Высокочастотная конденсаторная керамика
Отличается высоким удержанием кристаллической фазы и низким содержанием бесщелочной аморфной фазы. Как правило, стеклофаза не образуется, но могут присутствовать несколько кристаллических фаз с различными значениями ε и ТКε. У большинства материалов этой группы, имеющих высокие значения ε, основной составной частью кристаллической фазы является рутил (двуокись титана TiO2).
Рутил – это высокотемпературная кристаллическая модификация ТiO2, которая имеет в направлении главной кристаллографической оси ε=173. Однако в результате беспорядочного расположения кристаллитов рутила и наличия других добавок керамика имеет ε меньше указанного значения (ε≈80).
Кроме рутила TiO2 в кристаллическую фазу многих видов высокочастотной конденсаторной керамики входят соединения титаната кальция (перовскит) СаО·ТiO2, образующие перовскитовую керамику(марки Т-150, М-130), или титаната стронция SrO·TiO2, образующие стронциевую керамику(марка М-300). У этих видов керамики ε=180–230. Используются они для изготовления высокочастотных конденсаторов, к которым не предъявляют требований стабильности емкости. В состав конденсаторной керамики также вводят оксиды олова и металлов II и III групп периодической системы элементов. В зависимости от химического состава электрические свойства высокочастотной конденсаторной керамики имеют следующие значения: ε=14–250; ρ=1010–1011 Ом·м (при 100°С), tgδ=(3–5)·10–4 (при 1 МГц и 20°С); Eпр=6–35 кВ/мм, ТКε колеблется в пределах от минус 1300·10–6 до плюс 30·10–6 К–1.
|
|
Керамика на основе рутила при длительном воздействии предельного рабочего напряжения и повышенной температуры стареет, в результате электропроводность и диэлектрические потери возрастают, а электрическая прочность снижается. Однако ее вполне успешно можно использовать в области относительно слабых электрических полей и ограниченных рабочих температур. На значительно более жесткие эксплуатационные режимы рассчитана безрутиловая конденсаторная керамика: титано-циркониевая, станнатная, лантановая. Преимуществом этих марок керамики является более высокая стойкость к длительному воздействию постоянного напряжения.
Для получения титано-циркониевой керамикииспользуют составы на основе системы ZrTiO3–TiO2 с добавкой небольшого количества окисла магния MgO или твердые растворы титаната-цирконата кальция CaTiO3–CaZrO3 (Т-80, ТЦ-750, ТЛ-470). Изделия из керамики системы CaTiO3–CaZrO3 могут эксплуатироваться при более высоких температурах, чем из системы ZrTiO3–TiO2; они имеют ε=20–30; tgδ=(3–4)·10–4.
В станнатной керамикекристаллической фазой являются твердые растворы станната кальция CaSnO3, титаната кальция CaTiO3 и цирконата кальция CaZrO3. Кроме того, в состав керамической массы вводят небольшое количество глины и окисла цинка. Станнатная керамика имеет небольшие значения ε (12–30) и tgδ ((15–80)·10–4).
|
|
Лантановую керамикуполучают на основе системы LaAl2O3–CaTiO3. Она имеет значительно более высокие значения ε (40–150), чем станнатная керамика, и небольшой tgδ (5·10–4). Лантановая керамика применяется для изготовления контурных, разделительных и термокомпенсирующих конденсаторов. У термокомпенсирующих конденсаторов емкость с повышением температуры снижается.
Асбестовые и слюдяные материалы
Слюда– это природный кристаллический минерал с хорошими электрическими свойствами и высокой нагревостойкостью. Ее характерной особенностью является слоистая структура и анизотропия свойств. Кристаллиты слюды легко расщепляются по плоскостям спайности на пластинки толщиной 0,5–5 мкм и более.
Известно несколько десятков разновидностей слюды. Все они по химическому составу являются водными алюмосиликатами. В электроизоляционной технике применяют два вида слюды: мусковит, состав которого приблизительно выражен формулой – K2O·3Al2O3·6SiO2·2H2O, ифлогопит- К2О·6MgO·Al2O3·6SiO2·2H2O. Фактически состав слюд может существенно изменяться; в них могут входить и другие окислы (Fe2O3, TiO2, Cr2O3, MnO, CaO, Na2O).
|
|
Слюда мусковит бывает бесцветной или имеет красноватый, бурый, зеленый или другие оттенки. Флогопит чаще имеет более темную окраску: янтарную, золотистую, коричневую до почти черной. Слюда электротехнического назначения не должна содержать пятен (загрязнений) и воздушных включений. Мусковиты по электрическим свойствам лучше, чем флогопиты (табл. 3.2), у них более высокие механическая прочность, твердость, гибкость и упругость. Однако у флогопитов более высокая нагревостойкость и, что очень важно для изоляции коллекторных пластин электромашин, практически одинаковая с медью истираемость.
Таблица 3.2
Электрические свойства слюды
Вид слюды | ρ при температуре 20°С, Ом·м | ε при частоте | tgδ·104при частоте | Епр при толщине 0,025–0,05 мм, кВ/мм | ||
50 Гц | 1 кГц | 1 МГц | ||||
Мусковит | 1012–1014 | 6,1–8,4 | 4–80 | 2–10 | 1–6 | 100–250 |
Флогопит | 1011–1012 | 5–7 | 6–150 | 3–60 | 2–40 | 70–150 |
Фторфлогопит | 1012–1014 | 6,1–7,5 | – | – | 3 | 100–400 |
При нагревании кристаллизационная вода начинает выделяться у мусковита при температуре 500–600°С, у флогопита при 800–900°С. Слюда при этом вспучивается в результате расслаивания, теряет прозрачность, электрические и механические свойства резко ухудшаются.
|
|
При температуре 1260–1330°С слюда плавится. У некоторых видов флогопита с повышенным содержанием кристаллизационной воды электрические и механические свойства ниже и заметно ухудшаются при нагреве до температуры 150–250°С.
Слюдяную руду очищают от посторонних примесей, вручную расщепляют на отдельные пластинки, у которых обрезают дефектные края, и получают так называемую щепаную слюду.Щепаную слюду применяют для производства миканитов, а из лучших сортов мусковита готовят конденсаторную слюду.Конденсаторную слюду используют для изготовления слюдяных конденсаторов постоянной емкости типов: КСО (конденсатор слюдяной опрессованый), КГС (конденсатор герметизированный слюдяной), СГМ (слюдяной герметизированный малогабаритный). В настоящее время в производстве конденсаторов вместо слюды широко используют синтетические полимеры (полистирол, политетрафторэтилен).
Кроме слюды природной, в электроизоляционной технике получила распространение слюда синтетическая – фторфлогопит, отличающаяся от флогопита тем, что в ее кристаллической решетке гидроксильные группы ОН– замещены ионами фтора F–. Фторфлогопиты имеют более высокую нагревостойкость (до 1000°С), обладают более высокими электрическими свойствами (см. табл. 4.4), химически более устойчивы.
Микалексы представляют собой прессованную массу, в которой связующим являются легкоплавкие стекла (борно–свинцовые или борно–баритовые), а наполнителем – порошкообразный мусковит. Прессование производится при температуре размягчения стекла около 600°С и давлении 50–70 МПа, при этом стекло химически взаимодействует с поверхностью слюды. Электрические свойства микалексов: =6–8,5; ρ=1010–1011 Ом·м; tgδ=(3–10)·10–3 при 1 МГц; Епр=10–20 кВ/мм.
Выпускают микалексы в виде листов или стержней разного сечения, из которых методом механической обработки (точения, фрезерования, сверления) изготавливают детали нужных форм и размеров. Применяют микалексы для изготовления держателей мощных радиоламп, каркасов катушек индуктивности, плат переключателей, панелей воздушных конденсаторов.
При использовании в качестве наполнителя синтетической слюды образуется материал под названием новомикалекс. Его электрические свойства: ε=7,5–8; ρ=1010–1012Ом·м; tgδ=(8–15)·10–4 при 1 МГц; Епр=30 кВ/мм.
Миканиты представляют собой композиционный материал листового или рулонного строения, полученный путем склеивания отдельных пластинок щепаной слюды с помощью клеящего лака или сухой смолы, иногда с применением волокнистой подложки из бумаги или ткани. Подложка наклеивается с одной или обеих сторон, увеличивая прочность материала на разрыв и затрудняя отслаивание пластинок слюды при изгибе материала.
Классифицируют миканиты с помощью двух или трех букв и цифры. Первая буква обозначает тип миканита: К–коллекторный, П–прокладочный, Ф–формовочный, М–микафолий, Г–гибкий, Л–микалента. Вторая буква характеризует вид слюды: М–мусковит, Ф–флогопит, С–смесь мусковита и флогопита. Третья и дальнейшие буквы и цифры указывают на вид клеящего вещества и дополнительные характеристики материала.
Миканиты К и П являются твердым материалом, из которых изготавливают изоляционные прокладки, не подвергающиеся изгибу. При ударе они издают характерный звенящий звук.
Коллекторный миканит (К) изготавливают из слюды флогопит, как более легко истирающийся. В качестве связующего используют шеллак, глифталиевую или другую смолы в минимальном количестве – до 4%. Миканит К имеет хорошие механические свойства и малую усадку. Применяют в качестве изоляции медных коллекторных пластин (междупластинная изоляция) электрических машин.
Прокладочный миканит (П) производят из слюды мусковит, флогопит и их смеси. В качестве связующего используют шеллак, глифталевую или кремнийорганическую смолы. Содержание слюды в миканите П составляет 80–97%; применяют для изготовления различных электроизоляционных прокладок, шайб.
Формовочный миканит (Ф) изготавливают в виде листов толщиной от 0,1 до 0,5 мм с содержанием слюды 80–95%, остальное связующее – шеллак, глифталевая или кремнийорганическая смолы. При нормальной температуре миканит Ф тверд, однако при нагревании размягчается и становится способным принимать заданную форму, которая при охлаждении сохраняется. Применяют для изготовления коллекторных манжет (изоляция коллектора от вала в электромашинах), каркасов катушек, фланцев, трубок и других фасонных изделий.
Микафолий (М) – разновидность формовочного миканита; изготавливают его из флогопита или мусковита. В качестве связующего используют глифталевый, шеллачный, полиэфирный или кремнийорганический лаки. Содержание слюды в нем не менее 45–50%. Имеет с одной стороны подложку из бумаги, стеклоткани или стеклосетки. Выпускается в листах или рулонах толщиной от 0,15 до 0,30 мм. У микафолия из флогопита Епр≥13 кВ/мм, а из мусковита Епр≥15–16 кВ/мм. Применяют для изоляции стержней якорных обмоток машин высокого напряжения, где требуются большие усилия при намотке.
Гибкий миканит (Г) получают на основе мусковита или флогопита в виде листов толщиной от 0,15 до 0,50 мм. В качестве связующего применяют масляно-битумные, масляно-глифталевые или кремнийорганические лаки. Содержание слюды (без подложек) составляет 75–90%. Выпускают также гибкие миканиты на подложке, т.е. оклеенные с обеих сторон бумагой; содержание слюды в них – не менее 50%. Эти миканиты обладают гибкостью и применяются в качестве изоляции обмоток секций, гибких прокладок, пазовой изоляции электрических машин и аппаратов.
Микалента (Л) – разновидность гибкого миканита. Получают из крупных пластин слюды, склеенных в один слой с перекрытием примерно на одну треть. Имеет с одной или с обеих сторон подложки из бумаги, стеклоткани или стеклосетки. Микалента выпускается толщиной 0,10; 0,12; 0,15 и 0,17 мм и шириной от 10 до 35 мм. Является одним из основных видов изоляции электрических машин высокого напряжения. Хранят в закрытой металлической таре, заполненной насыщенным паром соответствующего лакового растворителя. При пересыхании микаленту необходимо выдержать в парах лакового растворителя.
Нагревостойкие миканиты производят на основе природной и синтетической смолы. В качестве связующего используют неорганические вещества – фосфорнокислый аммоний (аммофос), алюмофосфаты. Этот вид миканитов выпускают в листах толщиной от 0,2 до 1,0 мм, нагревостойкостью в несколько сот градусов (до 850°С).
Слюдиниты(за рубежом – самика) и слюдоспластыполучают с помощью бумагоделательных машин, отсюда и другое название – слюдяные бумаги. В отличие от миканитов их производство максимально механизировано и практически исключает ручной труд. Получают слюдиниты и слюдопласты из измельченной специальным способом очищенной исходной (нещепаной) слюды мусковит или флогопит, или их отходов. При измельчении слюды образуются пластинки (чешуйки) толщиной до 1 мкм, длиной и шириной порядка десятых долей миллиметра. Из массы измельченной слюды и воды с помощью бумагоделательной машины получают слюдинитовую бумагу толщиной от 10 до 150 мкм для производства слюдинитов или толщиной от 40 до 200 мкм – для слюдопластов. Полученный материал пропитывают связующим веществом на основе эпоксидной, кремнийорганической или другой смол. Слюдиниты используют и в сухом виде, т.е. без пропитки электроизоляционными лаками в качестве связующего. Такие слюдиниты легко разрушаются при соприкосновении с водой и имеют невысокую электрическую прочность (Епр=15–20 кВ/мм). В ряде случаев полученную слюдинитовую бумагу отпрессовывают. К слюдинитам и слюдопластам с одной или обеих сторон наклеивают подложку из бумаги, стеклоткани или стеклосетки, получая коллекторный, прокладочный, формовочный, гибкий слюдинит или слюдопласт, в том числе слюдинитофолий и слюдопластовые ленты. Слюдопласты, как правило, имеют более высокую механическую прочность и большую короностойкость, чем слюдиниты.
Асбест– это минерал волокнистого строения, волокна которого представляют агрегаты тончайших кристаллитов, нагревостойкий материал, с невысокими электроизоляционными свойствами, достаточно эластичный, с высокой механической прочностью, обладает прядильной способностью
Длина волокон колеблется от десятых долей миллиметра до нескольких сантиметров. В электроизоляционной технике из множества асбестовидных минералов получил применение хризотиловый (или серпентинный) асбест, представляющий собой водный силикат магния 3MgO·2SiO2·2H2O с содержанием до 3% различных примесей в виде окислов железа, алюминия, кальция.
Из асбеста изготавливают пряжу, ленты, шнуры, ткани, бумаги, картон и другие изделия. При температуре 450–700°С он теряет кристаллизационную воду и разрушается. Асбест относительно гигроскопичен и растворяется даже в слабых кислотах. При пропитке асбеста олифой, парафином, битумами и смолами его гигроскопичность и влагопоглощаемость снижаются. Электроизоляционные свойства асбеста невысокие: ρ=108–1010 Ом·м; Епр=2–6 кВ/мм, поэтому в высоковольтной и высокочастотной технике его не применяют.
Известны материалы на основе асбеста, главные из которых – электронит и асбестоцемент.
Электронит – пластмасса, наполнителем которой является асбестовое волокно, связующим – каучук. Выпускают электронит в листах толщиной от 0,1 до 6 мм. При толщине 0,5 мм его Епр>7 кВ/мм. Применяется электронит в низковольтной аппаратуре в качестве втулок, прокладок.
Асбестоцемент– неорганическая пластмасса, наполнителем которой является асбестовое волокно, связующим – портландцемент. Изготавливают из асбестоцемента доски толщиной от 4 до 40 мм, длиной 1200 и шириной 700–900 мм, трубы, муфты и другие фасонные изделия. У асбестоцемента неплохие механические свойства и высокая нагревостойкость (у непропитанного – более 220°С), искро- и дугостойкость. Благодаря последнему свойству он широко используется в производстве искро- и дугогасительных камер и перегородок.
Недугостойкие изделия из асбестоцемента, работающие в условиях окружающей атмосферы, в том числе для сильноточной аппаратуры, пропитывают обычно мазутом, каменноугольным пеком или битумом.
У пропитанного асбестоцемента водопоглощаемость до 2%, Епр=2–3 кВ/мм; ρ=108–1010 Ом·м.
Минеральные диэлектрики
К минеральным диэлектрикам относятся мрамор, тальк, мел и др. Все они в электроизоляционной технике имеют ограниченное применение из-за низких электроизоляционных свойств.
Мрамор – минерал зернисто-кристаллического строения, состоящий в основном из карбоната кальция СаСО3. Размер кристаллических зерен колеблется в широких пределах (от сотых долей миллиметра до 7 мм). Чем мельче зерно, тем выше механическая прочность, лучше электроизоляционные свойства, меньше гигроскопичность. Мрамор стоек к действию воды, щелочей, масел, органических растворителей, но растворяется в кислотах, даже слабых, с выделением СО2. Он малостоек к термоударам. Во влажной среде электроизоляционные свойства его значительно ухудшаются. Для повышения влагостойкости изделия из мрамора пропитывают парафином, битумом или стиролом с последующей его полимеризацией или лакируют. Нагревостойкость мрамора длительная – до 100–110°С и кратковременная –до 250°С. Водопоглощаемость за 24 ч 0,15–0,4%. Его электрические свойства: ε=8–10; ρ=105–109 Ом·м, tgδ=(5–10)·10–3 при 50 Гц; Епр=2,5 кВ/мм.
Тальк– минерал белого цвета или окрашенный в светлые тона, очень мягкий – легко режется ножом; его химическая формула – 3MgO4SiO2H2O. Температура плавления находится в пределах от 1200 до 1600°С, обладает относительно высокой кислотостойкостью.
В электротехнической промышленности тальк используют при изготовлении высоковольтной стеатитовой керамики и в качестве наполнителя для кабельных резин. В кабельной технике в качестве наполнителя также применяют и другие минералы: мел и каолин.
Тема 12.Органические диэлектрические материалы (полимеры)
Термопласты, или термопластичные полимеры, представляют группу диэлектриков, обладающих хорошими электрическими свойствами, что обеспечивает их широкое использование в электро- и радиотехнике. Макромолекулы их имеют строение линейное или разветвленное. В большинстве случаев термопласты – это аморфные или аморфно-кристаллические полимеры, нерастворимые в воде, однако, как правило, растворимые в близких по природе органических растворителях; они слабо гигроскопичны, стойки к химически агрессивным средам (кислотам и щелочам). Ряд из них имеет достаточно низкую температуру стеклования, поэтому при комнатной температуре они обладают гибкостью и эластичностью. При температурах выше температуры текучести термопласты переходят в вязкотекучее состояние и под действием внешнего давления принимают заданную форму, которую сохраняют после охлаждения. В этом состоянии из них изготавливают изделия. Повторный нагрев снова приводит термопласты в пластическое состояние.
Все термопласты, за редким исключением (например, политетрафторэтилен и полиимиды), горючи, а изделия из них пожароопасны. Для снижения горючести и повышения тем самым пожаробезопасности электро- и радиоаппаратуры в полимеры в ряде случаев вводят антипирирующие добавки.
Антипирен – это вещество, которое при температуре горения разлагается с выделением большого количества негорючих газообразных продуктов, снижающих концентрацию кислорода в зоне горения до величины гашения пламени.
В большинстве случаев термопласты используют в производстве изделий без наполнителей, поэтому их часто называют смолами, которые могут быть природными и синтетическими.
В электроизоляционной технике термопласты применяют как самостоятельно, например изоляция проводов и кабелей, каркасы катушек индуктивности, пленки для производства конденсаторов, волокнистые материалы, так и в виде составной части клеев, лаков, компаундов, пластмасс. Используют их и как конструкционные материалы. Все термопласты по своему поведению в электрическом поле подразделяются на две большие группы: термопласты неполярные и полярные. Для снижения температуры стеклования Тс, увеличения термо- или светостойкости в термопласты вводят небольшие количества соответствующих добавок (стабилизаторов, пластификаторов), в некоторых случаях – красители.
Неполярные термопласты имеют высокие значения удельного объемного сопротивления ρ, электрической прочности Епр и низкие диэлектрические потери tgδ. Значения диэлектрической проницаемости ε и tgδ у них мало зависят от температуры и частоты в широком интервале (табл. 3.3). Это позволяет использовать неполярные термопласты в области ВЧ и СВЧ.
Таблица 3.3
Свойства синтетических полимеров (смол)
Полимеры (смолы) | Предел прочности при растяжении, МПа | Относительное удлинение при разрыве, % | Водопоглощение за 30 сут при 20°С, % | ε при частоте 1 МГ при температуре 20°С | ρ при температуре 20°С, Ом·м | tgδ×104 при частоте 1 МГц и температуре 20°С | Епр при частоте 50 Гц и толщине ~1 мм, кВ/мм |
1 | 2 | 3 | 4 | 5 | 6 | 7 | 8 |
Неполярные термопласты | |||||||
Полиэтилены | 10–33 | 200–800 | 0,005–0,01 | 2,2–2,4 | 1015–1016 | 2–4 | 45–60 |
Полипропилен | 30–35 | 200–800 | 0,03 | 2,0–2,2 | 1014–1016 | 2–5 | 30–35 |
Полиизобутилен | 2–4,4 | 550–1000 | 0,05 | 2,2–2,3 | 1014–1015 | 3–5 | 16–23 |
Полистирол | 35–41 | 1,5 | 0–0,07 | 2,5–2,6 | 10|4–1016 | 1–3 | 25–35 |
Политетрафторэтилен | 14–35 | 250–500 | – | 1,9–2,2 | 1015–1018 | 2–2,5 | 40 |
Продолжение табл. 3.3
1 | 2 | 3 | 4 | 5 | 6 | 7 | 8 |
Полярные термопласты | |||||||
Политрифторхлорэтилен | 30–40 | 70–200 | – | 2,5–2,7 | 1014–1015 | 100 | 20–25 |
Поливинилхлорид | 40–60 | 5–100 | 0,4–0,6 | 3,5–4,5 | 1012–1013 | 150–180 | 35–45 |
Полиамиды | 54–108 | 100–150 | 1,4–3,3 | 4–6 | 1011–1012 | 220–300 | 20–25 |
Полиимиды | 160–180 | 65 | 0,8 (при 1000°С) | 3,5 | 1015 | 6–16 | 160–200 |
Полиэтилентерефталат | 150–200 | 70 | 0,5 | 3,1–3,5 | 1013–1015 | 20–200 | 30 |
Поликарбонаты | 65–80 | 50–110 | 0,2 | 3,0 | 1014–1015 | 6–20 | 30 |
Полиуританы | 50–60 | 500–1000 | 0,2 | 4,5–5,0 | 1012 | 200–300 | 26 |
Полиметилметакрилат | 76 | 3 | 0,2 | 2,8–3,7 | 1011–1012 | 200–300 | 18–35 |
Поливинилформаль | 60–70 | 5–10 | 0,5–3,0 | 3,3 | 1011–1014 | 200 | 26 |
Реактопласты | |||||||
Феноло- и крезолоформальдегидные | 49–56 | 1,0–1,5 | 0,1–0,2 | 4,5–5,0 | – | 150–300 | 12–16 |
Анилиноформальдегидные | 60–70 | – | 0,01–0,08 | 3,5–3,6 | 1012–1013 | 20–60 | 20 |
Карбамидоформальдегидные | 56–92 | – | 0,5–0,7 | 6,6–7,7 | 1010–1011 | 300 | 12–16 |
Меламиноформальдегидные | 56–92 | 0,6–0,9 | 0,3–0,6 | 3,5–7,6 | 1010–1011 | 500 | 12–16 |
Глифталевые | 21–28 | – | 0,08–0,10 | 6,0 | 1012 | – | – |
Эпоксидные (диановые) | 20–50 | – | 0,25 | 3,6–4,0 | 1012–1014 | 40–180 | 16–18 |
Следовательно, неполярные термопласты относятся к классу высокочастотных диэлектриков. Для них характерны следующие значения электрических характеристик: ε=2–2,6; ρ=1014–1018 Ом·м; tgδ~104; Епр≈до 60 кВ/мм при толщине пленок ~1 мм; у пленок толщиной 0,02–0,1мм Епр имеет значения до 250 кВ/мм. На значения электрических характеристик, особенно ρ, сильно влияет присутствие ионогенной примеси. Чем выше степень чистоты и меньше влажность неполярного полимера, тем лучше его электрические свойства. Этим можно объяснить значительную разницу в значениях , приведенных в литературных источниках.
Полиэтилен (ПЭ) – бесцветный прозрачный продукт полимеризации газообразного этилена; имеет общую химическую формулу (–СН2–СН2–). Фактически строение молекул ПЭболее сложно, чем это отображено формулой. В молекулярной цепи, хотя и в малом количестве, имеются боковые ответвления в виде –СН3, –С2Н5 и более сложных групп, двойные связи (не только в цепи, но и в ответвлениях), карбонильные группы в значительной мере и определяют электрические свойства ПЭ. Температура стеклования имеет примерно такие же значения, что и температура хрупкости. ПЭ пожароопасен, горит голубоватым пламенем с запахом горящей парафиновой свечи.
В зависимости от условий полимеризации различают полиэтилен высокого давления (ПЭВД), низкого давления (ПЭНД) и среднего давления (ПЭСД). ПЭВД получают при давлении 1470–2500 атмосфер (147–250 МПа) и температуре 180–270°С. Для получения ПЭНД и ПЭСД используют катализаторы. Полимеризация протекает при давлении и температуре, равными соответственно для ПЭНД 3–5 атмосфер (0,3–0,5 МПа) и 70–80°С, для ПЭСД 34–39 атмосфер (3,4–3,9 МПа) и 160–180°С. ПЭВД является полиэтиленом низкой плотности (ПЭНП), а ПЭНД и ПЭСД – полиэтиленами высокой плотности (ПЭВП).
Выпускают различные марки полиэтилена, отличающиеся плотностью, наличием или отсутствием стабилизаторов. Кроме того, отдельные партии ПЭ окрашивают в различные цвета. ПЭ при комнатной температуре не растворим в органических растворителях и лишь при температурах выше 70°С набухает и с трудом растворяется в хлорированных и ароматических углеводородах. К действию растворителей и масел ПЭНД более стоек, чем ПЭВД. ПЭВД имеет сравнительно низкую плотность (910–930 кг/м3), содержит в молекулярной цепи до 36 боковых ответвлений на каждую тысячу атомов углерода, которые затрудняют процесс кристаллизации. Поэтому ПЭВД содержит всего 50–65% кристаллической фазы. Его молекулярная масса равна (8–50)·104, Тпл=105–108°С, σр=10–17 МПа, σи=11,8–16,7 МПа, относительное удлинение при разрыве δ=500–800%, твердость по Бринеллю 13,7–24,5 МПа.
ПЭНД имеет плотность, равную 950–960 кг/м3, содержит до 6,0 боковых ответвлений на каждую тысячу углеродных атомов, степень кристалличности составляет 75-85% Его молекулярная масса равна (8–350)·104, Тпл=120–125°С, σр=22–30 МПа, σи=19,6–34,3 МПа, δ=300–800%, твердость по Бринеллю 44–60 МПа.
ПЭСД имеет плотность 960–970 кг/м3, содержит по 2,5 боковых ответвлений на каждую тысячу углеродных атомов. Меньшее число дефектов (числа боковых ответвлений) в молекулярной цепи, чем у ПЭВД, облегчает кристаллизацию, поэтому он имеет более высокую плотность (960–970 кг/м3) и степень кристалличности (80–90%), чем ПЭВД. Молекулярная масса равна (30–40)·104, Тпл=127–130°С, σр=27–33 МПа, σи=24,5–39,2 МПа, δ=200–800%, твердость по Бринеллю 60–64 МПа.
С повышением плотности ПЭ увеличиваются его температура плавления, разрушающие напряжения при растяжении σр и изгибе σи, модуль упругости и твердость; эластичность при этом снижается. Изделия из ПЭ при длительной статической нагрузке деформируются: из ПЭНД – при нагрузке, равной 2,45 МПа (25 кгс/см2), а из ПЭВД – при нагрузке 4,9 МПа (50 кгс/см2). Изделия из ПЭ, находящиеся длительное время в напряженном состоянии, могут растрескиваться.
ПЭ обладает высокой водостойкостью. Водопоглощение за 30 суток при 20°С составляет у ПЭВД – 0,02%, ПЭНД – 0,005% (при 70°С – 0,04%), ПЭСД менее 0,01%. Пленки из ПЭВД имеют низкую проницаемость по отношению к водяным парам, но высокую к газам. У ПЭВД диэлектрические потери несколько ниже, а стойкость к старению несколько выше, чем у ПЭНД и ПЭСД. Однако ПЭНД обладает несколько лучшими физико-механическими свойствами, чем ПЭВД. Стоимость ПЭВД ниже, чем ПЭНД и ПЭСД.
Нагревостойкость ПЭ при кратковременном воздействии тепла ограничивается ухудшением механических характеристик, а при длительном воздействии в условиях доступа воздуха – окислением. Нагревостойкость ПЭ составляет 80–90°С. Для повышения нагревостойкости в ПЭ вводят различные стабилизаторы. В некоторых случаях уже готовые изделия (например, кабели, электроизоляционные трубки, муфты, пленки) подвергают ионизирующему облучению. При облучении происходит частичная сшивка молекулярных цепей ПЭ благодаря наличию в них небольшого количества двойных связей (дефекты строения) и образованию пространственной структуры. Облученный ПЭ более тверд и имеет нагревостойкость, ограниченную тепловым старением, – до 105°С, а кратковременную нагревостойкость – до 200°С. Облученные в деформированном состоянии изделия из ПЭ обладают интересной способностью – при умеренном нагреве восстанавливают форму и размеры, существовавшие до облучения.
Полиэтилен широко используют в производстве разнообразных проводов и кабелей, в том числе высокочастотных и силовых. В настоящее время ПЭ является одним из крупнотоннажных материалов в кабельной промышленности. Перерабатывается ПЭ в изделия методом. экструзии при 150–230°С.
Полипропилен (ПП)– бесцветный материал высокой прозрачности для видимого света – получают путем полимеризации газообразного пропилена в присутствии катализатора. Общая химическая формула ПП:
Как и ПЭ, полипропилен огнеопасен. Молекулярные цепи имеют высокую регулярность, что облегчает их кристаллизацию. Поэтому ПП обладает высокой степенью кристалличности – 90–95%, плотность его равна 900–910 кг/м3, молекулярная масса (8–20)·104, Тпл=160–170°С, твердость по Бринеллю 59–64 МПа, удельная ударная вязкость σуд=78,5 кДж/м2. Существенный недостаток ПП – низкая морозостойкость.
ПП в сравнении с ПЭ имеет более высокую нагревостойкость и прочность при растяжении, большую твердость и жесткость. Его «длительная» нагревостойкость не более 105°C. При комнатной температуре ПП нерастворим в органических растворителях, при температуре 80°С и выше растворяется в хлорированных и ароматических углеводородах. Устойчив к действию кислот и щелочей, а также минеральных и растительных масел даже при повышенных температурах. Меньше, чем ПЭ, подвержен растрескиванию под воздействием агрессивной среды. Пленки из ПП наряду с высокой нагревостойкостью, прозрачностью и механической прочностью имеют низкую газо- и паропроницаемость.
При повышенных температурах в присутствии кислорода ПП окисляется; физико-механические и электрические свойства при этом ухудшаются. ПП также окисляется под действием прямого солнечного света. В помещении или на открытом воздухе в отсутствие прямых солнечных лучей свойства ПП не изменяются в течение длительного времени. Для увеличения стойкости к тепловому и световому старению в ПП вводят стабилизаторы. Наиболее перспективной областью его применения является конденсаторостроение.
Полиизобутилен (ПИБ) - бесцветный продукт полимеризации изобутилена в присутствии катализаторов. Общая химическая формула
–
ПИБ, как и ПЭ, огнеопасен. Производят его в виде низко-, средне- и высокомолекулярных продуктов. Высокомолекулярный ПИБ имеет молекулярную массу (20–25)·104; устойчив к действию кислот, в том числе концентрированной HNO3 и щелочей. Его плотность равна 910–930 кг/м3, морозостойкость составляет –50°С. ПИБ растворим в алифатических, ароматических и хлорированных углеводородах, в сероуглероде, нерастворим в полярных жидкостях: спиртах, кетонах, сложных эфирах. Под действием солнечных лучей и кислорода его свойства ухудшаются. Для повышения стойкости ПИБ к ультрафиолетовым лучам в него вводят активные наполнители – сажу, графит (до 150%).
Электрическая прочность ПИБ заметно ниже, диэлектрические потери несколько выше, чем у ПЭ.
Полиизобутилен в отличие от многих других полимеров имеет чрезвычайно низкую влаго- и газопроницаемость. Существенные его недостатки – низкая механическая прочность и высокая хладотекучесть. Поэтому в чистом виде его применяют редко. Для увеличения твердости в ПИБ добавляют наполнители. Высокомолекулярный ПИБ применяют в композиции с полистиролом для изготовления изоляционных лент; вводят в состав кабельного ПЭ, для повышения гибкости, стойкости к растрескиванию и снижению влагопроницаемости. Низкомолекулярный ПИБ используют для пропитки бумажных конденсаторов; вводят в состав некоторых клеев.
Полистирол (ПС) - твердый аморфный продукт полимеризации стирола (винилбензола). Общая химическая формула
где С6Н5 – бензольный заместитель.
В зависимости от способа полимеризации ПС выпускают блочный, суспензионный и эмульсионный. Кроме того, используя катализаторы, получен изотактический ПС кристаллического строения, обладающий более высокой температурой плавления (230–240°С) и более высокими механическими показателями, чем аморфный ПС. Однако изотактический ПС трудно перерабатывается в изделия, поэтому его производство ограничено.
Блочный ПС обладает высокой влагостойкостью – его водопоглощение за 24 ч равно 0%, в то время как у суспензионного ПС оно составляет 0,01–0,02%, а у эмульсионного – 0,07%. Блочный ПС – это бесцветный, прозрачный материал, пропускающий до 90% видимого света. В ультрафиолетовой и инфракрасной областях его прозрачность ниже. Показатель преломления света у него достаточно высок, благодаря чему его применяют для изготовления оптических стекол. Электрические характеристики эмульсионного ПС ниже, чем блочного и суспензионного.
Полистирол имеет плотность 1050–1070 кг/м3 и молекулярную массу, равную (5–30)·104, Тс=80–90°С, твердость по Бринеллю 137–196 МПа. С увеличением молекулярной массы электрические свойства ПС улучшаются – ρ и Епрвозрастают, tgδ уменьшается. Пожароопасен, горит с образованием сильнокоптящего пламени.
Полистирол – один из первых синтетических материалов, используемых в электро- и радиотехнике. Это хороший диэлектрик Его электрические свойства практически не зависят от влажности окружающей среды, температуры в пределах от минус 80 до плюс 90°С и частоты в интервале от 102–109 Гц. Обладает высокой стойкостью к действию кислот, щелочей, солей и спиртов, растворяется в четыреххлористом углероде, бензоле.
Недостатки ПС – относительно невысокая нагревостойкость, а главное – низкая удельная ударная вязкость (σуд=16–22 кДж/м2), относительно хрупок, а при старении хрупкость увеличивается. Для повышения нагревостойкости в ПС вводят до 30% кварцевой или слюдяной муки, белой сажи или талька, армируют стеклянным волокном. Для снижения хрупкости в ПС вводят до 8% каучука (получают привитой сополимер). Полученный материал называют ударопрочным полистиролом(марки УПС, УПМ, УПП). Он имеет высокую удельную ударную вязкость (σуд=30–60 кДж/м2) и высокие показатели других физико-механических свойств.
Перспективным материалом на основе стирола является его сополимер с акрилонитрилом и бутадиеном, получивший название пластик АБС (от начальных букв, образующих его трех компонентов). АБС-пластик отличается от ПС более высокими нагревостойкостью (выше на 10%) и удельной ударной вязкостью (до 70 кДж/м2), хорошей способностью металлизироваться; практически водонепроницаем, имеет хорошую термостабильность, повышенную химическую стойкость, неплохие электрические свойства (ε=2,9; =1013–1014 Ом·м; tgδ=8·10–3). АБС-пластик легко перерабатывается в изделия всеми характерными для термопластов способами. В электро- и радиотехнике применяется для изготовления корпусов приборов и отдельных деталей.
Полистирол широко используют в технике высоких и сверхвысоких частот как диэлектрик с очень низкими потерями. Из него изготавливают каркасы катушек индуктивности, панели электронных ламп, изоляцию высокочастотных кабелей, лаки, компаунды. Очень широко применяют ПС в производстве конденсаторов. Для этих целей используют пленку (стирофлекс)толщиной от 6 до 200 мкм (обычно не толще 40–50 мкм), ориентированную в двух перпендикулярных направлениях. Такая пленка менее дефектна и обладает высокими электрическими свойствами.
Политетрафторэтилен (ПТФЭ) – продукт полимеризации тетрафторэтилена; имеет общую химическую формулу
(–CF2–CF2–)..
Его плотность равна 2150–2240 кг/м3, молекулярная масса (14–50)·10–4, степень кристалличности 80–85%. При нагревании ПТФЭ практически не плавится, а при 415°С начинает разлагаться с выделением ядовитых газов. Твердость по Бринеллю составляет 30–40 МПа, σуд – до 100 кДж/м2. Полимер молочно-белого цвета, отечественное название – фторопласт-4, за рубежом (США) – тефлон. ПТФЭ негорюч, не растворяется ни в каких растворителях, практически негигроскопичен и не смачивается водой, имеет высокую стойкость к действию кислот и щелочей – на него не действуют никакие кислоты, в том числе смесь HNO3 и НСl («царская водка»). Обладает высокой нагревостойкостью – до 260°С и выдерживает кратковременный нагрев до 300°С. Тс=–120°С, а длительная рабочая температура имеет интервал от минус 269 до плюс 260°С.
Недостатки ПТФЭ – невысокая стойкость к радиационному излучению (он деструктирует) и хладотекучесть – под действием небольших статических нагрузок начинает деформироваться при комнатной температуре и ниже.
ПТФЭ – хороший диэлектрик; его электрические свойства остаются практически неизменными в пределах от минус 60 до плюс 200°С и в широком интервале частот вплоть до СВЧ включительно. Из него изготавливают пленки различной толщины, использующиеся в качестве ВЧ-изоляции, а также в производстве термо- и влагостойких конденсаторов и кабелей. Применяют для изготовления сплошной, в том числе тонкой (эмалевой) изоляции проводов, пластин, дисков, прокладок и других уплотнительных деталей. Монолитные заготовки и изделия изготавливают методом, имеющим много общего с порошковой металлургией.
Дляполярных термопластовхарактерны повышенные значения диэлектрической проницаемости ε и тангенса угла диэлектрических потерь tgδ, которые существенно зависят от температуры и частоты напряжения. Значения ρ и Епр у них ниже, чем у неполярных материалов.
Эти полимеры являются низкочастотными диэлектриками и применяются в электроустановках, работающих при постоянном напряжении или в области низких частот. Для них характерны следующие значения электрических характеристик: ε=3–6, ρ=1011–1014 Ом·м, tgδ≈10–2; Eпр≈ 40 кВ/мм при h≈1 мм; у пленок толщиной 0,02–0,1 мм Епр имеет значения 180 кВ/мм и выше. У слабополярных термопластов значение ρ выше, a tgδ ниже.
Политрифторхлорэтилен (ПТФХЭ)– продукт полимеризации трифторхлорэтилена белого цвета; общая химическая формула
(–CF2–CFCl–)n
Плотность его составляет 2090–2160 кг/м3, степень кристалличности 40–70%, молекулярная масса (2–36)·10–4, Тпл кристаллической фазы около 215°С, Тсаморфной фазы 50°С. Практически нехладотекуч, негорюч; отечественное название – фторопласт-3. В сравнении с фторопластом-4 имеет более низкую нагревостойкость, но более высокие эластичность и удельную ударную вязкость. Может эксплуатироваться без нагрузки в интервале температур от минус 195 до плюс 190°С, под нагрузкой в пределах от минус 60 до плюс 70°С. При температуре около плюс 300°С разлагается и окрашивается от темно-коричневого до черного цвета.
ПТФХЭ – слабополярный диэлектрик. Показатели его электрических характеристик несколько ниже, чем у фторопласта-4, однако выше радиационная стойкость и более простая технология переработки. Электрические свойства выше плюс 120°С существенно ухудшаются.
Применяют ПТФХЭ в кабельной технике и конденсаторостроении, а также для изготовления сложных по форме радиотехнических деталей, панелей ламп, гнезд и т.п.
Поливинилхлорид (ПВХ) – полупрозрачный с желтоватым оттенком твердый продукт полимеризации винилхлорида; общая химическая формула
(–СН2–СНСl–)n
Имеет широкое молекулярно-массовое распределение. Его плотность 1350–1360 кг/м3, молекулярная масса (5–10)·104, степень кристалличности может достигать 10%, Tc=78–105°С, Tт=180–220°С. При температуре 130–150°С начинается медленное, а при 170°С более быстрое разложение ПВХ, сопровождающееся выделением хлористого водорода НСl. Практически негорюч (горит только в пламени с выделением НСl и Сl2), стоек к действию воды, щелочей, разбавленных кислот, масел, бензина и спирта. Растворим при нагревании в тетрагидрофуране, циклогексаноне, ацетоне. Его электрические свойства зависят от температуры и частоты напряжения.
В связи с высоким значением Tс при комнатной температуре ПВХ находится в стеклообразном состоянии. В таком виде он выпускается под названием винипласт. Это листовой или трубчатый материал, легко сваривается или склеивается, в том числе с металлами. Для снижения Тси придания ПВХ большей гибкости и эластичности его пластифицируют, для чего в него вводят до 50% соответствующего пластификатора. Пластфицированный ПВХ имеет Тсоколо минус 40°С° и используется для изготовления изоляции проводов, защитной оболочки кабелей. При содержании дибутилфталата в количестве 8–40 мас.% Епр ПВХ увеличивается на 15–18%. При меньшем и большем содержании пластификаторов Eпр ниже, чем у ПВХ непластифицированного.
Для улучшения свойств ПВХ его в отдельных случаях подвергают дополнительному хлорированию. Такой материал называется перхлорвинилом (ХПВХ). Он содержит до 61,5–66% хлора (в ПВХ хлора 56,8%), растворим во многих растворителях: ацетоне, хлорбензоле, толуоле, ксилоле. Обладает повышенной адгезией к различным материалам, поэтому широко применяется для производства лаков, эмалей и клеев. Полимер эксплуатируется при температурах до 85°С. Имеет более низкую холодостойкость, чем ПВХ.
Полиамиды (ПА) – продукты поликонденсации, для которых характерным является наличие в химических звеньях макромолекул амидной группы
Это полярная группа, которая в основном и определяет весь комплекс электрических свойств. В зависимости от степени чистоты исходных продуктов ПА имеет окраску от бесцветной до желто-коричневой. Полимер горит с запахом прелых овощей. Наиболее распространенными отечественными видами полиамидов являются капрон (полиамид-6), имеющий общую химическую формулу
[–NH(CH2)5CO–]n
и найлон (анид, полиамид-6,6) с общей химической формулой
[–NH(CH2)6NH–OC(CH2)4CO–]n.
ПА имеют плотность 1120–1140 кг/м3, молекулярную массу (8–25)·10–3, Тпл=210–215°С, Тхр=–30°С, у некоторых видов до минус 70°С Они плавятся без разложения, отличаются высокой прочностью при ударных нагрузках (σуд=98–157 кДж/м2) и эластичностью. Растворяются только в концентрированных серной, соляной, азотной и муравьиной кислотах, фенолах и амидах. Растворы щелочей разрушают их. ПА устойчивы к действию жиров, масел, продуктов перегонки нефти, спиртов. При нагревании на воздухе происходит окислительная деструкция, которая резко возрастает под действием солнечного света и УФ-лучей. Физико-механические и электрические свойства при этом резко ухудшаются. ПА хорошо поддаются обработке резанием и горячим прессованием.
Электрические свойства ПА в значительной степени зависят от температуры, частоты напряжения и содержания влаги. Используют их для изготовления искусственных волокон, пластмасс, различных установочных и несущих элементов радиоаппаратуры. Входят ПА в состав некоторых компаундов, лаков и эмалей. В приборостроении применяют также и наполненные ПА. Для улучшения ряда физико-механических показателей, уменьшения водопоглощения и ТКЛР в ПА вводят такие наполнители, как тальк, аэросил, стеклянные волокна, графит. Из наполненных ПА изготавливают детали с жесткими размерами допусков, работающие в интервале температуры от минус 60 до плюс 120°С.
Полиимиды (ПИ) – группа полимеров, имеющих в химических звеньях молекулярных цепей имидную группу
,
которая и определяет электрические свойства. Это слабополярный диэлектрик с хорошими электрическими характеристиками. По химическому строению ПИ делятся на алифатические и ароматические, линейные и трехмерные. Плотность их равна 1430 кг/м3. Высокой степенью кристалличности (60% и более) обладают некоторые алифатические ПИ. Большинство ароматических ПИ – аморфные вещества с различной степенью упорядочности. Молекулярная масса их достигает до 200·103, σуд=50–80 кДж/м2, Тс≈500°С. Материал негорюч, может иметь окраску от светло-золотистой (почти бесцветной) до темно-красной. Нагревостойкость длительная – до 200–250°С и кратковременная – до 500°С. Стоек к действию озона и облучению электронами высокой энергии. Нестоек к действию щелочей и некоторых органических веществ.
ПИ используют в производстве некоторых видов пластмасс, лаков, эмалированных проводов. Пленки из ПИ применяют в качестве обмоточной изоляции электрических машин, в производстве кабелей, обмоточных проводов, печатных схем, конденсаторов. Они сохраняют гибкость при температурах вплоть до криогенных (минус 195°С). Кроме пленок из одного полиимида, выпускают также пленки на основе ПИ, покрытые с одной или обеих сторон ПТФЭ. Монолитные изделия из ПИ получают по технологии, имеющей много общего с порошковой металлургией.
Полиэтилентерефталат (ПЭТФ) - сложный полиэфир этиленгликоля (двухатомного спирта) и терефталевой кислоты с общей химической формулой
Его получают путем поликонденсации, отечественное название лавсан, в Англии – терилен, в США – дакрон. ПЭТФ способен кристаллизоваться; в аморфном состоянии совершенно прозрачен, в закристаллизованном утрачивает прозрачность. Его плотность равна 1380 кг/м3, молекулярная масса (5–8)·10–4, Тпл=235–265°С, Тс=80–90°С, Тхр=–80°С. Малогидрофилен (водопоглощаемость 0,5%). Нерастворим в обычных, широко применяемых органических растворителях: ацетоне, ксилоле, диоксане, этилацетоне и т.п. Растворяется в дихлорэтане, фенолах, муравьиной кислоте. При длительном воздействии концентрированной щелочи и концентрированной серной кислоты разрушается; при повышенных температурах легко окисляется. Плохо горит, образуя коптящее пламя.
Обычно ПЭТФ используют в виде пленок и волокон. Механические свойства его подобны механическим свойствам ПА и мало изменяются в широком интервале температур. При содержании кристаллической фазы до 70% обладает повышенной механической прочностью и нагревостойкостью (265°С). Наибольшую механическую прочность имеют пленки толщиной около 6,5 мкм.
ПЭТФ – слабополярный диэлектрик. Пленки из него обладают хорошими электрическими свойствами, электрическая прочность при микронных толщинах достигает 103 кВ/мм. В электроизоляционной технике ПЭТФ-пленки используют для межслойной изоляции в обмотках трансформаторов, дросселей и подобных изделиях, работающих в интервале температуры от минус 60 до плюс 150°С. Применяют пленки также в производстве конденсаторов, которые в сравнении с бумажными обладают более высокой рабочей температурой (до 150°С ) и меньшими габаритами.
Полиуретаны (ПУР)– высокомолекулярные соединения, содержащие в химических звеньях молекулярной цепи уретановую группу
В зависимости от природы исходных компонентов и строения образующихся макромолекул ПУР могут быть термопластичными и термореактивными, пластичными и хрупкими, мягкими и эластичными.
Из ПУР изготавливают эластичные, устойчивые к старению волокна и пленки, лаки, клеи (например, ПУ-2), компаунды высоко- и низкочастотные, обладающие высокой тепло-, водо- и атмосферостойкостью. Лаки используют для эмалирования проводов; клеи пригодны для склеивания металлов, пластиков, силикатных и органических стекол, керамики, резины и многих других материалов; компаунды применяют для пропитки и заливки (герметизации) высоковольтных трансформаторов, полупроводниковых выпрямителей, конденсаторов и других изделий. Компаунды стойки к циклическим температурным ударам. Колебания температуры от минус 60 до плюс 60°С не нарушают герметичности за счет образования трещин. Провода эмалированные ПУР более технологичны при монтаже, так как ПУР проявляют свойства флюса, и поэтому не требуется предварительная зачистка эмалевой изоляции, пайку можно производить путем погружения незачищенного конца провода в расплавленный припой либо непосредственно обработкой паяльником.
Широкое применение нашли полиуретановые эластомеры. Они масло- и бензостойкие, обладают высокой стойкостью к истиранию и высокой эластичностью, сочетающейся с относительно большой прочностью.
Изделия из ПУР могут работать в условиях высокой влажности в температурном интервале от минус (30–40)°С до плюс (110–120)°С без существенного ухудшения механических свойств.
Реактопласты или термореактивные полимеры (смолы) – это такие материалы, которые при нагревании претерпевают необратимые изменения свойств в результате сшивания молекулярных цепей поперечными химическими связями. Материал при этом отверждается – переходит из расплавленного состояния в твердое.
При небольшом числе поперечных связей образуются мягкие эластичные продукты (например, резины). По мере же увеличения числа связей повышаются жесткость и твердость полимерного материала, а при образовании очень частой сетки из поперечных связей получается совершенно твердый материал, который и является реактопластом. При повторном нагревании он уже не плавится, в растворителях не растворяется. Реактопласты имеют пространственное («сшитое») строение молекул, и в данном случае весь блок полимера можно рассматривать как одну гигантскую молекулу.
Поперечные химические связи в реактопластах могут образовываться как без добавления других веществ – в результате только химического взаимодействия функциональных групп самого материала, так и при помощи специальных веществ – отвердителей, вводимых в материал. Обычно отверждение происходит при высоких температурах (80–160°С) и очень быстро. Однако, уже известны системы полимер–отвердитель, в которых сшивание молекулярных цепей происходит и при низких температурах. В первом случае имеет место горячее отверждение, во втором – холодное отверждение.
Реактопласты содержат функциональные полярные группы и поэтому являются полярными диэлектриками. Электрические свойства их примерно такого же порядка, что и у полярных термопластов: ε=3,5–7,7; ρ=109–1014 Ом·м; tgδ≈10–3–10–1; Enp≈до 20 кВ/мм (в тонких пленках Епр=80 кВ/мм и выше). В реактопласты для улучшения тех или иных свойств вводят специальные добавки (стабилизаторы, пластификаторы, твердые наполнители); для придания желаемого цвета их окрашивают.
Фенолоформальдегидные смолы (ФФ) – продукт поликонденсации фенола С6Н5ОН и формальдегида СН2О. ФФ полимер имеет сложное пространственное строение, структурный элемент которого содержит неуравновешенные полярные группы, которые обусловливают его полярность.
ФФ применяют в производстве пресс-порошков, волокнитов, слоистых пластмасс, компаундов, клеев и лаков. Они хорошо совмещаются с такими полимерами, как ПВХ, ПА, каучуки. Изделия, полученные на их основе, отличаются высокими показателями механической прочности, теплостойкости, водо- и кислотостойкости, а клеи – хорошей адгезией к разнообразным материалам (металлам, стеклам, древесине).
При поликонденсации фенола с формальдегидом образуются как термореактивные, так и термопластичные продукты. Термореактивные продукты называют резольными (или резолами), а термопластичные – новолачными (или новолаками). Если в реакции смолообразования на моль фенола приходится не менее одного моля формальдегида и берется щелочной катализатор (например, аммиак), то образуется смола, называемая бакелитом. В начальной стадии (стадии А) бакелит представляет собой олигомер, называемый резолом. Резол имеет цвет от светло-желтого до красного, плавится при температуре 55–80°С и легко растворяется в спирте и ацетоне. Если резольный олигомер нагреть до 140–160°С, то через 1–3 мин в результате процессов сшивания он затвердеет, перейдя в бакелит стадии С, называемыйрезитом. В готовых изделиях бакелит находится в виде резита. Повышение давления, так же как и температуры, ускоряет процесс отверждения резола.
Резит – это реактопласт с очень густой сеткой поперечных химических связей. При повторном нагревании он не плавится, в растворителях не растворяется, имеет высокие нагревостойкость, механическую прочность и твердость, малую эластичность и невысокую влагостойкость.
Если при получении ФФ смолы фенола взять в избытке, а катализатор кислотный (например, НСl), то образуется смола типановолака. Это термопластичная смола, представляющая собой смесь олигомеров линейного строения, цвета от светло-коричневого до темно-коричневого. При нагревании смола плавится (при 100–120°С), в растворителях (спирте, ацетоне) растворяется. Применяют новолачные смолы в производстве клеев типа БФ и пресс-порошков. Новолаки отверждают обычно при температуре 160–180°С, при этом образуются неплавкие и нерастворимые продукты (реактопласты).
Длительная нагревостойкость ФФ полимера составляет 120°С. Разрушающее напряжение при статическом изгибе σи=50–100 МПа, σуд=10–20 кДж/м2. Отрицательным качеством является его склонность к образованию трекингов, т.е. когда под действием поверхностных электрических разрядов на поверхности изделия возникают (токопроводящие) науглероженные следы. Полимер горюч, при горении выделяется запах фенола и формальдегида.
Карбамидоформальдегидные (мочевиноформальдегидные) (КФ) и меламиноформальдегидные (МФ) смолы получают путем поликонденсации формальдегида СН2О соответственно с карбамидом (мочевиной) (NH2)2CO и меламином C3H6N6 и их производными.
Олигомерные продукты КФ и МФ широко применяют в качестве связующих в производстве слоистых пластиков, пресс-порошков, клеев и лаков. Изделия, полученные на основе КФ и МФ смол, имеют достаточно высокую механическую прочность, теплостойкость, хорошую адгезию; они бесцветны и прозрачны, что позволяет окрашивать их в различные цвета, в том числе светлые тона. Изделия, полученные на основе МФ смолы, кроме того, обладают высокой водостойкостью.
Эпоксидные смолы (ЭП) - очень большая группа материалов, для которых характерно наличие в молекулах эпоксидных групп :
Эти группы полярные, поэтому ЭП смолы – полярный диэлектрик.
К ним относятся смолы марок ЭД-24, ЭД-22, ЭД-20, ЭД-16, ЭД-14, ЭД-8, ЭД-4. Если ЭД-24 имеет молекулярную массу 350–400 и представляет собой жидкость с невысокой вязкостью, то ЭД-4 имеет молекулярную массу (15–70)·103 и при комнатной температуре представляет собой твердый продукт.
Все ЭП смолы в исходном состоянии растворяются в ацетоне и ряде других полярных растворителей и представляют собой олигомеры. Каждая молекула олигомера имеет не менее двух эпоксидных групп. В таком виде ЭП олигомеры могут длительно храниться без изменения свойств. Если к ним добавить отвердитель (обычно 10 мас.%), то произойдет отверждение и образуется трехмерный («сшитый») полимер. Отверждение происходит за счет процессов полимеризации без выделения побочных низкомолекулярных продуктов (например, воды) и сопровождается небольшой (0,5–2%) усадкой. В зависимости от типа отвердителя ЭП смолы могут отверждаться при комнатной температуре («холодное отверждение») либо при нагревании до 80–150°С («горячее отверждение»). В качестве отвердителей холодного отверждения используют алифатические амины и горячего – ангидриды кислот малеиновой, фталевой. Отвердители ангидридного типа дают возможность получать полимеры с более высокими электрическими и механическими характеристиками и с большей нагревостойкостью по сравнению с отвердителями аминами; к тому же они менее токсичны, чем амины.
ЭП смолы широко применяют в электро- и радиотехнике в качестве электроизоляционных и герметизирующих материалов. Ценятся ЭП смолы из-за высокой адгезии к различным материалам (металлам, неорганическим стеклам, керамике, пластмассам). Благодаря этому свойству их используют для изготовления клеев, лаков и различных компаундов. Пленки из ЭП смол отличаются высокой механической прочностью, химической стойкостью и стойкостью к атмосферным воздействиям.
Компаунды – это ЭП смолы, модифицированные пластификаторами (5–15 мас.%), ненасыщенными полиэфирами, каучуками и другими соединениями. Компаунды изготовляют без наполнителей и с наполнителями (до 100% от массы полимера).
Пластические массы– это композиционные материалы, состоящие обычно из связующего (полимера), наполнителей и других ингредиентов и находящиеся при эксплуатации в стеклообразном или кристаллическом состоянии. Основными образующими их компонентами являются связующее и наполнители.
Связующееобразует непрерывную фазу – матрицу, которая объединяет в единое целое все составные части пластмассы и в значительной мере обусловливает комплекс ее эксплуатационно-технических характеристик. В качестве связующего обычно используют органические смолы синтетические или природные, термопластичные или термореактивные, способные при нагреве и одновременном воздействии давления формоваться – деформироваться и приобретать заданную форму. Формование термопластов не сопровождается изменением химического состава полимера и, следовательно, его свойств. При формовании реактопластов протекают химические процессы отверждения олигомеров, в результате чего образуется трехмерный («сшитый») полимер, имеющий другую структуру и свойства.
Наполнителиобразуют прерывистую фазу, прочно сцепленную связующим. Наполнители – в основном инертные вещества. По своей природе они разделяются на органические и неорганические, которые, в свою очередь, делятся на наполнители порошкообразные, волокнистые и листовые.
К органическим порошкообразным наполнителям относятся: древесная мука, лигнин и другие дисперсные полимеры; к волокнистым – хлопковые и льняные очесы, линтер, сульфатная целлюлоза, синтетические волокна, текстильная и бумажная крошка; к листовым – бумага, ткань.
К неорганическим порошкообразным наполнителям относятся: молотые слюда и горные породы, тальк, каолин, кальцит, кварцевая мука, ферромагнитный порошок; к волокнистым – стекловолокно, длинноволокнистый асбест, базальтовое волокно; к листовым – слюда, стеклоткань.
Наполнители улучшают механические характеристики пластмассы, увеличивают нагревостойкость и существенно удешевляют материал. Однако при этом гигроскопичность и электрические свойства могут ухудшаться, поэтому в пластмассы, от которых требуются высокие электроизоляционные свойства, наполнители обычно не вводят.
Кроме наполнителя, в пластмассы для придания им желаемых свойств вводят пластификаторы, отвердители, смазывающие вещества, красители, антипирены и другие специальные добавки.Таким образом, пластмасса обычно является многокомпонентной системой.
Пластификаторыприменяют для улучшения технологических и эксплуатационных свойств пластмасс. Они понижают температуру стеклования и температуру хрупкости, расширяют интервал высокоэластического состояния полимера.
Отвердители вводят в композиции на определенной стадии переработки в целях создания (или увеличения) поперечных (боковых) химических связей между молекулами полимера.
Смазывающие вещества(парафин, воск, силиконовые жидкости используют в целях увеличения текучести и предотвращения прилипания пластмасс к оборудованию во время их изготовления и переработки в изделия.
Стабилизаторамиявляются вещества, повышающие стойкость полимеров к воздействию тепла, света или кислорода воздуха. Поэтому различают термостабилизаторы, фотостабилизаторы, антиоксиданты – стабилизаторы против термоокислительной деструкции.
Путем подбора полимеров в качестве связующего, наполнителей и других ингредиентов получают пластмассы сразнообразными свойствами. Пластмассы с небольшим содержанием добавок (смазок, стабилизаторов, красителей) называют ненаполненными, а с большим (до 65%), в том числе с наполнителями, – наполненными.
В электро- и радиотехнике они используются в качестве как электроизоляционных, так и конструкционных материалов, что обусловлено достаточно высоким уровнем их электрических и механических свойств, стойкостью к воздействию высоких и низких температур, химо- и влагостойкостью, эластичностью, небольшой плотностью и легкостью переработки в изделия. В зависимости от физического состояния полимера (связующего) в момент формообразования различают следующие основные методы переработки пластмасс:
1) переработка в вязкотекучем состоянии – литье под давлением, экструзия, горячее прессование, выдавливание;
2) переработка в высокоэластическом состоянии – горячая штамповка, пневмо- и вакуумформовка, обработка резанием;
3) переработка в стеклообразном состоянии – разделительная штамповка, обработка резанием.
Существует метод изготовления изделий непосредственно изжидкого мономера – путем его полимеризации в специальной форме.
Пресс-материалы с порошкообразным наполнителемчаще всего являются исходными материалами для изготовления из пластмасс многих изделий самой разнообразной формы,в которых наполнитель применяют впорошкообразном виде. Пресс-порошки представляют собой навески всех компонентов, высушенных, тонко измельченных и тщательно перемешанных. В зависимости от назначения изделий к пресс-порошкам предъявляются различные требования.
Различают следующие основные группы пресс-порошков.
Пресс-порошки общетехнического назначенияпроизводят на основе новолачных ФФ олигомеров и древесной муки. Предназначены для изготовления ненагруженных армированных и неармированных изделий технического назначения широкого потребления (ламповые патроны, штепселя, розетки, вилки, рукоятки, корпуса проигрывателей). Электрические свойства изделий этой группы ухудшаются при работе во влажной атмосфере.
Жаростойкиепресс-порошки изготовляют на основе новолачных ФФ олигомеров и неорганических наполнителей (слюды, асбеста) и применяют для изготовления радиодеталей и электроустановочных изделий, работающих в условиях высоких температур.
Электроизоляционные пресс-порошки получают на основе резольных ФФ олигомеров и древесной муки и применяют для изготовления армированных и неармированных деталей электротехнического назначения, эксплуатация которых допустима в среде масла и бензина.
Высокочастотные пресс-порошки производят на основе резольных ФФ олигомеров и неорганических наполнителей (слюды, кварцевой муки). Используют для изготовления ненагруженных и слабоармированных деталей радиотехнического назначения, работающих на воздухе при повышенной влажности (даже в условиях тропического климата).
Безаммиачные (не выделяющие при разложении аммиак) пресс-порошки изготавливают на основе резольных олигомеров, полученных путем совместной поликонденсации фенола и анилина с формальдегидом, и древесной муки. Используют их в производстве деталей слаботочной радиоаппаратуры, соприкасающихся или находящихся рядом с серебряными контактами.
Ударопрочные пресс-порошки производят на основе новолаков, совмещенных с каучуком, и наполнителя из древесной муки и применяют для изготовления деталей общетехнического назначения, армированных деталей сложной конфигурации.
Влагохимстойкие пресс-порошки приготавливают на основе новолаков, совмещенных с ПВХ, и органического или неорганического наполнителей (древесной муки, графита, каолина). Предназначены для изготовления радиотехнических деталей, крышек и пробок аккумуляторных бачков.
Пресс-материалы с волокнистым наполнителем обеспечивают изделиям более высокие механические характеристики, чем песс-порошки. Поэтому в ряде областей используют пресс-материалы с волокнистым наполнителем. Из волокнистых материалов наиболее широко применяются хлопковая целлюлоза, длинноволокнистый асбест и стеклянное волокно. Пресс-материалы, в которых в качестве наполнителя использована хлопковая целлюлоза, называют волокнитами, длинноволокнистый асбест – асбомассами и фаолитами, стеклянное волокно – стекловолокнитами.
Пресс-материалы с листовым наполнителем имеют слоистую структуру, поэтому и называются слоистыми пластиками. К ним относятся гетинаксы, текстолиты, стеклотекстолиты, асботекстолиты, стекловолокнистые анизотропные материалы (СВАМ) и древесно-слоистые пластики (ДСП). В электро- и радиотехнике наиболее применимы первые три слоистых пластика.
При изготовлении СВАМ и ДСП в качестве листового наполнителя используют шпон стеклянный и древесный, соответственно. Стеклянный шпон изготавливают из ориентированных стеклянных волокон (наполнитель) и связующего – ФФ олигомера. Для изготовления древесного шпона используют березу или бук.
Слоистые пластикипредставляют собой пластмассы, в которых наполнителем является листовой волокнистый материал (бумага, ткань, нетканый материал) с параллельно расположенными слоями, что определяет анизотропию их свойств. В зависимости от назначения различают: конструкционные, электроизоляционные и декоративные слоистые пластики. Производят слоистые пластики листового строения, профильные и в виде трубок и цилиндров. Последние называют намотанными изделиями.
Рассмотрим электроизоляционные пластики. Они обладают высоким уровнем механических свойств в широком интервале температур. В зависимости от химической природы связующего и наполнителя электрические свойства электроизоляционных слоистых пластиков могут изменяться в широких пределах (ε=6–8; ρ=108–1014 Ом·м; tgδ=(2–10)·10–2; Eпр=8–33 кВ/мм при h=1 мм), а сами пластики длительно эксплуатироваться при температурах до плюс 180°С. Наиболее распространенные виды этого материала – гетинакс и текстолит сразличными наполнителями. Все эти материалы получают методом горячего прессования или намотки листовых волокнистых материалов, предварительно пропитанных или лакированных термореактивным связующим.
Гетинакс - получают путем прессования бумаги в два или несколько слоев, пропитанной олигомерами феноло- или крезолоформальдегидных смол, или других реактопластов, или их смесями. Прессование производится при температуре 150–160°С, давлении 6–10 МПа и времени выдержки под давлением из расчета 2–5 мин/мм толщины. При этой температуре олигомер расплавляется, заполняет поры между волокнами бумаги и отдельными ее листами и затвердевает (переходит в стадию резит).
Гетинакс производят в зависимости от числа слоев толщиной от 0,2 мм до 50 мм, его плотность 1350–1450 кг/м3. Материал имеет заметную анизотропию свойств. Например, объемное сопротивление гетинакса вдоль слоев в 50–100 раз, а Епрв 5–8 раз ниже, чем поперек слоев. Недостатком его, так же как и других пластмасс на основе ФФ смол, является низкая трекингостойкость.
Сравнительно новые материалы – гетинакс на основе полиэтилентерефталатной бумаги и эпоксидной смолы и гетинакс, облицованный с обеих сторон слоем полиэтилентерефталатной бумаги, пропитанной эпоксидной смолой. Отличительные особенности гетинакса на основе ПЭТФ-бумаги – высокие показатели влагостойкости, механических и электрических свойств, хорошая перерабатываемость методом штамповки. Известен гетинакс, изготовленный на основе стеклянной бумаги – стеклогетинакс.
Фолъгированный гетинакс производят для изготовления печатных схем низкочастотных цепей радиоаппаратуры. Он представляет собой листовой материал, покрытый с одной или с обеих сторон фольгой из электролитической меди (99,9%) толщиной 5;18;25;35;50;70;105 мкм. Чем тоньше медная фольга, тем более плотный металлический рисунок можно получить.
Текстолит - представляет собой слоистый пластик, изготовленный из двух или большего числа слоев ткани, предварительно пропитанной олигомером ФФ смолы или другого реактопласта. В качестве наполнителя могут использоваться ткани хлопчатобумажная, стеклянная (стеклотекстолит), полиэтилентерефталатная (лавсановый текстолит), асбестовая (асботекстолит), а также нетканые материалы.
Наиболее распространенным является текстолит на основе хлопчатобумажной ткани. В сравнении с гетинаксом у него более высокие значения удельной ударной вязкости, стойкости к истиранию и сопротивлению раскалывания. Электрические свойства примерно такие же, как и у гетинакса, исключение составляет электрическая прочность, которая заметно ниже. Однако стоимость текстолита в несколько раз выше стоимости гетинакса, так как при его изготовлении используют дорогой наполнитель – хлопчатобумажную ткань. Поэтому его целесообразно применять лишь в изделиях, подвергающихся ударным нагрузкам или истиранию (детали переключателей).
В производстве электротехническогостеклотекстолитаиспользуют стеклоткань, полученную из алюмоборсиликатного стекла с содержанием окислов щелочных металлов не более 0,5%. В качестве связующего используют кремнийорганические лаки или композиции на основе кремнийорганических и эпоксидных смол. Изготавливают также фольгированный стеклотекстолит, который в сравнении с фольгированным гетинаксом имеет более высокую стойкость к повышенным температурам и влажности. Электрическая прочность стеклотекстолита почти в три раза выше, чем у текстолита из хлопчатобумажной ткани.
Резины -представляют собой вулканизированную многокомпонентную систему на основе каучуков. Из-за своей высокой эластичности резины относятся к классу эластомеров.
Отличительной особенностью эластомеровявляется высокая эластичность и широкий температурный интервал между Tс и Tт. При этом Тт находится намного выше максимально допустимой рабочей температуры, а Тс – ниже минимальной рабочей температуры. К эластомерам принадлежат такие материалы, как полиуретаны, некоторые виды кремнийорганических полимеров, смесь ПЭ (90%) и ПИБ (10%), пластифицированный ПВХ. Вулканизация каучуков заключается в частичном разрыве двойных связей макромолекул и сшивании их атомами серы (–S–) с образованием за счет боковых химических связей пространственной структуры. Процесс вулканизации протекает при температуре 138–200°С. Каучуки вулканизируют, чтобы устранить их пластичность и повысить эластичность (упругость). У технических резин относительное удлинение при разрыве составляет 150–500% и сохраняется до минус (40–60)°С.
При изготовлении резины в ее состав, кроме каучука, вводят вулканизирующие агенты (серу или тиурам, а чаще их смесь), ускорители вулканизации, наполнители (мел, тальк, каолин, окись цинка), которые улучшают механические свойства и удешевляют резину (наполнители дешевле каучуков в 20–75 раз), мягчители (стеарин, парафин) – для улучшения технологических свойств, антиокислители, красители и другие ингредиенты, которые составляют вместе до 65% и более (остальное каучук).
В зависимости от количества серы, вводимой в каучук, различают резину мягкую и твердую. Мягкая резинасодержит 1–3% серы и обладает высокой эластичностью. Твердая резина (эбонит)содержит 30–35% серы – это твердый материал с высокой стойкостью к ударным нагрузкам, но невысоким относительным удлинением при разрыве (2–6%).
Резина широко используется в производстве проводов и кабелей, диэлектрических перчаток и других изделий. Существенный недостаток резины – низкая стойкость к действию озона, кислорода, света (особенно ультрафиолетового), тепла, электрических разрядов. Под действием указанных факторов резина стареет и в результате термоокислительного структурирования становится хрупкой и растрескивается. Если старение резины вызвано термоокислительной деструкцией, то она размягчается и становится липкой. Этот вид старения обычно наблюдается в резинах с относительно высоким содержанием натурального каучука или его синтетического аналога и небольшой частотой боковых химических связей из-за низкого содержания серы (1–1,5%). При непосредственном контакте резины с медью свободная сера химически взаимодействует с последней, образуя сернистую медь CuS. Поэтому в таких случаях медная жила провода предварительно покрывается слоем оловянно-свинцового припоя либо используется тиурамовая резина, для изготовления которой берут не чистую серу, а ее соединение –тиурам [(СН3)2 N-CS-S]2.
Тиурамовая резина – это электроизоляционная резина, не содержит свободной серы и поэтому может непосредственно накладываться на медную жилу провода; кроме того, она более нагревостойка (65°С), чем «сернистая» резина (55°С).
В кабельной технике используют также резины, содержащие сажу. Эти резины имеют черный цвет и обладают сравнительно высокой стойкостью к действию солнечного света (его УФ-спектра), хорошими механическими, но очень низкими электроизоляционными свойствами. Поэтому такие резины используют только в качестве шланговой изоляции кабелей.
В производстве резин используют смеси каучуков натурального и синтетического. Натуральный каучук (НК) получают из млечного сока (латекса) каучуконосных деревьев, произрастающих в странах с тропическим климатом. В чистом виде НК представляет собой полимер изопрена (метилдивинила)
Это неполярный диэлектрик (ε=2,4; ρ=1014 Ом·м; tgδ=0,002, Eпр=40 кВ/мм). При вулканизации НК из-за влияния атомов серы усиливаются полярные свойства материала, показатели электрических свойств понижаются (ε=3–7; ρ=1013 Ом·м; tgδ=0,02–0,1; Епр=20–30 кВ/мм).
К синтетическим каучукам (СК), наиболее широко используемым в электроизоляционной технике, относятся: изопреновый (СКИ-30), бутадиеновый (СКВ), бутадиен-стирольный (СКС), бутилкаучук (БК), хлорпреновый (наирит), бутадиен-нитрильный (СКН). Первые четыре вида каучуков являются неполярными диэлектриками и по своим электрическим свойствам близки к НК; последние два – диэлектрики полярные, с пониженными электроизоляционными свойствами (ε=8–10; ρ=108 Ом·м; tgδ=0,3; Епр=12–22 кВ/мм). Резины на их основе более стойкие к действию масел, бензина, окислителей, тепловому старению, менее газопроницаемы.
Бутадиеновый каучук (–СН2–СН=СН–СН2–)n – продукт полимеризации бутадиена (дивинила). При температуре 200–300°С без вулканизирующих агентов в результате дополнительной полимеризации по месту двойных связей бутадиен переходит в твердый продукт, по механическим свойствам похожий на эбонит, но более стойкий к действию температуры, кислот и органических растворителей. На основе эскапона изготовляют лаки, лакоткани.
Получают бутадиеновый каучук и стереорегулярный. У нас он известен как СКД, в ФРГ – Буна ЦБ. У него высокая морозостойкость (до минус 65°С).
Бутадиен-стирольный каучук – продукт совместной полимеризации бутадиена СН2=СН–СН=СН2 и стирола СН2=СН2С6Н5. У нас известны его марки СКС-30, СКС-30 АРКМ-15, СКС-30 АРПД, в ФРГ – Буна С-3, буна С-4. По электроизоляционным свойствам каучук СКС-30 АРПД не уступает НК, но имеет более низкие прочностные свойства, поэтому в резиновых смесях его применяют совместно с НК.
Бутилкаучук получают путем совместной полимеризации изобутилена и небольшого количества изопрена. На его основе производят резины, стойкие к действию озона, кислорода и кислот; газопроницаемость у них ниже в 10–20 раз (важная особенность), чем у резин на основе НК, но меньше эластичность.
Хлорпреновый каучук получают путем полимеризации хлорпрена. Отечественное название наирит, в ФРГ, США, Японии – неопрен. Это полярный диэлектрик. На его основе производят масло и бензостойкие резины.
Бутадиен-нитрильный каучук – продукт совместной полимеризации бутадиена и акрилонитрила. Каучук, вулканизированный тиурамом, более нагревостойкий. Известны следующие марки: СКН-40, СКН-26 и СКН-18. В ФРГ выпускают Пербунан, Буна Н, Буна НН.
Кремнийорганические каучуки, в отличие от рассмотренных, у которых в основе строения молекулярных цепей находятся атомы углерода, имеют остов макромолекул, построенный из чередующихся атомов кремния и кислорода:
Это линейные полимеры, полученные путем поликонденсации. Недостатком является низкая прочность на раздир. Кремнийорганические резины применяют для изготовления различных изоляторов, кабелей, прокладок, шайб, трубок и других изделий.
Тема 13.Жидкие диэлектрики
Жидкие диэлектрики в сравнении с газообразными обладают рядом преимуществ: у них примерно в три раза и более выше электрическая прочность, в три раза больше теплоемкость, в тридцать раз выше теплопроводность. Электрические свойства в значительной мере зависят от степени их очистки. Даже небольшое содержание примеси заметно ухудшает их электрические характеристики. Особенно существенно на электрическую прочностьжидких диэлектриков влияет нерастворенная полярная примесь, например вода.
Основное назначение жидких диэлектриков заключается в повышении электрической прочности твердой пористой изоляции, отводе тепла от обмоток трансформатора, гашении электрической дуги в масляных выключателях.
Наиболее распространенными жидкими диэлектриками являются: нефтяные масла – трансформаторное, конденсаторное и кабельное; синтетические жидкости – полихлордифенил (совол, совтол), кремнийорганические и фторорганические. Растительные технические масла – касторовое, льняное, конопляное и тунговое – в настоящее время в электроизоляционной технике применяются ограниченно.
Нефтяные электроизоляционные масла -получают путем ступенчатой перегонки нефти с выделением и последующей обработкой первой масляной фракции – солярового масла. Обработка заключается в тщательной очистке от химически нестойких соединений и полярной примеси. Очистка достигается путем последовательной обработки серной кислотой, щелочью, промывки водой и сушки. В ряде случаев электроизоляционные масла дополнительно обрабатывают адсорбентами, которые активно поглощают остатки воды и полярную примесь.
Нефтяные масла– это слабовязкие, практически неполярные жидкости. По химическому составу они представляют смесь различных углеводородов парафинового, нафтенового, ароматического и нафтеново-ароматического рядов с небольшим содержанием присадок, улучшающих их стойкость к термоокислительному старению, а также температурно-вязкостные характеристики.
Нефтяные масла имеют желтый цвет (от почти бесцветного до темного). Чем глубже очистка, тем светлее масло. С ростом содержания ароматических углеводородов и полярной примеси гигроскопичность масел увеличивается. Поэтому масла всегда гигроскопичны и имеют пониженные электрические свойства. Химический состав, а, следовательно, свойства и стабильность масла зависят от месторождения нефти.
Нефтяное трансформаторное масло - получило наиболее широкое применение в высоковольтных аппаратах: трансформаторах, масляных выключателях, высоковольтных вводах. В трансформаторах нефтяное масло выполняет две основные функции: во-первых, заполняя поры волокнистой изоляции и промежутки между проводами обмоток, а также токопроводящими частями и баком трансформатора, значительно повышает электрическую прочность изоляции; во-вторых, улучшает отвод тепла, выделяющегося за счет потерь мощности в обмотках и в сердечнике трансформатора. В масляных выключателях трансформаторное масло способствует еще и быстрому гашению электрической дуги.
Нефтяное трансформаторное масло подразделяют на:
– свежее – поступившее от завода-изготовителя; оно может иметь отклонение от нормативных показателей по влаго- и газосодержанию;
– чистое, сухое – это масло «свежее», дополнительно прошедшее обработку (осушивание); оно соответствует всем нормируемым показателям и готово к заливке в оборудование;
– регенерированное – отработанное, прошедшее очистку с помощью физических, химических и физико-химических методов до требований нормативно-технической документации и пригодное к дальнейшему применению;
– эксплуатационное – залитое в оборудование и по показателям соответствующее нормам на эксплуатационное масло;
– отработанное – слитое из оборудования по истечению установленного срока службы или утратившее в процессе эксплуатации качества, установленные нормативно-технической документацией.
По электрофизическим свойствам нефтяное трансформаторное масло является неполярным диэлектриком. Поэтому в чистом масле диэлектрические потери обусловлены в основном токами проводимости, величина которых мала, следовательно, малы и диэлектрические потери (tg δ). Механизм пробоя масла объясняет теория теплового пробоя, которая учитывает решающее влияние на образование газоразрядного канала проводимости нерастворенной в масле полярной, полупроводящей и проводящей примеси. Чистое масло имеет относительно высокие значения Епр.Электрическую прочность электроизоляционных масел обычно характеризуют величиной пробивного напряжения Unp в стандартной измерительной ячейке с расстоянием между электродами 2,5 мм.
В зависимости от степени очистки масла и частоты измерительного поля при 20°С ε =2,2–2,3; tgδ=10–4, ρ=1010–1013 Ом·м, Епр=10–28 кВ/мм. У чистого сухого масла Епр при нагревании от 60 до 80°С практически не изменяется, а выше 80°С снижается в результате образования пузырьков газа из легких фракций масла и, как следствие этого, увеличения неоднородности электрического поля.
Эксплуатационно-технические характеристики трансформаторного масла нормируются стандартом. В табл. 3.4 приведены предельно допустимые значения основных характеристик нефтяного трансформаторного масла, подготовленного к заливке, а также находящегося в эксплуатации (в электрооборудовании).
Таблица 3.4
Предельно допустимые значения показателей качества трансформаторного масла, подтовленного и залитого в электрооборудование.
Показатель | Значение показателей качества трансформаторного масла | |
до залива в электрооборудование | после залива в электрооборудование | |
Пробивное напряжение, кВ, не менее, для трансформаторов, аппаратов и вводов напряжением до 15 кВ | 30 | 25 |
15–35 кВ | 35 | 30 |
60–150 кВ | 60 | 55 |
220–500 кВ | 60 | 55 |
750 кВ | 70 | 65 |
1150 кВ | 70 | 70 |
Тангенс угла диэлектрических потерь, %, не более, при 90°С до 500 кВ | 2,2 | 2,6 |
750 кВ | 0,5 | 0,7 |
1150 кВ | 0,5 | 0,5 |
Температура вспышки в закрытом тигле, °С, не ниже | 135 | 135 |
Газосодержание, % объема, не более (для герметичного электрооборудования) | 0,1 | 0,2 |
Вода, растворенная в масле, увеличивает электропроводность и tgδ, и изменяет электрическую прочность. Содержание воды(влаги) в трансформаторном масле ухудшает его эксплуатационные свойства. Масло способно поглощать воду при 20°С ~0,1%, а при 60°С ~0,2%. При дальнейшем добавлении вода осаждается на дно сосуда. При содержании 0,05% нерастворенной воды электрическая прочность масла снижается более чем на 20%, но особенно сильно снижается при поглощении воды, когда масло загрязнено органическими волокнами. Масло может увлажняться как при транспортировке и хранении, так и в процессе эксплуатации вследствие химических процессов старения и возможного соприкосновения его с воздухом, всегда содержащим влагу.
Один из важнейших показателей, указывающих на развитие процессов окисления в трансформаторном масле, – кислотное число(к.ч.). Величина к.ч. непрерывно возрастает вследствие накопления в масле кислых продуктов, образующихся под воздействием молекулярного кислорода, т.е. в результате термоокислительной деструкции. Резкое повышение содержания кислых продуктов в масле указывает на необходимость его замены или регенерации. Кислотное число масла перед заливкой в трансформатор не должно превышать 0,02 мг КОН/1 г масла для электрооборудования с Upa6 до 500 кВ и 0,01 мг КОН/1 г – свыше 500 кВ с ингибирующей присадкой. Предельно допустимое значение к.ч. масла составляет 0,25 мг КОН/1 г. При достижении к.ч. этого значения трансформаторные масла заменяют (или регенерируют).
Нефтяные масла представляют собой горючую жидкость. Степень их огнеопасности, зависящая от содержания в масле легко испаряющихся горючих веществ, оценивается температурой вспышки, которая у трансформаторного масла должна находиться в пределах 135–150°С, но не ниже 135°С.
Температура застывания масла– очень важная характеристика для масел, используемых в масляных выключателях и контактных устройствах для регулирования напряжения под нагрузкой, эксплуатируемых на открытых подстанциях в районах с суровой зимой. С понижением температуры вязкость масла существенно возрастает, надежность работы электроаппарата резко снижается.
В соответствии с требованиями МЭК (Международной электротехнической комиссии) все отечественные трансформаторные масла имеют температуру застывания не выше минус 45°С.
Рассмотрим процессы, происходящие при старении нефтяного трансформаторного масла. При эксплуатации маслоналивного электрооборудования под воздействием кислорода воздуха (или другого окислителя) в масле протекают глубокие необратимые химические процессы, приводящие к ухудшению всего комплекса его эксплуатационно-технических характеристик. Эти процессы существенно ускоряются под действием теплового и электрического полей. Химические процессы старения вызывают, с одной стороны, деструкцию молекул масла и образование низкомолекулярных ионогенных продуктов (перекисей, органических кислот, воды и др.), увеличивающих ионную проводимость масла, с другой – процессы структурирования («осмоления») окисленных молекул с образованием коллоидных частиц и более высокомолекулярных продуктов – шлама. Коллоидные частицы совместно с ионогенной примесью снижают удельное сопротивление масла и увеличивают диэлектрические потери. Шлам и другие нерастворенные в масле продукты старения, а также частицы примесей, внесенные в него извне, образуют мелкодисперсную фазу, которая увеличивает неоднородность электрического поля в масле, существенно снижает его электрическую прочность, а также увеличивает tg . Особенно опасными являются примеси, размер частиц которых составляет от 2 до 10 мкм.
Таким образом, старение ухудшает рабочие параметры масла. Поэтому при получении масла, его хранении и перед заливкой в электрооборудование, а также в процессе эксплуатации следует производить систематический контроль в соответствии с РД 34.43.105–89 («Методические указания по эксплуатации трансформаторных масел»).
Нефтяное конденсаторное масло. Конденсаторное масло получают из трансформаторного путем его более глубокой очистки адсорбентами и обезгаживания в вакууме. Его электрические свойства лучше, чем у трансформаторного масла: ε =2,1–2,3, tgδ не более 2·10–3 при 20°С и частоте 1 кГц; ρ не менее 1012 Ом·м при 20°С и 1011 Ом·м при 100°С, Eпр не ниже 20 кВ/мм, температура застывания минус 45°С.
Конденсаторное масло используют для пропитки бумажных конденсаторов, в особенности силовых. При пропитке в результате заполнения пор бумаги маслом увеличиваются диэлектрическая проницаемость и электрическая прочность бумаги, а, следовательно, возрастают емкость конденсатора и его рабочее напряжение или же при тех же параметрах емкости и рабочего напряжения снижаются габариты, масса и стоимость конденсатора.
Для пропитки бумажных конденсаторов используют также вазелиновое масло, которое по электрическим свойствам близко к нефтяному конденсаторному маслу, но имеет более высокую температуру застывания (минус 5°С).
Нефтяное кабельное масло. Кабельное масло применяют для пропитки бумажной изоляции силовых кабелей с рабочим напряжением до 35 кВ в свинцовой или алюминиевой оболочке, а также для заполнения металлических оболочек маслонаполненных кабелей на напряжения до 110 кВ и выше. В первом случае для пропитки бумажной изоляции используют масло с кинематической вязкостью не более 37 мм2/с (при 20°С) и не более 9,6 мм2/с (при 50°С). Для повышения вязкости до указанных значений в масло добавляют канифоль или синтетический загуститель.
Для маслонаполненных кабелей высокого давления (до 1,5 МПа), рассчитанных на напряжение от 110 до 500 кВ, используют особо тщательно очищенное нефтяное масло, имеющее значение tgδ не более 0,003 (при 50 Гц и 100°С), Епр не менее 20 кВ/мм (при 50 Гц и 20°С), кинематическую вязкость при 20°С не более 800 мм2/с и при 50°С не более 50 мм2/с; температура застывания должна быть не выше минус 30°С, а температура вспышки не ниже плюс 200°С.
Нефтяные электроизоляционные масла являются наиболее доступными и недорогими жидкими диэлектриками, обладающими при хорошей очистке достаточно высокими электроизоляционными характеристиками – малой величиной tgδ и высокой Епр. Недостатки нефтяных масел: пожаро- и взрывоопасность, невысокая стойкость к тепловому и электрическому старению, гигроскопичность (достаточно высокая у окисленных масел). Для пропитки бумажных конденсаторов желательно иметь жидкий диэлектрик с более высоким значением Епр.
Дата добавления: 2018-02-28; просмотров: 1611; Мы поможем в написании вашей работы! |
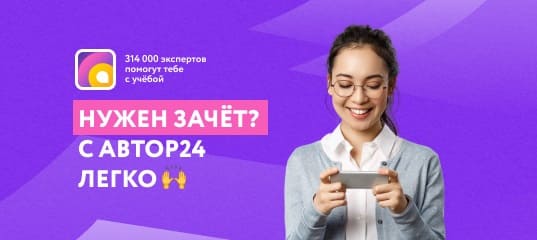
Мы поможем в написании ваших работ!