Тема №11. «Литейное производство»
Литье, виды литья, используемое оборудование, виды брака при разливке
Общие сведения о разливке стали
Разливка стали — завершающий этап сталеплавильного процесса. Это сложный и ответственный процесс, от которого зависит качество металла (его газонасыщенность, количество и характер неметаллических включений, химическая неоднородность, структура, качество поверхности слитков и прокатанных из них заготовок). При разливке стали протекают сложные физико-химические процессы и реакции, которые в итоге определяют качество металла (стали) и технико-экономические показатели работы металлургического передела предприятия.
Кратковременность этой технологической операции и связанное с нею непрерывное понижение температуры металла требуют точного соблюдения технологии. При несоблюдении технологии, даже из стали высокого качества можно получить слитки с такими дефектами, которые при прокатке вызывают повышенный расход металла или брак.
Способы разливки стали
В сталеплавильных цехах металлургических и машиностроительных предприятий применяются три способа разливки стали:
— разливка в слитки сверху («дождевая» разливка);
— разливка в слитки снизу («сифонная» разливка);
— разливка в водоохлаждаемые кристаллизаторы машин непрерывного литья передельных заготовок (трубных, сортовых и листовых).
Последний способ (способ непрерывной разливки) обладает целым рядом преимуществ по сравнению со способом разливки стали в изложницы и поэтому он находит все более широкое распространение в сталелитейном производстве.
|
|
Выбор способа разливки стали в изложницы зависит от массы и необходимого количества слитков. Если требуется получить много слитков, относительно, малой массы, то целесообразно применить сифонный способ разливки. При выборе способа разливки стали в изложницы учитывают также требования, предъявляемые к поверхности и структуре слитков, пропускной способности участков подготовки изложниц и разливки стали, наличию и мощности средств для удаления (зачистки) дефектов с поверхности слитков в прокатных цехах.
Преимущества разливки снизу:
— возможность, сравнительно, непродолжительной по времени одновременной разливки в мелкие слитки плавок большой массы;
— низкая скорость заполнения изложницы металлом обеспечивает увеличение глубины залегания подкорковых сотовых пузырей;
— отсутствие брызг жидкой стали при разливке обеспечивает получение более чистой поверхности слитков;
— из-за меньшей длительности разливки и меньшего количества циклов работы стопором или шибером сталеразливочного ковша, повышается стойкость футеровки ковша, стопорных механизмов и их межремонтный период;
|
|
— создаются условия для визуального наблюдения за поведением поднимающего в изложнице металла, соответственно, чему выполняется регулировка скорости разливки стали.
Недостатки разливки снизу:
— сложность, трудоемкость и дороговизна оборудования разливки;
— потери металла в литниковой системе (до 2%);
— более высокая начальная температура металла в ковше, необходимая для того, чтобы сталь не охлаждалась в литниковой системе - в каналах сифонного, кирпича (сифонного припаса).
Практика показала, что стали широкого потребительского назначения экономичнее разливать в слитки сверху, хотя дефекты разливки и кристаллизации слитка (прямые потери металла) лежат в пределах (15.. .25)%. Сифонной же разливкой получают только мелкие слитки для прокатных станов старой конструкции, а также для кузнечно-прессового производства. При сифонной разливке качественных марок стали резко сокращаются потери металла при разливке и зачистке перед прокаткой.
Скрап и недоливки (маломерные слитки из остатков стали в ковше) при разливке сверху составляют (0,5.. .2)%.
Оборудование для разливки стали сверху.
|
|
Из мартеновских и сталеплавильных печей сталь в сталеразливочные ковши поступает по выпускным желобам, из конверторных — через стальную летку.
Сталеразливочный ковш (рис. 11.1) — это футерованная изнутри емкость, в которую выпускают сталь из печи. Ковш может вмещать до 500т металла (сталь и сверху — слой шлака — до 5% общей массы металла). Шлак теплоизолирует металл в ковше.
Рис. 11.1. Сталеразливочный ковш.
1 – механизм перемещения стопора; 2 – стопор; 3 – огнеупорные «катушки»; 4 – «пробка» стопора; 5 – гнездовой кирпич; 6 – «стакан»; 7 – листовой асбест; 8 – шамотный кирпич;
Кожух ковша изготовлен электросваркой стальных листов толщиной до 30 мм. Обычно, сталеразливочные ковши имеют форму усеченного конуса, с широким основанием в верхней части. Корпус ковша снабжен ребрами жесткости и стальным поясом с цапфами для транспортировки электромостовыми кранами.
Ковши предназначены не только для вмещения плавки стали, но и для ее выдержки, во время которой завершаются физико-химические процессы, определяющие в последующем, качество металла (раскисление, легирование, обработка синтетическими шлаками, внепечная обработка инертными газами, вакуумирование и другие процессы).
|
|
Сталеразливочный ковш вместимостью 300т имеет размеры: 4,02 х 5,3 м; толщина футеровки — 320 мм.
Изнутри ковш футерован листовым асбестом (7) и двумя - тремя слоями огнеупорного кирпича (8).
Футеровка ковша — шамотная (из штучного кирпича) или монолитная (набивная) из кремнеземистой массы. Арматурный слой футеровки — шамот имеет стойкость 1,5 года, тогда как рабочий слой — (10.. .20) плавок. Применяется торкретирование разрушающегося рабочего слоя футеровки ковша. Стойкость монолитной футеровки — до 40 плавок, а расход огнеупоров (2.. .4) кг/т стали.
Торкретирование, пескометание устраняет тяжелый и непроизводительный труд каменщиков-огнеупорщиков сталеплавильных производств.
Выпуск стали из ковша производится через его днище. Эта часть выполняется из более толстого стального листа, чем корпус ковша. Дно имеет одно (или два) отверстия для установки сталеразливочных огнеупорных стаканов (6), представляющих собой полый усеченный конус для прохода стали. Диаметр сталевыпускного отверстия изменяется в пределах (50... 120) мм и оказывает определяющее влияние на скорость наполнения изложниц сталью, брызги струи стали, качество поверхности слитка и толщину первоначально застывающей «корочки» на поверхности слитка. Скоростные разливки стали осуществляются через стаканы с диаметром внутреннего отверстия (100... 120) мм.
Для закрывания и открывания отверстия стакана служит вертикальный стопор (2), представляющий собой металлический стержень, защищенный от жидкой стали шамотными трубками-«катушками» (3). Снизу стержень имеет резьбу и на нее навинчивается огнеупорная «пробка» (4), сферическая поверхность которой при установке стопора в ковш притирается к вогнутой поверхности «стакана» (6) с таким расчетом, чтобы в закрытом положении стопора, жидкая сталь из ковша не могла пройти между «пробкой» и «стаканом» (т.е. выливаться из ковша через его днище).«Стопор» и «стакан» служат только одну разливку плавки и их устанавливают заново перед каждой плавкой.
Для выпуска стали через дно ковша, стопор немного поднимают вверх (вертикально) гидравлическим механизмом (1). В кольцевой зазор, образовавшийся между «пробкой» стопора (4)и «стаканом» (6) вытекает сталь, которая плотной тяжелой струей падает в емкость (промежуточный ковш для одновременного наполнения сталью двух изложниц, или в центровую трубу с приемной воронкой при сифонной разливке, или в одну изложницу при одностопорной разливке стали сверху). Механизм привода стопора может быть и электромеханическим, однако, разливщик может управлять им вручную.
При одностопорной разливке в изложницы сверху очень важно постепенно открывать сталеразливочное отверстие ковша на полное сечение, а к концу наполнения изложницы начинать перекрывать отверстие. Этот технологический прием создает условия для улучшения качества поверхности слитка. В ковшах с двумя стопорамисокращается время разливки стали и при этом повышается качество поверхности слитков и стойкость футеровки промежуточного или сталеплавильного ковшей.
Промежуточный ковш емкостью до 35 т применяется для одновременной разливки стали из ковша не в одну, а в большее количество изложниц. Он имеет, соответствующее количество стопоров. Применение промежуточных ковшей при разливке стали сверху уменьшает нежелательный эффект разбрызгивания струи стали при ее ударе о дно (поддон) изложницы. Промежуточный ковш футеруется шамотным кирпичом.
Следует особо отметить, что тщательность и аккуратность выполнения работ по подготовке, установке и эксплуатации ковшевого (в т.ч. и стопорного хозяйства) служит залогом безаварийной работы на участке разливки стали.
В последнее время (в т.ч. и на ОЭМК) стопорное устройство заменяется шиберным затвором (рис. 11.2).
Рис. 11.2. Шиберный затвор
1 - сталеразливочный «стакан»; 2 - основание затвора; 3 - неподвижная шиберная плита (верхняя плита); 4 - подвижная шиберная плита (нижняя плита); 5 - опорный фланец; 6 – коллектор; 7 - гидропривод шибера.
Бесстопорная разливка стали обеспечивается установкой на днище сталеразливочного ковша оборудования со скользящим затвором (шибера). Основной узел шиберного затвора состоит из двух огнеупорных плит (3 и 4) изготовленных из высокоогнеупорного оксида магния. Поверхности плит хорошо пришлифованы друг к другу и смазаны графитовой смазкой. Сдвигом нижней подвижной плиты (4), относительно неподвижной верхней (3) при помощи гидроцилиндра (7), осуществляется полное или частичное перекрытие сталеразливочного отверстия. Шиберный затвор надежно работает только при тщательной подгонке плит и контакте их во время разливки стали. Диаметр отверстий в плитах шиберных затворов кислородно-конверторного цеха НЛМК составляет (70. . .90) мм, рабочее давление в гидросистеме (7. . .20) МПа.
Шиберный затвор может быть полностью закрыт (рис. 11.2 а), а при сдвигании нижней плиты (4) открывается сталеразливочное отверстие (рис. 11.2 б) - стакан. Затвор управляется разливщиком дистанционно с пульта управления разливкой. Через одно шиберное устройство можно разлить три-четыре плавки (с налива) стали (до 800 т).
После выпуска стали из ковша, на его дне остается слой шлака, и ковш «кантуют» (переворачивают) электромостовым (сталеразливочным краном), полностью сливая шлак. Сталевыпускное отверстие шиберного затвора продувают сжатым воздухом, если оно залито шлаком, или выжигают кислородной трубкой, если в затворе застыла сталь.
Перед заполнением ковша сталью, «стакан»(1) заполняют кварцевым песком, а перед началом разливки стали шиберный затвор открывают над пустой емкостью («шлаковней») и выпускают в нее песок и немного стали, после чего приступают к нормальной разливке по любому технологическому варианту.
Дата добавления: 2018-04-05; просмотров: 1025; Мы поможем в написании вашей работы! |
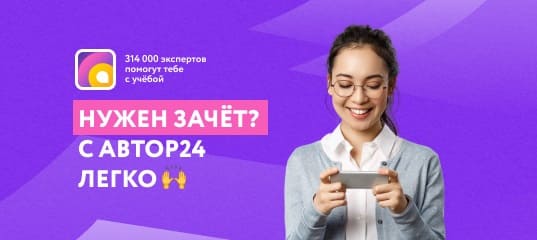
Мы поможем в написании ваших работ!