Общие сведения о производстве стали
Стальюназывается железоуглеродистый сплав, в котором содержится углерода до 2 % Как и чугун, сталь содержит также постоянные примеси (кремний, марганец, серу и фосфор), но в меньших количествах, что способствует улучшению механических и технологических свойств металла. Сталь хороша сваривается, куется, прокатывается, обрабатывается резанием и поэтому является основным материалом в промышленности
Сталь выплавляют из чугуна и лома черных металлов, из которых удаляют некоторое количество углерода и других примесей, предусмотренное ГОСТ для определенной марки стали. Удаляют примеси путем окисления их кислородом воздуха, вдуваемого в жидкий расплавленный металл.
Впервые сталь получили из чугуна в конце XVIII в. Однако способ, получивший название пудлингования, б ,.л малопроизводителен, требовал больших затрат топлива и труда. Пудлинговая печь выплавляла за сутки не более 1 т стали. В 1856 г. английский изобретатель Г. Бессемер предложил новый способ получения стали из чугуна. По его имени этот способ назвали бессемеровским. В 1878 г. английский металлург С. Томас предложил свой способ получения стали из чугуна, который также назвали по имени изобретателя — томасовским. Выплавка стали бессемеровским и томасовским способами производится в специальных сосудах, называемых конвертерами, поэтому оба предложенных способа получили общее название конвертерного способа. Производительность конвертеров намного выше производительности пудлинговых печей.
|
|
В 1864 г. французские металлурги братья П. и Э. Мартены предложили новый способ получения стали, который позволил переплавлять в сталь лом черных металлов и отходы производства (бракованные слитки и детали, отходы кузнечных и прокатных цехов, металлическую стружку и т. п.), ранее не используемые. В настоящее время более 80 % всей стали выплавляется мартеновским способом.
В 1899 г. был разработан электрический способ производства стали в электродуговых печах. Этот способ основан на применении электрической дуги (дуги Петрова), открытой в 1802 г. русским ученым В. В. Петровым.
Таким образом, в настоящее время существуют три способа производства стали: конвертерный, мартеновский и электрический.
Классификация стали.Сталь классифицируют по химическому составу, назначению и качеству.
По химическому составу сталь делится на углеродистую и легированную.
Углеродистая сталь — сплав железа с углеродом (до 2 %). Кроме железа и углерода, в состав углеродистой стали входят обычные примеси: кремний (до 0,37 %), марганец (до 0,8 %), сера (0,06 %) и фосфор (до 0,07%).
Легированными называются стали, в состав которых, кроме железа, углерода и обычных примесей, входят легирующие элементы (хром, никель, вольфрам и др.), повышающие физические, химические и механические свойства, стали. Сталь также будет легированной, если содержание в ней кремния 0,5 %, а марганца 1 %.
|
|
По назначению стали делятся на: конструкционные (общего назначения), идущие на изготовление деталей машин, приборов и элементов строительных конструкций; инструментальные, предназначенные для изготовления инструментов; стали специального назначения (нержавеющие, жаростойкие, жаропрочные, с высокой магнитной проницаемостью и др.).
По качеству стали подразделяются на стали обыкновенного качества, качественные, высококачественные (в конце марки таких сталей ставится буква А) и особовы-сококачественные (в конце марки ставится буква Ш). Качество стали зависит от способа ее производства и определяется однородностью химического состава и строения, а также другими свойствами. Основным показателем для классификации сталей по качеству является наличие в них вредных примесей (серы, фосфора, кислорода, азота и др.). Чем меньше в стали вредных примесей, тем качество ее выше.
Различают низкоуглеродистые (до 0,25 % углерода), средне-углеродистые (от 0,25 до 0,6 % углерода) и высокоуглеродистые стали (свыше 0,6 % углерода).
|
|
Кремний (до 0,5%) и марганец (до 0,7%) не оказывают существенного влияния на свойства стали. Сера вызывает красноломкость, т. е. хрупкость стали при высоких температурах, а фосфор — хладноломкость, т. е. хрупкость стали при пониженных температурах. Кроме того, сера понижает пластичность и прочность стали, коррозионную стойкость и износостойкость.
Легированные стали — это сплавы железа с углеродом—(при содержании углерода до 2 %), в которые введены специальные добавки (легирующие элементы) для придания определенных свойств, например, хром, никель, титан, молибден, вольфрам, кобальт, ниобий, ванадий, алюминий, медь и другие элементы. Марганец (при содержании более 1 %) и кремний (при содержании более 0,8 %) также являются легирующими элементами.
Для легирующих элементов, вводимых в сталь, приняты следующие условные буквенные обозначения: А — азот, Б — ниобий, В — вольфрам, Г — марганец, Д — медь, Е — селен, К—кобальт, Л — бериллий, М—молибден, Н — никель, П — фосфор, Р — бор, С — кремний, Т —титан, Ф — ванадий, X — хром, Ц — цирконий, Ю — алюминий.
Легирующие элементы оказывают различное влияние на свойства стали.
|
|
Хром, один из основных легирующих элементов, повышает прочность, твердость, коррозионную стойкость стали, а при повышенном содержании делает сталь нержавеющей, жаропрочной и обеспечивает стойкость магнитных свойств.
Никель придает стали высокую прочность, пластичность, коррозионную стойкость и ударную вязкость.
Вольфрам увеличивает твердость и красностойкость стали.
Молибден повышает прочность, упругость, красностойкость, окалиностойкость и коррозионную стойкость стали.
Кобальт увеличивает жаропрочность, магнитные свойства и ударную вязкость стали.
Ванадий повышает твердость и прочность стали, измельчает зерно.
Титан увеличивает прочность и плотность стали, измельчает зерно, улучшает коррозионную стойкость.
Марганец увеличивает прочность, твердость и износостойкость стали.
Кремний повышает прочность, упругость, кислотостойкость, окалиностойкость и жаропрочность стали.
Ниобий и медь улучшают коррозионную стойкость стали)
Различают низколегированные стали (до 5 % легирующих элементов), среднелегированные (от 5 до 10%) и высоколегированные (свыше 10%).
![]() |
о назначению стали разделяют на конструкционные, инструментальные и специальные.
Конструкционн ые стали применяют для изготовления строительных конструкций, деталей, машин и механизмов, корпусов судов и т. п. [
Инструментальные стали предназначены для изготовления режущего, мерительного, штампового и другого инструмента.
Специальные стали имеют особые свойства обрабатываемости, жаростойкости, коррозионной стойкости и т. п. Большинство специальных сталей используется для изготовления конструкций, деталей машин и механизмов, имеющих__ специальное назначение.
По качеству стали разделяют на стали обыкновенного качества, качественные, высококачественные и особовысококачественные.
Под качеством стали понимают совокупность свойств, определяемых металлургическим процессом ее производства.
Основным показателем качества служат нормы содержания вредных примесей (серы и фосфора).Cтали обыкновенного качества содержат до 0,06 % серы и 0,07% фосфора, качественные — не более 0,04 % серы и 0,035 % фосфора, высококачественные — не более 0,025 % серы и 0,025 % фосфора, особовысококаченные — не более 0,015% серы и 0,025% фосфора.
По степени раскисления стали разделяют на кипящие, полуспокойные и спокойные. Углеродистые стали могут выплавляться кипящими, полуспокойными и спокойными, а легированные — только спокойными.
По структуре стали в отожженном состоянии разделяют на шесть классов: доэвтектоидные, эвтектоидные, заэвтектоидные, ледебуритные, аустенитные и ферритные.
По структуре после нормализации стали разделяют на четыре класса: перлитный, мартенситный, аустенитн ы й и ферритный.
Для постройки судов применяют сталь всех вышеперечисленных групп. Например, из конструкционной стали строят корпуса металлических судов, изготовляют дельные вещи, судовые устройства, судовое механическое оборудование и т. д. Из инструментальных сталей делают инструменты и приспособления, необходимые для постройки судна, из специальных сталей — судовую . арматуру, гребные винты, детали судовых двигателей, механизмы и приборы.
Судно эксплуатируется в тяжелых условиях, при которых на его корпус действуют знакопеременные силы сжатия, растяжения, излома, кручения и др. Поэтому к корпусным судостроительным сталям, которые должны обеспечить прочность, надежность и долговечность судовых конструкций, предъявляются особые требования. Согласно требованию Регистра СССР и зарубежных классификационных обществ сталь для постройки судов должна обладать повышенной вязкостью, пластичностью и хорошей свариваемостью, иметь необходимую прочность и стойкость против возникновения трещин.
В зависимости от химического состава и механических свойств Правила Регистра СССР делят корпусную сталь на две группы.
Обычная судостроительная сталь (нормальной прочности)— это углеродистая сталь, у которой предел текучести составляет не менее 240 МПа. По Правилам Регистра СССР (а также других ведущих классификационных обществ) она делится на четыре категории: А, В, D, Е. Химический состав и механические свойства обычной судостроительной стали охарактеризованы в табл. 14.1
2. Судостроительная сталь повышенной прочности — это низколегированная сталь, у которой предел текучести более 300 МПа. По Правилам Регистра СССР (и некоторых других классификационных обществ) она делится на категории А32, D32. Е32, А36, Е36, Е36, D40, Е40. Цифры в обозначении категории стали соответствуют ее пределу текучести в килограмм- силах па квадратный миллиметр.
Химический состав и механические свойства этой стали представлены в табл. 15.
Основным нормативным документом для корпусной судостроительной стали является ГОСТ 5521—76 «Сталь, свариваемая для судостроения». Он распространяется на свариваемую углеродистую и низколегированную листовую и профильную сталь, предназначенную для изготовления корпусов и других конструкций судов.
Дата добавления: 2018-04-05; просмотров: 2017; Мы поможем в написании вашей работы! |
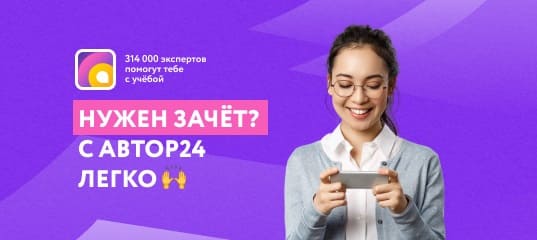
Мы поможем в написании ваших работ!