ПОРЯДОК ВЫПОЛНЕНИЯ ВИЗУАЛЬНОГО КОНТРОЛЯ ПОДГОТОВКИ И СБОРКИ ДЕТАЛЕЙ ПОД СВАРКУ
3.4.1. При подготовке деталей под сварку необходимо контролировать:
- наличие маркировки и/или документации, подтверждающей приемку полуфабрикатов, деталей, сборочных единиц и изделий при входном контроле;
- наличие маркировки материала на деталях, подготовленных под сварку (для деталей изделий, работающих под давлением, и для деталей, на которые распространяется действие Правил);
- наличие удаления механическим путем зоны термического влияния в месте термической (огневой) резки деталей (заготовок);
- Форму обработки кромок, з т.ч. при подготовке деталей с различной номинальной толщиной стенки:
- форму обработки внутренних поверхностей кольцевых деталей;
- материал и форму подкладных колец и расплавляемых вставок;
- наличие заварки разъема подкладного кольца, качество шва заварки
- подкладного кольца, а также наличие зачистки шва заварки разъема
- подкладного кольца;
- чистоту (отсутствие визуально наблюдаемых загрязнений, пыли, продуктов коррозии, масла и т.п.), подлежащих сварке (наплавке) кромок и прилегающих к ним поверхностей, а также подлежащих неразрушающему контролю участков основного материала.
3.4.2. При сборке деталей под сварку визуально необходимо контролировать:
правильность установки подкладных колец и расплавляемых вставок;
правильность установки временных технологических креплений;
правильность сборки крепления деталей а сборочных приспособлениях;
|
|
правильность (расположение и количество) установки прихваток и их качество;
правильность установки приспособлений для поддува защитного газа;
правильность нанесения активирующего флюса и защитной флюс-пасты;
наличие защитного покрытия от брызг расплавленного металла на поверхности деталей из аустенитных сталей, свариваемых ручной дуговой и полуавтоматической (автоматической) сваркой плавящимся электродом в среде защитного газа:
чистоту кромок и прилегающих к ним поверхностей деталей.
3.4.3. При подготовке деталей под сварку (рис. 1) осуществляется
проверка:
- размеров разделки кромок (угол скоса кромок, толщина и ширина притупления кромок разделки); радиусы округления размером до 1.0мм в местах перехода поверхностей разделки, а также размер скоса внутренней кромки, выполняемый для улучшения условий выявления не проваров в корне шва при радиографическом контроле, измерению не подлежат;
- размеров (диаметр, длина, угол выхода резца) расточки (раздачи)концов труб по внутреннему диаметру:
- размеров подкладных колец и расплавляемых вставок (ширина, толщина, угол скоса, диаметр);
- размеров элементов секторных отводов:
|
|
- перпендикулярности торцов, подготовленных под сварку цилиндриче-.ской детали после расточки по внутреннему диаметру;
- размеров отверстий под штуцер (патрубок) и обработки кромок в трубе (коллекторе,корпусе);
- ширины зоны зачистки механическим путем наружной и внутренней поверхностей деталей и шероховатости поверхностей кромок и прилегающих поверхностей деталей, в т.ч. места зачистки шва разъема подкладного остающегося кольца.
3.4.4. При контроле соединения, собранного под сварку (рис. 2)
осуществляется проверка:
- размеров швов приварки временных технологических креплений, расстояния технологического крепления от кромки разделки и расположение креплений по длине (периметпу) соединения (в''случае, если технологией оговорено расстояние между соседними креплениями);
- величины зазора в соединении, в т.ч. между деталью и подкладным кольцом;
- величины смещения кромок (внутренних и наружных) собранных де-талей);
- размеров (длина, высота) прихваток и их расположение по длине (периметру) соединения (в случае, если а технологии оговорено расстояние между соседниму прихватками);
- величины зазора в замке расплавляемой проволочной вставки;
|
|
- перелома осей цилиндрических деталей трубы и плоскостей плоских деталей (листы);
- несимметричности осей штуцера и отверстия в корпусе (трубе);
- ширины зоны нанесения защитного покрытия на поверхности деталей;
- геометрических (линейных) размеров узла. собранного под сварку (в случаях, оговоренных в технологии).
Рисунок 1 • Размеры, контролируемые измерениями
при подготовке деталей под сварку
а) V-образная разделка кромки; б) У -образная разделка кромки: в) (-образная разделка кромки (без скоса кромки); г) V-образная двухскосная разделка кромки: д) V-образная двухсторонняя разделка кромки; е) подготовка кромок штуцера Dу 10-65: ж) 1-образная разделка с присадочным выступом; э) цилиндрическая расточка (раздача) концов труб по внутреннему диаметру; и) коническая расточка концов груб по внутреннему диаметру, к) притупление внутренней кромки трубы
Продолжение рисунка 1
Рисунок 1 - Размеры, контролируемые измерением при
подготовке деталей под сварку
л), м), и н) подкладное стальное остающееся кольцо; о) расплавляемая проволочная вставка: л) сектор отвода: р) отклонение от перпендикулярности торца трубы: с), т), и у) рассверловка отверстия под штуцер в корпусе (трубе, коллекторе).
|
|
- Размеры измерению не подлежат. Размер обеспечивается режущим инструментом и оценивается визуально.
3.4.5. Визуальному и измерительному контролю подготовки и сборки деталей под сварку подлежат не менее 20% деталей и соединений из числа представленных к приемке.
Рисунок 2 - Размеры, контролируемые при сборке
соединения под сварку.
а) стыковое соединение: б) стыковое соединение на подкладном кольце: в) стыковое соединение с расплавляемой вставкой; г) тавровое (угловое) соединение; д) и е) угловые соединения штуцеров:
Объем выборочного контроля качества подготовки и сборки деталей под сварку может быть увеличен в зависимости от требований нормативной и технологической документацией или по требованию заказчика.
Продолжение рисунка 2
Рисунок 2 • Размеры, контролируемые при сборке соединения
под сварку
ж) соединение с несимметричностью осей штуцера и корпуса; з) соединение с приваренными элементами временных креплений: и) соединение с переломом осей цилиндрических деталей;
к) прихватим соединения.
При выявлени. отклонений от требований рабочих чертежей и/или технологии, которые могут привести к ухудшению качества сварных соединений, объем вы-. борочного контроля (20%, 50%) должен быть увеличен в двое для группы однотипных деталей (соединений). Если при дополнительном контроле снова будут выявлены отклонения, то объем контроля для группы деталей, предоставленных к приемке, дол>: эн быть увеличен до 100%.
Детали, забракованные при контроле, подлежат исправлению (доработиа). Собранные под сварку соединения деталей, забракованные при контроле, подлежат расстыковке с последующей повторной сборкой'после устранения причин. вызвавших их первоначальную некачественную сборку.
3.4.6. Визуальный контроль полноты удаления зоны термического влияния после резки термичискими способами (газовая, воздушно-дуговая, газофлюсовая, плазменная и др.) определяется на каждой дегали, подвергавшейся резке. Полнота удаления оценивается по отсутствию следов резки на кромках разделки (для деталей из низкоуглеродистых, марганцовистых и кремнемарганцови-стых сталей) и по отсутствию следов разметки (кернение), нанесенной на наружной поверхности деталей после резки.
3.4.7. Требования к выполнению измерений при подготовке деталей подсварку приведены в таблице в, а при сборке соединений под сварку - в таблице 7.
Таблица 6 • Требования к измерениям размеров при подготовки
деталей под сварку
Контролируемый параметр | Условное обозначение (рис.1) | Рисунок | Сродства измерений. Требования к измерениям |
1 | 2 | 3 | 4 |
1. Угол скоса кромки | а, в, а1 | 1а,б,г,д. е.к | Угломер или шаблон универсальный. Измерение в одном месте. |
2. Притупление кромки | Р.Р1 | 1а,б,г,д, е | Штангенциркуль ШЦ-1. Измерения в двух взаимоперпендикулярных сечениях (4 точки) |
3. Ширина "уса" разделки или скоса кромки | С | 16, е, т | Штангенциркуль ШЦ-1. Измерения а трех точках равномерно по длине(периметру) |
4. Глубина скоса кромки | м | 1д,к1.у | Штангенциркуль ШЦ-1. линейка. Измерения не менее, чем в трех точках по длине. |
5. высота присадочного выступ? | Нв | 1ж | Штангенциркуль ШЦ-1. Измерения в двух взаимоперпендикулярных сечениях (4 точки) |
6. Длина расточки (р. эда-чи) труб по внутреннему диаметру | Lp | 13 | Тоже |
7. Угол входа резца (калибра) | ? | 1з,и | Шаблон универсальный или уг-ломер. Измерение а одном месте |
8. Диаметр расточки | Dp | Штангенциркуль ШЦ-1. Измерения в двух взаимоперпендикулярных сечениях (4 точки) | |
9. Толщина стенки в месте расточки | Sp | 13, Н | Штангенциркуль ШЦ-1. Измерения не менее, чем в трех точках равномерно по длине |
10 Ширина подкладного кольца | Вк | 1л, м, н | Штангенциркупь ШЦ-1.. Измерения не менее, чем а трех точках по длине (периметру) |
1 | 2 | 3 | 4 |
11 Толщина подкаладного кольца | Sx | 1л, м, и | Тоже |
12. Притупление подкладного кольца | Р< | 1л, м, и | Тоже |
13. Диаметр расплавляемого кольца | Он. Dec | 1л, м, и, о | Штангенциркуль ШЦ-1 Измерения в двух азаимопрепендикулярных сечениях (4 точки) |
14 высота расплавляемого кольца(вставка) | А | 1о | штангенциркуль ШЦ-1. Измерения не менее, чем в трех точках равномерно по периметру |
15. Ширина расплавляемого кольца(вставка) | Вас | 1o | Тоже |
16. Длина сектора отвода (сварного) по наружной образующей | Н | 1n | Линейка. Измерение детали а зоне максимального размера |
17. Длина сектора отвода (сварного) по внутренней образующей | Р | 1n | Линейка. Измерение детали в |
18. Угол наклона кромки сектора отвода (сварного) | 02 | 1п | Линейка и угломер или шаблон универсальный. Измерение скоса кромки с обеих сторон
( ![]() |
19. Отклонение торца разделки (трубы) от перпендикуляра к образующей трубы | F | 1n | Угольник и щуп. Измерения не менее, чем в трех сечениях • зоне максимального смещения. Либо: отвес и линейка или щуп |
20. Диаметр отверстия в корпусе (трубе) | d | 1с, т, у | Штангенциркуль ШЦ-1. Измерения двух взаимоперпендикулярных сечениях (4 точки) |
21. Диаметр расточки в корпусе (трубе) | d1 | 1У | Тоже |
22. Шероховатость зачищенных поверхностей | Профилограф-профилометр, образцы шероховатости (сравнивания). Контролируют поверхности, указанные а п.4.2.6 |
Примечание - Допускаются другие способы и средства измерений. обеспечивающие достоверность контроля параметров подготовки деталей под сварку.
Таблица 7 - Требования к измерениям размеров сборки
соединений деталей под сварку
Контролируемый параметр | Условное обозначение (рис.2) | Номер Рисунка | Средства измерений. Требования к измерениям. |
1 | 2 | 3 | 4 |
1. Зазор в соединении | а | 26, в, г, д. е | Щуп. шаблон универсальный. Измерение - см. п. 3.4 8. |
1 | 2 | 3 | 4 |
2. Смещение кромок деталей с внутренней стороны соединения | 0 | 2а | Линейка и щуп. Измерение - см. п. 3.4.8. |
3. Смещение кромок деталей с наружной стороны соединения | F | 2а.б | Линейка и щуп. Измерение - см. п. 3.4.8. |
4. Зазор между подкладным кольцом и внутренней поверхности детали | b1 | 2б | Шаблон специальный. Измерения не менее, чем а трех точках по длине (периметру)соединения |
5.Смещение проволочной вставки с внутренней стороны | b2 | 2б | Штангенциркуль ШЦ-1. шаблон универсальный или щуп. Измерение выполняется после прихватки вставки к кромке разделки одной из деталей |
6 Зазор в эамке расплавляемого кольца (вставки) | a1 | Шаблон универсальный или щуп. Измерение выполняется после прихватки вставки к одной из деталей | |
7 Несимметричность штуцера | б2 | 2ж | Контрольный стенд специальный. Измерение согласно п. 3.4.13. |
8 Расстояние приварного элемента крепления от кромки разделки | С | 2з | Линейка. Измерени •) подлежит каждый элемент крепления |
9. Катет шва приварки элемента крепления | К | 2з | Линейка и щуп, штангенциркуль ШЦ-1. шаблон. Измерению подлежит каждый шов |
10. Перелом осей цилиндрических элементов к угловое смещение поверхностей листов | К | 2и | Линейка (L3 400мм) и щуп. Измерение - см. п. 3.4.12. |
11. Длина прихватки | In | 2к | Линейка или штангенциркуль ШЦ-1. Измерение каждой прихватки |
12. Высота прихватки | hn | 2к | Штангенциркуль ШЦ-1 Измерение каждой прихватки |
13. Расстояние между прихватками | Ln | 2к | Линейка. Измерение расстояния между прихватками соединения выполняется а случаях, когда расстояние между прихватками регламентируется технологии |
3.4.8. Измерения величины зазора в соединении, величины смещения кромок и перелома плоскостей в соединениях выполнять не реже, чем через один метр по длине соединения, но не менее, чем в трех сечениях, равномерно расположенных по длине шва. При невозможности (отсутствие доступа) контроля смещения кромок с внутренней стороны соединения оценку возможного смещения следует производить по смещению наружных кромок деталей (размер F) либо по смещению притупления "усов" V - образной разделки (см. рис. 16, размер р).
3.4.9. Измерения, в первую очередь, следует выполнять на участках, вызывающих сомнение в части размеров по результатам визуального контроля.
3.4.10. Контроль размеров и качества прихваток проводится на каждой прихватке в соединении.
3.4.11. Измерение швов прихватки временных технологических креплений и расстояния от приварного элемента крепления до кромки разделки выполняют в одном месте. Контролю подлежит каждое крепление и каждый шов крепления.
3.4.12. Перелом осей, собранных под сварку кольцевых соединений цилиндрических элементов, выполняется в 2-3 сечениях (в зоне максимального излома. выявленного при визуальном контроле) на расстоянии 200 мм от центра соединения, При отсутствии прямолинейного участка детали длиной 200 мм разрешается измерение размера производить на участке меньшей длины с последующим перерасчетом к длине 200 мм по формуле:
где М и L - размеры перелома осей и расстояние от соединения, на котором выполнено измерение (рис.3)
Рисунок 3 - Схема измерения перелома осей цилиндрических элементов
.4.13. Несимметричность штуцера в поперечном сечении определяется путем выполнения не менее двух измерений в одном сечении. Разрешается выполнять контроль несимметричности отверстия под штуцер на стадии контроля подготовки деталей под сварку.
3.4.14. Схемы измерения отдельных размеров подготовки деталей под сварку и сборки соединений под сварку с помощью шаблонов универсального типа УШС приведены на рис.4-8.
Рисунок 4 - Шаблон универсальный типа УШС
Рисунок 5 - Схема измерения угла скоса разделки
Рисунок 6 • Схема измерения размера притупления разделки
Рисунок 7 • Схема измерения зазора в соединении
Рисунок 8 - Схема измерения смещения наружных кромок деталей
Дата добавления: 2018-04-15; просмотров: 1751; Мы поможем в написании вашей работы! |
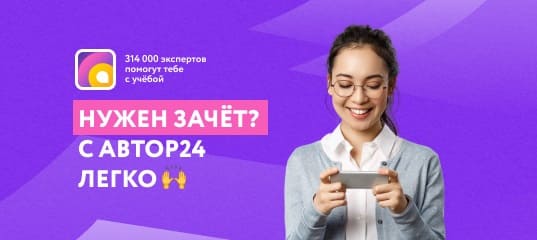
Мы поможем в написании ваших работ!