Испытание оборудования на прочность и плотность. Нормы гидравлического и пневматического испытаний аппаратов
Федеральное агентство по образованию
Нижнекамский химико-технологический институт (филиал)
Государственное образовательное учреждение
высшего профессионального образования
«Казанский государственный технологический университет»
Кафедра: Машин и аппаратов химических производств и предприятий строительных материалов
КОНТРОЛЬНАЯ РАБОТА
По дисциплине: Монтаж и ремонт оборудования
Вариант 14
Выполнил: студент 2522 группы
механического факультета
…………………
Проверил: Вилохин
Нижнекамск 2010г
Содержание:
Вопрос 8.
Мачтовые подъемники: мачты, порталы, шевры . Гидравлический подъемник. (дать эскизы).
Вопрос 24.
Испытание оборудования на прочность и плотность. Нормы гидравлического и пневматического испытаний аппаратов.
Вопрос
Система планово-предупредительного ремонта (ремонтные нормативы, документация, структура организации и управления ремонтно-механических служб предприятий).
Задача А2.
Задача Б2.
Литература.
1.Вопрос 8.
Мачтовые подъемники: мачты, порталы, шевры . Гидравлический подъемник. (дать эскизы).
Мачтовые подъемники (мачты, порталы, шевры) являются простейшими грузоподъемными механизмами и применяются для подъема и установки в проектное положение крупногабаритных, тяжеловесных аппаратов на значительную высоту, при недостаточных грузовысотных характеристиках стреловых кранов.
|
|
Монтажная мачта (рис. 1) представляет собой металлическую
конструкцию 1 (трубчатую или решетчатую), оголовок 3 которой для удержания мачты в рабочем положении и изменения угла ее наклона укреплен тремя или четырьмя гибкими вантами 2. Ванты одним концом крепят за проушины оголовка мачты, а другим - к неподвижным якорям. Угол наклона вант к горизонту составляет 45 – 60о. Для уменьшения подвижности мачты после ее установки в проектное положение вантам с помощью винтовых стяжек (на рис. 7.3 не показаны) или полиспастов и лебедок придается предварительное усилие натяжения в 10 ¸ 30кН.
Оголовок 3 мачты может быть вращающимся или неподвижным. К нему крепятся один или два грузовых полиспаста 4, сбегающие ветви 5 которые через отводной блок 6 (или ролик) направляются к барабану лебедки. Мачта передает вертикальное усилие на грунт через опорный башмак 7, который устанавливают на шпалы или на специальный фундамент и закрепляют от горизонтального сдвига специальными растяжками 8 и якорями 9. Соединение мачты с опорой бывает жесткое, (мачта работает в строго вертикальном положении), через цилиндрический шарнир или сферический шарнир 10 (мачта может изменять угол наклона в плоскости подъема груза). Наибольшее распространение получило соединение мачты с опорой через сферический шарнир, который позволяет поворачивать мачту без перестановки вант и наклонять ее на угол до 12° от вертикали.
|
|
В тех случаях, когда условия монтажной площадки не позволяют разместить боковые ванты мачты и в некоторых других случаях, обусловленных методами производства работ, применяют шевры.
Монтажный шевр (рис. 3) представляет собой А-образную раму 1, которую изготавливают из стальных труб или прокатных профилей (на виде А оснастка условно не показана). К оголовку шевра подвешивают грузовой полиспаст 2, сбегающую ветвь 5 которого через отводной блок 4 направляют
на барабан лебедки. В вертикальном и наклонном положениях шевр удерживается канатом 6, который с целью изменения угла наклона шевра снабжается тяговым полиспастом (на рисунке не показан). Нижние концы шевра посредством шарнира соединены с опорами 3, которые закреплены на фундаментах и удерживаются тросами от сдвига при наклоне шевра. При высоте шевра более 10 м для удобства транспортирования их выполняют разборными с помощью фланцевых соединений. Грузоподъемность шевров 50 – 250т, высота подъема – до 35м.
|
|
Для монтажа крупногабаритных тяжеловесных аппаратов, а также для сборки уникальных сооружений с большим количеством тяжеловесных подъемов целесообразно использовать портальные подъемники, или порталы (рис.4). Портал представляет собой однопролетную П-образную конструкцию и состоит из двух опорных стоек 1, которые в верхней части соединяются ригелем 2. Ригель и стойки портала представляют собой сварную пространственную конструкцию, собираемую из отдельных секций.
1 – опорная стойка; 2 – ригель; 3- грузовой полиспаст; 4 – отводной блок; 5 – ванты; 6 – опорный башмак
К ригелю 2 на специальных осях крепят грузовые полиспасты 3, сбегающие ветви которых через отводные блоки 4, прикрепленные к оголовку и опоре стоек, направляются к лебедкам. В рабочем положении портал удерживается шестью вантами 5, концы которых прикреплены к якорям. Портал может работать и в наклонном положении, для чего на ванты ставят полиспасты. Соединение стоек портала с опорными башмаками 6 осуществляется с помощью горизонтальных осей, обеспечивающих поворот портала при его монтаже, а также при изменении угла наклона в процессе работы. Опорные башмаки 6 во избежание сдвига крепят расчалками. Для соединения ригеля 2 с оголовками стоек портала 1 применяют сферический шарнир, который обеспечивает передачу нагрузки строго по оси стоек портала и допускает незначительный перекос стоек. Порталы позволяют перемещать груз вертикально и горизонтально; их грузоподъемность составляет 100 – 500т, высота поднимаемых аппаратов до 100м.
|
|
При монтаже вертикальных аппаратов успешно используют гидравлические подъемные механизмы. По кинематической схеме способ подъема аппаратов гидроподъемником относится к безъякорным и называется способом выталкивания (рис. 5). Перед подъемом аппарат 1 с помощью крана укладывается нижней частью в шарнир 5, а верхней - на козлы или шпальную выкладку 2. Стойки гидроподъемника 3 устанавливают по обе стороны аппарата и расчаливают. Опоры стоек соединяются стяжками 4 или полиспастами с поворотным шарниром поднимаемого аппарата.
При перемещении подъемных устройств (каретки и траверсы) вдоль стоек поднимаемая колонна поворачивается вокруг шарнира; одновременно вокруг шарнирных опор поворачиваются стойки гидроподъемника. При подходе к положению
Рис.5. Схема монтажа аппарата гидроподъемником:
1 – аппарат; 2 – шпальная выкладка; 3 – гидроподъемник; 4 – стяжка; 5 – шарнир; 6 – тормозная оттяжка
неустойчивого равновесия включается тормозная оттяжка 6. Если длина стоек недостаточна, то аппарат переводят в вертикальное положение методом выжимания, перемещая опоры стоек гидроподъемника полиспастами, связывающими опоры стоек с поворотным шарниром аппарата. При этом стойки движутся по металлическим листам, смазанным солидолом.
Вопрос 24.
Испытание оборудования на прочность и плотность. Нормы гидравлического и пневматического испытаний аппаратов.
Гидравлическое испытание — один из наиболее часто используемых видов неразрушающего контроля, проводящееся с целью проверки прочности и плотности сосудов, трубопроводов, теплообменников, насосов и другого оборудования, работающего под давлением, их деталей и сборочных единиц. Также гидравлическим испытаниям могут подвергаться схемы тепломеханического оборудования в сборе и даже целые тепловые сети. По принятой в большинстве стран практике, всё оборудование, работающее под давлением, подвергают гидравлическим испытаниям:
- после изготовления предприятием-изготовителем оборудования или элементов трубопроводов, поставляемых на монтаж;
- после монтажа оборудования и трубопроводов;
- в процессе эксплуатации оборудования и трубопроводов, нагружаемых давлением воды, пара или пароводяной смеси.
Гидравлическое испытание — необходимая процедура, свидетельствующая о надёжности оборудования и трубопроводов, работающих под давлением, в течение всего срока их службы, что крайне важно, учитывая серьёзную опасность для жизни и здоровья людей в случае их неисправностей и аварий.
Ход процедуры
В испытуемом оборудовании, трубопроводе или системе (контуре) создаётся пробное давление (во избежание гидроударов и внезапных аварийных ситуаций это производится медленно и плавно), превышающее рабочее на определяемую по специальным формулам величину, чаще всего на 25 %. При этом тщательно контролируют рост давления по двум независимым поверенным манометрам или каналам измерений, на этом этапе допускается колебание давления вследствие изменения температуры жидкости. В процессе набора давления в обязательном порядке должны быть приняты меры для исключения скопления газовых пузырей в полостях, заполненных жидкостью. Затем, в течение так называемого времени выдержки, оборудование находится под повышенным давлением, которое не должно падать вследствие неплотности испытуемого оборудования, что также внимательно отслеживается. После чего давление снижается до рабочего. На протяжении этих этапов персонал должен находиться в безопасном месте, нахождение рядом с испытуемым оборудованием строжайше запрещено. После снижения давления персонал проводит визуальный осмотр оборудования и трубопроводов в доступных местах в течение времени, необходимого для осмотра. В комбинированных сосудах с двумя и более рабочими полостями, рассчитанными на разные давления (например в теплообменниках), гидравлическому испытанию должна подвергаться каждая полость.
Оценка результатов
Оборудование и трубопроводы считаются выдержавшими гидравлические испытания, если в процессе испытаний и при осмотре не обнаружено течей жидкости и разрывов металла, в процессе выдержки падение давления не выходило за пределы, объясняемые колебаниями давления вследствие изменения температуры жидкости, а после испытаний не выявлено видимых остаточных деформаций.
Пневматическое испытание
В случаях, специально оговоренных в проектной документации на испытуемое изделие или государственными правилами и стандартами, допускается замена гидравлических испытаний пневматическими. Чаще всего это разрешается при условии дополнительного обследования предприятием-изготовителем изделия другими методами неразрушающего контроля, например сплошным ультразвуковым и радиографическим контролем основного металла и сварных соединений. В некоторых случаях пневматические испытания являются своеобразным подготовительным этапом перед гидравлическими. Они проводятся аналогично гидравлическим, иногда, при небольших давлениях и применительно к оборудованию со специфической конструкцией (например теплообменникам), места, где могут быть неплотности, обрабатываются мыльным раствором. После повышения давления на местах, имеющих дефекты, вздуваются мыльные пузыри, что позволяет легко их обнаружить. Таким способом определяется плотность, но не прочность оборудования.
Дата добавления: 2018-02-28; просмотров: 1035; Мы поможем в написании вашей работы! |
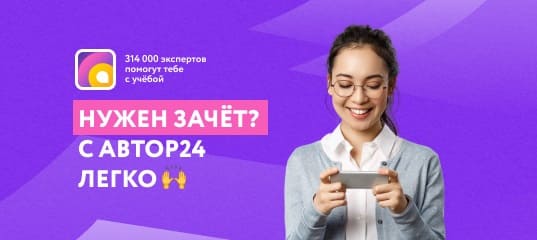
Мы поможем в написании ваших работ!