Повышение качества формирования структуры арболита путем улучшения режима уплотнения упругой арболитовой смеси
|
Макроструктура теплоизоляционного арболита, где коэффициент уплотнения небольшой (1,2-1,35), и конструктивно теплоизоляционного арболита большой толщины с коэффициентом уплотнения до 1,8 значительно отличается от структуры тонких и плотных изделий. С увеличением толщины формуемого изделия из арболитовой смеси все меньше частиц заполнителя ориентируются параллельно прессуемым плоскостям. С утолщением арболитовых изделий дезориентированное их возрастает в связи с хаотичностью расположения частиц заполнителя.
|
|
В зависимости от фракции и породы насыпная масса древесной дробленки варьируется в пределах от 90—120 кг/мЗ, а на 1 мЗ арболита (марок 5—35) расходуется от 160 до 240 кг древесной дробленки. Уплотнение обычной арболитовой смеси всегда связано с уменьшением объема формуемой смеси за счет обжатия и уменьшения межзернового пространства. Если учесть еще упругие свойства древесного заполнителя и малую подверженность гравитационному уплотнению за счет обычной вибрации из-за малой средней плотности заполнителя, то уплотнять арболитовую смесь традиционными способами затруднительно. Поэтому выбор способа и режима уплотнения упругой арболитовой смеси, позволяющих получить структуру арболита с минимальными остаточными напряжениями с высокой деформативной устойчивостью и обеспечивающих немедленную распалубку изделий, представляет большой практический интерес.
|
|
Применяются следующие способы уплотнения арболитовой смеси: циклическое прессование (немедленная распалубка), вибрирование с пригрузом (немедленная распалубка), вибропрессование с фиксирующей крышкой, силовой вибропрокат, послойная укладка и уплотнение и др. Каждый из этих способов имеет как преимущества, так и недостатки [1, 9, 42, 52]. Поскольку оптимизация процесса уплотнения арболитовой смеси может стать предметом особого исследования, мы ограничимся лишь рассмотрением структурно-механических процессов, протекающих при первых трех способах уплотнения, два из которых разработаны с нашим участием [24, 28]. Критерий оценки оптимальности уплотненной структуры следующий: чем оптимальнее уплотненная структура арболита, тем меньшими должны быть давление набухания и относительная величина деформации набухания. Результаты опытов приведены в табл. 12.
Таблица 12. Влияние способа уплотнения арболитовой смеси на относительные деформации и давление набухания арболита
Способ уплотнения | Средняя плотность, кг/м3 | Прочность на сжатие, МПа | Развиваемое давление набухания, МПа | Относительные деформации, мм/м |
Прессование с фиксирующей крышкой | 650 | 24,5 | 0,98 | 4,8 |
Циклическое прессование (немедленная распалубка) | 648 | 24,8 | 0,91 | 4,3 |
Вибрирование с пригрузом (немедленная распалубка) | 647 | 25,1 | 0,73 | 4,1 |
Примечание: состав смеси принят по Руководству 6-74 и ГОСТ 19222-73 на марку 25
Как видно из таблицы, наибольшая деформативная устойчивость свойственна арболитовым образцам, полученным вибрированием с пригрузом, и несколько меньшая — образцам, полученным циклическим прессованием. При виброуплотнении с пригрузом частицы древесного заполнителя, перемещаясь одна относительно другой, занимают в структуре арболита оптимальное положение, обеспечивающее наибольшую площадь контактных зон; при этом уменьшается редеформация — распрессовка. При обычном же способе прессования арболитовой смеси для получения изделий одинаковой средней плотности частицы древесного заполнителя сжимаются, вызывая упругие деформации, что ведет к распрессовке отформованного изделия и, в конечном итоге, к снижению конечной прочности.
Следовательно, для получения арболитовых изделий одинаковой средней плотности при уплотнении арболитовой смеси обычным прессованием необходимо приложить усилие в 10—20 раз больше, чем при прессовании вибропригрузом (причем эти усилия необходимо фиксировать жесткой крышкой, что связано с увеличением металлоемкости оснастки).
На рис. 24 приведены кривые зависимости степени уплотнения арболита от удельной величины пригруза; коэффициент уплотнения
Куп= H/h,
где Н — высота заполнения формы, мм; h — проектная высота изделия, мм.
Значение уплотнения арболитовой смеси (коэффициент 1,27) при вибрировании, равное 0,01 МПа, соответствует уплотнению при прессовании с удельным давлением 0,1 МПа, а воздействие виброуплотнения при пригрузе 0,02 МПа (коэффициент 1,35) соответствует прессованию с усилием 0,35 МПа. Это достигается за счет эффекта псевдоразжижения арболитовой смеси при уплотнении вибрированием с пригрузом. Дальнейшее повышение величины пригруза (более 0,02 МПа) и времени воздействия вибрирования под пригрузом в меньшей степени способствует уплотнению арболитовой смеси. Так, при изменении пригруза с 0,01 до 0,02 МПа, т.е. вдвое, коэффициент уплотнения возрастает лишь с 1,27 до 1,34. Структура арболита, полученная при вибрировании с пригрузом при одинаковой средней плотности и прочности, менее подвержена влажностным деформациям (см. табл. 12), чем структура, полученная только прессованием, что объясняется, очевидно, наличием напряжений в изделии, характер и величина которых зависят от способа формования.
Рис. 24. Влияние удельной величины пригруза на степень уплотнения арболитовой смеси (коэффициент уплотнения Ку)
1 – пригруз 0,02 МПа; 2 – пригруз 0,01 МПа; 3 – пригруз 0,005 МПа; 4 – пригруз 0,003 МПа.
Совершенствуя режим уплотнения арболита, удалось подобрать режим циклического прессования арболитовой смеси с последующей немедленной распалубкой отформованного изделия, что позволило сократить металлоемкость формующей оснастки. "Упругость" арболитовой смеси удалось снизить практически до нулевых значений благодаря режиму многократного сжатия и сброса давления прессования до нуля и введения мелкой фракции известнякового штыба.
Число циклов попеременного сжатия и удельное давление зависят от таких технологических факторов, как фракция древесного заполнителя, толщина прессуемого изделия, а также количество уплотняющей добавки — известнякового штыба (при изготовлении плит пола сборной стяжки). В зависимости от средней плотности и толщины изготовляемых арболитовых плит режим уплотнения (прессования) при немедленной распалубке будет различаться. Для теплоизоляционных плит со средней плотностью 400-500 кг/м3 удельное давление при толщине 60—80 мм составляет 0,5 МПа, а при толщине 80-120 мм - 0,6 МПа. Режим уплотнения при этом следующий: арболитовую смесь сжимают и выдерживают при постоянной деформации 30 с, а затем усилие прессования снижают до нуля и выдерживают смесь еще 10 с. Цикл проводится три раза. Для конструктивно-теплоизоляционных изделий — плит пола сборной стяжки со средней плотностью 850—900 кг/м3 (при введении в арболитовую смесь до 25% уплотняющей добавки — известнякового штыба) при толщине 70 мм удельное давление равно 0,6— 0,7 МПа. Режим уплотнения такой: сжатие арболитовой смеси и выдерживание при постоянной деформации — 30 с, снижение усилия прессования до нуля, выдерживание без давления — 15 с, затем давление прессования восстанавливают до первоначального значения. Цикл повторяется три раза.
Деформация смеси, т.е. ее уплотнение, возрастает после каждого нагружения, несмотря на то, что повторная нагрузка не превышает начального значения. Относительная деформация возрастает и тогда, когда давление прессования, снижающееся вследствие релаксации (переход упругой деформации в пластическую), периодически восстанавливается до исходного значения. Как показал опыт, при многократном нагружении давление прессования может быть значительно уменьшено. Применение такого метода целесообразно не только при формовании с немедленной распалубкой, но и при традиционном прессовании в формах, когда для уплотнения крупноразмерных арболитовых изделий не хватает мощности пресса.
Экспериментально доказано, что эффективность способа немедленной распалубки с многократным прессованием при уменьшении толщины формуемого изделия возрастает. Объем укладываемой смеси в форму определяется коэффициентом опрессовки. Для конструктивно-теплоизоляционных плит он составляет 1,5-1,8. Колебания коэффициента уплотнения объясняются некоторой разницей фракционного состава древесной дробленки. Смесь на крупной дробленке имеет меньший коэффициент уплотнения, чем смеси на мелком заполнителе. В принятой технологии после многократного прессования форма сразу же после извлечения ее цепным конвейером из пресса распалубливается. Как видно из табл. 12, как при вибрировании с пригрузом, так и при циклическом прессовании структурно-механические и деформативные свойства арболита улучшаются по сравнению с полученными при обычном способе прессования, когда упругая смесь сжата до набора распалубочной прочности. Поэтому эти способы более предпочтительны.
Дата добавления: 2018-04-15; просмотров: 673; Мы поможем в написании вашей работы! |
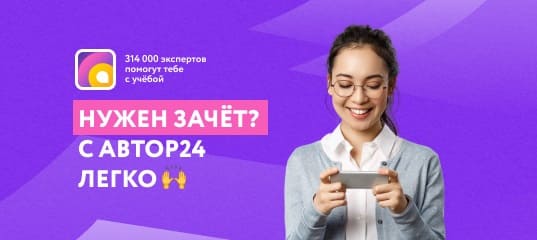
Мы поможем в написании ваших работ!