ТРЕБОВАНИЯ К ПРИБОРАМ И ИНСТРУМЕНТАМ ДЛЯ ВИЗУАЛЬНОГО И ВИЗУАЛЬНО-ОПТИЧЕСКОГО КОНТРОЛЯ
БЕЛОРУССКАЯ АССОЦИАЦИЯ НЕРАЗРУШАЮЩЕГО КОНТРОЛЯ И ТЕХНИЧЕСКОЙ ДИАГНОСТИКИ БЕЛОРУССКАЯ ГОСУДАРСТВЕННАЯ ПОЛИТЕХНИЧЕСКАЯ АКАДЕМИЯ ФАКУЛЬТЕТ ПОВЫШЕНИЯ КВАЛИФИКАЦИИ КАФЕДРА «ЭКСПЕРТИЗА И ЭКСПЛУАТАЦИЯ ОБЪЕКТОВ ПОВЫШЕННОЙ ОПАСНОСТИ» ПРАКТИЧЕСКОЕ ПОСОБИЕ ПО ВИЗУАЛЬНОМУ И ВИЗУАЛЬНО-ОПТИЧЕСКОМУ КОНТРОЛЮ Настоящее практическое пособие разработано для проведения обучения в целях сертификации и в помощь специалистам, проводящим визуальный и визуально-оптический контроль при изготовлении, монтаже, ремонте, реконструкции, включая грузоподъемные краны, и эксплуатации энергетического оборудования, металлических конструкций, трубопроводов, газопроводов, сетей и сооружений водоснабжения и других объектов, в том числе подконтрольных Проматомнадзору. Практическое пособие не является нормативным документом для проведения контроля. При разработке практического пособия были учтены требования действующих нормативных документов и Правил Проматомнадзора Республики Беларусь. Составители: Никифорова З.С. к.т.н., Корольков Д.И., Нестеренко Н.Л. к.т.н. СОДЕРЖАНИЕ 1. Общие положения. 2 2. Требования к приборам и инструментам для визуального и визуально-оптического контроля. 2 3. Требования к выполнению визуального и визуально-оптического контроля. 2 3.1. Подготовка места производства работ. 2 3.2. Подготовка объекта к контролю.. 2 3.3. Порядок выполнение визуального и визуально-оптического контроля основного материала. 2 3.4. Порядок выполнения визуального контроля подготовки и сборки деталей под сварку. 2 3.5. Порядок выполнения визуального контроля сварных соединений. 2 3.6. Порядок выполнения визуального контроля сварных узлов и деталей и сборочных едениц (сварных узлов идеталей). 2 3.7. Порядок выполнения визуального и визуально-оптического контроля при исправлении дефектов в основном материале и сварных соединениях изделий. 2 3.8. Порядок выполнения визуального и визуально-оптического контроля при техническом диагностировании. 2 4. Оценка результатов контроля. 2 5. Регистрация результатов контроля. 2 Приложение А Основные термины и определения. 2 Приложение Б Требования к содержанию "Программы (плана) входного контроля" 2 Приложение В Требования к содержанию "Технологической карты визуального (визуально-оптического) контроля" 2 Приложение Г Требования к содержанию "Карты операционного контроля" 2 Приложение Д Формы документов, оформляемых по результатам визуального контроля и визуально-оптического контроля. 2 Приложение Е Клеймение деталей, сборочных единиц и сварных соединений 2 Приложение Ж Перечень нормативных документов. 2
|
|
ОБЩИЕ ПОЛОЖЕНИЯ
|
|
1.1. Настоящее практическое пособие ориентировано на визуальный и визуально-оптический контроль качества
основного материала (полуфабрикаты, заготовки, изделия); подготовки деталей к сварке;
сборки соединений деталей (сборочных единиц, изделий) под сварку;
Сварных соединений и наплавок;
изготовления деталей и сборочных единиц;
исправления дефектов в сварных соединениях и основном металле,
который выполняется на стадиях входного контроля основного материала, изготовления (монтажа, ремонта) деталей, сборочных единиц и изделий и при техническом диагностировании состояния Металла и сварных соединений в процессе эксплуатации.
1.2. Визуальный и визуально-оптический контроль основного материала на стадии входного контроля выполняется при поступлении материала на предприятие с целью подтверждения его соответствия требованиям стандартов (ГОСТ, СТБ), технический условий (ТУ), рабочей конструкторской документации (рабочие чертежи) и Правил Проматомнадзора (Правил).
1.3. Визуальный и визуально-оптический контроль качества подготовки деталей выполняется перед началом технологической операции, например, перед сборкой соединения под сварку или перед гибкой колена и т.д., с целью подтверждения соответствия качества подготовки требованиям рабочих чертежей, технологии изготовления (технологии), нормативной документации (НД) и Правил.
|
|
1.4. Визуальный и визуально-оптический контроль качества сборки соединений деталей под сварку выполняется с целью подтверждения соответствия качества сборки требованиям рабочих чертежей, технологии и / или НД и Правил.
1.5. Визуальный и визуально-оптический контроль качества изготовления изделий (деталей. сборочных единиц) выполняется с целью подтверждения их соответствия требованиям рабочих чертежей, ТУ и Правил.
1.6. Визуальный и визуально-оптический контроль качества сварных соединений и наплавок оборудования, конструкций и трубопроводов, выполняется с целью подтверждения их соответствия требованиям рабочих чертежей, технологий и / или НД и Правил.
1.7. Визуальный и визуально-оптический контроль качества исправления дефектов (Приложение А) в основном материале, сварных соединениях и наплавках выполняется с целью подтверждения полноты удаления дефекта, формы и размеров выборки дефектного участка, а также качества заварки выборок (в случаях, когда выборка подлежит заварке) требованиям технологии, НД и Правил.
|
|
1.8. Визуальный и визуально-оптический контроль изделий при техническом диагностировании производят с целью выявления изменений их формы (деформации изделия), а также поверхностных дефектов в основном материале и сварных соединениях, образовавшихся в процессе эксплуатации.
1.9. Визуальный и визуально-оптический контроль на стадии входного контроля основного материала (полуфабриката, заготовок, изделий) выполняется в соответствии с "Программой (планом, инструкцией) входного контроля" (Приложение Б), которая разрабатывается предприятием, выполняющим входной контроль. "Программа (план, инструкция) входного контроля" разрабатывается в соответствии с требованиями ГОСТ 24297 и отраслевых руководящих материалов. 8 "Программе (плане, инструкции) входного контроля" должны указываться виды изделий (полуфабрикатов, заготовок), подлежащих контролю, виды и объемы контроля, способы контроля, включая схемы выполнения измерений контролируемых параметров, а так же нормативные показатели допустимых отклонений.
1.10. Визуальный и визуально-оптический контроль качества изделий (деталей, сборочных единиц), а также сварных соединений при изготовлении (монтаже. ремонте, реконструкции) выполняется в соответствии с требованиями "Технологической карты контроля" или "Карты (схемы) операционного контроля" (Приложения В и Г).
В указанных картах должны приводиться контролируемые параметры, последовательность контроля, схемы выполнения измерений контролируемых параметров. Технологические карты и карты операционного контроля разрабатываются а соответствии с ГОСТ 23479.
1.11. Визуальный и визуально-оптический контроль состояния металла и сварных соединений при техническом диагностировании оборудования и трубопроводов должен выполняться в соответствии с "картами (схемами) визуального и визуально-оптического контроля", которые разрабатываются в составе "Программы технического диагностирования". Разработку "Программы технического диагностирования" производит предприятие, выполняющее работы по техническому диагностированию или специализированная организация, имеющая лицензию Проматомнадзора на право выполнения этого вида работ. В "Картах (схемах) контроля" должны указываться места проведения контроля на конкретном объекте, схемы контроля, средства измерения контролируемого параметра, нормы оценки качества и бланки оформления результатов измерений и контроля.
1.12. Визуальный контроль, как правило, выполняется невооруженным глазом или с помощью лупы. Увеличение луп должно быть 4-7 кратное при контроле основного материала и сварных соединений при изготовлении, монтаже и ремонте и до 20-кратного при техническом диагностировании.
1.13 Визуальный и визуально-оптический контроль должен выполняться до проведения контроля изделия (сварного соединения) другими методами неразрушающего и разрушающего контроля.
1.14. При доступности визуальный визуально-оптический контроль основного металла и сварных соединений деталей следует выполнять как с наружной, так и с внутренней стороны изделия.
1.15. Визуальный и визуально-оптический контроль основного материала сварных соединений и наплавок изделий, подлежащих термической обработке. следует производить как до. так и после указанной обработки. Если изделие, в т.ч. сварное, подлежит полной термической обработке (нормализации или закалке с последующим отпуском), контроль следует проводить после ее выполнения не зависимо от проведения предварительного отпуска.
1.16. Если сварное соединение подлежит механической обработке (в том числе, с удалением валика усиления шва) или деформированию, то визуальный контроль следует выполнять после проведения указанных операций.
1.17. Дефекты, выявленные при визуальном и визуально-оптическом контроле, должны быть исправлены до проведения последующего вида контроля другими методами. либо до выполнения технологической операции. Исправление дефектов в основном материале должно выполняться в соответствии с требованиями технологии действующей на предприятии.
1.18. Контролируемая зона сварного соединения должна включать весь объем металла шва. а также участки основного металла в обе стороны от шва шириной:
не менее 5 мм - для стыков соединений, выполненных дуговой и электронно-лучевой сваркой при нормальной толщине сварных деталей 5 мм включительно;
не менее нормальной толщины стенки детали - для стыковых соединений, выполненных дуговой и электронно-лучевой сваркой при нормальной толщине сварных деталей свыше 5 до 20 мм;
не менее 20 мм - дг" стыковых соединений, выполненных дуговой и электронно-лучевой сваркой при нормальной толщине сварных деталей свыше 20 мм. а также для стыковых и угловых соединений, выполненных газовой сваркой, независимо от нормальной толщины стенки сварных деталей и при ремонте дефектных участков в сварных соединениях;
не менее 6 мм (независимо от нормальной толщины сварных деталей) - для угловых, тавровых, торцевых и нахлесточных сварных соединений и соединений вварки труб в трубные доски, выполненных дуговой и элэктронно-лучевой сваркой;
не менее 50 мм (независимо от нормальной толщины сваренных деталей) - для сварных соединений, выполненных электрошлаковой сваркой.
1.19. К выполнению каждого последующего вида работ (технологической операции) разрешается приступать только после приемки предыдущего вида работ (технологической операции).
Например, к изготовлению заготовок деталей разрешается приступать после входного контроля металла; к изготовлению сборочных единиц путем сварки деталей - после приемки качества подготовки деталей, в т.ч. подготовки кромок; к сварке соединений - после приемки качества сварки деталей: к контролю качества сварных соединений неразрушающими и разрушающими методами -после приемки готовых сварных соединений; к исправлению дефектных участков • после выявления и разметки границ дефектного участка и т.д.
Разрешение на выполнение каждого последующего вида работ (технологической операции) выдается специалистом, выполняющим визуальный и визуально-оптический контроль, который делает отметку о приемке предыдущего вида работ в учетных документах (Журнал сварочных работ. Карта операционного контроля. Маршрутная карта и др.). либо путем клеймения на поверхности изделия (детали, сборочной единицы).
ТРЕБОВАНИЯ К ПРИБОРАМ И ИНСТРУМЕНТАМ ДЛЯ ВИЗУАЛЬНОГО И ВИЗУАЛЬНО-ОПТИЧЕСКОГО КОНТРОЛЯ
2.1. Визуальный и визуально-оптический контроль основных материалов, сварных соединений и изделий проводится невооруженным глазом и (или) с применением оптических приборов (луп. микроскопов, визуально-оптических приборов для контроля удаленных и скрытых объектов - цистоскопов, эндоскопов. бароскопов, флексоскопов, биноклей, перископических дефектоскопов, зеркал, зрительных труб и др.).
2.2. Для измерения формы и размеров изделий и сварных соединений, угловых и линейных величин полуфабрикатов, деталей, сборочных единиц, сварных соединений, изделий, а также поверхностных дефектов следует применять исправные, прошедшие проверку или метрологическую аттестацию, инструменты и приборы:
-лупы измерительные по ГОСТ 25706;
- линейки измерительные металлические по ГОСТ 427;
- угольники поверочные 90 ° лекальные по ГОСТ 3749;
- штангенциркули по ГОСТ 166 и штангенрейсмасыпо ГОСТ 164:
- щупы №2....4;
- угломеры с нониусом по ГОСТ 5378;
-стенкомеры и толщиномеры индикаторные по ГОСТ 11358:
- микрометры по ГОСТ 6507;
- нутромеры металлические по ГОСТ 10 и индикаторные по ГОСТ 868;
- шаблоны, в том числе универсальные (например, типа УШС по ТУ 102.338-83). радиусные, резьбовые и др.;
- толщиномеры ультразвуковые, типа УТ-93П и другие аналогичные им
2.3. Для измерения больших линейных размеров изделий или отклонений от формы и расположения поверхностей изделий следует применять:
- поверочные плиты;
- плоскопараллельные концевые меры длины по ГОСТ 9038 с набором
специальных принадлежностей по ГОСТ 4119;
- штриховые меры длины по ГОСТ 427 и ГОСТ 7502 (стальные измерительные линейки, рулетки);
- оптические и лазерные приборы (нивелиры, макротелескопы), а также измерительные приборы и инструменты, приведенные в п.2.2.
Для измерения линейных размеров изделий, помимо перечисленных средств, допускается применение других специальных приборов и методов измерений, при условии обеспечения заданной погрешности измерения. Технические характеристики отдельных средств измерений приведены з таблицах 1.2 и 3.
Таблица 1 - Типы луп
Тип | Назначение | Конструктивное исполнение | Группа лупы | Оптическая система |
ЛП | Для просмотра деталей, мелких предметов | Складные с ручкой. штативные | Малого, среднего. большого увеличения | Простая одно-линзовая, многолинзовая, корригированная |
ЛИ (измерительная) | Для линейных и угловых измерений | В оправе имеющей диоптрийную подвижку и измерительную шкалу | Среднего увеличения | Многолинзовая корригированная |
2.4. Для измерения конструктивных элементов формы и размеров кромок, зазоров собранных под сварку соединений, а также размеров выполненных сварных швов разрешается применять шаблоны различных типов, при условии подтверждения их характеристик метрологической службой предприятия или органом государственной метрологической службы.
2.5. При проведении измерения погрешность не должна превышать величин. указанных в таблице 4. если в рабочих чертежах не предусмотрены более жесткие требования.
2.6. Для определения шероховатости и волнистости поверхности следует применять профилографы-профилометры, либо образцы шероховатости (сравнения).
2.7. Измерительные приборы и инструменты в процессе эксплуатации, а также после ремонта должны проходить проверку в метрологических службах в установленные сроки.
Таблица 2 - Технические характеристики приборов и инструментов для визуального и визуально-оптического контроля
Тип прибора. инструмента | Марка | ГОСТ. ТУ | Диапазон измерений | Цена деления,MM | Допускаемая погрешностьизмерений. MM |
1 | 2 | 3 | 4 | 5 | 6 |
1 Профипограф - | Мод. 280 | ТУ2.03423-88 | Профилограф 0.02-100 мкм | ||
профилометр | ГОСТ 19300 | Профилометр | |||
Ra - 0.02-25мкм | |||||
Rz- 0.2-100мкм | |||||
Rp-0.1-50мкм | |||||
Rmax-0.2-100мкм | |||||
Образцы Шероховатости поверхности | ГОСТ 9378 (СТ СЭВ 848) | ||||
Угломер с нониусом | УН мод. 127 2УМ 5УМ 4Ум | ГОСТ 5378 | 0-180 град | 2 мин 2 мин 5 мин 15 мин | ±2 мин ± 2 мин ± 3 мин ± 15 мин |
Стенкомер индикаторный | С-2 С-10А С-10Б | ГОСТ 11358 | 0-2 мм 0-10 мм 0-10 мм | 0.01 0.01 0.1 | ± 0.015 ± 0.020 ±0.1 |
С-25 | 0-25 мм | 0.1 | ±0.1 | ||
С-50 | 25-50 мм | 0.1 | ±0.1 | ||
Толщиномер индикаторный | ТР 10-60 ТР25-60 ТР50-250 | ГОСТ 11358 | 0-10 мм 0-25 мм 0-50 мм | 0.01 0.01 0.1 | ± 0.018 ±0.03 ±0.15 |
Микрометр | МК50-1 МК75-1 МК100-1 МК125-1 МК15С-1 МК175-1 | ГОСТ 6507 | 25-50 мм 50-75 мм 75-100 мм 100-125 мм 125-150 мм 150-175 мм | 0.01 | ±0.02 ± 0.0025 ± 0.0025 ±0,003 |
МК200-1 | 175-200 мм | ||||
Нутромер микрометрический | НМ-75 НМ-600 НМ-1250 | ГОСТ 10 | 50-75 мм 75-бООмм 600-1250мм | ± 0.003 ± 0.003 ±0.004 |
1 | 2 | 3 | 4 | 5 | 6 |
Нутромер | НИ-6-10-2 НИ-10-18-2 НИ-18-50А-2 | ГОСТ 868 | 6-10 мм 10-18 мм 18-50 мм | 0.01 0.01 0.01 | ±0.012 ±0.012 ±0.015 |
Штангенциркуль ШЦ-1 Двусторонний с глубиномером | ШЦ-1-125-0.1 | ГОСТ 166 | 0-125 мм• | 1 | ±0.1 |
Штангенциркуль ШЦ-П двусторонний с микрометрической подачей | ШЦ-ПИ60 ШЦ-П-200-0.1 ШЦ-П-250-0.1 | ГОСТ 166 | 0-160 мм 0-200 мм 0-250 мм | 1 1 1 | ±0.07 ±0.08 ±0.1 |
Щуп | №1 №2 №3 №4 | 0.02.0.1 мм 0.02-0.5 мм 0.055-1.0 мм 0.1-1.0 мм | |||
Набор радиусных шаблонов | РЩ-1 РШ-2 РШ-3 | 0-25 мм | |||
Набор резьбовых шаблонов | М60* М 55- | Шаг резьбы 0.4-6.0 мм Число ниток на 1 дюйм 28-4 | |||
Шаблон универсальный | УШС-3 | ГОСТ 15150-69 ТУ 102-338-83 | |||
Линейка Измерительная Металлическая | Линейка-150 Линейка - 300 Линейка - 500 Линейка -1000 | ГОСТ 427 | 0-1000 мм | 1 | ±0.1 ±0.1 ±0.16 ±0.2 |
Метр складной металлический хромированный | ТУ2-17-ЗОМ1 | 0-1000 мм | 1 | ±1 | |
Рулетка в закрытом корпусе самосвертывающаяся | ЗКПЗ-1АНТ/1 ЗКПЗ-АНТ/1 | ГОСТ 7502 | 0-1000 мм 0-2000 мм | 1 1 | ±0.20 ±0.2 |
Угольник поверочный 90° лекальный плоский | УЛП-1-60 УЛП-1-160 | ГОСТ 3749 | |||
Меры длины концевые плоско-параллельные | 2-Н7 | ГОСТ 9038 (СТ СЭВ 720) | 1-200 мм | ±0,01 | |
Набор принадлежностей к плоскопараллельным концевым мерам длины | Н-бор №1 | ГОСТ 4119 |
1 | 2 | 3 | 4 | 5 | 6 |
Меры угловые призматическую | Набор №2 Набор №8 | ГОСТ 2875 ГОСТ 12069 | 100-700 | ||
Меры длины штриховые многозначные | ГОСТ 12069 | ||||
Лупа измерительная | ЛИ-4-10х | ГОСТ 25706 | Увеличение 10 крат | ||
Лупа складная карманная | ЛАЗ-6х | ГОСТ 25706 | Увеличение 6 крат | ||
Лупа бинокулярная | ВЛ-2 | ТУЗ-3.687 | Увеличение 2 крат | ||
Толщиномер ультразвуковой | УТ-93П | ЩЮ 2.787.011 | 0.6-1000 мм | 0.1 | 0.1 |
Таблица 3 - Приборы и средства измерений отклонений
отпрямолинейности и плоскостности
Наименование средств и методов измерения | Тип | Длины измеряемых поверхностей, мм |
Интерферометр | ИЗК-1 | Свыше 400 до 6300 |
Автоклиматор | АК-1У АК-6У | Свыше 400 до 10000 то же |
Оптическая линейка | ИС-36 ИС--43 ИС-49 | до 4000 to же то же |
Индуктивная линейка | ЛИП-3 УИП-5 | до 1000 то же |
Уровни (рамные брусковые, Индуктивные) | Свыше 400 до 10000 | |
Поверочные линейки (прямоугольного я двутаврового сечения, мостики) | ШП, ШД. ШМ | Свыше 400 до 4000 |
Оптические струны | ДГ--477М | Свыше 400 до 10000 |
Визирные трубы (ЛОМО) | ППС-11 ППС-12 | Свыше 400 до 10000 то же |
Уровни гидростатические (завод 'Калибр") | 115-I 115-II |
Таблица 4-Допускаемая погрешность измерения
при измерительном контроле
Дата добавления: 2018-04-15; просмотров: 560; Мы поможем в написании вашей работы! |
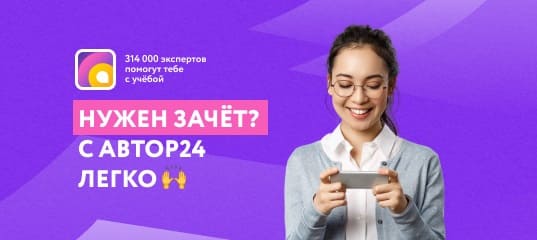
Мы поможем в написании ваших работ!