Кондиционирование базисных рулонов плёнки
Экструзия рукавной пленки
2.1.1 Подготовка сырья
Исходным сырьем для соэкструзионной установки является полиэтилен высокого давления (LDPE). Также используется высококачественное импортное сырье: линейный полиэтилен низкой плотности (LLDPE), металлоценовый линейный полиэтилен низкой плотности (mLLDPE), термополимер РР, полипропилен (РР), сополимер пропилена (СР), мастербатч (добавки – антистатик, скользящая, антиблокирующая). Полимерное сырье выпускается в виде гранул одного цвета одинаковой геометрической формы. Размер гранул колеблется в пределах 2-5 мм.
Полиэтилен и сополимеры поступают на склад сырья в полиэтиленовых мешках. Поступивший в мешках полиэтилен раскладывается по партиям и хранится при температуре не выше 25°С и относительной влажности 40-80%. Если сырье хранилось на холоде, то перед переработкой его необходимо не менее
12 часов выдержать в теплом помещении.
Доставка сырья на участок осуществляется электропогрузчиками грузоподъемностью 1 тонна.
Каждая партия сырья проходит входной контроль на соответствие показателей требованиям ТНПА.
2.1.2 Загрузка и транспортирование сырья
Полимерное сырьё из мешков загружается в расходные ёмкости (поз. 1). Для каждого вида сырья предусмотрена отдельная ёмкость. Из расходных емкостей сырьё пневмотранспортом подаётся в загрузочный бункер вакуум-загрузчиков (поз. 2). Для каждого экструдера предусмотрен вакуум-загрузчик для главного компонента и три вакуум-загрузчика для дополнительных компонентов.
|
|
Из вакуум-загрузчиков сырьё ссыпается в гравиметрический дозатор (поз. 3). Для каждого экструдера предусмотрен один гравиметрический дозатор с дозированием четырёх видов сырья. Максимальная общая производительность дозатора 310 кг/ч. Производительность по различным видам сырья с насыпной плотностью 0,55 кг/дм3:
1 компонент (10-100) %;
2 компонент (10-100) %;
3 компонент
для экструдеров А, В, Д, Е (1-20) %,
для экструдера С (5-20)%;
4 компонент
для экструдеров А, В, Д, Е (0,8-5) %,
для экструдера С (3-20)%.
Дозатор снабжён четырьмя приёмными воронками со смотровым стеклами, весовой воронкой, камерой смешения, скоростным выпускным клапаном для сырья.
Управление дозаторами в автоматическом режиме осуществляется компьютером.
Дозатор снабжён датчиком минимального уровня материала в смесителе.
После смесителя дозатора полимерный материал подаётся в загрузочную зону экструдера через загрузочный бункер (поз. 4).
2.1.3 Получение расплава, его фильтрация
Плавление полимеров происходит в экструдерах (поз. 5). Экструдер представляет собой обогреваемый цилиндр, внутри которого вращается шнек. Соэкструзионная установка снабжена пятью экструдерами.
|
|
Для центрального слоя (С) используется экструдер со шнеком диаметром 90 мм и отношением длины к диаметру (L/D) –30. Мощность привода 132 кВт.
Для слоёв (А, В, D, Е) используются экструдера со шнеком диаметром
60 мм и отношением длины к диаметру (L/D)–30. Мощность привода 45 кВТ.
Смесь полимеров ссыпается из загрузочного бункера (поз. 4) в загрузочную зону экструдера. Во избежание сплавления гранул полимера загрузочная зона экструдера охлаждается водой.
Шнек захватывает полимерную смесь в зоне загрузки и продавливает её вперед по экструдеру, где смесь проходя через нагреваемые зоны расплавляется и гомогенизируется по составу, температуре и вязкости.
Экструдеры А, В, Д и Е имеют по три зоны нагрева, экструдер С имеет пять зон нагрева. Температура по зонам нагрева поддерживается с помощью электронной системы регулирования температуры и датчиков температуры. Система имеет аварийную сигнализацию, срабатывающую при превышении заданного значения температуры. Регулирование температуры осуществляется компьютером, расположенным на пульте управления. Охлаждение зон нагрева воздушное. Расплавопроводы экструдеров А и В имеют по пять зон обогрева, экструдеров С, Д и Е - по четыре зоны.
|
|
Пройдя через расплавопровод, расплав подаётся на шиберный фильтр.
Пять шиберных сменных фильтров (поз. 6) (по одному для каждого экструдера) укомплектованы адаптерами для подсоединения к экструзионной головке, нагревателями и термопарами. Каждый фильтр содержит подвижную пластину с посадочными местами для двух фильтрующих элементов, один из которых находится в работе, а другой – в резерве. Замена фильтрующих элементов производится вручную, с помощью редукторного рычажного механизма.
Каждый из пяти фильтров имеет два датчика давления расплава (до и после фильтра) и датчик температуры (термопару) для контроля температуры расплава. Вся информация выводится на дисплей системы управления. Для оповещения машиниста о необходимости замены фильтрующего элемента предусмотрена система двухпороговой сигнализации. При подходе давления расплава к первому порогу (для экструдеров А, Е – 290 бар, для экструдеров В, С, Д – 320 бар) включается сигнализация. При достижении второго порога (для экструдеров А, Е – 310 бар, для экструдеров В, С, Д – 350 бар) автоматически отключаются экструдеры. Отфильтрованный расплав через адаптерный узел подается в коническо – цилиндрическую головку с центральной подачей расплава (поз. 7).
|
|
2.1.4 Формование первичной трубчатой заготовки (первичного рукава)
Головка укомплектована фильерой диаметром 300 мм. Фильера оснащена термоболтами, предназначенными для регулировки толщины первичного рукава пленки. Ширина формующей щели фильеры – 1,6 мм. Головка имеет 8 зон нагрева. Давление расплава в головке определяется датчиком давления.
Зазор щели регулируется 36 термоболтами, установленными на верхней гибкой губе фильеры. Каждый термоболт представляет собой металлический стержень с надетым на него теплоэлектронагревателем, и каналами воздушного охлаждения.
При нагреве болта он удлиняется, что уменьшает зазор щели в этом месте. При охлаждении болта происходит обратное явление (он укорачивается). Автоматическое регулирование нагрева каждого болта осуществляется контроллером, принимающим данные от толщиномера. Охлаждение термоболта происходит за счет подачи воздуха индивидуально к каждому болту.
Оформленные пять независимых плоских потока расплава сливаются в один общий поток на небольшом расстоянии перед выходной щелью. Общий поток расплава выходит из головки через плоскую выходную щель фильеры.
Номинальная толщина пленки (суммарная от пяти слоев) определяется производительностью экструзионной системы, а поддерживается постоянно с помощью автоматической регулировки производительности (скорости) экструдеров. В свою очередь автоматическая система регулирования расхода сырья (дозирование), поддерживает на заданном уровне расход полимерного сырья через каждый из экструдеров в зависимости от заданной производительности.
Формование первичной трубчатой заготовки осуществляется на устройстве формирования первичного рукава, состоящем из кольца водяного охлаждения (поз. 8) для наружного охлаждения первичного рукава и калибратора (поз. 9) диаметром 300 мм. Диаметр калибратора увязан с диаметром первичного рукава.
Выходящий из головки фильеры объединенный поток расплава, охлаждается потоком воды, поступающей из водяного кольца, и формуется в виде первичного рукава. Рукав протягивается через ванну с охлаждающей водой (поз. 10) тянущими валами приёмно – вытяжного устройства (поз. 11) и подаётся на верхнюю вытягивающую группу (поз. 13) валов башни ориентации.
Во время заправки линии рукав наматывается на дополнительный намотчик (поз. 12).
Ванна (поз. 10) из нержавеющей стали предназначена для сбора воды, стекающей вниз из кольца. Вода является оборотной и используется в замкнутом контуре водоснабжения.
Для охлаждения воды предусмотрен теплообменник (вода-вода). Первичный контур теплообменника подключен к сети охлаждённой воды с температурой не более 8 °С, поступающей из чиллера. Вторичный контур, непосредственно контактирующий с пленкой, заполнен отфильтрованной артезианской водой.
Температура воды (12-20)°С регистрируется системой управления.
2.1.5 Вытягивание первичного рукава на башню ориентации
Из нижнего приёмно – вытяжного устройства первичный рукав через комплект холостых роликов, подается на верхние тянущие валы, расположенные на самом верху башни (поз. 13).
Вытягивающее устройство состоит из трех валов, покрытых специальной резиной. Два тянущих вала обеспечивают прием первичного рукава и его перемещение к камерам предварительного разогрева (поз. 14), а третий, обрезиненный вал используется для раздува рукава со стороны экструзионной головки.
Вытягивающее устройство установлено в фиксированном положении над первой нагревающей камерой.
2.1.6 Предварительный разогрев, раздув и ориентация плёнки в поперечном (TD) и продольном (MD) направлениях
Первичный рукав пройдя верхние тянущие валы поступает в камеры предварительного нагрева (поз. 14), где разогревается до 90 - 100°С. Камеры представляют собой жесткие цилиндрические конструкции размером 2000 х 1500 мм, в которых установлены керамические инфракрасные излучатели. Обе камеры имеют три яруса нагревателей (шесть зон нагрева). Высота камеры ориентации 1200 мм.
Предварительно разогретый до пластического состояния первичный рукав поступает в камеру ориентации (поз. 15), в которой так же установлены керамические инфракрасные излучатели. Здесь он раздувается и вытягивается при постоянной температуре в поперечном (TD) направлении до 6 раз по сравнению с исходным диаметром и в продольном (МD) направлении за счет разницы скоростей верхних (поз. 13) и нижних (поз. 26) тянущих валов, благодаря чему пленка становится двуосноориентированной и приобретает прочность и способность к термической усадке. Температура разогретого первичного рукава пленки контролируется с помощью пирометра.
Наполнение воздухом первичного рукава происходит через головку для оптимизации размеров рукава до 450 мм. Основной второй раздув рукава происходит путем нагнетания большого объема (до 4 м3) воздуха с помощью специального устройства (базуки) снизу со стороны намотки при открытом прижимном вале нижнего тянущего устройства.
После раздува рукава прижимной вал нижнего тянущего устройства смыкается.
Таким образом, раздутый рукав закрыт, соответственно, прижимным валом верхних тянущих валов устройства и прижимным валом нижнего тянущего устройства и воздух, находящийся внутри, не может выйти наружу, в результате чего поддерживается высокая стабильность рукава.
2.1.7 Охлаждение пленочного рукава
После окончания процесса ориентации раздутый и растянутый по двум направлениям рукав охлаждается с помощью многостадийной кольцевой системы воздушного охлаждения. В систему входит: одно вертикально перемещаемое кольцо (поз. 17), оснащенное автономным вентилятором (поз. 18) и водо – воздушным теплообменником (поз. 19) с клапанами для контроля и управления температурой воздуха; два неподвижных кольца (поз. 20,21), в комплекте с одним вентилятором (поз. 22) и водо – воздушным теплообменником (поз. 23) с системой регулировки температуры.
Измерение толщины пленки производится радиоизотопным толщиномером (поз. 24) вращающемся вокруг рукава пленки.
2.1.8 Складывание рукава и намотка базисных рулонов
Охлажденный рукав переводится в плоское состояние с помощью панелей складывающего рольганга с регулируемым углом схождения (поз. 25).
Модуль складывания и намотки представляет собой единую сборочную систему, установленную на непрерывно вращающейся платформе. Вращение происходит медленно, но этого достаточно, чтобы равномерно распределять по рулону небольшие неравномерности толщины пленки, что гарантирует получение гладкой поверхности рулона.
Складывающие рольганги опираются на рамную конструкцию, которая установлена на подшипнике большого диаметра.
Нижние тянущие валы (поз. 26), установленные на нижней вращающейся рампе по оси пленочного рукава, обеспечивают протягивание пленки от верхних тянущих валов (поз. 13). Более высокая скорость вытяжки в нижней части рукава обеспечивает продольную ориентационную вытяжку пленки.
Плоскосложенный рукав разрезается по краям с помощью торцевых ножей с
принудительной подачей воздуха в эти ножи и разводится на две независимые станции намотчика (поз. 27) Две станции намотки расположены симметрично, по обе стороны нижнего тянущего устройства.
Намотчик пленки представляет собой контактный намотчик с двумя намоточными станциями, он пригоден для производства рукавов, сложенных в плоское состояние; полурукавов (рукавов прорезанных с одной стороны); плоских пленок.
Сложенный в плоское состояние рукав пленки подается к намотчику приемными валами нижнего вытяжного устройства.
По достижению заданного числа метров намотки ролик поворачивается перед поперечным резаком. При этом полотно пленки поднимается с контактного валика. Намоточный вал с намоточной гильзой и клейкой лентой опускается в вилку поворотного рычага передней намоточной станции на контактный валик. Поперечный резак перерезает пленку между намоточным валом и роликом. Звуковой сигнал сигнализирует об окончании процесса намотки и, одновременно, о начале нового процесса намотки. Следующее полотно пленки захлестывается и прилипает к клейкой ленте, намотанной на гильзу, установленную на намоточном валу. Готовый рулон автоматически укладывается на наклонную рампу Намотанный рулон выходит из рычага намотчика и скатывается на «выход». Приблизительно через 4 секунды рычаг намотчика снова автоматически поворачивается обратно в позицию приема перед контактным валиком. Рулон в передней намоточной станции опускается поворотным рычагом с подъемным роликом в рычаги намотчика. Поворотный рычаг движется дальше непосредственно в исходное положение. Звуковой сигнал автоматически выключается. На этом смена рулона завершена.
Для нейтрализации электростатического заряда, скапливающегося на пленке применяется активная (ионизирующая) система съёма статического заряда.
Готовые рулоны пленки гидравлической тележкой-штабелёром отвозятся на стеллажи кондиционирования (поз. 28). На базисный рулон оформляется этикетка с указанием даты наработки, толщины пленки, длины плёнки в рулоне, массы нетто, номера технологической партии, личного номера машиниста. Производится отбор пробы пленки для проведения физико-механических испытаний.
Кондиционирование базисных рулонов плёнки
С целью выравнивания физико-механических свойств плёнки, для релаксации (выравнивания) внутренних напряжений и миграции добавок, базисные рулоны плёнки кондиционируются на трехярусных стеллажах (поз. 28) в течение не менее 72 часов. В зоне стеллажей кондиционирования поддерживается температура (20-25) ºС.
Стеллаж кондиционирования представляет собой трехярусную металлическую конструкцию длиной-10 м, шириной –3 м, высотой –2,5 м.
После истечения времени кондиционирования базисные рулоны
направляются на резку./8/
Дата добавления: 2023-01-08; просмотров: 38; Мы поможем в написании вашей работы! |
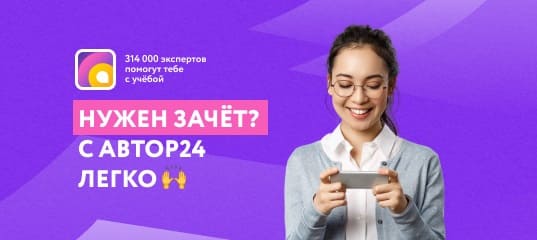
Мы поможем в написании ваших работ!