Влияние пленкообразующих добавок на физико-механические свойства арболита
|
Упрочнение каркаса структуры арболита путем увеличения растворной части при введении минеральных добавок
|
При обработке древесного заполнителя композиционной добавкой поверхность его покрывается минеральной пленкой.
В результате взаимодействия дисперсной фракции известняка с натриевым жидким стеклом (с модулем не выше 2) образуется силикат кальция, ускоряющий кристаллообразование - твердение цементного теста (которое в присутствии органического целлюлозного заполнителя из-за присутствия в его составе легкогидролизуемых сахаров замедленно).
В процессе вызревания и высыхания арболита с добавками известняка пылевидной фракции и натриевого жидкого стекла образующееся при их взаимодействии твердое вещество содействует упрочнению структуры. Предполагается [3], что процесс идет по реакции Na2O∙nSiO2 + СаСO3 = Na2CO3 (n - 1) SiO2 + CaSiO2 (10).
|
|
В то же время дисперсная фракция известняка и натриевое жидкое стекло, образуя минеральный слой на поверхности древесного заполнителя, уменьшают возможность диффундирования легкогидролизуемых cахаров из заполнителя в цементное тесто. Образование минеральной пленки на поверхности органического целлюлозного заполнителя одновременно улучшает сцепление в системе "древесина — цементный камень" за счет большего количества растворной части и увеличения площади контактной зоны между отдельными структурными элементами. Предложенный состав может быть рекомендован для районов, имеющих карьерные разработки известняка, в том числе в Крыму, УССР, АзССР и др. [25, 28], поскольку при этом эффективно используются отходы лесопереработки и камнепиления. Этот состав применен нами при производстве плит пола сборной стяжки в цех арболитовых изделий Главбакстроя (г. Баку). Плиты пола из арболита марки 50 нашли широкое применение в жилищном строительстве [23, 26, 27, 28].
Введение добавки известнякового штыба в количестве 25% массы вяжущего, рассчитанной на получение арболита марки 35, позволяет повысить эту марку до 50 или добиться экономии цемента до 15% при получении марки 35 за счет замены части цемента измельченным известняком (рис. 21).
Рис.21. Влияние добавки измельченного известняка на прочность и водопоглощение арболита при нормативном расходе цемента для марки 35 и при снижении его расхода при нормальном режиме твердения
1 – прочность при сжатии; 2 – водопоглощение, %
Способ создания на поверхности "агрессивного" по своей природе по отношению к портландцементу органического целлюлозного заполнителя (древесина, камыш, сечка конопли, льна) минерального слоя из карбоната кальция защищен авторским свидетельством № 660966 (Бюллетень изобретений, 1979,№ 17).
Как видно из рис. 22, введение в арболитовую смесь гидроксида кальция совместно с карбонатом аммония позволяет повысить марочную прочность арболита при расходе портландцемента, предусмотренном для марки 35, и снизить его водопоглощение, Такое улучшение свойств арболита можно объяснить образованием на поверхности древесного заполнителя минеральной пленки из карбоната кальция. Получается она в результате реакций между двумя веществами (см. реакцию), благодаря чему заполнитель становится менее "агрессивным" по отношению к цементу. Помимо этого улучшается адгезия к цементному камню (известно, что карбонат кальция имеет высокую адгезию к цементу).
Рис.22. Влияние В/Ц и соотношения компонентов комплексной добавки для обработки древесного заполнителя на прочность и водопоглощение арболита при нормативном расходе цемента и нормальном режиме твердения.
Для R1,W1 – В/Ц=0,9; для R2, W2 – В/Ц=1,2; для R3, W3 – В/Ц=0,8;
Реакция на поверхности заполнителя протекает предположительно по следующей схеме:
Са(ОН)2 + (NH4)2CO3 = CaCO3 + 2H2O + 2NH3. (11)
Обрабатывают древесный заполнитель растворами гидроксида кальция и карбоната аммония в смесителе во время приготовления арболитовой смеси. При непрерывном перемешивании в смеситель подают сначала древесную дробленку, затем раствор Са(ОН)2 через короткий промежуток (NH4)2CO3 и последним - цемент.
Анализ полученных результатов (см. рис. 22) свидетельствует о том, что оптимальное количество добавки находится в пределах 5—6% массы цемента при таком соотношении компонентов (% по массе): гидроксид кальция - 67, карбонат аммония - 33. Присутствие комплексной добавки при оптимальном соотношении компонентов позволяет снизить водопотребность (из-за выделения воды в процессе реакции между компонентами), доведя В/Ц смеси до 0,9, что положительно влияет на свойства арболита предложенного состава.
Введение в арболитовую смесь пленкообразующей добавки раствора полиакриламида совместно с хлоридом алюминия позволяет увеличить прочность арболита (авторское свидетельство № 624909. Бюллетень изобретений, 1978, № 35). Полиакриламид — высокомолекулярное синтетическое вещество, представляющее собой сополимер акриламида и карбоксильных групп. Наличием большого числа полярных карбоксильных групп можно объяснить улучшение прочности сцепления древесины с цементным камнем в конгломерате "древесина — цементный камень". Водный раствор полиакриламида обладает флокулирующим действием, способен образовывать тонкие пленки, закупоривающие морфологическую пористость древесного заполнителя. В результате повышается его гидрофобность и уменьшается выход из древесины цементных "ядов", чему способствует также возрастание вязкости растворной части арболитовой смеси.
Как показали исследования, наибольшая прочность арболита при расходе портландцемента, принятом для марки 35, при введении добавки полиакриламида (оптимальное соотношение компонентов, % по массе: цемент — 40, древесный заполнитель - 22, полиакриламид - 0,24, хлористый алюминий - 0,8 и вода — 36) составила 5 МПа. Благодаря пластифицирующему действию полиакриламида удалось снизить В/Ц с 1,2 до 0,92; что способствовало повышению прочности арболита. Увеличение прочности арболита и снижение его водопоглощения может быть объяснено также способностью полиакриламида образовывать коагуляционные структуры в порах и "сшитые" нерастворимые в воде сополимеры.
Дата добавления: 2018-04-15; просмотров: 356; Мы поможем в написании вашей работы! |
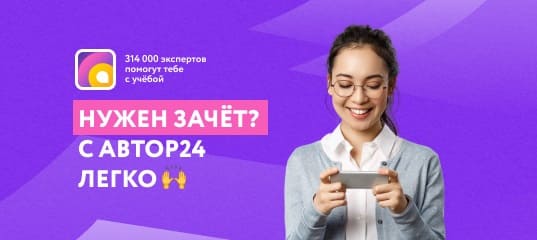
Мы поможем в написании ваших работ!