Метод продувки инертными газами
Для повышения качества металла получил промышленное распространение по мере освоения технологии получения дешевого аргона в больших количествах (как сопутствующего продукта при производстве кислорода, как известно, в воздухе ~ 1 % Аг). На кислородных станциях аргон выделяют при ректификации жидкого воздуха. Если завод имеет мощную кислородную станцию, то объем попутно получающегося аргона достаточен для обработки больших количеств стали. В тех странах, где имеются запасы гелия, для продувки используют также гелий.
Рис.10.10. Фурма в виде «ложного стопора» для вдувания порошкообразных реагентов в металл.
Для продувки металла, не содержащего нитридообразующих элементов (хрома, титана, ванадия и т.п.), часто используют азот, т.к. при 1550-1600 °С процесс растворения азота в жидком железе не получает заметного развития. Расход инертного газа составляет обычно 0,1-3,0 м3/т стали. В зависимости от массы жидкой стали в ковше снижение температуры стали при таком расходе аргона составляет 2,5-4,5 °С/мин (без продувки металл в ковше охлаждается со скоростью 0,5-1,0 °С/мин). Тепло при продувке дополнительно затрачивается на нагрев инертного газа и излучение активно перемешиваемыми поверхностями металла и шлака. Большая часть тепловых потерь связана с увеличением теплового излучения, поэтому такой прием, как накрывание ковша крышкой при продувке позволяет заметно уменьшить потери тепла; при этом одновременно снижается степень окисления обнажающегося при продувке металла. Простым и надежным способом подачи газа является использование так называемого ложного стопора (рис. 10.10). Продувочные устройства типа ложного стопора безопасны в эксплуатации, так как в схему футеровки ковша не нужно вносить никаких изменений, но они обладают малой стойкостью. В результате интенсивного движения металл-газовой взвеси вдоль стопора составляющие его огнеупоры быстро размываются.
|
|
Большое распространение получил способ продувки через устанавливаемые в днище ковша пористые огнеупорные вставки или пробки (рис. 10.11); в тех случаях, когда продувку проводят одновременно через несколько пробок (вставок), эффективность воздействия инертного газа на металл существенно увеличивается.
Рис.10.11.Конструкция пористой пробки(вставки) для продувки металла аргоном:
1-вставка с каналами для прохода газов; 2-огнеупорный корпус;3-гнездовой кирпич
Продувка с расходом газа до 0,5 м3/т стали достаточна для усреднения химического состава и температуры металла; продувка с интенсивностью до 1,0 м3/т влияет на удаление из металла неметаллических включений; для эффективной дегазации необходим расход инертного газа 2-чЗм3/т металла.
|
|
Во многих случаях продувку инертным газом проводят одновременно с обработкой металла вакуумом. В этом случае расход инертного газа может быть существенно уменьшен. Совмещение продувки инертным газом обработкой шлаком способствует повышению эффективности использования шлаковых смесей, так как интенсивное перемешивание при продувке увеличивает продолжительность и поверхность контакта металла со шлаком. Если при этом ковш, в котором осуществляется такая обработка, накрыт крышкой, то наличие в пространстве между крышкой и поверхностью шлака атмосферы инертного газа предохраняет металл от окисления, а снижение потерь тепла позволяет увеличить продолжительность контакта металла с жидким шлаком. На этом принципе основана разработанная на одном из заводов Японии технология так называемого САВ-процесса (от слов Capped-Argon-Bubb- ling) (рис. 10.12); данная технология предусматривает наличие на поверхности металла в ковше синтетического шлака заданного состава.
В тех случаях, когда из плавильного агрегата в ковш попадает какое-то количество конечного окисленного шлака (например, при выпуске плавки из конвертера), используют метод, названный металлургами Японии SAB-процессом (рис. 10.13).
|
|
Введение в металл добавок в нейтральной атмосфере и хорошее их усвоение при перемешивании металла инертным газом обеспечивается в несколько усложненном способе защиты зоны продувки, названном CAS-процессом.
По этому способу в ковш сверху вводят огнеупорный колпак, закрытый снизу расплавляющимся металлическим конусом, таким образом, чтобы внутрь этого колпака не попал шлак; затем снизу под колпак подают аргон.
Рис.10.12.Схема САВ-процесса:
1-ковш с металлом; 2-крышка ковша;3-устройство для загрузки ферросплавов;
4-отверстие для отбора проб; 5-синтетический шлак;6-шиберный затвор;7-пористая пробка для введения аргона
Рис.10.13. Схема SАВ-процесса:
1-подача флюсов и добавок; 2-синтетический шлак; 3-окислительный конечный шлак.
Аргонокислородная продувка.
Влияние продувки металла инертным газом на уменьшение парциального давления монооксида углерода, образующегося при окислении углерода, использовано при разработке такого процесса, как аргонокислородное обезуглероживание или аргонокислородное рафинирование (АКР) .
При продувке металла кислородом равновесие реакции [С] + 1/2О2(г) = СОг определяется парциальным давлением кислорода и образующегося монооксида углерода. Продувая металл смесью кислорода с аргоном, мы добиваемся "разбавления" пузырей СО аргоном и соответствующего сдвига вправо равновесия реакции. Окислительный потенциал газовой фазы при этом достаточен для проведения реакций окисления примесей ванны.
|
|
Для осуществления процесса аргонокислородного рафинирования создан агрегат, обычно именуемый AOD-конвертер (рис.10.14). Конструкция фурм для подачи смеси аргона и кислорода позволяет в широких пределах регулировать соотношение О2:Аг; при этом соответственно меняется окислительный потенциал вдуваемой газовой смеси, вплоть до продувки одним аргоном (обычно в заключительной стадии плавки). Если при этом продувку вести под высокоосновным шлаком, обеспечивается также эффективная десульфурация расплава.
Сравнительная простота организации аргонокислородной продувки, высокая производительность агрегатов и возможность изменять в широких пределах окислительный потенциал газовой фазы (отношение О2: Аг) приводят к непрерывному расширению сферы распространения этого метода. Этот метод используют для производства не только коррозионностойких, но также и электротехнических, конструкционных и других сталей. Этот метод позволяет получать в конвертере высокохромистые стали непосредственно из чугуна с использованием в качестве шихтового материала хромистой руды. Жидкий чугун подвергают внедоменной обработке (обескремниванию, дефосфорации), после чего заливают в конвертер. В процессе продувки в конвертере осуществляют обезуглероживание, десульфурацию и легирование хромом. Часть хрома вводят в металл с феррохромом, а часть - с хромистой рудой, оксиды которой восстанавливаются углеродом чугуна.
Рис.10.14. Кострукция конвертера для аргонокислородной продувки (АКР-процесс;AOD-процесс)
На одном из заводов Японии организовали производство коррозионностойкой стали из расплава никелевых и хромистых руд. Никелевую руду с высоким содержанием железа подвергают дроблению, обогащению и предварительному нагреву в смеси с углеродистым восстановителем и в нагретом (~1000 °С) состоянии загружают в рудовосстановительную печь, в которой получают расплав с 13—15 % Ni.
Хромистую руду также подвергают предварительной обработке и в нагретом (~500 °С) состоянии загружают в рудовосстановительную печь, в которой получают расплав с 40-43% Сг. Расплавы смешивают в ковше и заливают в конвертер, в котором подвергают аргонокислородной продувке для получения специальных высокохромистых никельсодержащих коррозионностойких сталей.
По сравнению с известным способом получения таких сталей из скрапа по схеме дуговая электропечь — конвертер аргонокислородной продувки затраты энергии в новом процессе ниже, содержание неметаллических включений и азота меньше, поскольку используют первородную шихту и не происходит образование атомарного азота в зоне продувки.
Обработка стали шлаками
В тех случаях, когда основную роль в удалении примеси выполняет шлаковая фаза, скорость процесса пропорциональна величине межфазной поверхности шлак—металл, интенсивности и продолжительности перемешивания металла и шлака. На практике используют ряд технологий. Одна из них-использование высокоосновного и малоокисленного конечного шлака электроплавки. Если при этом в электропечи расплавить лигатуру и смешать ее (вместе с таким шлаком) с металлом, выплавленном в конвертере или мартеновской печи, получается так называемый "совмещенный" процесс (рис. 10.15).
Рис.10.15. Схема совмещенного процесса раскисления, легирования и рафинирования стали.
Падая с большой высоты в ковш, струя металла энергично премешивается с лигатурой и высокоосновным, раскисленным шлаком, происходит раскисление, легирование и десульфурация стали.
Во многих случаях в электропечах просто расплавляют один шлак (основные составляющие СаО и А12О3) и этим шлаком обрабатывают сталь, выплавленнную в конвертере, мартеновской или электропечи. Операция называется "обработка металла синтетическим шлаком" (СШ). Такой метод обработки металла был предложен в 1925-1927 гг. нашим соотечественником инж. А.С.Точинским.
В тех случаях, когда по условиям производства нет возможности разместить оборудование для расплавления синтетического шлака, используют метод обработки металла твердыми шлаковыми смесями (ТШС). Обычно в состав таких смесей входят СаО, CaF2, алюминиевая стружка и т.п. Эффективность использования ТШС, естественно, ниже, чем жидких СШ. Основное требование к составам ТШС и СШ- минимум оксидов железа (для обеспечения максимального обессеривающего эффекта).
При обработке металла синтетическим шлаком такого состава (высокая основность и низкая окисленность) протекают следующие процессы:
1. Десульфурация. Обычно после обработки шлаком содержание серы в металле снижается до 0,002—0,010 %.
2. Раскисление. Окисленность металла снижается (в полтора—два раза).
3.Удаления неметаллических включений. В тех случаях, когда межфазное натяжение на границе капля синтетического шлака - неметаллическое включение δс.ш-вкл меньше, чем межфазное натяжение на границе металл – неметаллическое включение δМ-вкл т.е. при δс.ш-вкл < δМ-вкл капли синтетического шлака будут рафинировать металл от включений (капли шлака, всплывая, уносят неметаллические включения). Соотношение между величинами δс.ш-вкл и М-вкл зависит от состава включений. Практика показала, что общее содержание неметаллических включений после обработки синтетическим шлаком уменьшается примерно в два раза. При проведении операции обработки металла шлаком приходится учитывать нежелательность попадания в ковш, в котором производится обработка, вместе с металлом также и шлака из печи или из конвертера.
Дата добавления: 2018-04-05; просмотров: 1199; Мы поможем в написании вашей работы! |
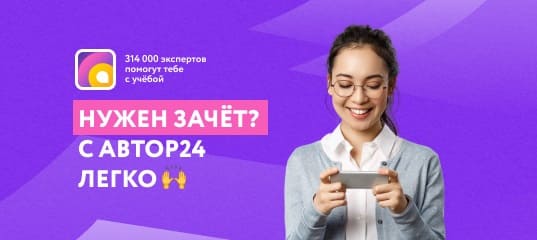
Мы поможем в написании ваших работ!