РАСЧЁТ МАТЕРИАЛЬНОГО БАЛАНСА ПРОИЗВОДСТВА
Исходные данные:
Мощность ксилитного цеха, М | 2500 т/год |
Сырьё – берёзовая древесина Выход РВ из 1 тонны а.с.д. (пентоз), Z | 20% |
Выход целлолигнина из 1 тонны а.с.д., Zцлг | 72% |
Зольность сырья, L | 0,3% |
Номинальный объём гидролизаппарата, V1 Рабочий объём, V2 | 50 м3 42 м3 |
Оборот гидролизаппарата, t | 420 мин |
Число рабочих дней в году, N | 345 |
Загрузка а.с.д., D | 160 кг/м3 |
Влажность сырья, W | 45% |
Модули: - отбора пентозногогидролизата, m1 - смачивания сырья, m2 | 5,0 0,5 |
Температура пентозного гидролиза, T (i = 546,6 кДж/кг) | 130оС |
Концентрация H2SO4: - на смачивание, C1 - на пентозный гидролиз, C2 | 10% 0,8% |
Расход H2SO4 на гидролиз, R | 1,86% |
Выход ксилита от РВ, Zкс1 | 37% |
Влажность целлолигнина, Wцлг | 69% |
Потери по стадиям производства, p: - нейтрализация, фильтрация - отстаивание - выпарка нейтрализата - фильтрация сиропа - ионообмен сиропа - гидрирование - ионообмен ксилита - подупаривание, 1-ая кристаллизация - упаривание оттека - 2-ая кристаллизация | 2,5% 2,0% 6,0% 1,0% 12% 5% 9,5% 2,5% 1,0% 1,0% |
Выход ксилита от утфеля, Zкс2 | 61% |
Выход 2-х кристаллов из оттёка, Z3 | 27% |
Расход H2SO4нанейтр. зольных элементов, % ота.с.д. | 0,3 |
Предварительный расчёт:
1. Часовая производительность завода:
|
|
G = M/(N*24) = 2500/(345*24) = 0,302 т/ч
2. Выход пищевого ксилита иза.с.д.:
Zпищ.кс=Z*(1-0,02)*Zкс1/100 = 20*(1-0,02)*0,37 = 7,25%
3. Расход а.с.д.:
Rа.с.д. = G/(Zпищ.кс/100) = 0,302/0,073 = 4,14 т/ч
4. Выход РВ:
ZРВ = Rа.с.д.*Z/100 = 4,14*0,20 = 0,828 т/ч
Баланс периодического гидролиза:
1. В гидролизаппарат загружается а.с.д.:
Dа.с.д. = V2*(1-0,05)*D/100 = 42*(1-0,05)*0,16 = 6,384 т
2. Влажного сырья:
S = Dа.с.д./(1-W) = 6,384/(1-0,45) = 11,61 т
Влаги в сырье:
Dвлаги = 5,22 т
3. Варочной кислоты на загрузку:
DH2SO4 = Dа.с.д*m2 = 6,384*0,5 = 3,19 т
4. Пара на прогрев и перколяцию:
Dпр = =
= = 2,01 т
где: с1и с2 – теплоёмкости а.с.д. и воды при 130оC
5. Всего влаги:
∑D = Dвлаги+ DH2SO4+Dпр = 5,22+3,19+2,01 = 10,42 т
6. Модуль прогрева:
mпр = ∑D/Dа.с.д. = 10,42/6,38 = 1,63
7. Выдача гидролизата:
g = Dа.с.д.*m1 = 6,38*5,0 = 31,9 т
8. Остаток лигнина:
· абсолютно сухого: O1 = Dа.с.д.*Zцлг = 6,38*0,72 = 4,59 т
· влажного: O2 = O1/(1-Wцлг) = 4,59/(1-0,69) = 14,8 т
· влаги в нём: DO влаги = O2–O1 = 14,8 – 4,59 = 10,21 т
9. Варочная кислота на прогрев должна содержать H2SO4:
· для создания концентрации 0,8%:
c1 = ∑D*c = 10,42*0,008 = 0,08336 т
· на поглощение зольными веществами:
Dз.в. = Dа.с.д.*0,3/100 = 6,38*0,3/100 = 0,0192 т
· всего:
B = c1+Dз.в. = 0,08336+0,0192 = 0,1025 т
10. Концентрация варочной кислоты на смачивание:
CH2SO4 = B*100/DH2SO4 = 0,1025*100/3,19 = 3,21%
11. Варочной кислоты на перколяцию:
Q = g+O2-Dа.с.д.-∑D = 31,9+14,8-6,38-10,42 = 29,9 т
|
|
12. Общий расход H2SO4 на варку:
Rобщ. = Dа.с.д.*R = 6,38*0,0186 = 0,1187 т
Из них пойдёт на перколяцию:
Rпер = Rобщ-B = 0,1187-0,1025 = 0,0162 т
А при концентрации 75%:
R75% = Rобщ*0,75 = 0,1187*0,75 = 0,089 т
13. С лигнином удержится кислоты:
U1 = Dа.с.д.*x = 6,38*0,0035 = 0,0223 т
И выйдет с гидролизатом:
U2 =Rобщ–(Dз.в+U1) = 0,1187 –(0,0192+0,0223) = 0,0772 т
14. Расход воды на перколяцию:
RH2O = Q-R75% = 29,9-0,089 = 29,811 т
Эта вода включает конденсат греющего пара, поданного в подогреватель в количестве:
X = (RH2O-X)*c2*1,04/с3
X = (29,811-X)*546,6*1,04/2730
X = (29,811-Х)*0,20823
Х = 6,2075-0,20823Х
1,20823Х = 6,2075
Х = 5,138 т
где: 1,04 – коэффициент, учитывающий потери тепла, а с3 = 2730 МДж – теплоёмкость 1 т пара при 130oС
15. Поступает воды из решоферов:
DH2O = RH2O-X = 29,811-5,138 = 24,673т
16. Общий расход пара на варку:
Rп.общ = Dпр.+X = 2,01+5,138 = 7,148 т
17. При выстреле лигнина из него испарится влаги:
Iвл = (O1*c4+DO влаги*с2)/с3 = (4,59*176,6+10,21*546,6)/2730 = 2,34 т
где: с4 =176,6 МДж – теплоёмкость 1 т лигнина при 130oC
Остаётся влаги в лигнине:
Овлаги =DO влаги –Iвл = 10,21-2,34 = 7,87 т
Влажность лигнина в циклоне:
Wлигн = Овлаги*100/(О1+Овл) = 7,87*100/(4,59+7,87) = 63,2%
Часовой баланс:
Для обеспечения подачи требуемого количества гидролизата в ксилитный цех необходимо проводить Rа.с.д./Dа.с.д. = 4,14/6,384 = 0,649 варок в час для получения 2500 тонн ксилита в год. Фазовый сдвиг 60/0,649 = 92,45 мин.
|
|
Баланс варки и часовой батареи гидролизаппаратов (в тоннах):
Приход | Варка | В час | Расход | Варка | В час |
Сырьё | 6,384 | 4,14 | Гидролизат | 31,9 | 20,7 |
Влага сырья | 5,22 | 3,39 | 2. Лигнин абс. сухой | 4,59 | 2,98 |
Влага смачивания | 3,19 | 2,07 | 3. Влага в лигнине | 7,87 | 5,11 |
Пар на прогрев | 2,01 | 1,3 | 4. Влаги испарилось | 2,34 | 1,52 |
Вода из решоферов | 24,673 | 16,01 | |||
Пар на перколяцию | 5,138 | 3,335 | |||
Кислота на перколяцию | 0,089 | 0,058 | |||
Баланс: | 46,7 | 30,3 | Баланс: | 46,7 | 30,3 |
Испарение гидролизата:
Испаряется жидкости в испарителе: IH2O = g(iг – i1)(1 – zn)/r1 = 20,7*(546,6-437)*(1-0,03)/2179 = 1,01 т/ч, где zn – коэффициент, учитывающий потери тепла, отн. ед.; iг – удельная энтальпия (теплосодержание) гидролизата в общем коллекторе, кДж/кг.
Поступит в сборник гидролизата: Dгидр = g- IH2O = 20,7-1,01 = 19,6 т/ч,
где дополнительно испарится: Iдоп = 19,6*(437-415)*0,96/2265 = 0,183 т/ч.
Поступит на нейтрализацию: Dнейтр = Dгидр- Iдоп = 19,6-0,183 = 19,42 т/ч.
|
|
Отделение инверсии, нейтрализации и фильтрации:
1. Поступает РВ в цех для выработки 2500 тонн ксилита в год:
DРВ = М*100*103/Zkc1*N*24 = 2500*100*1000/37*345*24 = 816,03 кг/ч
2. Количество гидролизата:
qгидр = DРВ*100/y = 816,03*100/5,2 = 15692,88 кг/ч,
где 5,2 – содержание РВ в 1м3гидролизата.
Количество сухих веществ в гидролизате:
qc.в. = DРВ*100/d = 816,03*100/65 = 1255,43 кг/ч,
где 65 – доброкачественность гидролизата после инверсии, %.
3. Расход активированного угля на осветление гидролизата:
Добавляется активированного угля абсолютно сухого 25% к сухим веществам гидролизата:
Rа.у. = qc.в.*25/100 = 1255,43*25/100 = 313,86 кг/ч,
или влажного активированного угля (суспензии коллактивита):
Rвл.а.у. = Rа.у.*100/(100-Wа.у.) = 313,86*100/(100-85) = 2092,4 кг/ч,
где Wа.у. – воды в суспензии коллактивита, %.
4. Общее количество раствора, поступающего на нейтрализацию всего:
qр-ра = qгидр+ Rвл.а.у. = 15692,88+2092,4 = 17785,28 кг/ч.
5. Содержание H2SO4 в гидролизате, считая на 100%:
SH2SO4 = qc.в.*C H2SO4/100 = 1255,43*12/100 = 150,65 кг/ч,
где CH2SO4 – концентрация H2SO4 к сухим веществам.
6. Расход извести на нейтрализациюH2SO4 в гидролизате:
· расход активногоСаО:
Rакт = SH2SO4*М1/М2 = 150,65*56/98 = 86,09 кг/ч;
где М1=56 и М2=98 – молекулярные массыСаО и H2SO4;
· технической извести, считая на 85%:
Rтехн = Rакт*100/85 = 86,09*100/85 = 101,28 кг/ч;
· расход известкового молока:
Rмол = Rакт*1000/200 = 86,09*1000/200 = 430,45 л/ч,
где 200 – содержание СаОактивной в 1 л известкового молока илие = Rмол*b = 430,45*1,11 = 477,8 кг/ч.
Расход воды на приготовление известкового молока:
RH2O.1 = е-Rтехн = 477,8-101,28 = 376,52 кг/ч.
7. Количество шлама, образовавшегося при нейтрализации:
· образуется би-гидрата сульфата кальция:
q1 = Rакт*М3/М1 = 86,09*172/56 = 264,42 кг/ч,
где М3=172 – молекулярная масса СаSО4*2Н2О;
· количество раствора:
q3 = qр-ра-Rа.у. = 17785,28-313,86 = 17471,42 кг/ч;
· количество растворенного би-гидрата сульфата кальция, считая, что его содержится 0,2 в растворе:
q2 = qр-ра*Iдоп/100 = 17471,42*0,183/100 = 31,97 кг/ч;
· количество би-гидрата сульфата кальция, переходящего в шлам:
q4 = q1-q2 = 264,42-31,97 = 232,45 кг/ч;
· количество выпадающих коллоидных взвешенных веществ 0,3% по весу от гидролизата:
q5 = qр-ра*0,3/100 = 17785,28*0,3/100 = 53,36 кг/ч;
· количество активированного угля в оборотной лепешке с сиропных фильтр-прессов(qа.у.) с влажностью 50% - 341,5 кг/ч (170,75 кг/ч (68,3 на 1000 т/год) – см. баланс фильтрации сиропа);
· общее количество сухих веществ в шламе нейтрализованного гидролизата (qобщ), кг/ч:
- бигидрата сульфата кальция232,45
- коллоидных и органическихвеществ53,36
- активированного угля в лепешке 170,75
- активированного угля свежего 313,86
- ИТОГО 770,42
8. Потери РВ при нейтрализации:
R1 = DPB*р/100 = 816,03*2,5/100 = 20,4 кг/ч,
где р = 2,5 – потери PB, %
Остаётся РВ после нейтрализации:
ОРВ = DPB- R1 = 816,03-20,4 = 795,63 кг/ч.
9. Поступает нейтрализата в отстойник:
Dнейтр = qр-ра+е+q = 17785,28+477,8+341,5 = 18604,58 кг/ч.
10. Общее количество абсолютно сухого шлама в отстойнике с учётом потерь РВ со шламом:
q6 = OPB*p/100 = 795,63*2,0/100 = 15,91 кг/ч,
q7 = qобщ+q6 = 773,69+15,91 = 789,6 кг/ч,
10% абсолютно сухого шлама уходит с отстойника с осветлённым нейтрализатом на фильтр-пресс:
q8 = q7*10/100 = 789,6*10/100 = 78,96 кг/ч.
Получается шлама с 65% влаги после его фильтрации:
qшлама = q7*100/(100-65) = 789,6*100/35 = 2256 кг/ч.
11. Количество воды, подаваемое на отмывку осадка, считая кратность промывки шлама равную 1 по отношению к массе шлама:
q9 = qшлама*1 = 2256 л/ч.
12. Количество фильтрованногонейтрализата:
q10 = Dнейтр+q9 –qшлама = 18604,58+2256-2256 = 18604,6 кг/ч.
13. Содержание РВ и сухих веществ в нейтрализате:
· РВ в нейтрализате:
q11 = OPB-q6 = 795,63-15,91 = 779,72 кг/ч;
· концентрация РВ в нейтрализате:
СРВN = q11*100/q10 = 779,72*100/18604,58 = 4,19 %;
· содержание кристаллизованной воды в гипсе:
qк.в. = q4*(1 – М4/М3) = 232,45*(1 – 136/172) = 48,65 кг/ч,
где М3 – молекулярная масса СаSО4*2Н2О
М4 – молекулярная масса СаSО4;
· количество сухих веществ в нейтрализате:
q12 =qСВ +qа.у. +Rакт +Ra.y.– (qобщ–qк.в.) – (R1+q6) =
= 1255,43+170,75+86,09+313,86 – (770,42–48,65)– (20,4+15,91) =
= 1068,05 кг/ч.
14. Доброкачественность нейтрализата:
F = q11*100/q12 = 770,42*100/1068,05 = 72,1%.
Сводный баланс нейтрализационного отделения и отделения фильтрации нейтрализата:
Израсходовано | Раствора, т/ч | Сухих веществ, т/ч | Получено | Раствора, т/ч | Сухих веществ, т/ч |
Гидролизата в т. ч.: РВ | 15,6929 | 1,2554 | Нейтрализата в т.ч.: РВ | 18,6046 | 1,068 |
Известкового молока в т. ч.: СаО активного | 0,4778 | 0,0861 | Шлама, за исключением безводного гипса | 2,256 | 0,7218 (qобщ–qк.в.) |
Активированного угля в нейтрализаторах | 2,0924 | 0,3139 | Потерь при нейтрализации и отстое R1+q6 | 0,0363 | |
Активированного угля в «оборотной лепешке» | 0,3415 | 0,1708 | |||
Воды на промывку шлама | 2,256 | ||||
Всего | 20,8606 | 1,8262 | Всего | 20,8606 | 1,8262 |
ЗАКЛЮЧЕНИЕ
В ходе выполнения курсового проекта были изучены технологические параметры гидролиза гемицеллюлоз пентозансодержащего сырья, приведена характеристика пентозныхгидролизатов и товарного ксилита. Представлена типовая технологическая схема гидролизно-нейтрализационного отделения производства ксилита. Рассчитан материальный баланс гидролизно-нейтрализационного отделения мощностью 2,5 тыс. тонн ксилита в год.
СПИСОК ЛИТЕРАТУРЫ
1. Холькин Ю. И. Современная технология ксилита. – М.- 1982, 56 с.
2. Холькин Ю. И. Технология гидролизных производств. Учебник для вузов.- М.: Лесная промышленность, 1989. - 496 с.
3. Шарков В. И., Сапотницкий С. А., Дмитриева О. А., Туманов И. Ф. Технология гидролизных производств.- М.: Лесная промышленность, 1973г., 408 с.
4. Ёлкин В. А. Оборудование и проектирование предприятий гидролизной и лесохимической промышленности. Учебник для вузов / Ёлкин В. А., Выродов В. А., Рябов В. В., Кречмер М. М.- М.: Лесная промышленность, 1991. – 304 с.
5. Промышленные регламент на производство кристаллического ксилита. ПР 64 – 206 – 91, 1991 – 325 с.
6. Получение углеродистых материалов и адсорбентов из целлолигнина, полученного от ксилитной варки.Бахтиярова А.В., ЁлкинВ.А.,СпицынА.А.,РощинВ.И. Известия Санкт-Петербургской лесотехнической академии. 2015. Вып. 213. С. 242–252.
7. http://www.dissercat.com/content/tekhnologiya-ochistki-gidroliznykh-sred-makroporistymi-ionitami-i-polielektrolitami-v-proizv
Дата добавления: 2018-04-15; просмотров: 1185; Мы поможем в написании вашей работы! |
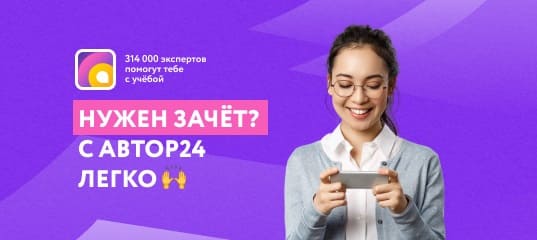
Мы поможем в написании ваших работ!