МЕТОДЫ ПОВЫШЕНИЯ НАДЁЖНОСТИ ТЕХНИЧЕСКИХ СИСТЕМ
Общие положения. Все методы повышения надёжности технических средств систем сводятся к следующим видам:
- резервирование;
- уменьшение интенсивности отказов технических средств;
- сокращение времени непрерывной работы;
- уменьшение среднего времени восстановления.
Реализация указанных методов может осуществляться либо при проектировании, либо при изготовлении, либо в процессе эксплуатации технических средств.
Уменьшить среднее время восстановления можно, повышая надёжность технических систем и тем самым, уменьшая число отказов, или сокращая время, необходимое для отыскания и устранения отказов. Сократить время, необходимое для отыскания и устранения неисправностей, можно, применяя встроенный контроль, автоматизацию проверок, повышение квалификации обслуживающего персонала, сбор и обобщение опыта эксплуатации.
Уменьшить время непрерывной работы объектов можно в том случае, если имеется возможность выключать объекты на определённые промежутки времени.
Среди разнообразных методов повышения надёжности систем необходимо выделить три группы: доэксплуатационные, производственные и эксплуатационные.
В доэксплуатационных (т.е. при проектировании) мероприятиях по повышению надёжности можно выделить следующие группы: системные методы, схемные методы, конструктивные методы.
К системным методам относятся организационно-экономические мероприятия по стимулированию повышения надёжности и технические мероприятия. К числу таких мероприятий относятся: выбор и обоснование принципов технического обслуживания, выбор основного показателя надёжности, назначение норм надёжности, распределение норм надёжности системы по элементам, составление программы обеспечения надёжности. Содержание этих связанных мероприятий во многом зависит от конечной цели, которую стремятся достигнуть. При этом необходимо так сбалансировать затраты на разработку и проектирование изделий с затратами на их эксплуатацию, чтобы общая сумма затрат не превышала заданную при обеспечении наилучших технических характеристик изделий.
|
|
Схемные методы объединяют мероприятия по повышению надежности объектов путем совершенствования принципов построения этих объектов.
К конструктивным методам относятся мероприятия по созданию и подбору элементов, созданию благоприятных режимов работы, принятию мер по облегчению ремонта и т.д. Обычно более надежными оказываются те элементы, которые не имеют перемещающихся деталей, накаливаемых нитей и тонких обмоток.
Выше упоминалось, что отказы в основном являются следствием наличия «слабых» элементов со скрытыми пороками. Иначе говоря, одна из основных причин появления отказов состоит в разбросе значений качества элементов. Поэтому значительную часть производственных мероприятий по повышению надежности элементов и систем составляют мероприятия по улучшению однородности выпускаемой продукции. Все эти мероприятия можно свести в четыре группы: совершенствование технологии производства, автоматизация производства, технологические (тренировочные) прогоны, статистическое регулирование качества продукции. Все эти мероприятия взаимно связаны между сабой.
|
|
Совершенствование технологии производства является одной из сторон общего прогресса науки и техники. В большинстве отраслей промышленности технический прогресс является сравнительно медленным, постепенным процессом. Все мероприятия в этой области опираются не только на последние достижения науки, но и в значительной мере на накопленный опыт производства продукции. Борьба за совершенствование технологии производства с целью получения однородной (т.е. надежной) продукции может быть успешной только в том случае, если она охватывает все стадии производственного процесса от получения сырья до сборки и регулировки систем.
|
|
Автоматизация производства обеспечивает высокую степень однородности продукции, а следовательно, и высокую надежность изделий. Например, в изготовляемых вручную трансформаторах часто происходят обрывы тонких обмоток. Автоматизация этого процесса обеспечивает равномерное натяжение провода при намотке, из-за чего число обрывов резко сокращается.
Технологические (тренировочные) прогоны производятся с целью выявления скрытых производственных дефектов и причин их возникновения. Кроме тренировочных прогонов в условиях, близких к эксплуатационным, могут применяться ускоренные прогоны с тяжелыми условиями работы. В последнем случае усложняется вопрос о выборе режима и длительности прогона, которые должны быть такими, чтобы полностью удалить «слабые» элементы и вместе с тем не ухудшать качество «нормальных» элементов. Такая жесткая тренировка применяется редко.
Выявлено, что в начальный период эксплуатации, характеризуемый повышенным числом отказов (период приработки), в основном отказывают механические и электромеханические узлы, проявляются дефекты монтажа, сборки, регулировки. Эти отказы удается выявить в процессе прогона при вибрационных нагрузках на включенное под электрическую нагрузку изделие. Введение тренировочных прогонов в технологический процесс производства позволяет сократить расходы заводов-изготовителей на гарантийные ремонты. Может быть установлена продолжительность прогона из условия, чтобы суммарные затраты завода-изготовителя на проведение технологического прогона и на ремонты или замены в течение гарантийного срока были бы минимальными.
|
|
Статистическое регулирование качества продукции также значительно повышает однородность продукции. Основная идея статистического регулирования качества состоит в следующем. Причины, вызывающие отклонения качества продукции, разбиваются на две группы. Одна из них – группа случайных причин – считается недоступной воздействию человека вследствие многочисленных причин и ничтожности каждой из них. Помимо случайных величин, которые всегда существуют в любом производстве, иногда могут появляться «определимые причины», которые могут быть устранены путем сознательного вмешательства в технологический процесс. Если все определимые причины устранены и остались только постоянная группа случайных причин, то дальнейшего даже незначительного повышения качества продукции можно добиться лишь путем полной перестройки производства, что, как правило, требует очень больших затрат. Поэтому в производстве допускается лишь постоянная система случайных причин, а всякого рода определимые причины устраняются. При этом определимые причины выявляются путем применения статистических методов оценки качества. Так как постоянная группа причин проявляется в постоянном разбросе характеристик качества, то все дело сводится к наблюдению за постоянством разброса значений показателей качества.
Наиболее эффективными и многочисленными методами повышения надёжности, являются методы, которые применяются при проектировании технических средств. К таким методам относятся:
- резервирование;
- выбор наиболее надежных элементов;
- создание схем с ограниченными последствиями отказов элементов;
- облегчение электрических, механических, тепловых и других режимов работ эле
ментов;
- стандартизация и унификация элементов и узлов;
- встроенный контроль;
- автоматизация проверок.
Эффективность этих методов состоит в том, что они принципиально позволяют из малонадёжных элементов строить надёжные объекты и системы. Эти методы позволяют уменьшить интенсивность отказов объектов и систем, уменьшить среднее время их восстановления и время непрерывной работы.
Дата добавления: 2018-04-05; просмотров: 1420; Мы поможем в написании вашей работы! |
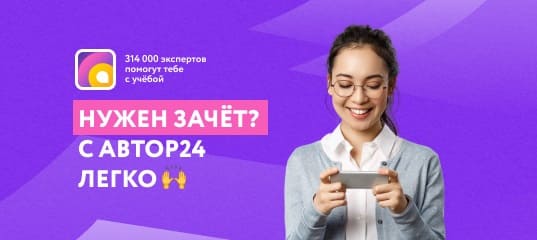
Мы поможем в написании ваших работ!