующего действия.
Выработка и проведение корректирующих действий осуществляется: в процессе текущей работы подразделений, при обнаружении несоответствий; совещаниях подразделений, совещаниях Управленческого комитета, на совещаниях Комитета по качеству.
Корректирующие действия проводятся по несоответствиям выявленным: при проведении внутренних аудитов; в текущей деятельности; в процессе испытаний продукции.
Корректирующие действия проводятся на основании: отчётов о результатах внутренних аудитов; по записям о текущей деятельности; протоколам совещаний; претензий потребителей.
Порядок выработки корректирующих действий описан в процедуре Е.16.11.03-П «Корректирующие и предупреждающие действия».
Саранский филиал определяет предупреждающие действия, чтобы устранить причины потенциальных несоответствий и предупредить возникновение проблем.
Предупреждающие действия вырабатываются перед началомпроведения работ и относятся к планированию выполнения работ. Предупреждающие действия вырабатываются также по результатам мониторинга/анализа процесса, для предотвращения возникновения потенциального несоответствия.
Заключение
Производственная структура ОАО «САН Инбев» создается при строительстве и реконструкции ОАО «САН Интербрю». Правильный выбор ее вида предопределяет эффективность производства. Однако он не может быть произвольным, так как, в свою очередь, обуславливается типом производства, уровнем и формой специализации и кооперирования производства. К факторам, предопределяющим тип производственной инфраструктуры, кроме того, относятся характер выпускаемой продукции и технология ее изготовления. Со временем, после завершения строительства или очередной реконструкции ОАО «САН Инбев», производственная структура, как правило, не отвечает новым требованиям. Это происходит потому, что за этот период меняется номенклатура выпускаемой продукции, серийность ее выпуска, происходит расширение некоторых производств, меняется технология и, следовательно, расстановка оборудования. Поэтому с целью улучшения производственной инфраструктуры и определения путей ее совершенствования необходимо периодически анализировать ее, сравнивать с передовыми аналогичными ОАО «САН Инбев»ми, а также необходимо отвечать требованиям научно-технического процесса не только относительно производственного процесса в целом, но и организационному управлению, создавая при этом благоприятные условия для рабочего персонала.
Технологическая линия описанная в данной работе функционирует на базе импортного оборудования кроме того, ее можно монтировать прямо на месте производства, т.е. перерабатывать продукцию сразу же. Это дает определенные преимущества т.к. значительно упрощается вопрос о техническом обслуживании, снабжении запасными частями и т.д. Остается только желать, чтобы отечественные производители оборудования вышли на тот же уровень, что и зарубежные.
Особая наука, для каждого сорта пива оно проводится со своими технологическими нюансами. Сначала солод перемалывают на мельнице. Молотый солод не должен быть однородным, но состоять как из мелких, так и из грубых крупинок, а также из тонкой муки, причем зерновые ости должны оставаться почти нетронутыми. Разные сорта пива требуют разного соотношения мелких и крупных частиц в измельченном солоде.
Дробленый солод и воду смешивают в затирочном чане, при этом возобновляется деятельность ферментов, приостановившаяся после сушки солода. Ожившие ферменты начинают превращать крахмал, из которого на 70% состоит зерно, в солодовый сахар. Чтобы ускорить процесс ферментации, солодовую кашу (затор) постепенно нагревают до температуры осахаривания - 76°C. В результате почти весь оставшийся крахмал расщепляется на сахара и декстрины, которые в процессе затирания растворяются в воде. Образовавшаяся масса перекачивается для очистки в большое сито, которое пока остается закрытым снизу. Затертый солод оставляют здесь на некоторое время, чтобы на дно осели нерастворимые частички, которые называют дробиной. Благодаря нетронутым остям дробина не слипается, выступая в качестве дополнительного сита. Когда сито открывают, сквозь него и дробину просачивается прозрачное светлое сусло, представляющее собой раствор сахаристых веществ, перешедших в него из солода.
Дата добавления: 2018-05-01; просмотров: 1352; Мы поможем в написании вашей работы! |
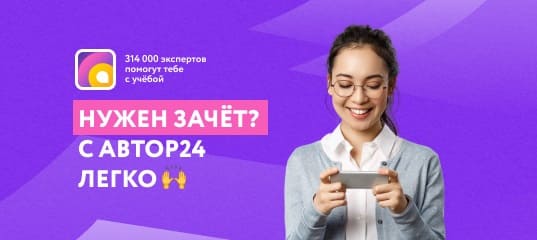
Мы поможем в написании ваших работ!