Кем и в каких документах указывается
Значения давления гидравлических испытаний для оборудования и сборочных единиц (блоков) трубопроводов должны указываться предприятием-изготовителем в паспорте оборудования и свидетельстве об изготовлении деталей и сборочных единиц трубопровода.
Значения давлений гидравлических (пневматических) испытаний систем (контуров) должны определяться проектной организацией и сообщаться предприятию-владельцу оборудования и трубопроводов, которое уточняет эти значения на основе данных, содержащихся в паспортах оборудования и трубопроводов, комплектующих систему (контур).
Определение температуры
В большинстве случаев для гидравлического испытания должна применяться вода температурой не ниже 5 °С и не выше 40 °C, если в технических условиях не указано конкретное значение температуры, допускаемой по условию предотвращения хрупкого разрушения и определяемое согласно Нормам расчета на прочность. При этом во всех случаях температура испытательной и окружающей среды не должна быть ниже 5 °C.
Однако в некоторых отраслях промышленности к выбору допускаемой температуры подходят более строго, что связано с изменением физических свойств материалов и воды при очень высоких давлениях и воздействии других факторов. Например, на АЭС допускаемая температура металла при гидравлических (пневматических) испытаниях в процессе эксплуатации (в том числе после ремонта) устанавливается на основе данных расчета на прочность, паспортов оборудования и трубопроводов, чисел циклов нагружения, зафиксированных в процессе эксплуатации, фактических флюенсов нейтронов с энергией МэВ и данных испытаний образцов-свидетелей, устанавливаемых в корпуса ядерных реакторов.
|
|
Кем и в каких документах указывается.
Допускаемая температура металла при гидравлических испытаниях, проводимых после изготовления, должна определяться конструкторской (проектной) организацией и указываться в чертежах, паспортах оборудования и свидетельствах об изготовлении деталей и сборочных единиц трубопроводов.
Определение времени выдержки
Время выдержки под пробным давлением устанавливается разработчиком проекта, но должно быть не менее 10 мин. При отсутствии указаний в проекте время выдержки должно быть не менее значений, указанных в табл.
Толщина стенки, мм | Время выдержки, мин |
До 50 | 10 |
Свыше 50 до 100 | 20 |
Свыше 100 | 30 |
Для литых, неметаллических и многослойных сосудов независимо от толщины стенки | 60 |
Вопрос
Система планово-предупредительного ремонта (ремонтные нормативы, документация, структура организации и управления ремонтно-механических служб предприятий).
|
|
Принятая в химической промышленности система ТО и Р базируется на сочетании ТО и планово-предупредительных ремонтов (ППР).
ППР проводят по методу планово-периодических ремонтов для основного оборудования и методу послеосмотровых ремонтов (ремонт по техническому состоянию) для вспомогательного оборудования.
Деление на основное и вспомогательное оборудование условно и зависит от конкретных условий эксплуатации данного оборудования и степени его влияния на получение конечного продукта. Обычно к основному относят оборудование, предназначенное для проведения основных химико-технологических процессов и получения целевого продукта. Выход из строя основного оборудования приводит к остановке технологической линии (установки) или резкому снижению ее производительности.
Сущность планово-периодических ремонтов заключается в том, что ремонты всех видов планируют и выполняют в строго установленные ремонтными нормативами сроки. Сущность ремонта по техническому состоянию заключается в том, что виды и сроки ремонта планируют на основе сведений о техническом состоянии оборудования, полученных при проведении периодического технического обслуживания.
|
|
Система ППР оборудования химической промышленности предусматривает текущий и капитальный ремонт.
Текущий ремонт выполняют для обеспечения или восстановления работоспособности оборудования; он состоит в замене или восстановлении отдельных сборочных единиц и деталей оборудования. Текущие ремонты включают: операции периодического ТО; работы по замене или восстановлению быстроизнашивающихся деталей и сборочных единиц; ремонт футеровки и защитного покрытия; окрашивание; проверку крепежных соединений и замену вышедших из строя деталей; замену сальников и прокладок; ревизию арматуры; смену масла в смазочных системах и т.д.
Капитальный ремонт выполняют для восстановления исправности оборудования и полного или близкого к полному восстановлению ресурса оборудования с заменой или восстановлением любых его элементов, включая базовые. При капитальных ремонтах выполняют, как правило, работы по модернизации оборудования и внедрению новой техники. Объем капитального ремонта и подробный перечень работ устанавливаются ведомостью дефектов. Типовые работы при капитальном ремонте: мероприятия в объеме текущего ремонта; полная разборка, очистка и промывка ремонтируемого оборудования; замена или восстановление всех изношенных деталей и узлов, включая базовые; полная или частичная замена изоляции, футеровки; сборка, выверка, регулирование оборудования; окраска и послеремонтные испытания. При капитальном ремонте устраняют дефекты оборудования, выявленные как в процессе эксплуатации, так и при проведении ремонта.
|
|
ППР оборудования проводят на основе ремонтных нормативов, разработанных для машин и оборудования различных типов. Эти нормативы определяют: межремонтный период (ресурс); продолжительность простоя с разбивкой на подготовительный, ремонтный и заключительный периоды (в часах); трудоемкость ремонта (в человеко-часах).
Межремонтный период определяет время работы оборудования между двумя последовательно проведенными ремонтами и является основой для разработки такого показателя системы планово-предупредительного ремонта, как структура ремонтного цикла. Общее число рабочих часов оборудования условно принято 720 ч в месяц, 8640 ч в год. В зависимости от условий работы производства и с учетом технического состояния оборудования допускаются следующие отклонения от норматива межремонтного периода: ±15 % между текущими ремонтами; ±10 % между капитальными ремонтами. На основе межремонтного периода разрабатывается ремонтный цикл – это наименьшие повторяющиеся интервалы времени или наработка оборудования, в течение которых выполняются в определенной последовательности и в соответствии с требованиями нормативно-технической документации все установленные виды ремонта. Для химического оборудования в качестве ремонтного цикла принимают период между двумя капитальными ремонтами.
Чередование ремонтов в определенной последовательности и через определенные промежутки времени называется структурой ремонтного цикла. Она основана на объединении деталей и узлов по группам, внутри которых наработка до первого отказа имеет практически одинаковое значение. Таким образом определяют группы быстроизнашивающихся деталей, восстановление которых при ремонте производится путем замены или незначительного по объему ремонта, и группы деталей с большим сроком наработки, требующих при ремонте больших трудозатрат для восстановления. Соотношением таких групп деталей и определяется структура ремонтного цикла.
Продолжительность простоя в ремонте исчисляют с момента отключения оборудования до момента сдачи отремонтированного оборудования эксплуатационному персоналу и вывода оборудования на рабочий режим и включает время проведения подготовительных, ремонтных и заключительных работ. К подготовительным работам относятся: остановка оборудования; сброс давления; вывод продукта; продувка, промывка, нейтрализация; установка заглушек и т.д. Подготовительные работы завершают сдачей оборудования ремонтному персоналу. Продолжительность собственно ремонтных работ – это период от момента приемки оборудования в ремонт до момента сдачи отремонтированного оборудования эксплуатационному персоналу, включая время испытаний на прочность и плотность для сосудов и аппаратов (или обкатки вхолостую для машин и механизмов). К заключительным работам относятся подготовка, пуск оборудования в эксплуатацию и вывод его на рабочий режим.
Трудоемкость ремонта – это трудозатраты на проведение одного ремонта оборудования данного вида. Ее рассчитывают с учетом сложности и конструктивных особенностей оборудования (без изготовления запасных частей). В системе ППР используют нормативы трудоемкости ремонтов всех видов в человеко-часах для ремонтников четвертого разряда при шестиразрядной сетке.
При планировании ремонтов основными документами являются: годовой (перспективный) график планово-периодических ремонтов оборудования; месячный (оперативный) план-график ремонта оборудования; проект графика ремонтных остановок производств химической продукции; титульный список капитального ремонта основных фондов предприятия; установленные ремонтные нормативы; нормы периодичности освидетельствования и испытания сосудов и аппаратов; сметно-техническая документация; акт на установление (изменение) календарного срока ремонта предыдущего года. Кроме того, при планировании ремонта необходимы: план ремонтно-механического цеха, предназначенный для изготовления запасных частей и нестандартного оборудования; расчет объема ремонтных работ на плановый год; расчет трудоемкости ремонтных работ; расчет численности ремонтного персонала.
4. Задача А2.
Рассчитать такелажную оснастку для подъема колонного аппарата методом скольжения с отрывом низа аппарата от земли двумя вертикальными мачтами.
Исходные данные. Вес колонны Р = 1,2 МН; вес мачты РМ = 0,05 МН; вес грузовых полиспастов РГП = 4 кН; усилие предварительного натяжения ванты S1 = 10 кН; число вант на одной мачте п = 4; длина мачты l = 55 м; высота колонны H = 50 м; расстояние центра массы колонны от основания l цм = 23 м; диаметр колонны D = 2,2 м; расстояние от оси мачты до якоря задней ванты а = 55 м; расстояние между осями мачт b = 5 м; расстояние от оси мачты до якоря боковой ванты g = 55 м; расстояние по горизонтали от оси мачты до центра массы аппарата в момент отрыва d = 10 м; длина тормозной оттяжки f = 40 м; расстояние по вертикали от уровня земли до центра массы аппарата в момент отрыва h = 20 м; кратность полиспаста т= 8; коэффициент динамичности кд = 1,1. Расчетная схема приведена на рис. 1.
![]() |
Р и с. 1. Расчетная схема определения усилий в двух мачтах при подъеме груза
с оттяжкой
Предварительно определим:
♦ длину задней ванты
♦ расстояние по вертикали от оголовка мачты до точки пересечения осей грузовых полиспастов, оттяжки и центра массы груза
;
;
;
♦ длину боковой ванты
Далее последовательно вычисляем:
♦ расчетное усилие для полиспастов и вант
♦ вертикальную составляющую, обусловленную усилием предварительного натяжения
♦ суммарную составляющую усилий в грузовых полиспастах
♦ усилия в грузовых полиспастах при симметричном подвесе груза
относительно осей мачты
♦ горизонтальную и вертикальную
составляющие, обусловленные усилиями в полиспасте Т и Т1 действующих в плоскости полиспаста:
♦ усилие в задней ванте
♦ усилие в боковой ванте
♦ вертикальные составляющие Q7 и Q8 соответственно усилий Q5 и Q6 , действующие по оси мачты:
♦ суммарное усилие от веса груза, действующее на оголовок мачты
♦ усилие в тормозной оттяжке
♦ суммарное усилие на основание мачты
Q11 = Q4 + Q7 + Q8 + Po + Pм,
Q11 = 0.769 +0,258 +0,128 +28.28 +0,05=29.48
Ро = S1×l /с×n = 10×55/77.78×4 = 28.28
Усилие в сбегающей нитке грузового полиспаста, идущей на лебедку, определяется как
где — КПД одного ролика в блоке (
= 0,96 при установке роликов на подшипниках скольжения;
= 0,98 при установке ролика на подшипниках качения).
Суммарное усилие на основание мачты составит
5.Задача Б2
Рассчитать такелажную оснастку для подъема колонного аппарата методом поворота вокруг шарнира двумя вертикальными мачтами.
![]() |
Рис.3.3. Расчетная схема подъема аппарата методом поворота вокруг шарнира
а-мачта установлена за поворотным шарниром; б- мачта установлена между поворотным шарниром и центром масс (цм) аппарата.
Исходные данные. Вес колонны Р= 0,8 МН; диаметр колонны D= 2,2 м; расстояние центра массы колонны от ее основания lцм = 18 м; высота мачты H= 40 м; расстояние от оси шарнира до оси мачты lш = 5 м; расстояние от места строповки аппарата до его основания lс = 22 м; расстояние от мачты до якоря ванты lя = 40 м; высота фундамента hф = 0,5 м; длина аппарата Lап = 40 м; вес мачты РМ = 50 кН; расстояние от оси шарнира до точки крепления тормозной оттяжки hТ = 40 м; угол между тормозной оттяжкой и горизонталью = 45°; усилие предварительного натяжения вант
= 10 кН; КПД одного ролика в блоке
= 0,96; кратность полиспаста т = 8.
Предварительно определим:
♦ расстояние между шарниром и центром массы аппарата
♦ угол между образующей аппарата и линией, соединяющей шарнир с его центром масс,
♦ угол между мачтой и грузовым полиспастом:
установка мачты по первому варианту
установка мачты по второму варианту
Угол между мачтой и вантой определяется графически по расчетной схеме или по формуле
Расчетные усилия в грузовом полиспасте находятся в начальный момент подъема при ф = 0°:
♦ при установке мачт по первому варианту
при одиночной мачте
при парных мачтах
♦ при установке мачт по второму варианту
при одиночной мачте
при парных мачтах
где kH = 1,1 — коэффициент перегрузки, учитывающий возможное отклонение фактической нагрузки от нормативного значения вследствие неточного определения центра массы аппарата и изменчивости нагрузки; кД = 1,1 — коэффициент динамичности, учитывающий повышение нагрузки на такелажную оснастку вследствие изменений скорости подъема или опускания груза; км — коэффициент неравномерности нагрузки на такелажные элементы с использованием спаренных мачт (км =1,1 при использовании балансирных устройств; км= 1,2 в отсутствие балансирных устройств).
По усилию Qв рассчитывают грузовой полиспаст, т.е. подбирают полиспастные блоки, определяют диаметр роликов в блоке и их число, находят усилие в сбегающем конце полиспаста, по которому подбирают лебедку, подсчитывают диаметр и длину каната для оснастки полиспаста, а также подбирают тип и диаметр каната для гибкого стропа.
Усилие в задней ванте независимо от места расположения мачт определяется как
расчет выполнен для двух мачт, установленных по схеме на рис. 2, б.
По усилию подбирают тип и диаметр каната для задней ванты и рассчитывают для нее якорь, т.е. определяют вес якоря или усилия в анкерных болтах и проверяют устойчивость якоря против горизонтального сдвига и опрокидывания.
По усилию в тормозной оттяжке:
рассчитывают трос для тормозной оттяжки и подбирают лебедку.
По суммарному усилию, действующему по оси мачты,
усилие в сбегающей ветви полиспаста, проверяют прочность и устойчивость мачты на сжатие.
При установке мачт по второму варианту рассчитывают дотягивающую систему для подъема аппарата мачтами на втором этапе от угла подъема до положения неустойчивого равновесия. С этой целью определяют максимальное усилие F, задаваясь углом наклона дотягивающей системы к горизонту. При F< 147 кН подбирают лебедку или трактор и рассчитывают дотягивающий трос; при F > 147 кН рассчитывают дотягивающий полиспаст и якорь для него.
Литература:
1. Тавастшерна Р.И. Монтаж технологических трубопроводов. М: Высш. Школа, 1980. 285с.
2. Паникаров И.И. и др. Машины и аппараты химических производств. – М.: Машиностроение, 1989. 368 с.
3. Монтаж и монтаж и ремонт технологического оборудования: Учеб. Пособие / М.Г. Гайнуллин и др. Казан. Гос. Технол. Ун-т. Казань, 2002. 104 с.
Дата добавления: 2018-02-28; просмотров: 416; Мы поможем в написании вашей работы! |
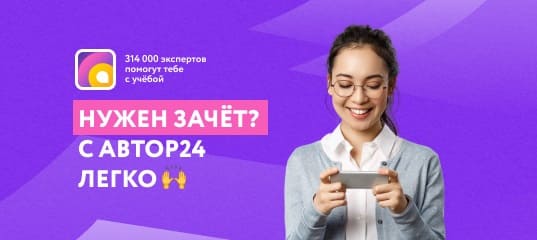
Мы поможем в написании ваших работ!