Возведение постоянной крепи из бетона
Крепь ствола является искусственной грузонесущей конструкцией, предназначенной для предотвращения обрушения горных пород, сохранения первоначального размера и рабочего состояния ствола.
Возведение крепи является наиболее важным иответственным процессом. Стоимость и трудоемкость работ по возведению крепи составляют: стоимость 50-б0 %, а трудоемкость ее возведения - 40 % от общей стоимости и трудоемкости проходки ствола.
К крепи предъявляются следующие требования:
- крепь должна быть прочной, выдерживать нагрузку от давления горных без деформаций, трещин;
- обладать хорошей водонепроницаемостью;
- иметь минимальное аэродинамическое сопротивление;
- занимать минимальный объем;
- иметь минимальную трудоемкость по ее возведению.
Отклонение стенок крепи по радиусу от вертикальной оси не должно превышать ±50 мм для монолитной и ±30 мм для тюбинговой крепи.
В разные периоды времени применялись различные виды крепей (монолитный бетон и железобетон, кирпич, чугунные и железобетонные тюбинги, набрызгбетон и дерево).
В последнее время наибольшее применение получила монолитная бетонная крепь. В угольной ирудной промышленности применение монолитной бетонной крепи ежегодно составляет 85-90 %, ежегодное применение чугунных тюбингов составляет 5-8 % от общего объема строительства стволов. Набрызгбетонная крепь применяется в основном при проходке вспомогательных стволов в крепких породах. Деревянная крепь применяется редко, в основном для крепления шурфов, гезенков, восстающих и других вспомогательных выработок. Широкое применение для крепления стволов монолитной бетонной крепи объясняется следующими ее преимуществами:
|
|
- технологичность работ по возведению крепи, механизация работ составляет 84 % и только 16 % работ выполняются вручную;
- при железобетонных тюбингах соответственно 46 и 54 %;
- стоимость монолитной бетонной крепи ниже на 30-50 % бетонитовой и крепи из железобетонных тюбингов;
- хорошая связь крепи с породными стенками;
- малое аэродинамическое сопротивление;
- возможность использования местных материалов (песка, щебня) для приготовления бетона;
- большой срок службы и огнестойкость.
Для крепления ствола бетонную смесь с поверхности по трубопроводу подают за опалубку. При проходке основной части ствола наибольшее распространение получили металлические передвижные опалубки секционного типа, самоотрываюшиеся.
Бетонопровод монтируется из става труб, гасителя и воронки. Трубы применяют диаметром 150 мм с толщиной стенки 8-10 мм. Соединение труб осуществляется при помощи фланцев, полумуфт или накладными хомутами. Бетонопровод подвешивается на канатах или закрепляется к крепи ствола. В стволах диаметром до 65 м монтируют один трубопровод, при большем диаметре ствола - 2 бетонопровода. Гаситель предназначен для уменьшения скорости падения бетонной смеси при выходе ее из бетонопровода. Гашение скорости движения бетонной смеси основано на изменении направления движения. В бетонопроводе устанавливается один гаситель - в конце бетонопровода. В последнее время гаситель скорости устанавливают на опалубке. Такой гаситель представляет собой приемный карман, из которого по плите бетонная смесь перемещается за опалубку. Подача бетона за опалубку производится по одному или двум гибким стенам. При одном гибком ставе он располагается в центре ствола, при двух - у крепи. При одном бетонопроводе и двух гибких ставах на полке устанавливается распределительное устройство.
|
|
Схема размещения комплекса оборудования для возведения монолитной бетонной крепи показана на рисунке 2.9.
Рисунок 2.9 - Схема размещения оборудования для возведения
монолитной бетонной крепи
Гибкий став собирается из механических патрубков длиной 500 мм. Патрубки между собой соединяют при помощи канатов или крючков и накладных петель. Длина гибкого става определяется расстоянием между опалубкой и полком и изменяется от 10 до 20 м. Бетонная смесь укладывается равномерными слоями высотой 0,4-0,5 см. После укладкибетонной смеси на высоту опалубки заделывается шов, прочищается бетонопровод (спускается 0,2-0,3 м3 щебня и промывается водой). Высота опалубки изменяется от 2 до 5 м. С увеличением высоты опалубки с 2 до 5 м удельное время на возведение 1 м бетонной крепи толщиной 0,5 м уменьшается на 25-30 %. Сокращение времени возведения бетонной крепи за счет применения опалубки высотой 4-5 м вместоопалубки высотой 2 м позволяет при прочих равных условиях увеличить скорость проходки ствола на 5-6 м/мес. В настоящее время при проходке стволов в основном применяют опалубки высотой 3,5-4 м.
|
|
В процессе строительства ствола ведется контроль закачеством возведения бетонной крепи. Основными вопросами контроля являются геометрические размеры ствола, качество бетонной смеси и технология ее укладки за опалубку.
Поверхность крепи ствола должна быть гладкой. Общая площадь раковин глубиной до 20 мм не должна превышать 100 см2 на каждые 5 м2 поверхности крепи. Швы между отдельными звеньями должны быть плотно заделаны.
|
|
2.24. Тампонаж закрепного пространства
Вода из водоносных горизонтов, просачиваясь через бетонную крепь, поступает в ствол, создавая дополнительные расходы на ее откачку. В настоящее время 50 % эксплуатируемых и строящихся шахт имеют приток воды в ствол более 10 м3/ч. По нормам остаточный приток воды в пройденный ствол глубиной 800 м не должен превышать 5 м3/ч. При большей глубине ствола допускается увеличение притока воды 0,5 м3/ч на каждые 100 м.
Фильтрующаяся через крепь вода вызывает коррозию бетона, последняя приводит к уменьшению толщины крепи, увеличению ее пористости и снижению грузонесущей способности. Кроме того, вызывает интенсивную коррозию проводников и расстрелов. Для уменьшения остаточного притока воды производится тампонаж закрепного пространства. Суть его состоит в том, что в бетонной крепи бурят шпуры, через которые нагнетают цементный или цементно-песчаный раствор. Раствор, заполняя пустоты в закрепном пространстве, поры в бетоне и трещины в водоносных породах, повышает водонепроницаемость бетонной крепи и препятствует поступлению воды в ствол. Шпуры бурят диаметром 50-60 мм, располагают их в шахматном порядке по периметру ствола. Расстояние между шпурами в ряду составляет 1,5-2,0 м, между рядами шпуров - 1,0-2,5 м. Чем больше приток воды в ствол, тем меньше расстояние между шпурами в ряду и рядами.
В шпуры вставляют кондукторы (труба диаметром 40-50 мм длиной 0,5-0,6 м), которые заделывают быстросхватывающимся раствором и ветошью. Выступающие в отвод концы кондукторов оборудуются запорными кранами. Применяют цементно-песчаные растворы состава Ц:П от 1:1 до 1:4 в зависимости от притока воды, трещин в породе и пористости бетона. Тампонаж ведут с подвесного полка. Раствор подается с поверхности по трубам в бак, установленный на полке. В шпур раствор нагнетается насосом с давлением 0,3-0,5 МПа. Максимальное давление не должно превышать расчетных нагрузок на крепь. При достижении максимального давления подача раствора в шпур прекращается, перекрывается запорный вентиль. Шланг присоединяется к следующему шпуру. В такой последовательности проводят тампонаж всех шпуров водоносного участка. В отдельных случаях бывает необходимо проводить повторный тампонаж.
Дата добавления: 2018-02-28; просмотров: 521; Мы поможем в написании вашей работы! |
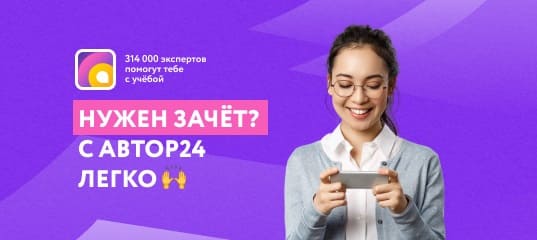
Мы поможем в написании ваших работ!