Методы испытаний добавок, придающих бетонам и растворам
Специальные свойства
10.1 Испытание противоморозных добавок
10.1.1 Испытание противоморозных добавок для «холодного» бетона и раствора
10.1.1.1 Эффективность действия противоморозных добавок для «холодного» бетона и раствора оценивают сравнением прочности бетонов и растворов основных составов, твердевших при заданной отрицательной температуре, с прочностью бетона и раствора контрольного состава, твердевшего в нормальных условиях.
10.1.1.2 Марка по удобоукладываемости контрольного и основных составов бетонной смеси должна быть П3, растворной смеси – 2.
10.1.1.3 Из смесей отбирают пробы для изготовления образцов для испытания на прочность при сжатии (для одной партии).
10.1.1.4 Образцы бетона изготавливают и испытывают на сжатие по ГОСТ 10180, раствора − по ГОСТ 5802.
10.1.1.5 Образцы контрольного состава должны в течение 28 суток твердеть в нормальных условиях, после чего должны быть испытаны на сжатие.
10.1.1.6 Образцы основных составов непосредственно после изготовления должны быть помещены на 28 суток в морозильную камеру с заданной отрицательной температурой (соответствующей виду и рекомендуемой дозировке испытываемой добавки). В морозильной камере
образцы укладывают на стеллажи так, чтобы расстояние между образцами, а также между образцами и стенками камеры было не менее 50 мм. Образцы должны быть испытаны на сжатие
после оттаивания на воздухе при температуре 20 ± 2
в сроки, указанные в нормативном или техническом документе на добавку конкретного вида.
|
|
10.1.1.7 Изменение прочности бетонов основных составов по сравнению с контрольным составом ∆R, %, определяют по формуле
R
*100, , (11)
Где − прочность бетонов или растворов основных и контрольного составов в возрасте 28 суток, МПа.
10.1.2 Испытание противоморозных добавок для «теплого» бетона и раствора
10.1.2.1 Эффективность действия противоморозных добавок для «теплого» бетона и раствора оценивают сравнением прочности бетонов и растворов основных составов, твердевших по режиму, указанному в 10.1.2.6, с прочностью контрольного состава, твердевшего в нормальных условиях.
10.1.2.2 Марка по удобоукладываемости контрольного и основных составов бетонной смеси должна быть П3, растворной смеси – 2.
10.1.2.3 Из смесей контрольного и основных составов отбирают пробы для изготовления образцов для испытания на прочность при сжатии (для одной партии).
10.1.2.4 Образцы бетонов изготавливают и испытывают на сжатие по ГОСТ 10180, растворов − по ГОСТ 5802.
10.1.2.5 Образцы контрольного состава должны твердеть в нормальных условиях в течение 28 суток, после чего они должны быть испытаны на сжатие.
|
|
10.1.2.6 Образцы основных составов непосредственно после изготовления должны быть помещены на 4 часа в морозильную камеру с заданной отрицательной температурой (соответствующей виду и рекомендуемой дозировке испытываемой добавки). В морозильной камере образцы укладывают на стеллажи так, чтобы расстояние между образцами, а также между образцами и стенками камеры было не менее 50 мм. Последующее твердение образцов должно осуществляться в нормальных условиях в течение 28 суток, после чего они должны быть испытаны на сжатие.
10.1.2.7 Изменение прочности основных составов по сравнению с прочностью контрольного состава ∆R, %, определяют по формуле (11).
10.1.2.8 Бетоны с противоморозными добавками должны быть испытаны на коррозионное воздействие добавок на бетон или раствор в соответствии с приложением А.
10.2 Испытание гидрофобизирующих добавок
10.2.1 Эффективность действия гидрофобизирующих добавок оценивают по степени уменьшения водопоглощения бетонов и растворов основных составов по сравнению с контрольным составом и по гидрофобизирующей способности добавок. Гидрофобизирующую способность добавок определяют по ГОСТ 10834, подраздел 3.4.
10.2.2 При определении водопоглощения бетонов и растворов контрольного и основныхсоставов марка по удобоукладываемости смеси должна быть П3 для бетонной смеси, 2 – длярастворной смеси.
|
|
10.2.3 Образцы бетона изготавливают и испытывают на водопоглощение
по ГОСТ 12730.3, раствора – по ГОСТ 5802.
10.2.4 Твердение бетонов и растворов с гидрофобизирующими добавками проводят по режиму, указанному в нормативном или техническом документе на добавку конкретного вида.
10.2.5 При испытании на водопоглощение образцы контрольного состава выдерживают в воде до полного насыщения, основных составов – в течение 28 суток. Уменьшение водопоглощенияПw вычисляют по формуле
, (12)
где – водопоглощение образцов контрольного состава, % по массе;
− водопоглощение образцов основного состава, % по массе.
Приложение А
(обязательное)
Определение коррозионного воздействия противоморозных добавок на бетоны и растворы
Испытание в соответствии с настоящим приложением проводят в случае предполагаемо-
го коррозионного воздействия противоморозных добавок на бетоны или растворы.
А.1 Средства испытания
Морозильная камера, обеспечивающая достижение и поддержание заданной отрица-
тельной температуры.
|
|
Сетчатый стеллаж для размещения образцов-балочек в морозильной камере.
Формы для изготовления образцов-балочек размером 4×4×16 см по ГОСТ310.4.
А.2 Порядок подготовки и проведения испытания
А.2.1 Испытание проводят на образцах-балочках, изготовленных из мелкозернистого бетона, путем их попеременного замораживания в морозильной камере и оттаивания в воздушной
среде.
А.2.2 Приготавливают смесь основного состава с соотношением цемент : песок = 1 : 3,
марки по удобоукладываемости П2 с выбранной оптимальной дозировкой противоморозной добавки.
А.2.3 Из смеси, приготовленной в соответствии с А.2.2, изготавливают три образца-балочки размером 4×4×16 см, которые непосредственно после изготовления помещают
на 28 сут в морозильную камеру при заданной отрицательной температуре.
А.2.4 По истечении 28 сут замораживания образцы-балочки оттаивают в воздушно сухих условиях при температуре плюс (15 ± 5) °Св течение 3 − 4 ч, после чего образцы расформовывают.
А.2.5 Последующие циклы замораживания образцов-балочек при заданной отрицательной температуре и оттаивания при температуре плюс (15 ± 5) °С проводят при скорости изменения температуры 3 – 5 °С/ч. Число циклов − 50.
А.2.6 По окончании испытания образцы-балочки осматривают. Отсутствие признаков разрушения образцов (растрескивание, выкрашивание ребер, шелушение) после испытания свидетельствует о возможности применения в бетоне испытываемой добавки в оптимальном количестве.
2 Вопрос : Разработать методику испытаний: определение морозостойкости щебня ускоренным методом (ГОСТ 8269)
Методика испытаний щебня на морозостойкость.
Цель: определить морозостойкость щебня ускоренным методом
При проведении испытания применяют следующие средства измерений, вспомогательные устройства.материалы и реактивы:
• сушильный шкаф, обеспечивающий циркуляцию воздуха и поддержание температуры в интервале (110 ±5) °С:
• весы по ГОСТ OIML R 76-1;
• сита с размером ячеек 4; 8; 16; 31.5:45; 63 мм в соответствии с ISO 3310-1 [1] и ISO 3310-2 [2];
• противни металлические;
• таймер с точностью измерений не более 1 мин;
- металлический сосуд для насыщения щебня (гравия) раствором сульфата натрия:
- дистиллированная вода по ГОСТ 6709:
• натрий сернокислый по ГОСТ 4166 (натрий сульфат 10-водный по ГОСТ 4171).
Подготовка к выполнению испытания
1 Мерную пробу щебня (гравия) готовят в соответствии с п. 7.2.
2 Затем готовят раствор сульфата натрия в необходимом количестве. Для этого отвешивают (185 ± 2) г безводного сернокислого натрия или (420 ± 3) г кристаллического сернокислого натрия и постепенно добавляют в подогретую до (40 ± 2) вС дистиллированную воду объемом один литр при тщательном перемешивании. Раствор сульфата натрия готовят в требуемом количестве.
3 Готовый раствор сульфата натрия охлаждают до температуры в лабораторном помещении, сливают в емкость и хранят не менее 2 суток.
Порядок выполнения испытания
1. Мерную пробу щебня (гравия) определенной фракции высылают на противни в один слой и заливают раствором сульфата натрия таким образом, чтобы все зерна щебня (гравия) были покрыты раствором.
2. Насыщение щебня (гравия) раствором сульфата натрия проводится в течение (20,0 ± 0.5) ч при комнатной температуре.
3. После насыщения щебня (гравия) раствор сульфата натрия сливают, а противни с мерной пробой помещают на (4.5 ±0.5) ч в сушильный шкаф, в котором поддерживается температура (110 ±5) вС.
4.Затем щебень (гравий) охлаждают до комнатной температуры и вновь заливают раствором сульфата натрия
5. Последующие циклы испытания включают в себя выдерживание щебня (гравия) в течение (4,5 ± 0,5) ч в растворе сульфата натрия и высушивание в течение (4,510,5) ч в сушильном щкафу при температуре (11015)°С с последующим охлаждением до комнатной температуры.
6. Примечание — 8 перерывах между циклами мерную пробу щебня (гравия) оставляют на воздухе.
7. После 3.5,10 и 15 циклов мерную пробу щебня (гравия) промывают водой для удаления сульфата натрия, затем высушивают до постоянной массы и просеивают через контрольное сито с размером ячеек, равным d.
8.Зерна щебня (гравия) фракции свыше 31.5 до 45 мм.имеющие свежую поверхность раскола и оставшиеся на сите с размером ячеек 31,5 мм. относят к неморозостойким, их массу не включают в массу остатка на контрольном сите.
Обработка результата испытания
Потеря массы мерной пробы щебня (гравия) при испытании в процентах, рассчитывается по формуле
( 1 )
где М — масса мерной пробы до испытания, г:
—- масса остатка на сите с размером ячеек d. после определенного цикла испытания, г.
Результат испытания рассчитывают с точностью до первого знака после запятой. За результат испытания принимается среднеарифметическое значение двух параллельных испытаний. Расхождение результатов двух параллельных испытаний не должно превышать 1 %, в противном случае испытание необходимо повторить.
Морозостойкость зерен щебня (гравия) в широкой фракции, а также смеси фракций рассчитывают по формуле
X= ,
где — потеря массы при испытании в отдельной фракции щебня,%;
— содержание данной фракции,%.
Результат испытания рассчитывают с точностью до первого знака после запятой.
Оформление результата испытания
Результат испытания регистрируют в журнале и оформляют в виде протокола, который должен содержать:
- номер протокола;
• дату проведения испытания.
• название организации, проводившей испытание;
- ссылку на настоящий стандарт:
• ссылку на акт отбора проб:
- наименование испытуемого материала:
• результат испытания:
• сведения об условиях проведения испытания;
- фамилию, имя, отчество и подпись лица, проводившего испытание:
• фамилию, имя, отчество и подпись лица, ответственного за испытание.
Контроль точности результата испытания
Точность результата испытания обеспечивается:
- соблюдением требований настоящего стандарта:
• проведением периодической оценки метрологических характеристик средств измерений;
• проведением периодической аттестации оборудования.
Лицо, проводящее испытание, должно быть ознакомлено с требованиями настоящего стандарта.
3.Задачапосле просеивания щебня масса частых остатков на ситах в % составила: m_40=4; m_20=51; m_10=39; m_5=5, прошло через сито 5-1. Построить график зернового состава и дать оценку щебню о пригодности его для приготовления бетона.
Щебень и гравий выпускают в виде следующих основных фракций: от 5 до 10 мм; св. 10 до 20 мм; св. 20 до 40 мм; св.40 до 80 мм и смеси фракций от 5 до 20 мм. Полные остатки на контрольных ситах при рассеве щебня н гравия фракций от 5 до 10 мм, св. 10 до 20 мм, св. 20 до 40 мм, св. 40 до 80 мм и смеси фракций от 5 до 20 мм и от 5 до 15 мм должны соответствовать указанным в таблице, где d и D — наименьшие и наибольшие номинальные – размеры зерен, мм
Диаметр отверстий контрольных сит, мм | d | 0,5 (d + D) | D | 1,25 D |
Полное остатки на ситах % по массе | От 90 до 100 | От 30 до 80 | До 10 | До 0,5 |
Примечание – для щебня и гравия фракций от 5 (3) до 10 мм применяют соответственно сита 2,5 и |
По известным значениям частных остатков рассчитывают полные остатки, %
определяют полые остатки на каждом сите в процентах от массы пробы,
равные сумме частных остатков на данном и всех ситах с большими размерами отверстий и вносим в таблицу:
Остаток на сите | 40 | 20 | 10 | 5 |
Частные остатки,% | 4 | 51 | 39 | 5 |
Полные остатки,% | 4 | 55 | 94 | 99 |
Строим график по полученным данным полных остатков :
Вывод:
Щебень не пригоден для приготовления бетона, т.к. кривая его просеивания не располагается в заштрихованной зоне.
Список литературы
1. Адаскин, А.М. Материаловедение (металлообработка): Учебное пособие для начального профессионального образования / А.М. Адаскин, В.М. Зуев.. - М.: ИЦ Академия, 2012.;
2. Панкова, Т. А. Строительные материалы [Текст]: методические указания к лабораторным занятиям / Т. А. Панкова, В. А. Мещеряков, Т. И. Болуто, О. В. Михеева. − С.: ООО Наука, 2013.
Интернет ресурсы:
1. http://docs.cntd.ru/document/1200078684;
2. http://files.stroyinf.ru/Data1/5/5182/;
3.http://dortver.ru/for-students/useful/230.html.
Дата добавления: 2018-04-04; просмотров: 1233; Мы поможем в написании вашей работы! |
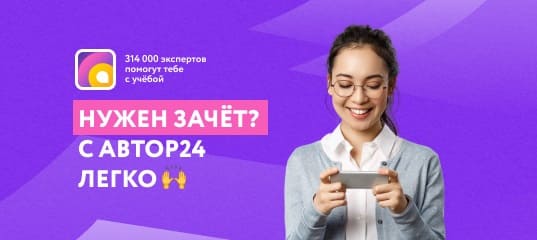
Мы поможем в написании ваших работ!