Твердость по Шору ISO 868 (DIN 53505, ASTM D2240)
Значениями твердости по Шору являются показания шкалы, полученные в результате проникновения в пластик определенного стального стержня. Эта твердость определяется склероскопами двух типов, оба из которых имеют калиброванные пружины для приложения нагрузки к индентору. Склероскоп А применяется для более мягких материалов, а склероскоп D - для более твердых.
![]() | ![]() |
Рис. 8: Определение твердости по Шору | Рис. 9: Инденторы для склероскопов |
Значения твердостей по Шору изменяются:
- от 10 до 90 для склероскопа Шора типа А - мягкие материалы,
- от 20 до 90 для склероскопа Шора типа D - твердые материалы.
Если измеренные значения >90А, то материал слишком тверд, и должен применяться склероскоп D.
Если измеренные значения <20D, то материал слишком мягок, и должен применяться склероскоп А.
Не существует никакой простой зависимости между твердостью, измеренной с помощью этого метода испытаний, и другими основными свойствами испытуемого материала.
ИСПЫТАНИЯ НА ПРОЧНОСТЬ ПРИ УДАРЕ
Понятие прочности при ударе
При стандартных испытаниях, например, испытаниях на растяжение и изгиб, материал поглощает энергию медленно. Реально материалы очень часто быстро поглощают энергию приложенного усилия, например, усилия от падающих предметов, ударов, столкновений, падений и т.д. Целью испытаний на прочность при ударе является имитация таких условий.
|
|
Для исследования свойств определенных образцов при заданных ударных напряжениях и для оценки хрупкости или ударной вязкости образцов применяются методы Изода и Шарпи. Результаты испытаний по этим методам не должны использоваться как источник данных для проектных расчетов компонентов. Информация о типовых свойствах материала может быть получена посредством испытания разных типов испытуемых образцов, приготовленных в различных условиях, с изменением радиуса надреза и температуры испытаний.
Испытания по обоим методам проводятся на ударном маятниковом копре. Образец зажимают в тисках, а маятниковый копер с закаленной стальной ударной поверхностью определенного радиуса отпускают с заданной высоты, что вызывает срез образца от резкой нагрузки. Остаточная энергия маятникового копра поднимает его вверх. Разность высоты падения и высоты возврата определяет энергию, затраченную на разрушение испытуемого образца. Эти испытания могут проводиться при комнатной температуре либо при пониженных температурах для определения хладноломкости. Испытуемые образцы могут быть разными по типу и размерам надрезов.
Результаты испытаний на удар падающим грузом, например, по методу Гарднера или изогнутой плитой, зависят от геометрии падающего груза и опоры. Их можно использовать только для определения относительного ранжирования материалов. Результаты испытаний на удар не могут считаться абсолютными, кроме случаев, когда геометрия испытательного оборудования и образца соответствуют требованиям конечного применения. Можно ожидать, что относительное ранжирование материалов по двум методом испытаний будет совпадать, если характер разрушения и скорости удара одинаковы.
|
|
Интерпретация результатов испытаний на удар –
Сравнение методов ISO и ASTM
Ударные характеристики могут в большой степени зависеть от толщины образца и ориентации молекул. Разные толщины образцов, используемых в методах ISO и ASTM, могут весьма значительно повлиять на значения прочности при ударе. Изменение толщины с 3 мм на 4 мм может даже привести к переходу характера разрушения от вязкого к хрупкому из-за влияния молекулярной массы и толщины образца с надрезом при использовании метода Изода, как это продемонстрировано для поликарбонатных смол. На материалы, уже показывающие хрупкий характер разрушения при толщине 3 мм, например, материалы с минеральными и стекловолоконными наполнителями, изменение толщины образца не влияет. Такими же свойствами обладают материалы с модифицирующими добавками, увеличивающими ударную прочность.
|
|
Рис. 10: Влияние толщины и молекулярной массы образца с надрезом на результаты ударных испытаний поликарбонатных смол по Изоду
Необходимо четко представлять, что:
- изменились не материалы, а только методы испытаний;
- упомянутый переход от вязкого разрушения к хрупкому играет незначительную роль в реальной действительности: конструируемые изделия в преобладающем большинстве имеют толщину 3 мм и менее.
Дата добавления: 2018-04-15; просмотров: 2083; Мы поможем в написании вашей работы! |
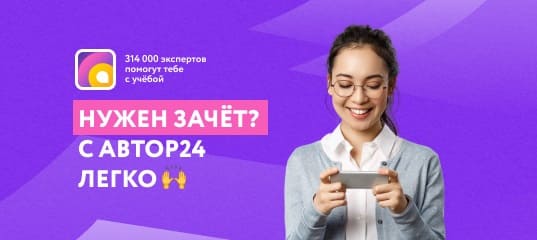
Мы поможем в написании ваших работ!