Методы расчета точности и анализа техпроцессов
1. Теоретический, расчетный
2. Экспериментальный, статистический
1. Расчетно-аналитическийй метод предполагает полную определенность техпроцесса, на основе решения системы уравнений, описывающих закономерность переноса погрешностей техпроцесса и определение искомой точности.
Правомерность применения определенных моделей зависит от степени исследования, изучения изучаемого процесса. Математическое описание процессов заключается в последовательном определений исходных погрешностей и дальнейшее установление в аналитическом виде их влияния на окончательную точность обработки.
Трудности метода:
1)Невозможно учесть все факторы, влияющие на точность техпроцесса; 2)Сложность решения большого числа уравнений; 3)По точности изготовления одного изделия нельзя судить о точности тех.процесса в целом.
Этот метод применяется: 1)для оценки влияния отдельных факторов в определенных условиях производства, но не позволяет получить комплексную оценку всех факторов, влияющих на точность обработки; 2)для расчета погрешностей единичных деталей.
2. Вероятностный метод может быть использован для анализа точности обработки партии деталей или процесса в целом, т.к. он охватывает все возможные и важные комбинации условий хода тех. процесса. Вероятностная модель содержит законы распределения характеристик, параметров размеров и рассеивания погрешности обработки, как для партии деталей, так и для всего процесса в целом.
|
|
3. Метод статического моделирования для него необходимо располагать экспериментальными данными о точности отдельных операций и отдельных параметров тех.процесса.
Статические методы:
1.Кривых распределения
2.Точностные диаграммы
3.Корреляционные методы
4.Регрессионные методы
5.Дисперсионный анализ
6.Теория планирования эксперимента.
4. Расчет анализа точности на основе решения технологического размерного уравнения возможен при настройке станков, но необходимо четко представлять взаимодействие отдельных параметров влияющих на точность настройки.
1. 2.
Аст – статический размер, определяемый положением инструмента относительно установочных поверхностей станка при ненапруженной технолог. системы.
Адин – динамическая деформация технолог. системы в направлений выдерживаемого размера под действием сил резания.
Ауст – размер определяющий положение измерительной базы относительно установочных поверхностей станка.
; где
Дата добавления: 2015-12-21; просмотров: 35; Мы поможем в написании вашей работы! |
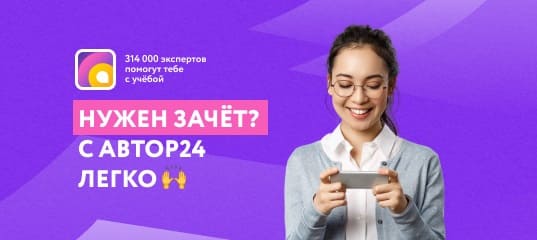
Мы поможем в написании ваших работ!